Thermoforming is a plastic manufacturing process in which a piece of plastic is heated to make it pliable, then shaped or contoured using a mold and trimmed to create the final part or product. There are two common forming methods in the thermoforming industry: vacuum forming and pressure forming. Vacuum forming and pressure forming are both methods used to create plastic sheets into a variety of shapes and sizes. This blog will introduce you to the characteristics and differences between vacuum forming and pressure forming (Vacuum Forming vs Pressure Forming).
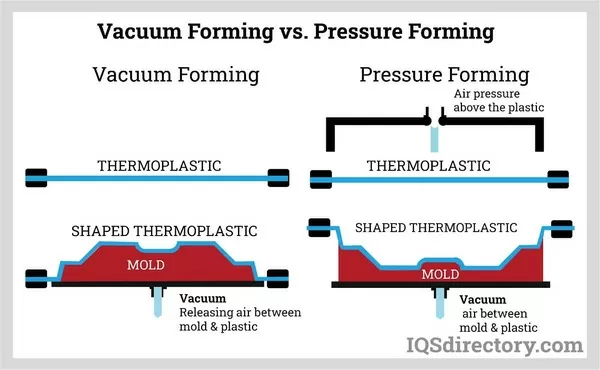
Different Principles
Vacuum Forming
Vacuum Forming, often called blister, is a plastic processing technology. The main principle is to heat a flat hard plastic sheet to soften it, then use vacuum to adsorb it to the surface of the mold, and then cool it into shape. It is widely used in plastic packaging. , lighting, advertising, decoration and other industries.
The so-called vacuum forming refers to relying on a vacuum pump to draw a vacuum state between the mold 1 and the heated thermoformed plate (sheet), causing a pressure difference between the upper and lower parts of the plate (sheet), thereby making the plate (sheet) tightly adhere to each other. A method of forming on the surface of a mold. vacuum forming involves single male mold (convex mold), single female mold (concave mold), and no mold.
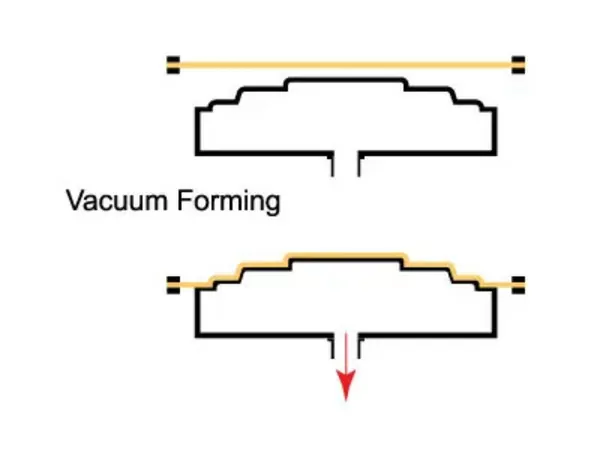
Pressure Forming
Pressure forming is a secondary molding method. It refers to the use of compressed air or steam pressure to force the heated and softened sheet to adhere closely to the surface of the mold to form. Since the pressure difference is larger than that of vacuum forming, products with more complex shapes can be manufactured.
Pressure forming machine is a kind of plastic product processing and molding equipment. The molding method is to heat the thermoplastic sheet until it softens. Under gas pressure, compressed air is used to stretch and pressurize the heated sheet and softened plastic sheet so that it adheres closely to the surface of the mold. After cooling and shaping, the product becomes a finished product.
At the same time, the production cycle can be repeated according to certain procedures to produce exactly the same product.
Pressure forming process types include: differential pressure forming, cover molding, plunger-assisted molding, concave and convex molding, moldless air pressure forming, and double-piece thermoforming.
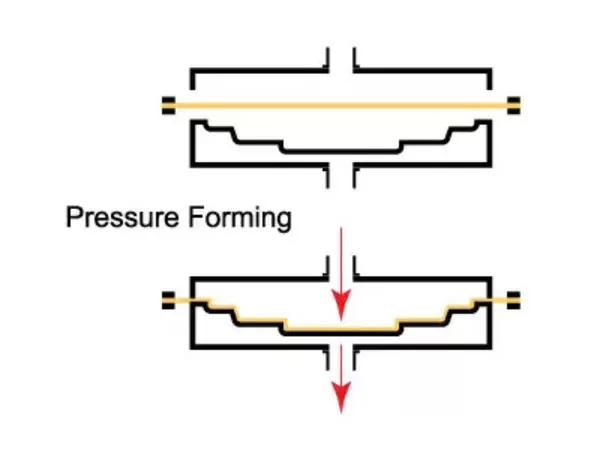
Advantages and Disadvantages
Vacuum Forming
Advantage
1. Vacuum forming has low mold cost due to its molding method. At the same time, vacuum forming molds can also be made of cheap materials, such as gypsum, wood, copper plating, etc.
2. Products with relatively simple shapes or sizes can be quickly prototyped or produced through vacuum forming.
3. The production cycle is short, and vacuum forming is very suitable for small batch production or prototype proofing.
Disadvantage
Limited detail: While vacuum forming allows for complex shapes, the level of detail (especially undercuts and sharp corners) can be limited compared to pressure forming or injection molding.
Material Thickness Variation: Due to the nature of the process, material stretching may cause uneven thickness. The areas furthest from the mold may be thinner, which may affect the structural integrity of the final product.
Not suitable for high-volume production: For very large production runs, unit costs may be higher than other processes such as injection molding due to slower cycle times.
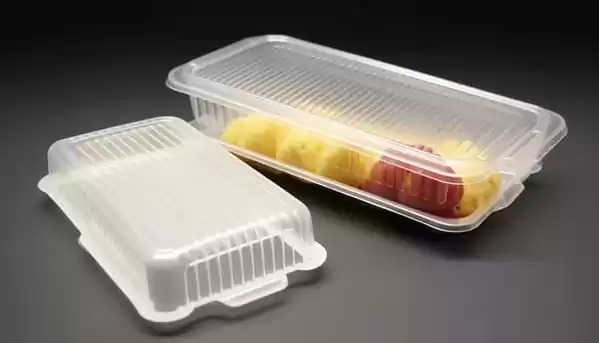
Pressure Forming
Advantage
1. Pressure forming has good surface forming effect and is suitable for producing products with textured surfaces or more surface details.
2. Products are produced with high quality and small tolerances.
3. Pressure forming is more efficient for plastic sheets. Pressure forming can stretch plastic sheets more effectively, is suitable for producing thinner products, and has less impact on product strength.
Disadvantage
1. Higher tooling costs: Compared to vacuum forming, pressure forming requires more complex and expensive tooling, making it less cost-effective for very small production runs.
2. Increased process complexity: The process requires more complex machinery and tighter control of process parameters, which may mean a higher initial learning curve and potentially longer setup time.
3. Material limitations: Not all materials suitable for vacuum forming are suitable for pressure forming, especially those that cannot withstand higher pressures without tearing or excessive thinning.

Different Product Quality
Vacuum Forming
In vacuum forming, since the vacuum degree that the tabletop vacuum forming machines vacuum pump can form is less than 0.1MPa, but the vacuum degree that can be achieved in industry is only 0.069-0088MPa, the molding pressure is insufficient for vacuum forming products with thicker sheets or complex shapes. It will cause the parts to be poorly formed, have unclear outlines, or even not be formed at all.
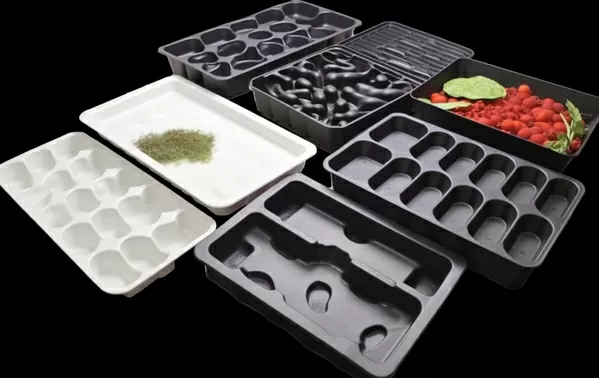
Pressure Forming
If pressure forming is used, the pressure of the air compressor can easily reach 0.3-06MPa, and the molding of thicker plates and complex-shaped parts can also be achieved. Moreover, air pressure forming is fast, about three times more than vacuum forming. Pressure forming, because of its different process, produces products with a higher level of detail and quality.
There may be bubbles or horizontal lines on the surface of products produced by vacuum forming. If your project has higher product requirements, requires fine textures and clear details, or requires smaller tolerances for the product, then pressure forming will be a better choice.
Pressure forming should be used under the following circumstances:
1. The molded parts are higher (the mold depth is larger).
2. The surface of the workpiece has fine patterns or ribs.
3. The corners of the workpiece are acute angles.
4. The material has high tensile strength.
5. The production batch of parts is large.
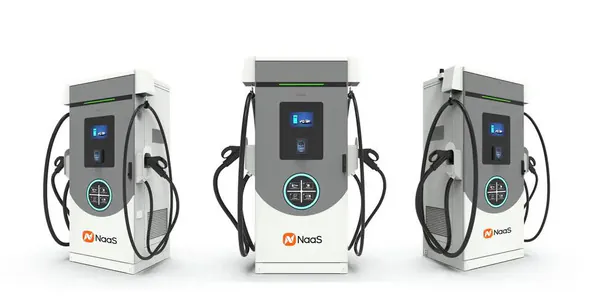
Different Costs
During the pressure forming process, an air compressor or compressed air needs to be used, which involves additional machines, so the cost of pressure forming is higher than that of vacuum forming. At the same time, vacuum forming molds are generally relatively simple and can also be made of cheaper materials, so the cost is lower. Pressure forming generally requires more expensive and durable molds.
Different Applications
Vcuum Forming
Vacuum forming is suitable for relatively simple parts and is widely used in signage, plastic packaging, automotive panels, lighting, advertising, decoration and other industries.
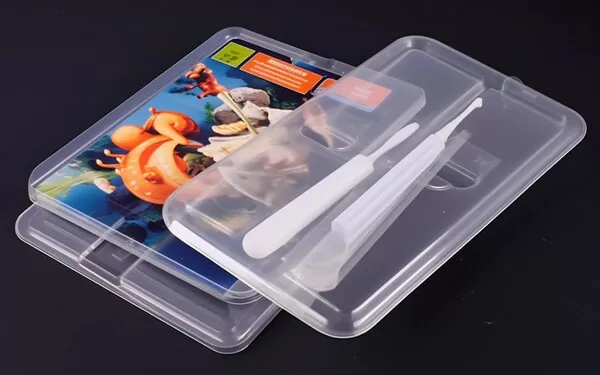
Pressure Forming
Since the pressure difference is larger than that of vacuum forming, pressure forming can produce products with more complex shapes. Pressure forming is better suited for smaller, more complex parts that require fine textures and high-quality finishes, such as medical device components, electronics housings and high-end consumer packaging.
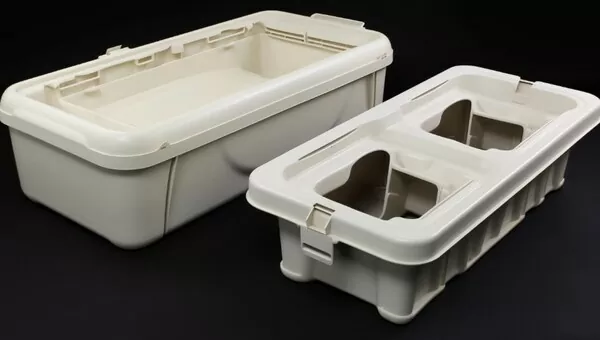
Different Molds
Vacuum forming is the simplest type of plastic thermoforming and uses a mold and vacuum pressure to obtain the desired part geometry. During the vacuum forming process, a sheet of plastic is heated and then suction is used to pull it around a mold. This method is the simplest, but the pressure difference caused by vacuuming is not large, and it is only used for products with simple shapes. It is suitable for parts that only need to be accurately formed on one side, such as contour packaging for food or electronic products.
There are two basic types of molds: male (convex) and female (concave). In male mold production, plastic sheets are placed over the mold to outline the internal dimensions of the plastic part. In negative mold production, sheets of thermoplastic are placed inside the mold to accurately form the outer dimensions of the part.
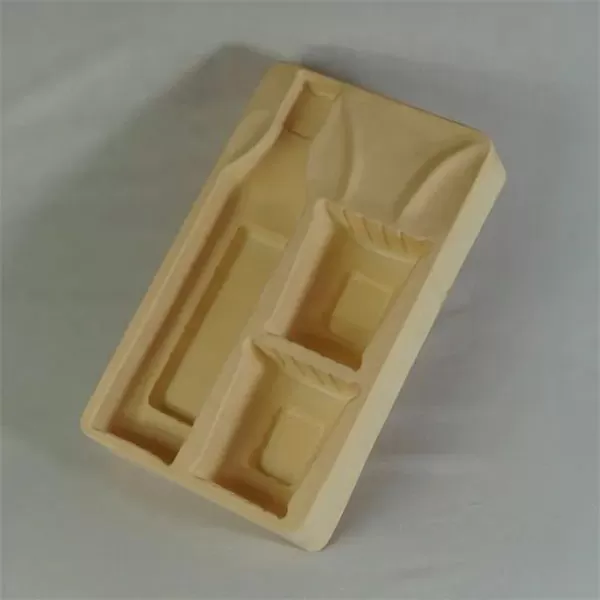
In pressure forming, a heated plastic sheet is squeezed between two dies (hence the name), rather than using suction to pull it into position around a single mold. Since the pressure difference is larger than that of vacuum molding, products with more complex shapes can be manufactured.
Pressure forming is suitable for making plastic parts that need to be formed more precisely on both sides and/or need to be deeper (they need to extend further/deeper into the mold), such as electrical housings that need to look nice on the outside and snap into place or on the inside Install to exact dimensions.
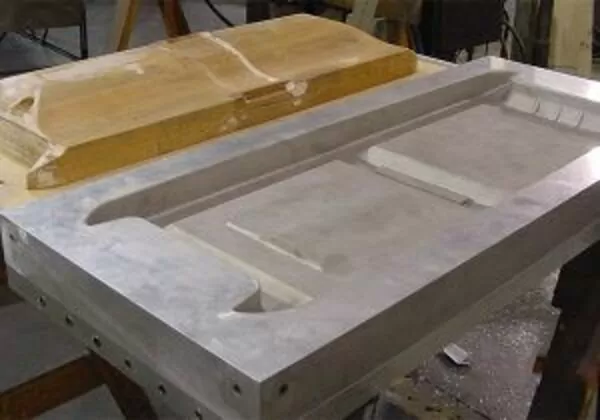
Conclusion
In summary, while both vacuum forming and pressure forming offer valuable advantages for thermoforming plastic materials, the choice between them depends on the specific requirements of the project, including detail, quality, budget, and throughput. Understanding these differences is critical to optimizing the design and manufacturing process for specific applications.