Introduction
Vacuum forming is a manufacturing process that uses vacuum pressure to shape thermoplastic plastic sheet into desired shapes by heating and shaping. It is commonly employed to manufacture plastic parts and products across numerous industries. Materials chosen for vacuum forming play a vital role in its success as they can impact the quality and durability of the final product.
This article seeks to provide an overview of the different materials that can be used for vacuum forming, their properties, and their applications. We will also examine how temperature and pressure affect this process as well as provide details on DIY vacuum-forming machines. By the conclusion of this piece, readers should have an increased knowledge of vacuum-forming materials used for producing high-quality plastic products.

II. Vacuum Forming Process
A. Brief Overview of the Vacuum Forming Process
Vacuum forming is a process in which a thermoplastic sheet is heated until it becomes soft and malleable, then draped over a mold surface and placed into its cavity with a vacuum applied. Once this process has been completed, once cooled and solidified it can be removed from its mold and cut to shape according to your specifications.
B. Vacuum Forming Machines and Their Components
Vacuum forming machines are used to automate and enhance production efficiency in vacuum forming processes. They typically consist of a heating element, vacuum table, mold frame, and vacuum pump. The heating element heats thermoplastic sheet materials while the vacuum table and mold frame hold them in place during the vacuum forming process while creating vacuum pressure that removes air from mold cavities.

C. Types of Vacuum Forming Machines
Vacuum-forming machines come in various varieties, each offering distinct advantages and drawbacks. Industrial vacuum forming machines are built for high-volume production by large manufacturers while DIY models offer smaller and more affordable alternatives that make them popular among hobbyists and small businesses alike. Other types of vacuum forming machines available include pressure forming devices which use additional pressure to shape plastic products while structural foam machines add structural foam material into plastic to strengthen products further.
III. Materials Used in Vacuum Forming Process
A.Vacuum Forming Materials A. Suitability for Vacuum Forming Applications
Plastic materials commonly used for vacuum forming include high-density polyethylene (HDPE), polyethylene terephthalate glycol (PETG), polycarbonate (PC), polypropylene (PP), and acrylonitrile butadiene styrene (ABS). Ideal materials should have heat stability, high impact strength, chemical resistance, and the capacity to stretch without breaking.
B. Plastic Materials Used in Vacuum Forming
PETG and ABS plastic materials are two popular choices when it comes to vacuum forming due to their ease of use, versatility, and affordability. PETG is often chosen due to its clarity; while ABS is often utilized as vehicle parts and toys due to its strength.
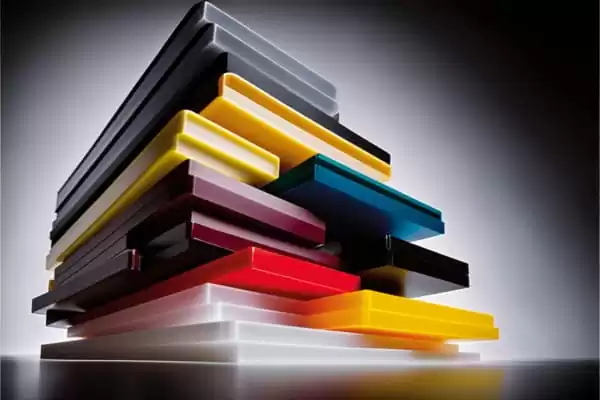
C. Advantages and Disadvantages of Different Plastic Materials
Different plastics offer distinct advantages and disadvantages when used for vacuum forming, such as HDPE which is known for its toughness and chemical resistance but lacks UV resistance, making it difficult to form. By contrast, lightweight PP plastic has strong chemical resistance but may not be as strong. Polycarbonate boasts superior impact resistance while being transparent but more expensive.
D. Thickness for Vacuum Forming Materials
The optimal thickness for vacuum-forming materials depends on both the material chosen and desired shape of the product being created. Thicker materials tend to work better when it comes to larger products with more complex shapes; thinner ones may work best with simpler shapes or thin walls. Vacuum forming materials typically range from 0.5mm-6mm depending on the application and material being used.
IV. Clear Plastic for Vacuum Forming process
A. Properties of Clear Plastic Used in Vacuum Forming
Clear plastic materials are often chosen for vacuum forming due to their transparency, which enables easy inspection of finished products. Ideal materials should possess superior optical clarity, impact resistance, and high dimensional stability for this process.
B. Different Types and Applications of Clear Plastic and Their Benefits
There are various clear plastic materials used for vacuum forming, including PETG, polycarbonate, and acrylic. PETG is often chosen due to its clarity and lower cost; polycarbonate stands out due to its impact strength, heat, and chemical resistance as well as weatherproof properties; while acrylic may be suitable for applications requiring optical clarity with weather resistance requirements like light diffusers.
C. Applications of Clear Plastic in Vacuum Forming
Clear plastic materials can be found in many applications, from food packaging to medical equipment and electronics. Food industry applications of clear plastic include food containers; medical applications include packaging for medical supplies and skid plates; as well as production of machine guards and electrical enclosures due to their optical clarity and fire retardancy properties.
V. HDPE in Vacuum Forming
A. Properties of HDPE for Vacuum Forming
High-density polyethylene (HDPE) plastic material is widely utilized in vacuum forming due to its outstanding chemical resistance, toughness, and impact strength. HDPE’s versatility enables its use for various applications like food packaging, storage containers, vehicle parts, and much more makes vacuum forming.
B.Advantages and Disadvantages of HDPE Film
One of the many advantages of HDPE for vacuum forming is its chemical resistance, making it a suitable material for storage containers of corrosive substances. Furthermore, HDPE offers excellent toughness and impact strength making it suitable for vehicle parts requiring durability. Unfortunately, HDPE may not be ideal when dealing with high levels of detail or sharp corners due to being difficult to mold into complex shapes.

C. Applications of HDPE in Vacuum Forming
HDPE plastics are widely utilized across a range of applications, from food storage containers to vehicle parts. Food manufacturers rely on HDPE storage containers due to their chemical and moisture resistance; in manufacturing industries like car production, they utilize its toughness and impact resistance in producing vehicle parts such as bumpers, fenders, underbody covers, and bumper covers due to toughness or toughness; also it is widely utilized by construction industries for producing rigid pipes or medical industries for producing medical equipment.
VI. Temperature and Pressure in Vacuum Forming
A.Temperature and Pressure Conditions Are Vital Components in Vacuum Forming Process
Temperature and pressure play an integral role in vacuum forming, as they have the power to significantly impact product quality and durability. Heating temperature must be high enough to soften thermoplastic material without melting it completely; while pressure applied to mold must force plastic material to conform to its surface without tearing or distorting its shape.
B. Recommended Temperature and Pressure Conditions for Different Plastic Materials
Forming temperature and pressure requirements for different plastic materials depend upon their type and thickness; typically 320degF to 400degF is recommended for most materials; thicker ones may need higher temperatures. When it comes to mold pressure applications, 10-30psi should provide optimal results depending on the material and desired detail levels.
C. Understand Different Types of Pressure Forming Solutions
Pressure forming is another form of the plastic part-forming process used to produce plastic components. Pressure forming utilizes both vacuum and pressure to form plastic material into molds, producing products with more detailed features and smoother finishes than vacuum forming would. It is most suitable for intricate designs requiring greater accuracy or precision; however, additional equipment and costs tend to make pressure forming more expensive than its vacuum counterpart.
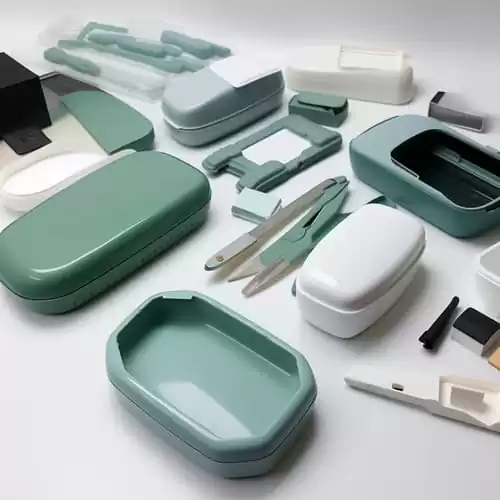
VII. Common Applications of Vacuum Forming
A. Vacuum Formed Products Examples
Vacuum forming is a widely used manufacturing technique used to produce plastic products such as trays, packaging materials, automotive parts, signs, and toys. In addition, vacuum forming is frequently employed for producing medical equipment, machine guards, and electrical enclosures.
B. Industries That Employ Vacuum Forming
Vacuum forming can be found across a wide range of industries, such as food packaging, automotive, medical, and electronics manufacturing industries. Furthermore, vacuum forming can also be found used to manufacture industrial products like machine guards, skid plates, and equipment housings.
C. Advantages of Vacuum Forming for Mass Production
Vacuum forming is an economical and efficient manufacturing method designed for mass production. It enables designers to quickly form complex shapes out of different materials quickly and economically; mass-producing parts quickly is another advantage, as is creating large numbers of identical parts at low costs – ideal for high-volume runs! Furthermore, vacuum forming allows manufacturers to produce products with different properties or characteristics with this versatile process.
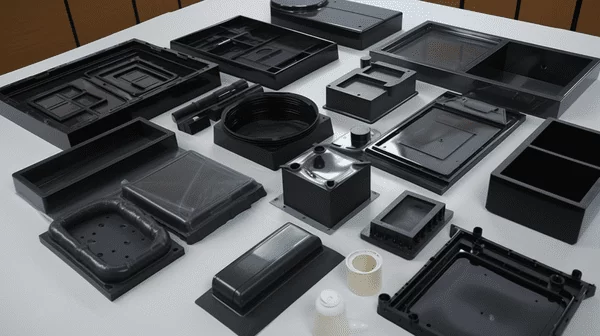
VIII. DIY Vacuum Forming Machines
A. Introduction to DIY Vacuum Forming Machines
DIY vacuum-forming machines provide an affordable alternative to industrial machines, making them popular among hobbyists and small businesses alike. Generally smaller in size and less complex than industrial models, DIY machines can still produce high-quality plastic parts and products; often made out of wood or metal and powered by either a vacuum pump or household vacuum cleaner.
B. Cost-Effective Alternatives to Industrial Machines
DIY vacuum forming machines provide a cost-effective alternative to industrial machines that are both costly and require specialized skills for operation. Ideal for short production runs and tailored specifically to specific applications and requirements, DIY machines tend to be smaller and more portable compared to their industrial counterparts; making them suitable options for those with limited space.
C. Steps for Building a DIY Vacuum Forming Machine
Building a DIY vacuum forming machine requires knowledge of woodworking or metalworking as well as basic electrical skills, as well as careful design planning and selecting suitable materials to ensure its safety and effectiveness. Some tips for building such machines include using ceramic heaters for warming plastic material, vacuum pumps or household vacuum cleaners for creating vacuum pressure, machined aluminum mold surfaces for optimal heat distribution, as well as safety features that disable heating elements should they overheat, well ventilation and safety features such as switches that turn off heating elements should they overheat during operation.
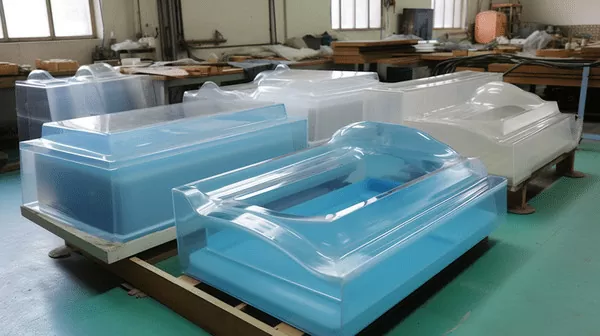
Conclusion
Overall, this article explored the vacuum forming process and highlighted its significance when selecting appropriate materials for this manufacturing technique. We examined different plastic materials commonly used for vacuum forming such as clear plastic and HDPE as well as their advantages and disadvantages; temperature and pressure are also discussed to highlight how these factors may influence final products; common applications of vacuum forming were discussed as well as benefits associated with mass production using this manufacturing technique; finally, we discussed building your own DIY vacuum forming machine as a cost-cutting alternative to industrial machines.
Selecting appropriate materials for vacuum forming is crucial to producing products that meet desired specifications and requirements. Careful selection can enhance the vacuum-forming plastics process and result in high-quality parts or products. When selecting materials it is also important to take note of the temperature and pressure needed to achieve your desired outcomes.
Vacuum forming is a highly flexible and cost-effective manufacturing method with multiple applications. From small-scale production runs to mass production runs, selecting appropriate materials and understanding the vacuum forming process can help optimize production for optimal results.