Plastic molding processing is an engineering technology that involves various processes for transforming plastic into plastic products, such as injection molding, thermoforming, rotational molding, compression molding, extrusion, blow molding, 3D Printing, CNC Machining etc.
When it comes to shaping products, vacuum forming and vacuum casting have been two widely used manufacturing process. At first glance, they may seem almost the same – both mould materials using a vacuum pressure process. However, on closer inspection they are different processes with distinct uses and advantages.
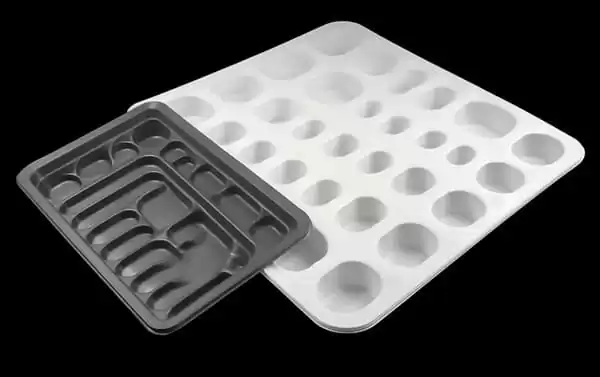
If you want to know more about vacuum forming and vacuum casting – the processes that make so many of our everyday objects – then prepare yourself for an in-depth investigation!We’ll explain what’s involved in each technique, when they’re typically used and why.
Whether you’re a product designer, an engineer, or simply curious about the back-end of product development, this comprehensive analysis will provide the insights you need.
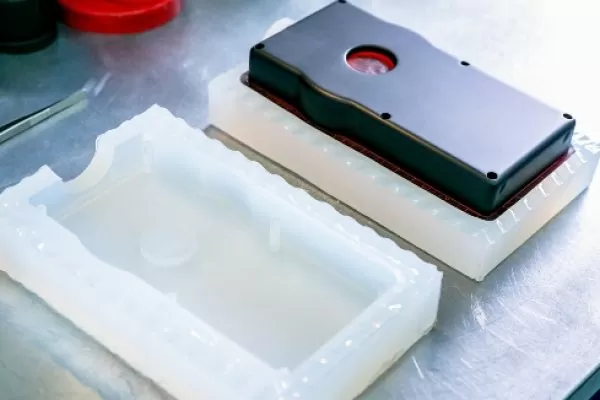
What is Vacuum Forming?
Understanding Vacuum Forming
Vacuum forming is often used to create things like packaging, plastic components, car parts and even items for space travel. It’s a simpler version of something called thermoforming or pressure forming. Here’s how it works: first heated plastic sheet until it becomes soft and bendy.
Then air is sucked away (using a vacuum) between this thermoplastic sheet and whatever shape the maker wants the plastic to copy – maybe a mold that looks like an apple or perhaps one shaped like a spaceship.With no air left between them, the two can now meet closely without anything getting in their way!
The Machinery and Materials Involved
At the heart of this process are vacuum forming machines, molds and plastic sheets. These sheets can be made from countless thermoplastic material such as HIPS, ABS, HDPE (and more). In general these sheets are around 0.25mm-10.0mm thick: but of course bigger items need thicker plastic than smaller ones!
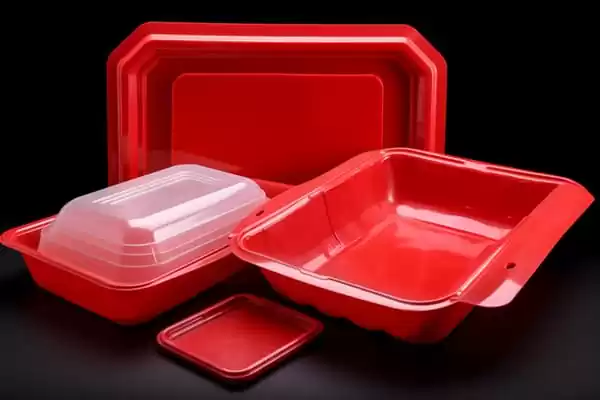
Benefits of Vacuum Forming
Cost-effective for Large Runs: If you arrange things well, vacuum forming can be cheaper than other methods when making lots of simple items.
Rapid Prototyping: Vacuum forming is easy and quick – just right for trying out new designs.
Variety of Materials: With vacuum forming process, you’ve got plenty of choices about what stuff to use – so your creation could be hard or see-through; whatever suits it best.
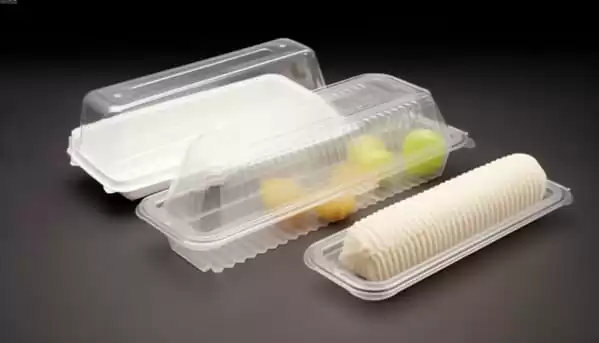
What is Vacuum Casting
What Sets Vacuum Casting Apart?
Vacuum casting, also called silicone molding—this is a way of making lots of things out of elastomers—or rubber-like materials. Using suction to pull the stuff you want into shapes made by other stuff made before. It’s fast at prototyping because it uses a temporary, copy–mold (called a tool) made out of silicone—itself made from an original part—to make only a few copies.
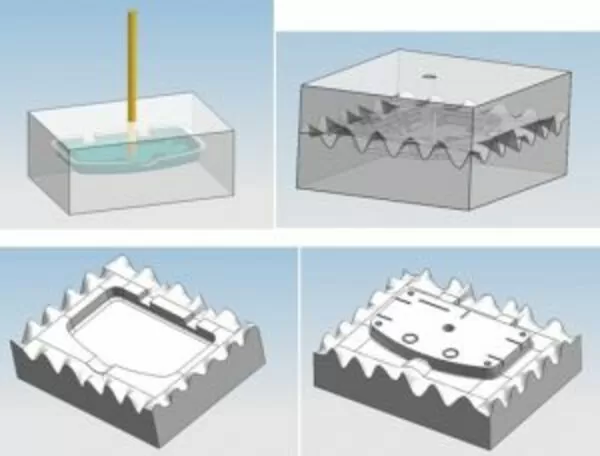
The Vacuum Casting Process
To start, one pours liquid resin into a silicone mold. This is put inside a chamber and air is sucked out – kind of like when you use a vacuum to seal food in plastic. Next, the mould rotates so resin spreads evenly across its surface. Once the resin cures, the mold is removed, and the cast part is ready.
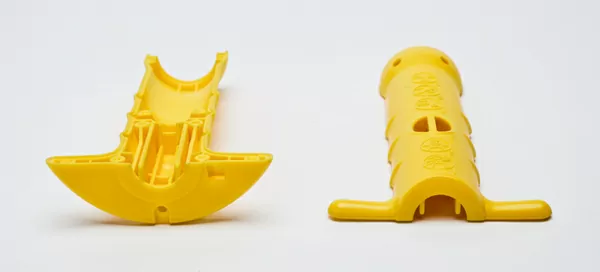
Advantages of Vacuum Casting
1. High-Quality Finishes: Vacuum casting is famous for its knack to create objects with smooth surfaces that stand up to injection molding in terms of quality.
2. Customization is Key: When it comes to making items as per a given design, this technique excels – which makes it ideal for creating things that are all about looks during the prototyping phase, or even manufacturing small batches.
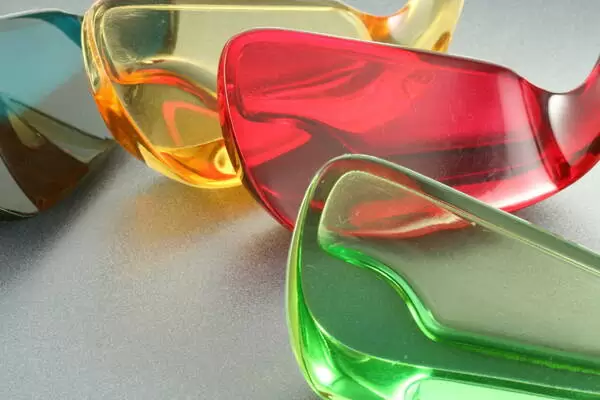
3. Material Variety: On top of having a wide range of resin recipes to choose from (just like when vacuum forming), we can also pick formulations that give different colours and degrees of hardness – plus individual performance properties too.
Vacuum Forming vs Vacuum Casting
When deciding which method to use – vacuum forming or vacuum casting – several factors need consideration. These include cost and lead time, as well as material properties in the finished item.
When to Use Vacuum Forming or Vacuum Casting
Production Scale
Vacuum Forming: Originally intended for mass production, this approach can now be used for smaller batches as well.
Vacuum Casting: Perfect when you only need a limited number of products to test or show others and those items have complex shapes (and maybe even different materials too).
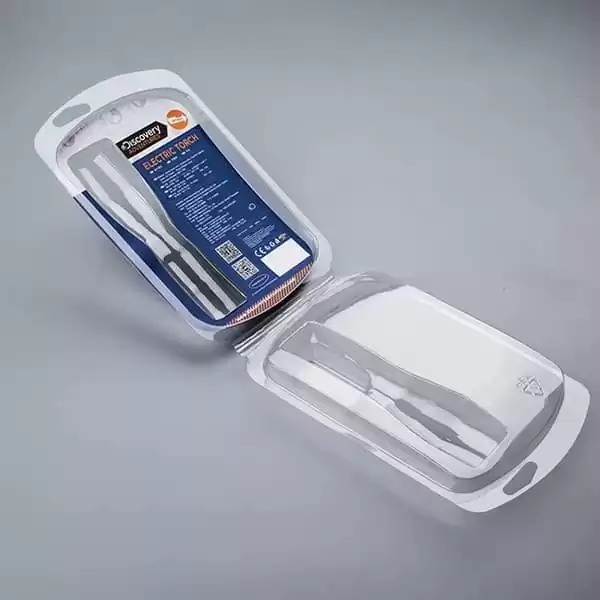
Part Complexity
When it comes to producing large, relatively uncomplicated items that don’t have many sharp bits or recesses, vacuum forming is the way to go. For intricate objects with multiple nooks and crannies – which usually require a more polished look and feel – then vacuum casting tends to be better.
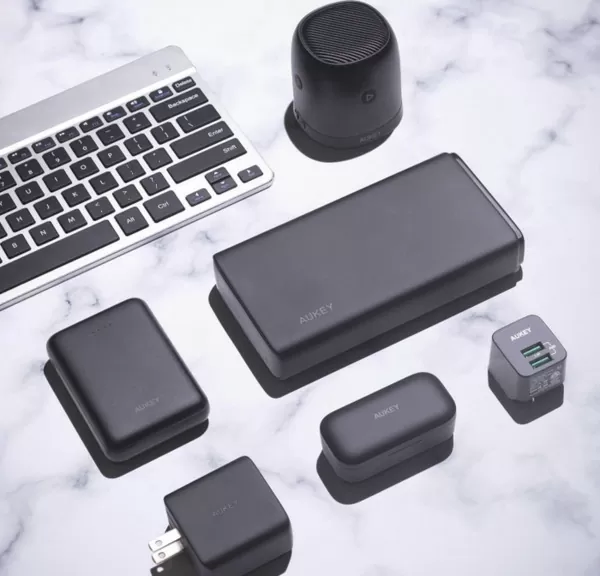
Time-to-Market
Vacuum Forming: With its simplicity, this method is perfect when you want to quickly test how something looks or works.
Vacuum Casting: Although more complicated, Vacuum Casting can also be used for rapid prototyping and producing small numbers of things – making top-quality products in no time at all!
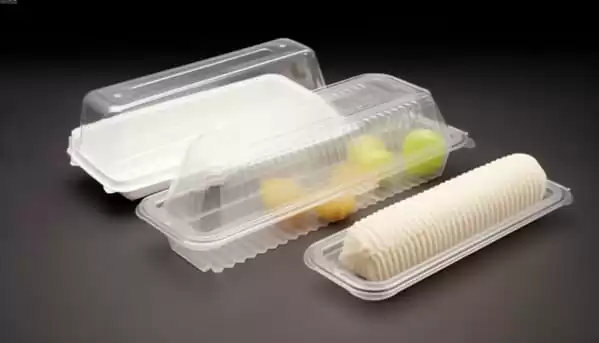
Cost Considerations
Vacuum Forming: When it comes to vacuum forming, it’s more cost-effective if you’re producing a significant number of items – because the moulds required work out cheaper per unit when spread across high volumes.
Vacuum Casting: While tooling costs can be higher due to the creation of a master part, unit costs can be more affordable, especially for small quantities.
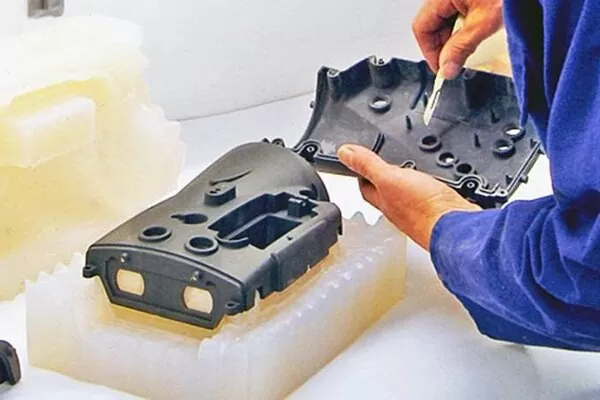
Material Range
When it comes to vacuum forming, there are plenty of thermoplastic materials to choose from: ABS, polystyrene, polyethylene — you name it. One reason these types of plastics are popular is because they have great mechanical properties and can be translucent or opaque with a range of surface finishes.On the flip side, vacuum casting often uses only one type: polyurethane resin.
While this doesn’t cover every property a thermoplastic might have, said resins can be tailor-made to mimic some characteristics quite well.
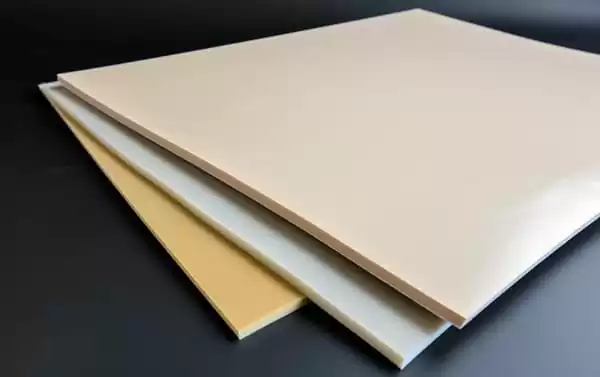
Speed and Volume
Vacuum-formed prototypes can be turned around fast – a major plus if you’re iterating designs quickly. Unlike vacuum casting, where silicone moulds take a long time to create and are better suited to low–medium volume runs, vacuum forming machines can produce much larger series.
Detail and Precision
Although both methods can create intricate objects, vacuum casting often achieves greater accuracy by using silicone molds. This makes it perfect for prototypes requiring fine detail – consumer goods and medical equipment being just two examples.
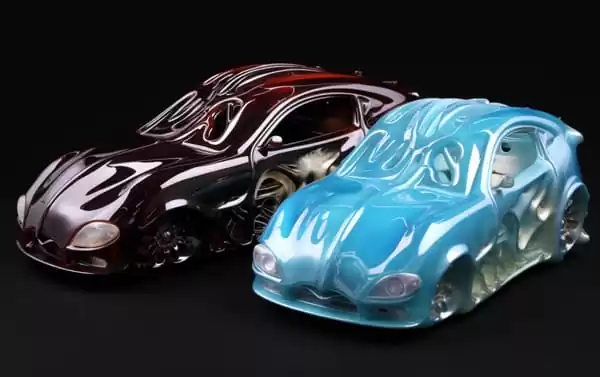
Surface Finish
When it comes to surface finish, vacuum formed parts can usually achieve a quality level similar to the mold they were made from. On the other hand, vacuum casting allows for a variety of finishes by using different mold materials and/or treating those materials in specific ways; you could even wind up with something super glossy!
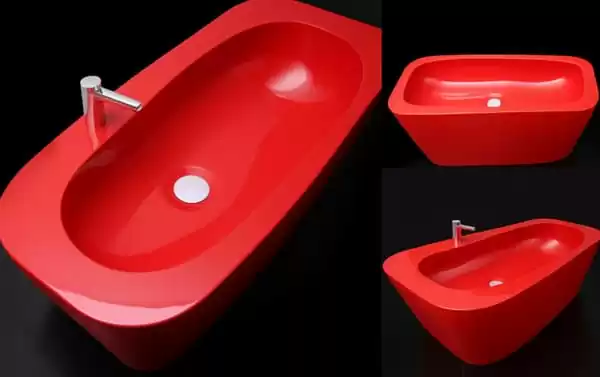
A Closer Look at Cost and Efficiency
When it comes to manufacturing decisions, cost is king. Vacuum forming and vacuum casting each bring different cost profiles depending on the size of your project and what you need done.
Mold
Vacuum forming is cheaper for tooling as this technique uses basic molds which are easier to produce. In contrast, vacuum casting tooling – often silicone molds – can be more intricate and therefore more costly to make.
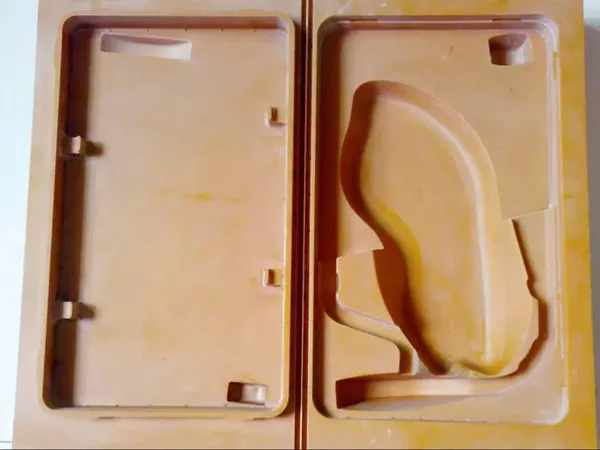
Material Costs
When it comes to vacuum forming, raw plastic thermoplastic sheets are usually a cheaper option than two-part polyurethane resins which are used in vacuum casting. Why? Vacuum casting can be more affordable for smaller productions because it employs less material overall to make one part – even though initial outlay may seem higher at first glance.
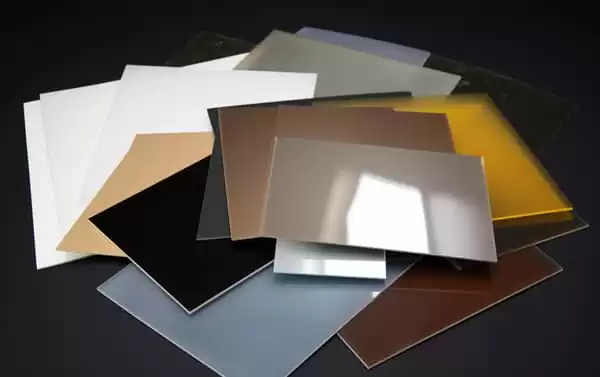
Labor and Post-Processing
There can be a big difference in how much it costs to pay workers for the two methods. You need more skilled staff when you vacuum cast because the molds are complicated and making parts this way is hard work too. When you vacuum form things, on the other hand, they often look nearly finished when they come out of the mold – so there’s less that needs doing afterwards.
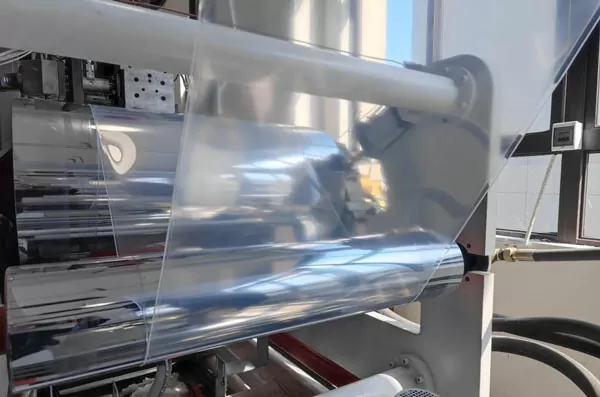
Case Studies
Vacuum Forming in the Consumer World
1. Packaging Solutions
When it comes to making custom packaging that both showcases and guards products, vacuum forming is a trusted method that won’t break the bank.
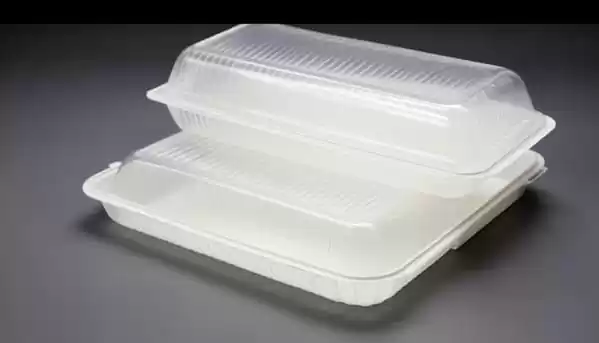
2. Automobile Manufacturing
Car manufacturers often turn to this technique for fabricating interior and exterior trims or other elements because it’s efficient and generates lightweight pieces.
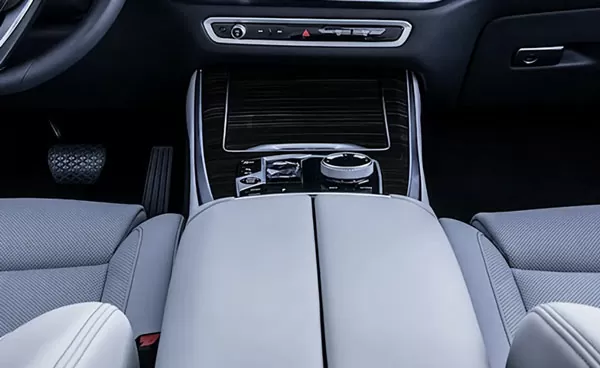
How Vacuum Casting Supports Innovation
1. Design and Engineering Prototyping
During the initial phases of product development, designers and engineers use vacuum casting to create visual prototypes that confirm both form and function.
2. Medical and Aerospace Industries
By mimicking intricate details and complicated shapes so accurately, vacuum casting helps create parts for businesses where accuracy is crucial – all while allowing those involved to see how materials behave and make any necessary changes.
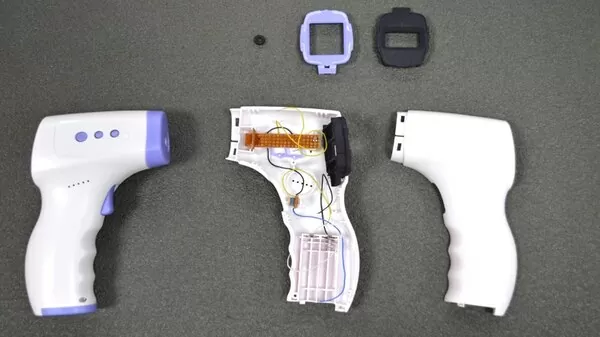
How to Choosing the Right Method?
When deciding between vacuum forming and vacuum casting, consider the following factors:
Material and Application
If your goal is to create a long-lasting, high-quantity item with a basic shape, vacuum forming could be the solution. Conversely, if you’re producing only a few items at a time but they need intricate details – think fine textures or undercuts – then vacuum casting may be your best bet.
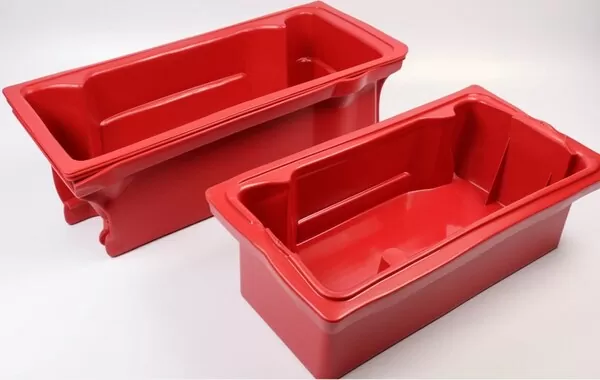
Timing and Prototyping Phase
When it comes to testing initial ideas or taking something into full-scale production, vacuum forming is often a good option. But if you need to check on details before giving the go-ahead – or want something that can bridge design and functional testing – then vacuum casting might be worth considering instead.
Budget and Quality Requirements
When it comes to making many items at once, vacuum forming is cheap and tough enough. But if you want something that looks nearly ready as soon as it’s made – and don’t mind spending more on special materials or finishes – go for vacuum casting.
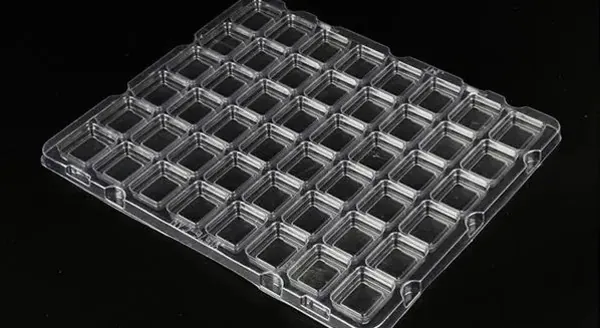
Conclusion
Vacuum forming and vacuum casting both rely on the use of a vacuum, but they serve different purposes at different stages of product development. Knowing how each method works is essential if you want to create great prototypes or products fast.
By taking into account everything I’ve talked about here – cost, equipment needed, speed and so on – you should have a pretty good sense of which one suits your needs best.
As society continues to place importance on finding the right mix of speed, customization and cost, understanding when to cast or form parts becomes a powerful weapon in your manufacturing arsenal – whether you are looking to scale up production lines or create one-off prototypes.