Packaging plays a vital role in product design. From a certain perspective, it is usually the first thing customers see, but the importance of packaging to a product is sometimes overlooked. In a crowded market, products that can stand out play a huge role in product sales. Thermoformed packaging is growing in popularity due to its sustainability, versatility and ability to enhance the shelf appeal of almost any kind of merchandise.
Unlike mold injection or other complex processes, thermoforming molds plastic sheets with ease, creating a practical packaging solution for a wide range of industries. In this blog post, we’ll explore exactly what thermoforming is; which products it works best with, and how this technology is shaking up the packaging world like never before.
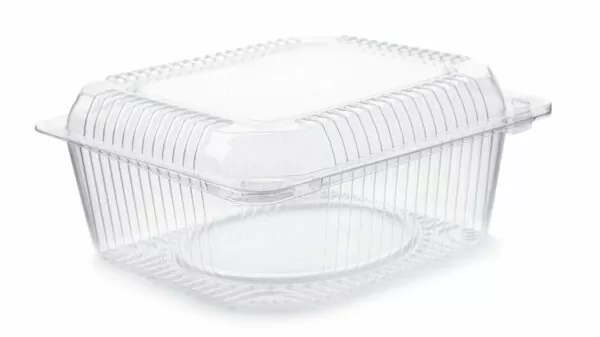
The Thermoforming Advantage
Thermoforming is a key player in the packaging industry for many reasons. Its ability to create durable and attractive packaging at a lower cost than competing methods has made it popular with companies making everything from electronics to candy bars. Additionally, thermoforming machines excel at customization, making containers in multiple shapes or sizes based on the customer’s needs; something that would not be possible using alternative technologies such as injection molding alone.
Key Benefits of Thermoforming
Sustainability: Thermoformed packaging is made from recycled materials and is itself fully recyclable, making it a sustainable choice.
Protection: The robustness of thermoformed packaging means anything they contain will be well protected during transport or when displayed in stores.
Visibility: Vacuum forming process can produce packaging with good transparency. The contents of these packages can be easily seen, which is an important selling point for shoppers.
Customizability: The thermoforming manufacturing process allows for a high degree of customization, including color, texture, size, and more.
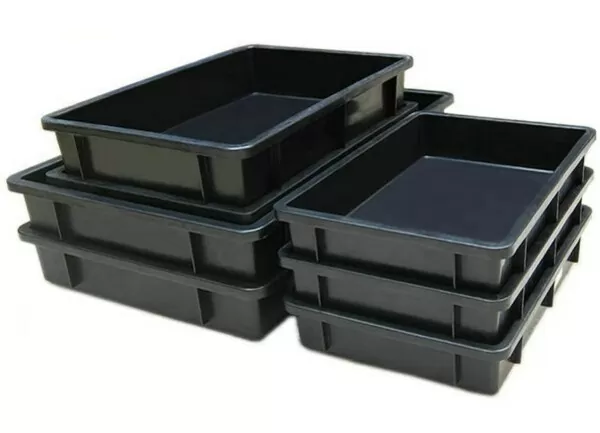
What is Thermoformed Packaging?
Thermoforming is a production technique that involves heating a plastic sheet until it is malleable, shaping it using custom molds, and then trimming it to create the finished product. This process can use a variety of plastics, including polyethylene (PE), polypropylene (PP), and polyvinyl chloride (PVC). Its main advantages are speed and cost; additionally, there is no limit to the level of detail that can be achieved. Most thermoformed blister packaging is designed for single-use applications and its life cycle ends with consumer disposal or recycling.
Why Thermoformed Packaging?
Customizability: Thermoformed packaging can be designed to fit the exact dimensions of your product, making it ideal for any shape of item.
Advantages: With the right materials chosen, thermoformed packaging can protect delicate products from everything from rough handling during shipping to exposure to changing weather conditions. If you want your goods to reach your customers safely, this is an option worth seriously considering.
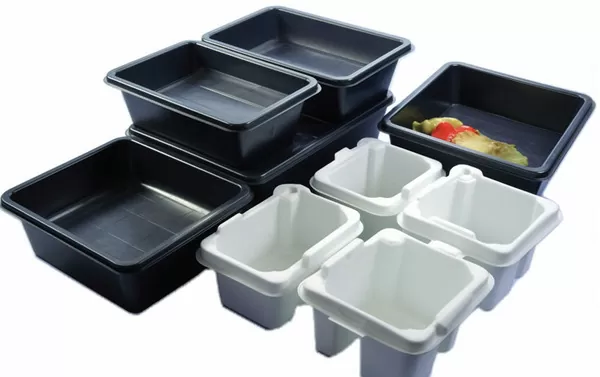
Environmentally Friendly Options: Biodegradable plastics are increasingly being used in thermoforming applications, which means business efforts are being aligned with broader sustainability commitments, providing options that align with sustainability efforts.
Application of Thermoforming Packaging
Thermoformed plastic packaging is suitable for almost any industry. The following are some representatives of thermoforming packaging application areas:
Food and Beverage
Thermoforming is an excellent choice for food packaging and beverage packaging as it provides them with fresh, safe and convenient packaging solutions. Thermoforming can provide packaging for food products and more with a sterile barrier that protects contents from air and moisture. This means food stays fresher longer! Thermoformed products can also be customized to perfectly fit a brand’s needs while still allowing consumers to visually see what they are purchasing, making thermoforming suitable not just for salads but also for things like candy bars, fruit, and more.
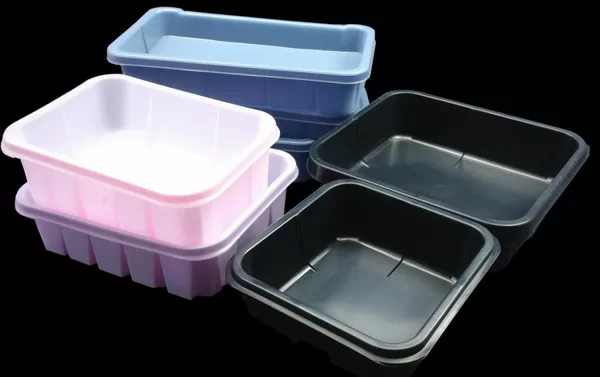
Medical and Pharmaceutical
In the medical and pharmaceutical fields, there is no compromise on precision, cleanliness and compliance. Thermoformed packaging offers a safe way to package items such as medical equipment or pharmaceuticals while also making them easy to dispose of properly afterwards! At the same time, the visual clarity and precise details of thermoformed packaging make it easier for consumers to read instructions and expiration dates. On the other hand, creating medical packaging also requires ensuring that your packaging company operates in a clean environment. Requires an ISO Class 8 cleanroom environment with HEPA filtration and positive pressure HVAC system
Consumer Goods
Thermoforming enables products to be custom-fitted to size, making them both safe and visually appealing. In addition, thermoformed plastics allow packaging company to design beautiful transparent packaging to display their goods, which is a huge advantage in industries such as consumer electronics or cosmetics, where buyers want to have as much information as possible up front.
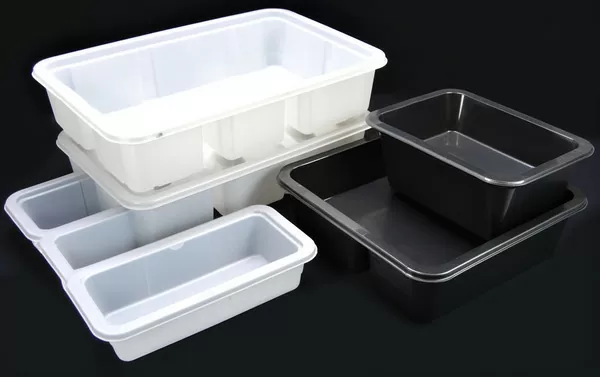
Electronics and Gadgets
In the competitive world of electronics sales, products must be eye-catching while being packaged compactly and securely. Pressure forming process can customize plastic trays to keep delicate items safe during travel, and it can provide a platform to display electronics to emphasize their stylish design.
Automotive Parts
Thermoforming is the perfect solution for automotive packaging as it can handle complex shapes and require precise fits. When parts are put into this type of packaging, there is no need to worry about them getting bumped during shipping.
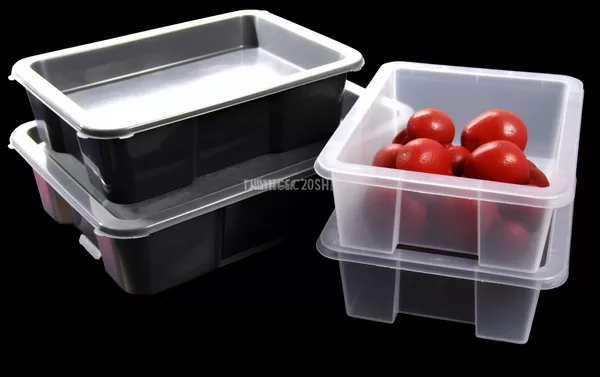
The Shift Toward Sustainable Thermoformed Packaging
The packaging industry is changing as demands for environmental responsibility continue to increase, and thermoforming is experiencing similar changes. Companies are starting to look into biodegradable materials as well as plant-based plastics when considering packaging materials.
Biodegradable Materials
For example, PLA (polylactic acid) is used in thermoforming as an environmentally friendly alternative to regular plastics. Because PLA comes from renewable resources like sugar cane or cornstarch, it can be composted under the right conditions.
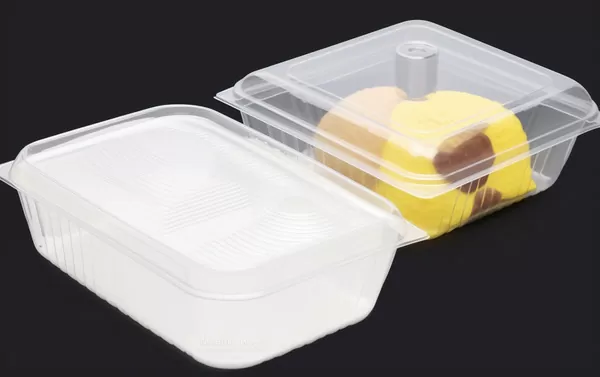
Recycled Plastics
For example, to increase the reusability of plastics, consider thermoforming with post-consumer recycled (PCR) content: it helps reduce the need for virgin plastic while rejuvenating waste materials, reducing their entry into landfill waste at a site or elsewhere.
Design for Disassembly
You can create thermoformed packaging that is easily recyclable if you consider its end-of-life options during the design process. Using materials that can be easily separated and avoiding mixing different types of plastics together are two ways to achieve this, both of which help streamline the process and therefore make it more efficient.
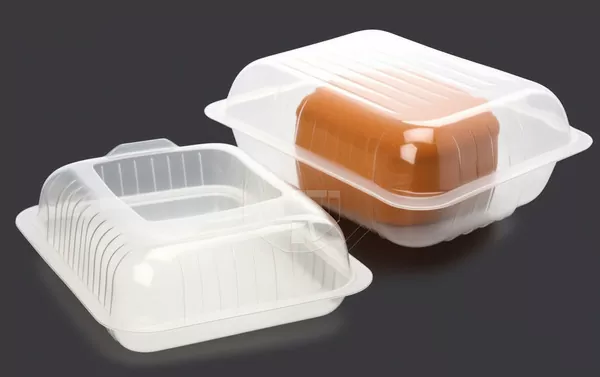
The Future of Thermoformed Packaging
The rise of consumer environmental awareness is an undeniable force that will influence the future of packaging. Thermoforming has emerged as a sustainable option to provide recyclable plastic materials ready to meet these requirements and more, especially as biodegradable plastics and waste reduction processes continue to develop. Therefore, expect continued interest from packaging team of manufacturers looking for options they will feel good about over time.
The development of thermoformed packaging technology continues unabated. There are always fresh materials, new machinery and innovative processes emerging to provide a better tomorrow for this type of packaging.
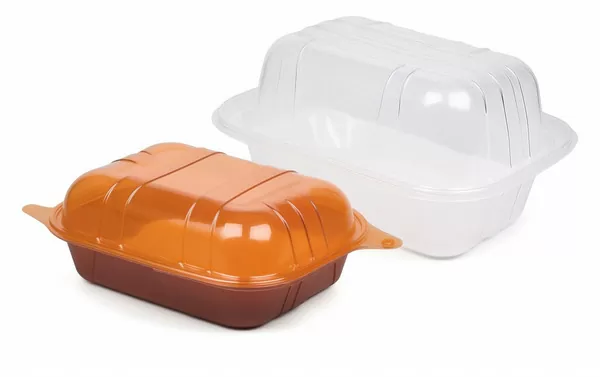
1. 3D Printing and Prototyping
An exciting example is 3D printing. From a commercial perspective, by enabling rapid prototyping, it significantly reduces the time and cost required to bring innovative packaging designs onto ships. In fact, it provides an excellent way to test different molds or shapes before making an expensive commitment to mass production.
2. Automation
Robotics and automation continue to advance the thermoforming process, making it faster and enabling mass customization. Automated systems also help ensure quality so every package is perfect.
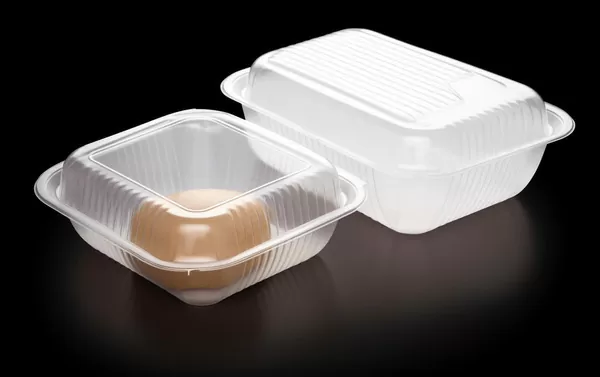
3. Mixed Material Packaging
Future thermoforming could be done using mixed materials, for example, to embed electronic components into packaging. This enables interactive elements (such as displays) or information capabilities (such as sensors). It also means there will likely be new ways to market products and get consumers to interact with them after purchase.
4. Innovations in Thermoforming
Given the dominance of thermoforming in certain areas, it is an area where manufacturers are always keen to innovate and improve. They do this by researching new materials, building better machinery than ever before, and figuring out ways to make more customized or automated products.
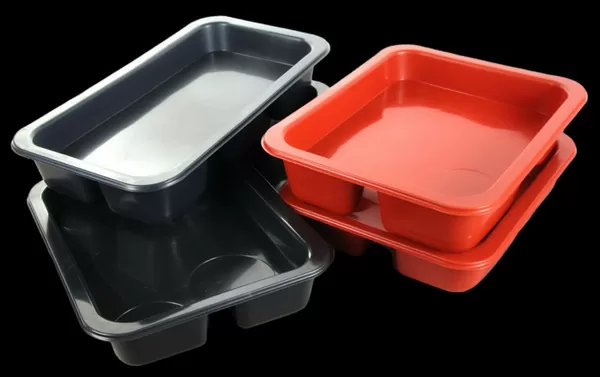
How to Choose the Right Thermoforming for Your Product
If you want to make the right choice about packaging, it’s important to get help from someone who knows what they’re doing. You need someone with expertise in the field, someone who can take into account all the factors that make your product different from everyone else’s. Discussing factors such as the environment the product will be exposed to, shipping conditions, and the level of visibility and interaction required will help determine the best thermoforming method for your business.
Points to Consider When Thermoforming
Material Selection: Material selection is a key factor in determining packaging strength, recyclability and even transparency.
Design: Make sure any design you use appeals to shoppers while adequately protecting your content.
Functional Considerations: Thermoformed packaging requires careful consideration. Does it require a specific type of opening or specific in-package functionality? These requirements often determine the choice between competing formats, all made of plastic, as they are vacuum formed.
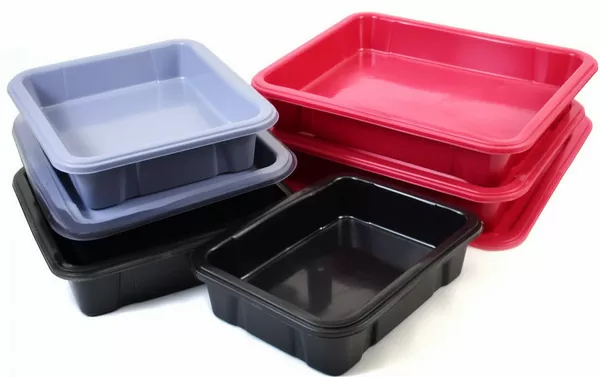
Conclusion
Thermoforming is an adaptable packaging solution that offers numerous advantages for many different types of products. Whether it’s protecting delicate electronics or improving the aesthetics of premium chocolate, thermoforming has a variety of uses in the packaging industry, and its importance becomes increasingly apparent as our world focuses on sustainability and personalization. It will only increase.
Overall, thermoformed packaging can offer many different types of products. It can be adapted and changed in many interesting ways, especially in terms of being more environmentally friendly. If you are considering thermoformed packaging for your items, this article should help you determine if it is suitable. Whether it’s food that needs to stay fresh, cool and safe during transport, or consumer electronics that need to demonstrate their functionality; thermoformed packaging may well be just what your goods need; both protective and aesthetically pleasing.
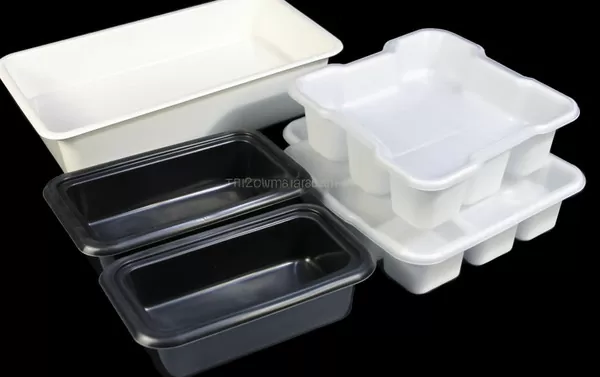
By determining which products would benefit most from thermoforming and monitoring changes in materials and technologies, companies can stay ahead of the curve in the market. This means that thermoforming is not just something that is used to package goods well, but becomes part of an overall strategy: it has the potential to enhance both the brand itself and individual products!