Introduction:
Molding processes play a vital role in the whole manufacturing process of plastic products, enabling the creation of diverse and functional items that are used in numerous industries. From packaging materials to intricate plastic parts, molding processes provide the means to shape and form plastic materials into desired objects. Among the various molding techniques available, vacuum forming emerges as a cost-effective solution that offers numerous advantages. In this article, we will explore why vacuum forming is considered a cost-effective option for plastic manufacturing and how it has become a preferred choice for many industries.
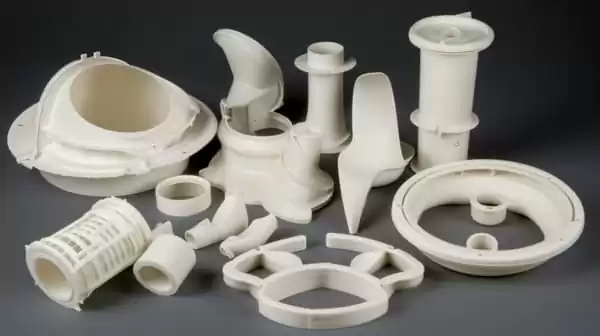
II. Vacuum Forming Process and Advantages of vacuum forming process
A. Explanation of the Vacuum Forming Process:
Vacuum forming, also known as thermoforming, is a plastic molding process that involves several key steps:
1.Heating the Thermoplastic Sheet:
The process begins with a flat thermoplastic material or sheet, which is commonly made of materials such as ABS, polycarbonate, or PVC.
The sheet is heated until it reaches a pliable state, allowing it to be easily shaped and formed.
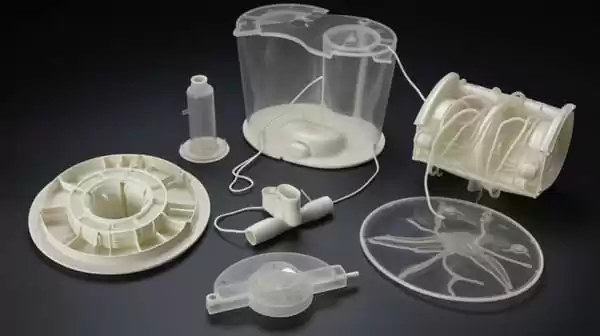
2.Drawing the Sheet Over a Mold Using Vacuum Pressure:
Once the thermoplastic sheet is heated, it is carefully positioned over a mold.
The mold can be made from various materials, including wood, epoxy, or even 3D-printed materials, which helps reduce tooling costs.
A vacuum is applied to plastic material beneath the mold, which creates a pressure differential.
The back vacuum pulls air from the heated sheet tightly against the mold’s contours, causing it to take the shape of the mold.
B. Advantages of Vacuum Forming Compared to Injection Molding:
1.Lower Tooling Costs and Faster Prototyping:
Vacuum forming utilizes less expensive molds compared to injection molding.
The molds can be produced more quickly and cost-effectively, allowing for faster prototyping and shorter lead times.
This makes vacuum forming an ideal choice for small-scale productions, prototypes, and projects with shorter timelines.
2.Versatility in Material Selection and Cost Efficiency:
Vacuum forming offers versatility in material selection, accommodating a wide range of thermoplastic materials.
Manufacturers can choose materials based on specific requirements, such as strength, transparency, or impact resistance, without incurring additional costs associated with material compatibility.
This versatility makes vacuum forming a cost-effective option for producing plastic components with varying material properties.
Reduced Energy Consumption and Manufacturing Costs:
Vacuum forming generally requires less energy consumption compared to high-pressure processes like injection molding.
The absence of high temperatures and lower molding pressures contribute to reduced energy requirements.
This energy efficiency translates into cost savings, making vacuum forming an economically viable choice.
Additionally, the streamlined production processes of vacuum forming, including simplified mold production and minimal manual labor, further contribute to lower manufacturing costs.
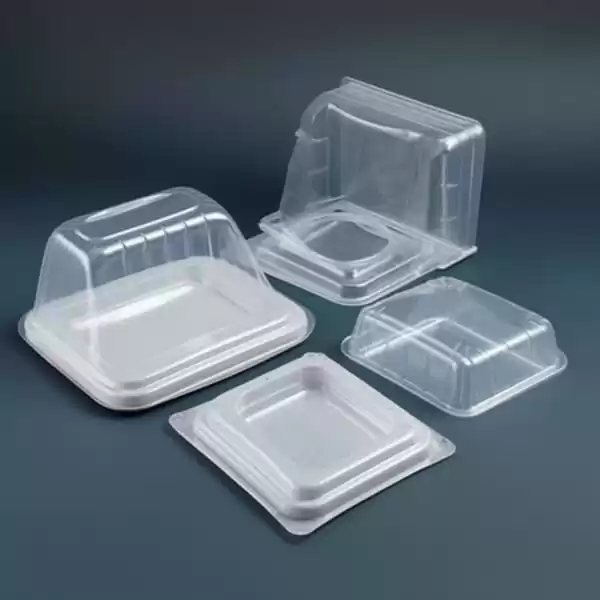
By understanding the vacuum forming process and the advantages it offers, manufacturers can make informed decisions about selecting the most cost-effective injection molding tooling method for their specific needs. The lower tooling costs, faster prototyping, versatility in material selection, reduced energy consumption, and overall manufacturing cost efficiency make vacuum forming an attractive option in the realm of plastic molding.
III. Cost Comparison: Vacuum Forming vs. Injection Molding
When considering the cost-effectiveness of molding processes, it is essential to compare vacuum forming and injection molding, two commonly used methods in the plastic manufacturing industry. Several factors influence the overall costs associated with each process, including tooling costs, material selection, and production volume.
Tooling Costs:
Vacuum forming generally incurs lower tooling costs compared to the injection molding process.
Vacuum forming molds can be made from less expensive materials, such as wood, epoxy, or 3D-printed materials, which reduces upfront tooling expenses.
In contrast, injection molding requires precision steel molds, which are more expensive and time-consuming to produce.
The lower tooling costs of vacuum forming make it an attractive option for small-scale productions, prototypes, or projects with limited budgets.
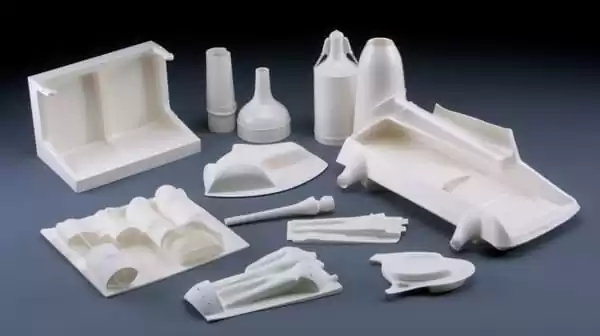
Material Selection:
Both vacuum forming and injection molding offer versatility in material selection, allowing manufacturers to choose from a wide range of thermoplastic materials.
However, injection molding may have an advantage when it comes to high-performance or specialized materials that require higher temperatures or pressure during the molding process.
Vacuum forming, on the other hand, provides cost efficiency in material selection, as it allows for the use of less expensive thermoplastics without compromising quality.
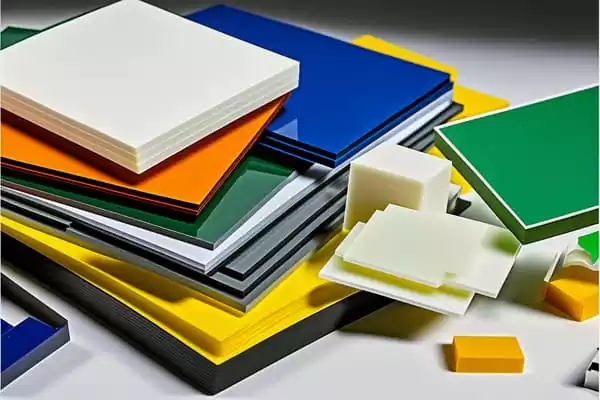
Production Volume:
Injection molding excels in high-volume production scenarios.
Once the first injection molding machine is created, it enables the rapid and efficient production of identical parts at a relatively low cost per unit.
Vacuum forming is more suitable for low to medium production volumes, making it ideal for small-batch orders, prototypes, or customized products.
The ability to produce large parts in a single operation without the need for assembly or joining of multiple components adds to the cost efficiency of the vacuum forming machine.
When comparing the overall costs of vacuum forming and injection molding, it is crucial to consider the specific requirements of the project. For small-scale productions, prototypes, or projects with limited budgets, vacuum forming offers significant cost advantages due to its lower tooling costs and material flexibility. On the other hand, injection molding shines in high-volume production scenarios, where the cost per unit decreases due to economies of scale.
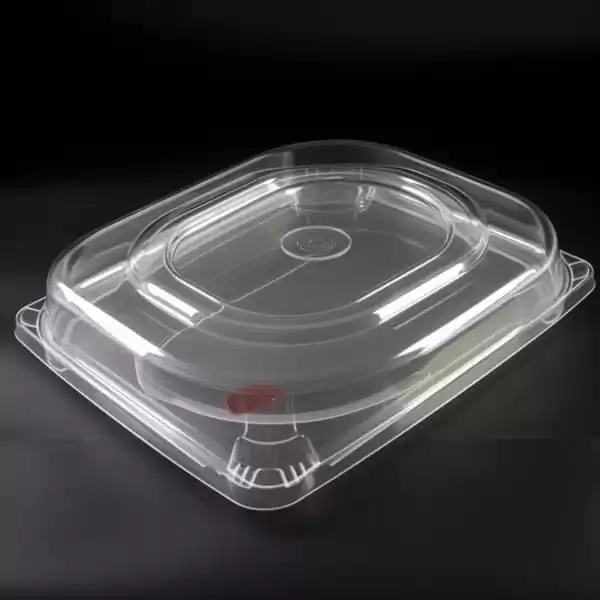
Manufacturers must carefully evaluate their production volume, material requirements, and budget constraints to determine which process is the most cost-effective for their specific needs. By assessing these factors and understanding the cost differences between vacuum forming and injection moulding, businesses can make informed decisions and optimize their plastic manufacturing processes.
IV. Advantages and Disadvantages of Vacuum Forming
A. Advantages
Lower Tooling Costs:
Vacuum forming offers lower tooling costs compared to processes like injection molding.
The molds used in vacuum forming can be made from less expensive materials such as wood, epoxy, or 3D-printed materials.
This cost advantage makes vacuum forming an attractive choice for small-scale productions, prototypes, and projects with limited budgets.
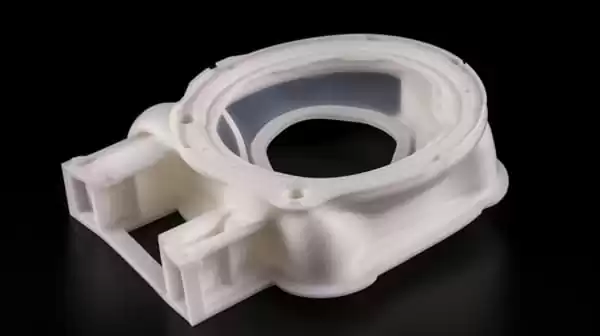
Faster Prototyping and Setup:
Vacuum forming enables quicker prototyping and setup compared to other molding processes.
The simplicity of the molds used in vacuum forming allows for rapid modifications and adjustments, reducing lead times and speeding up the product development cycle.
Manufacturers can iterate and refine their designs more rapidly, saving time and resources.
Versatility in Material Selection:
Vacuum forming offers versatility in material selection, accommodating a wide range of thermoplastic materials.
Manufacturers can choose materials based on specific requirements such as strength, transparency, or impact resistance without incurring additional costs associated with material compatibility.
This flexibility allows for the production of diverse plastic products, catering to various industries and applications.
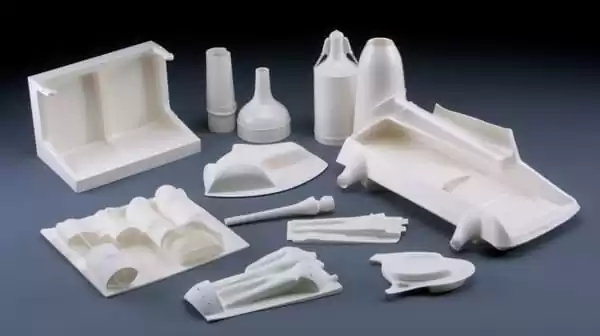
Reduced Energy Consumption:
Vacuum forming generally requires lower energy consumption compared to high-pressure processes like injection molding.
The absence of high temperatures and lower molding pressures contribute to reduced energy requirements.
This energy efficiency not only lowers manufacturing costs but also aligns with sustainable manufacturing practices.
Lower Production Costs:
Vacuum forming’s simplified production processes and lower tooling costs result in lower overall production costs.
Fewer production steps and minimal manual labor reduce labor costs and increase production efficiency.
The ability to produce large parts in a single operation eliminates the need for assembly or joining of multiple components, further reducing costs.
B. Disadvantages
Limited Precision and Detail Compared to Injection Molding:
- Vacuum forming may have limitations in achieving the same level of precision and intricate detail as injection molding.The nature of the process and the flexibility of the heated plastic sheet can result in slight variations or imperfections in the final product.
- Unsuitable for Complex or Intricate Designs:Vacuum forming may not be the best choice for complex or highly intricate designs that require very fine details.The process is better suited for products with relatively simple geometries and contours.
- Limitations in Producing Parts with Uniform Wall Thickness:Vacuum forming may result in variations in wall thickness, particularly in deep-drawn parts or large areas of the formed product.Achieving consistent wall thickness throughout the product can be challenging in vacuum forming.
Understanding the advantages and disadvantages of vacuum forming is crucial in determining its suitability for specific applications. While vacuum forming offers cost advantages, faster prototyping, and material versatility, it may not be suitable for projects with strict precision requirements or complex designs. By considering these factors, manufacturers can make informed decisions and leverage the benefits of vacuum forming while acknowledging its limitations.
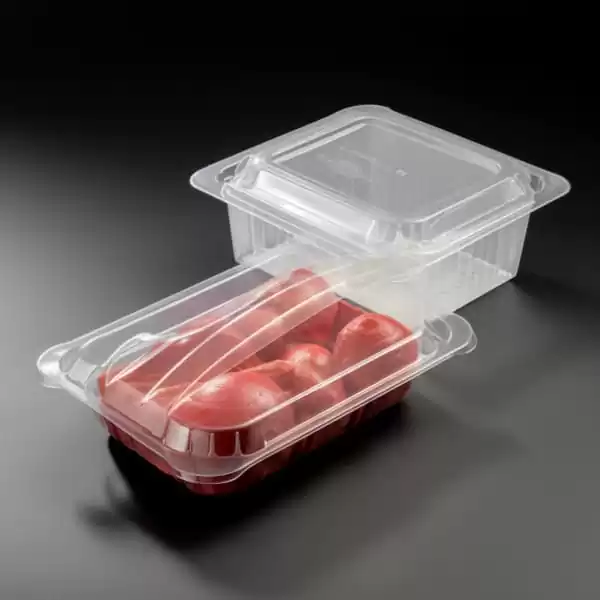
Conclusion
In conclusion, vacuum forming emerges as a cost-effective and versatile molding process for producing high-quality plastic components. Its advantages in terms of cost-effectiveness, lower tooling costs, faster prototyping, versatility in material selection, reduced energy consumption, and lower production costs make it an attractive option for manufacturers across various industries.
The cost advantages of vacuum forming, including lower tooling costs and simplified production processes, make it accessible for small-scale productions, prototypes, and projects with limited budgets. Additionally, the ability to choose from a wide range of thermoplastic materials provides flexibility and cost efficiency in material selection, catering to diverse industry needs.
Furthermore, the streamlined production processes of vacuum forming contribute to reduced energy consumption, aligning with sustainable manufacturing practices. The lower energy requirements not only lower manufacturing costs but also have a positive environmental impact.
While vacuum plastic forming methods may have limitations in achieving intricate details or uniform wall thickness, its cost-effectiveness, faster prototyping, and suitability for various industries make it an attractive choice. Manufacturers should consider vacuum forming as a cost-effective molding process that provides high-quality plastic components while optimizing production costs.
By leveraging the advantages of vacuum forming and understanding its limitations, businesses can make informed decisions in selecting the most suitable and cost-effective molding process for their specific applications. Whether it’s for packaging materials, customized products, or small to medium production runs, vacuum forming stands as one of the most economical thermoforming technologies available in the plastic manufacturing industry.