Efficiency is more than just a buzzword in manufacturing – it’s the linchpin on which successful businesses are built. Among the many ways companies strive for efficiency, thermoforming is appealing because of its cost-effectiveness. So what makes thermoforming cheap – and how can businesses leverage this technique to reduce costs while maintaining quality? This exhaustive guide delves into these questions and more. It explores all the reasons why cost-conscious manufacturers find thermoforming a game changer.
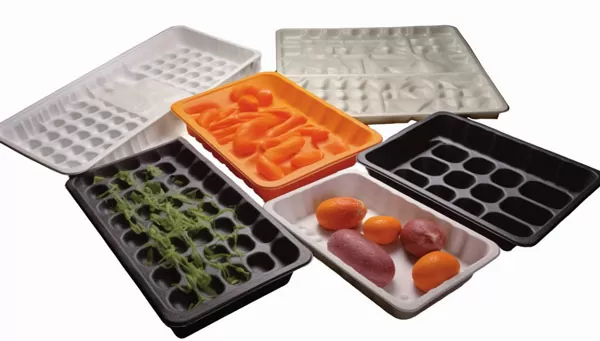
What is Thermoforming?
Thermoforming involves heating plastic sheets until they’re pliable enough to form to specific shapes inside moulds, before being cut into usable products. Industries that use this versatile process include packaging, automotive, medical and consumer goods—among others. Because of its straight for wardness and adaptability, thermoforming offers economies of scale without exorbitant upfront investment.
There are several thermoforming methods used in actual production: differential pressure molding, cover molding, plunger-assisted molding, suction back molding, opposite mold molding, female mold and male mold thermoforming, thin gauge thermoforming, heavy gauge thermoforming and twin sheet forming.
The Fundamental Principles
Principles at play Thermoforming becomes an option with obvious advantages over other manufacturing methods when you consider several key principles at its core:
Materials Cost
Raw materials—usually plastic sheet—used during vacuum forming are relatively inexpensive compared with alternatives such as metals.
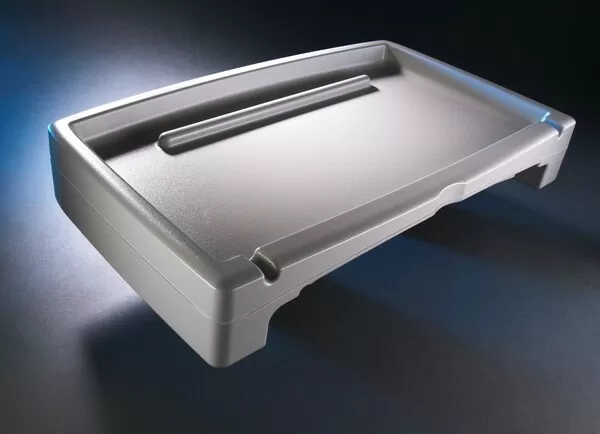
Tooling Simplicity
Moulds needed for thermoformed parts aren’t nearly as complex or expensive as those required by alternative processes like injection moulding.
Energy Efficiency
Thermoforming requires less energy overall versus injection moulding (and similar manufacturing method); lower power consumption translates directly into smaller utility bills per unit produced/operational savings across-the-board.
Speed and Production Volume
Thermoforming can produce plastic parts at high speeds with minimal need for human intervention, fostering efficiency in large-scale operations.
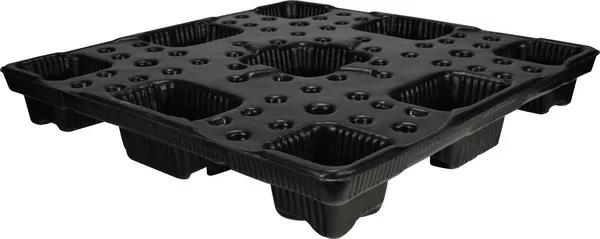
Comparative Costs
Thermoforming vs Blow Molding
When comparing the costs of thermoforming and blow molding, it becomes clear that thermoforming often has lower tooling costs as well as faster cycle times. Pieces made using this method can be cheaper by a significant amount – thanks in part to how quickly they’re produced, but also because less material is wasted throughout production cycles.
Thermoforming vs Injection Molding
Although injection molding is known for its high precision and ability to work with more materials overall, manufacturers focused on standardization or volume regularly choose thermoform over injection based on relative savings when factored against tooling, material inputs or time per unit manufactured.
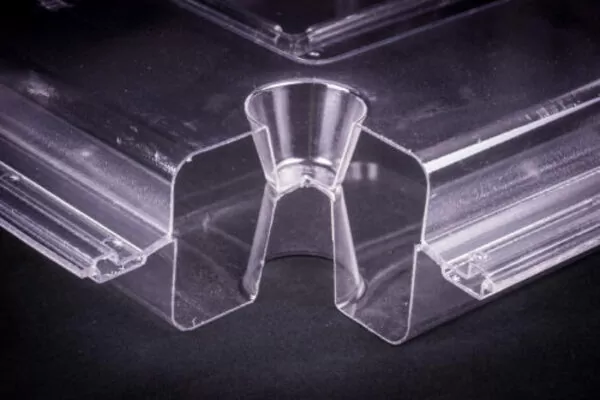
Thermoforming vs 3D Printing
Scale & cost efficiency considerations play into why large quantity runs may favor thermoformed parts instead; they both allow for customization however scalability wise there is still an advantage from matched mold forming due simply being cheaper than getting things done through additive processes while dealing better overall mass manufacturing volumes.
Materials Selection Impact
The specific plastic materials picked dramatically impact whether or not this process will prove cost-effective; each type their own unique pricing brackets plus performance aspects – which means determining final price tags besides quality levels fall onto you too!
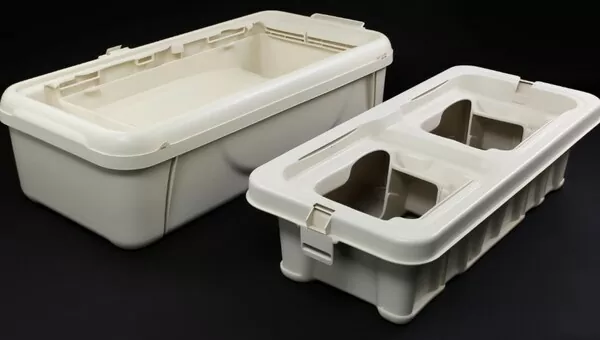
Consideration for On-Hand Materials
Keeping stockpile small & reusing what’s typically used most often are ways one might cut corners financially speaking — reduced lead times = potential bulk deals just some benefits here really.
Material Waste Reduction
By choosing right design along with best possible raws save money minimize amount thrown away thus help decrease total outlays involved during entire operation.
Designing for Efficiency
Making sure all aspects align towards achieving goals at hand so no unnecessary costs incurred important.Good Designs = Low Cost + Functionality + Aesthetics.
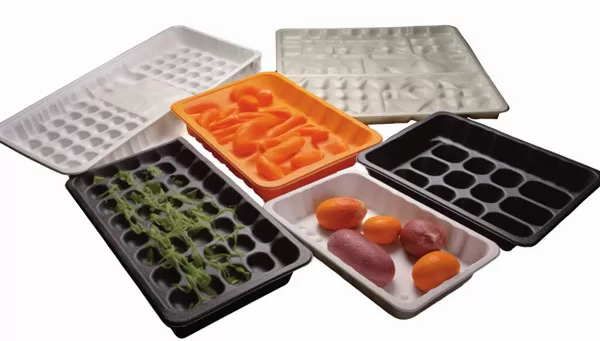
Utilizing Standard Molds and Tooling
To save on production costs, it is advisable to use standard mold sizes and tooling when possible. This will also reduce setup times and allow for faster turnarounds.
Part Consolidation
Design parts that can be combined into one using thermoforming—this reduces assembly costs and labor time too.
The Human Touch in Thermoforming
Automating as much as you can in pressure forming can help cut labor costs and make things run more smoothly but don’t underestimate the value of skilled staff members: they’ll contribute to lower scrap rates, higher yields, overall process optimization—and they’re worth every penny invested!
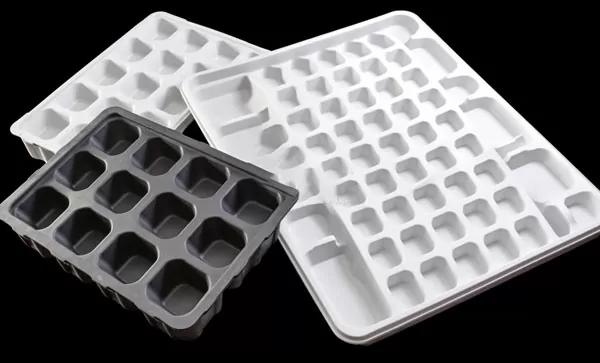
Training for Technology
Ongoing training is important; if new tools or equipment come online, ensure team members know how best utilize them (especially those related specifically thermostatic processes) so productivity levels stay up.
Production Monitoring and Optimization
Operators who are well-versed with thermoforming techniques will notice inefficiencies early on – requiring less down-time through proactive maintenance drives overall operating cost reduction significantly while simultaneously reducing unnecessary wastage by taking advantage cutting edge technology such advanced machinery monitoring software available today.
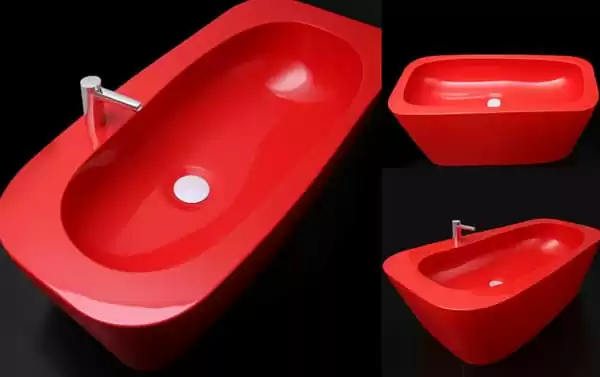
Leveraging Technology for Cost Savings
From advanced machinery to innovative software, technology is a driving force in the continual cost reduction and process improvement within the thermoforming industry.
Simulation Software
Advanced simulation software allows manufacturers to run through multiple design and material scenarios virtually, reducing the trial and error usually associated with real-world prototyping.

Energy-Efficient Machinery
Newer thermoforming machines are designed for greater energy efficiency, using heated plastic sheet and vacuum systems that save on power consumption. These machines also operate with precise controls for material distribution, cutting down on waste and associated costs.
Environmental Impact & Cost Effectiveness
Being eco-friendly isn’t just about doing right thing planet—it’s business sense too: sustainable practices like recycling packaging materials prevents unnecessary expenditure thus helping maintain positive public perception brand sustainability.
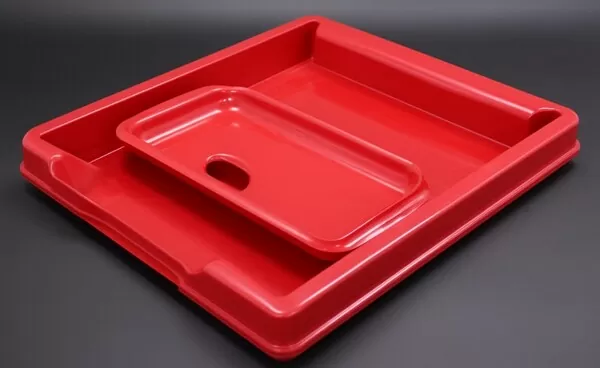
Recycling and Lower Material Costs
One way to save money on materials while also being sustainable is by using recycled materials. These can be cheaper than buying new ones, plus it means less waste going into landfill sites.
Composting and Biodegradability
Another option is to use things that can break down naturally (like plants) instead of throwing them away – this could work out cheaper too!
Regulatory Compliance and Cost Control
Sometimes you just have to make sure your products or services meet certain standards set by government bodies – if not there may be fines involved!
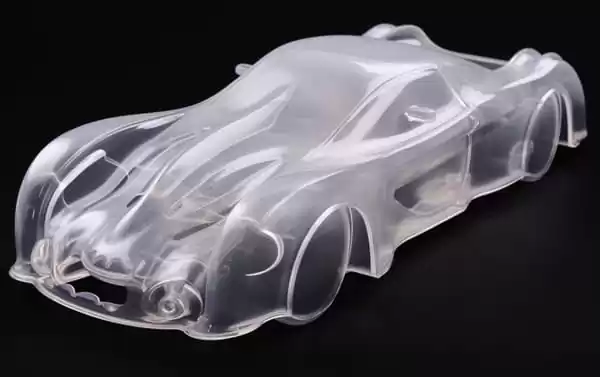
Material Safety and Health Standards
Some plastics are better for the environment than others because they contain fewer harmful chemicals. By using safer types from the start, rather than risking having products banned later on due to health concerns, companies could save money in legal fees as well as sales lost during recall periods.
Production Facility Design
If you own or rent property where goods get made then making changes such as improving lighting systems so they use less electricity might reduce costs over time since bills will go down too.
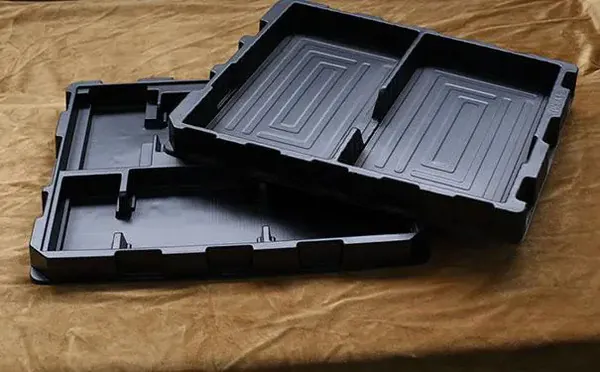
Navigating Market Fluctuations
Knowing what customers want before competitors do enables firms’ pricing strategies; this knowledge may stop them entering into price wars that erode profits unnecessarily when some higher priced product features remain desirable despite economic conditions changing rapidly else where within manufacturing sectors encompassing thermoforming process used by these organizations themselves also included within marketplace.
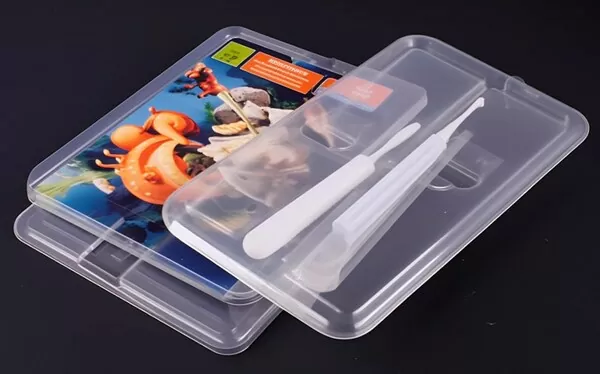
Just-in-Time Manufacturing
Companies don’t always need lots stock hanging around warehouses gathering dust waiting until people place orders – sometimes all items needed quickly once customer makes decision buy item – technique called ‘just-in-time’ means holding onto smaller quantities inventory gets ordered immediately then sent straight out from factory production line rather than sitting onsite somewhere taking up space doing nothing apart from costing its owner money through reduced available floor-space leasing costs or re-allocation efforts required should other uses desired some future point time period meantime whilst remaining unsold prior current moment.
Market Research and Flexibility
In fast changing markets where company needs keep coming new things don’t necessarily know what these will be until actually launched they may want stay ahead game by being able switch production focus at short notice – maybe even make few different items same time scale up production levels rapidly if required -without huge expense involved this kind changeover within manufacturing sector encompassing thermoforming manufacturing process covered.
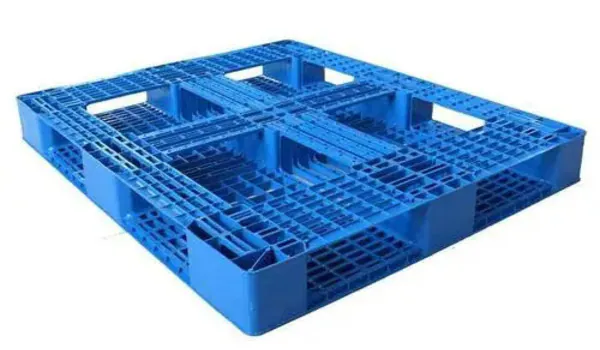
Cost-Benefit Analysis in Action
If you really want see how beneficial using thermoforming could prove your organization consider examples businesses given article that show not only did switching save them money but also improved way their operated day basis too!
Automotive Interiors
Leading automaker saves over 30% on manufacturing costs compared to injection molding by using thermoforming to produce vehicle interior components. This translates into significant overall savings without compromising quality.
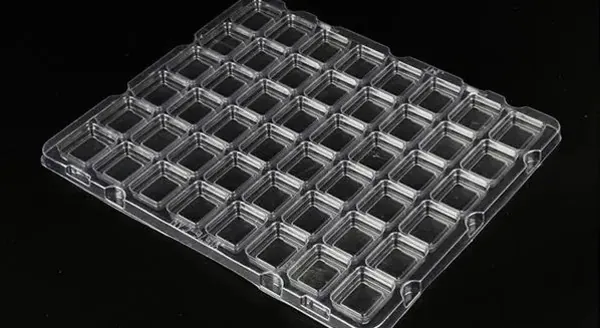
Real-Life Applications:Medical Devices
Thermoforming offers medical device manufacturers cost-efficient ways to produce products that meet strict performance standards. Instrument trays, packaging and other items can be made affordably – and at high levels of customization for different markets.
Planning for the Future of Thermoforming
Using thermoforming in your processes could give you an edge in today’s fast-changing industrial markets where every manufacturer wants a competitive advantage.
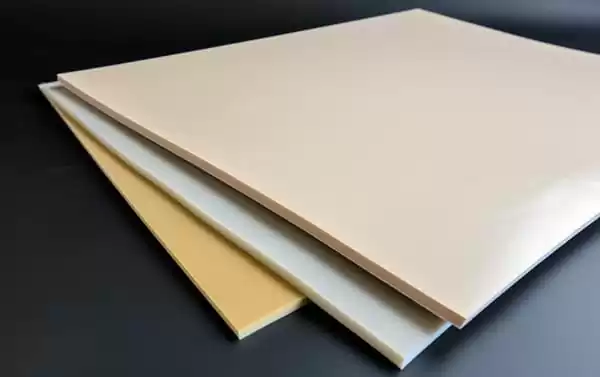
Investing in R&D
Keeping research-and-development programs up-to-date means staying ahead of competitors as new materials, machinery and methods are developed.
Promoting a Culture of Efficiency
By always trying to make things better, organizations can build upon thermoforming’s inherent strengths—and develop an overall approach that helps hold down costs all the time.
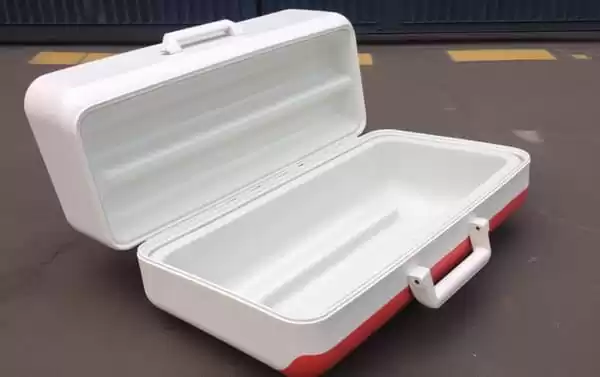
Conclusion
Understanding the financial dynamics underlying how thermoforming works is vital for companies hoping to run leaner, more affordable production lines while maintaining product quality. As this feature has shown, however, the economic advantages are only part of why so many manufacturers across sectors believe it offers them a sustainable future — one that allows them to stay agile, keep costs under control and turn out top-notch items at low prices. Armed with knowledge about its financial pluses too (and see above): Who wouldn’t want something like that? To achieve greater cost efficiency, it is important to thoroughly understand the plastic molding processes. This can be done by carefully examining material choices, refining design methods or using new manufacturing technology.