Introduction
Plastic manufacturing techniques play a crucial role in today’s industrial landscape, allowing for the production of a wide range of products that we use in our daily lives. Among the various methods employed, vacuum forming and injection molding are two prominent techniques that deserve attention. Understanding these processes and comparing their advantages and limitations is essential for manufacturers and designers seeking the most suitable approach for their specific needs.
Plastic manufacturing techniques enable the creation of products across industries such as automotive, packaging, electronics, and consumer goods. Injection molding and vacuum
molding are particularly significant due to their versatility and wide-ranging applications. By exploring these processes and analyzing their unique characteristics, manufacturers can make informed decisions and achieve optimal results.
Vacuum forming involves heating a plastic sheet and using a vacuum to mold it into a desired shape. This method is often employed for low-volume production, prototyping, and the creation of larger parts or complex geometries. On the other hand, injection molding utilizes molten plastic material injected into a mold cavity under high pressure. Injection moulding offers exceptional precision, surface finish, and strength, making it suitable for high-volume production runs and intricate designs.
Comparing these two processes is crucial as it allows manufacturers to assess factors such as cost-effectiveness, production volume, material selection, surface quality, and lead times. By understanding the advantages and limitations of vacuum forming and injection molding, manufacturers can choose the most appropriate technique for their specific product requirements, production volumes, and budget constraints.
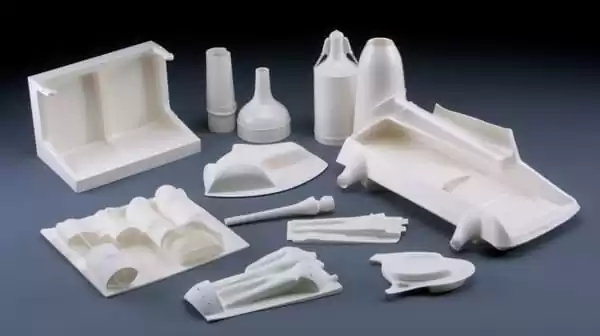
In the following sections, we will delve deeper into the intricacies of vacuum forming and injection molding, exploring their processes, advantages, and considerations. By the end of this article, you will have a comprehensive understanding of these manufacturing techniques, empowering you to make informed decisions and achieve success in your plastic manufacturing endeavors.
II. Understanding Vacuum Forming
A. Definition and Process
Explanation Vacuum forming is a plastic manufacturing process that involves heating a plastic sheet and molding it into a desired shape using a vacuum. The process begins by placing a flat plastic sheet over a mold. The sheet is then heated until it becomes pliable. Once heated, the sheet is stretched over the mold, and a vacuum is applied to remove the air between the sheet and the mold. The atmospheric pressure forces the sheet to conform to the mold’s shape, creating the desired plastic product.
B. Key Components:
Plastic Sheet, Heating, Stretching, and Vacuum forming utilizes several key components to shape the plastic sheet. These components include:
Plastic Sheet: A thermoplastic sheet is commonly used in a vacuum forming machine. Materials such as ABS, polystyrene, and PVC are popular choices.
Heating: The plastic sheet is heated using various methods, such as radiant heaters or infrared lamps. Heating makes the sheet pliable and easier to form.
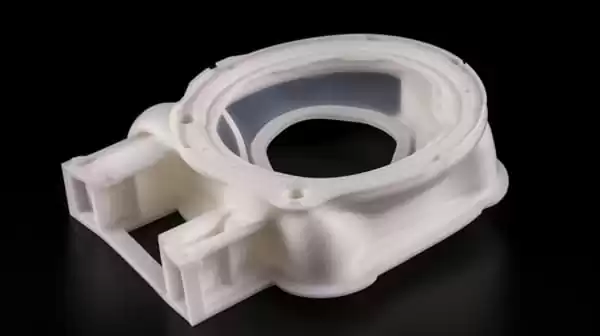
Stretching: The heated sheet is stretched over the mold using mechanical or pneumatic devices. This stretching allows the sheet to take on the used injection molding tooling’s shape.
Vacuum: A vacuum is applied between the sheet and the mold, pulling the sheet tightly against the mold’s surface and ensuring proper forming.
C. Advantages of Vacuum Forming
Vacuum forming offers several advantages as a plastic manufacturing technique:
1.Cost-effectiveness: Vacuum forming is generally a more cost-effective method compared to other various plastic forming methods and techniques, making it suitable for low-volume production or prototypes.
2.Material Versatility: Vacuum forming accommodates a wide range of thermoplastic rubber materials, allowing for flexibility in thermoplastic material selection based on the product requirements.
3.Quick Turnaround: The process of vacuum forming has relatively shorter production cycles, enabling faster product iterations, reduced time to market, and increased responsiveness to market demands.
4.Large Part Capability: Vacuum forming is capable of producing larger parts and accommodating complex shapes that might be challenging or more expensive to achieve with other manufacturing methods.
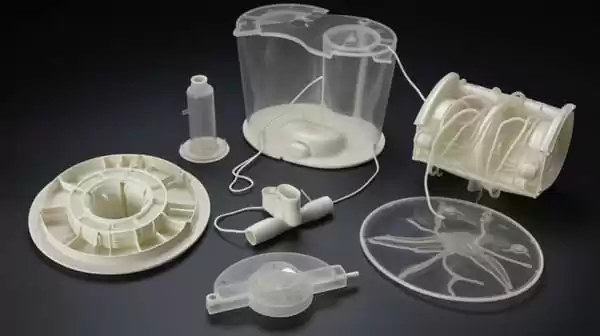
D. Limitations of Vacuum Forming
While vacuum forming offers numerous advantages, it also has certain limitations to consider:
1.Precision Limitations: Vacuum forming may not achieve the same level of precision and intricate details as some other manufacturing processes, especially for highly complex designs.
2.Material Restrictions: The suitability of materials for vacuum forming depends on their ability to withstand the heating and stretching processes. High-temperature applications or products that require extreme durability might require alternative manufacturing methods.
3.Surface Finish Considerations: Vacuum-formed parts may exhibit variations in surface finish, with a texture that may not match the smoothness and consistency achieved through other processes like injection moulding and vacuum made. Surface finish requirements should be evaluated when considering vacuum forming for specific applications.
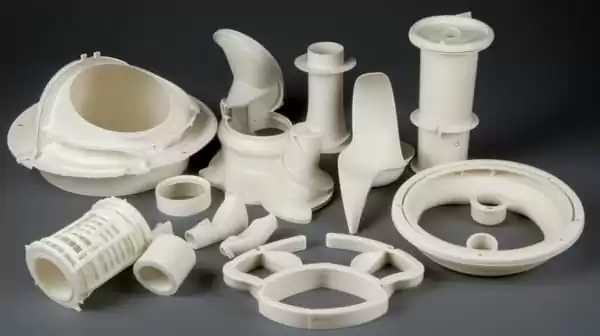
Understanding the process, advantages, and limitations of vacuum forming provides valuable insights for manufacturers seeking a cost-effective and versatile method for producing plastic parts.
III. Exploring Injection Molding
A. Definition and Process capabilities
Explanation Injection molding is a highly versatile plastic manufacturing process that involves injecting molten plastic material into a mold cavity under high pressure. The process begins with plastic pellets or granules, which are fed into a heating barrel and melted. Once the plastic is in a molten state, it is injected into a mold cavity using a plunger or screw mechanism. The molten plastic then cools and solidifies within the mold, forming the desired shape. Finally, the mold is opened, and the finished part is ejected.
B. Key Components
Plastic Pellets, Heating, Injection, and Mold Injection molding relies on several key components to shape the plastic material:
Plastic Pellets: Thermoplastic materials in the form of small pellets or granules are commonly used in injection molding. These pellets are melted and injected into the mold.
Heating: The plastic pellets are heated in a heating barrel using a combination of heating elements and mechanical shearing forces, allowing them to melt and become a viscous molten state.
Injection: The molten plastic is injected into the mold cavity under high pressure, ensuring complete filling of the mold and replicating the mold’s shape.
- Mold: The mold consists of a cavity and a core that define the final shape of the part. The mold is typically made of metal and designed to withstand the high pressures and temperatures involved in the process.
C. Advantages of Injection Molding
Injection molding offers several advantages as a plastic manufacturing technique:
- Superior Precision and Detail: Injection molding provides exceptional precision and intricate detail reproduction, making it ideal for complex designs, tight tolerances, and precise geometries.
- Excellent Surface Finish: The high pressure during injection molding ensures excellent surface finish, reducing the need for additional finishing operations.
- Durability and Strength: Injection-molded parts tend to exhibit superior strength and durability, making them suitable for applications that require robust performance.
- High-Volume Production Efficiency: Injection molding is highly efficient for large-scale production runs, ensuring consistent quality and minimizing production time per unit.
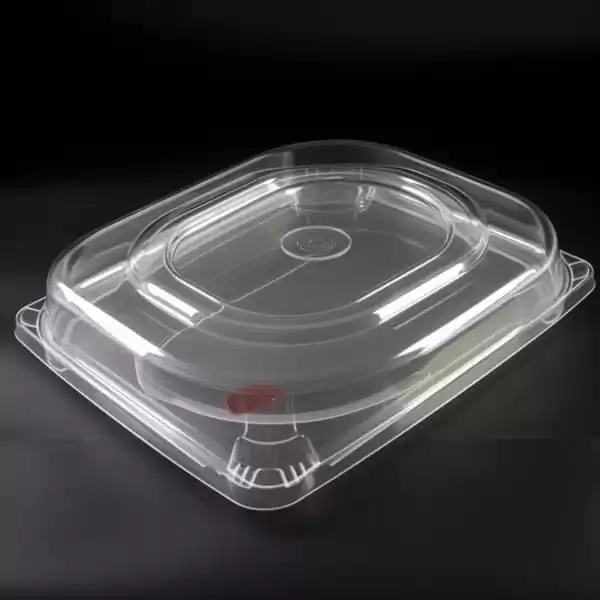
D. Limitations of Injection Molding
While injection molding offers numerous advantages, it also has certain limitations to consider:
- Higher Initial Costs: Injection molding requires higher upfront investment due to the complexity of mold design and manufacturing. This can be a barrier for smaller production volumes or prototypes.
- Design Limitations: The complex tooling required for injection molding makes it less flexible for design changes compared to other manufacturing processes.
- Longer Lead Times: Developing molds and tooling for injection molding takes time, which can lengthen the initial setup phase and lead to longer lead times for production.
Understanding the process, advantages, and limitations of injection molding provides valuable insights for manufacturers seeking precise, high-quality, and efficient production of plastic parts.
IV. Comparative Analysis: Vacuum Forming vs. Injection Molding
A. Differences between the Two Processes
- Process: Vacuum forming utilizes a heated plastic sheet stretched over a mold using a vacuum, while injection molding involves injecting molten plastic material into a mold cavity under high pressure.
- Precision: Injection molding offers superior precision and intricate detail reproduction compared to vacuum forming.
- Surface Finish: Injection molding delivers high-quality surface finishes, whereas vacuum-formed parts may have a relatively lower surface quality.
- Production Volume: Injection molding is highly efficient for large-scale production runs, while vacuum forming is better suited for smaller volumes or prototypes.
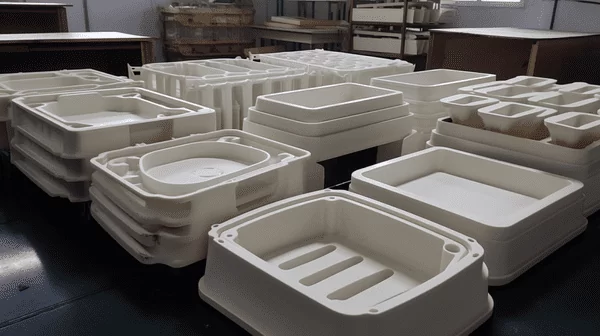
B. Cost Comparison:
Is Vacuum Forming Cheaper?
Vacuum forming is generally more cost-effective than injection molding, especially for smaller production volumes or prototyping. Vacuum forming requires less initial investment, making it an affordable option for those with budget constraints. On the other hand, injection molding involves higher setup and tooling costs, making it more viable for larger production volumes where economies of scale can be realized.
C. Advantages of Thermoforming (Vacuum Forming) over Injection Molding
- Cost-Effectiveness: Vacuum forming is generally more cost-effective, making it suitable for low-volume production runs or prototypes.
- Material Versatility: Thermoforming accommodates a wide range of materials, allowing for flexibility in material selection based on product requirements.
- Quick Turnaround: Vacuum forming has shorter production cycles, enabling faster product iterations, reduced time to market, and quicker response to market demands.
- Large Part Capability: Vacuum forming can accommodate larger parts and complex shapes that may be challenging or more expensive to produce using injection molding.
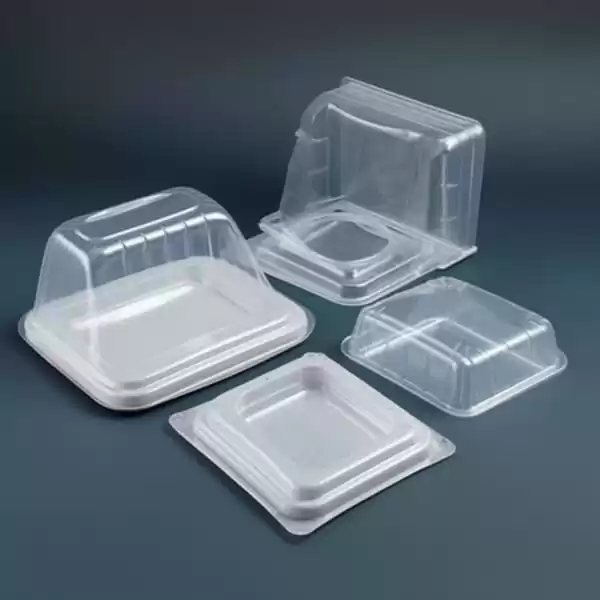
D. Comparison of Thermoforming (Vacuum Forming) Process with Injection Molding
When comparing the thermoforming (vacuum forming) process with the injection molding process, the following factors come into play:
- Precision and Detail: Injection molding provides superior precision and intricate details, especially for complex designs and tight tolerances, surpassing what can be achieved with vacuum forming.
- Surface Finish: Injection molding delivers high-quality surface finishes, eliminating the need for additional finishing operations, while vacuum-formed parts may have a relatively lower surface quality.
- Production Volume: Injection molding is highly efficient for large-scale production runs, ensuring consistent quality and minimizing production time per unit, whereas vacuum forming is better suited for smaller volumes or prototypes.
- Cost Efficiency: Vacuum forming offers cost advantages, particularly for low-volume production or prototypes, due to lower tooling and setup costs compared to injection molding.
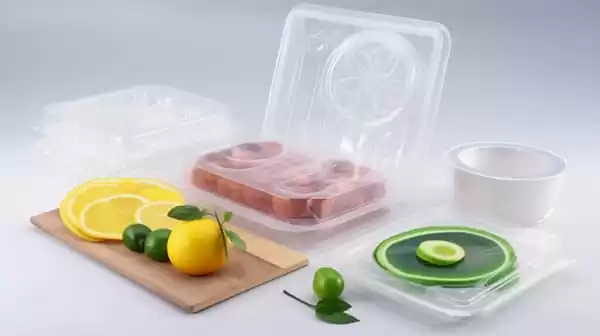
Understanding the differences and advantages of vacuum forming and injection molding enables manufacturers to make informed decisions based on their specific requirements, budget, production volumes, and desired product characteristics.
V. Conclusion
In conclusion, the comparative analysis of the vacuum forming processes and injection molding highlights their differences and advantages in plastic manufacturing. Vacuum forming, with its process of heating a plastic sheet and using a vacuum to mold it, offers cost-effectiveness, material versatility, quick turnaround times, and the ability to produce larger parts and complex shapes. On the other hand, injection molding excels in precision, surface finish, durability, and efficiency for high-volume production runs.
When choosing between using vacuum forming tooling and injection molding, several considerations come into play. Factors such as production volume, budget, desired precision, surface finish requirements, and material selection should be carefully evaluated. Understanding specific requirements and goals is crucial in selecting the most suitable manufacturing process for a particular application.
Plastic manufacturing processes play a significant role in various industries, enabling the production of a wide range of products. Whether it’s vacuum forming or injection molding, both processes have their own merits and considerations. Manufacturers must assess their specific needs and goals to determine which process aligns best with their requirements.
In the ever-evolving world of plastic manufacturing, staying informed about the latest technologies and advancements is essential. By understanding the differences, advantages, and limitations of vacuum forming and injection molding, manufacturers can make informed decisions, optimize their production processes, and achieve success in their plastic manufacturing endeavors.