Our daily lives are undeniably intertwined with plastic products – they’re found everywhere; in our mobile phones, the cars we drive and even the food storage containers we use. When it comes to manufacturing these items traditionally injection moulding has been the go-to technique. However, as technology expands its horizons thermoforming is becoming an increasingly popular alternative: it’s versatile, cost-effective and efficient.
The question therefore arises – can thermoforming replace injection molding process entirely for plastic item production? This blog aims to provide you with everything you need to know in order to answer that query. We’ll discuss the differences between these two manufacturing techniques – highlighting situations where thermoforming excels.
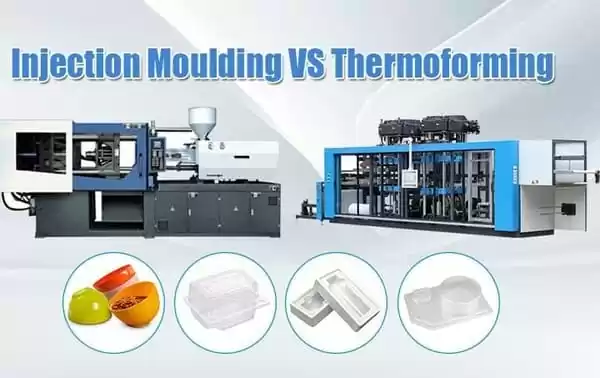
What is Thermoforming?
Thermoforming is a process of manufacturing that involves heated plastic sheet of plastic until it can be shaped into a particular form by being put into a mold. After this, any extra bits are taken off so what remains is something you can actually use. It may sound simple enough but vacuum forming has many different uses.
There are several thermoforming methods used in actual production: differential pressure molding, cover molding, plunger-assisted molding, suction back molding, opposite mold molding, female mold and male mold thermoforming, thin gauge thermoforming, heavy gauge thermoforming and twin sheet forming.
Advantages of Thermoforming
Cost-effective Prototyping: When compared to enjection molding, pressure forming is a cost-effective option for producing prototypes and low-volume production runs because it requires less expensive moulds (plaster, wooden, beryllium copper alloy, aluminum, etc.).
Versatility in Design: Even complex structures (including ones that have undercuts) can be made without compromising on strength.
Rapid Production: Thermoforming takes less time than plastic injection molding, often because there’s no cooling phase involved.
No Gates or Runners: Without the need for gates and runners, material waste is minimal, leading to more cost and material-efficient production.
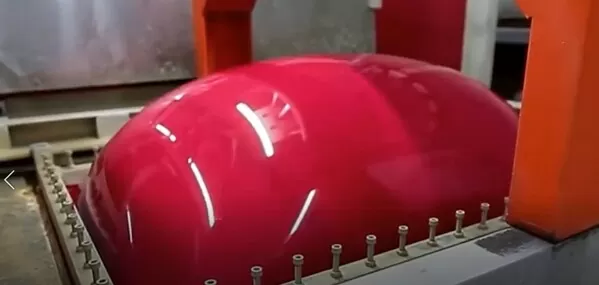
Limitations of Thermoforming
Material Thickness Matters: Thickness is key when it comes to getting intricate details from plastic sheet forming.
Uniform Wall Thickness Can Be Challenging: Keeping walls uniform across your part might not be easy in thermoforming.
Size and Dimension Constraints: When a product exceeds certain measurements, you may need more time or another method than vacuum forming.
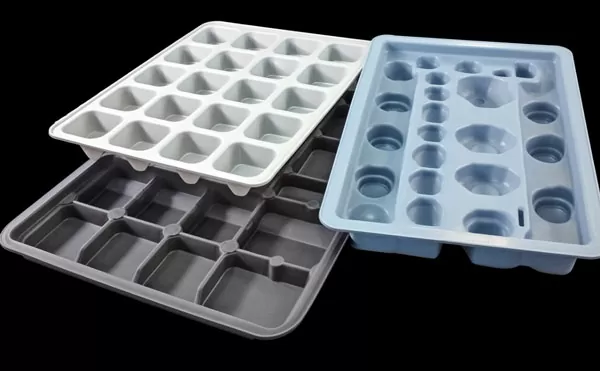
What is Injection Molding?
Injection molding process is an injection-molding molding method. The advantages of the injection molding method are fast production speed and high efficiency, the operation can be automated, there are many designs and colors, the shapes can be from simple to complex, and the sizes can be from large to small, and the product dimensions are accurate, the products are easy to replace, and can be made into complex shapes Parts, plastic injection molding is suitable for mass production and complex-shaped products and other molding processing fields.
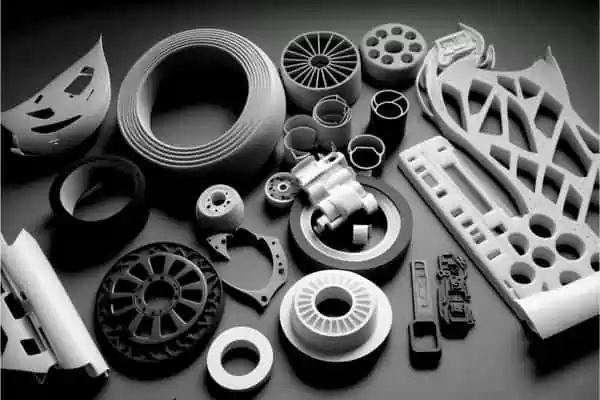
Advantages of Injection Molding
Efficiency and High Production Speed: Why It’s So Popular for Large Production RunsOne major reason injection molding is so widely used is because it can churn out parts at a very fast clip. In fact, once the mold is designed and the method set up, making parts can be astonishingly quick compared to other manufacturing methods.
Complex Part Design: By injecting material at high pressures, intricate and complicated part designs are achievable. High pressure forces the substance to occupy every bit of space in a mold – meaning it ends up looking just like the original template (both inside and out).
Strength and Durability: Incorporating fillers into the injection molds enhances both strength and endurance of molded components. Concurrently, these fillers decrease plastic density during molding processes.

Automation and Labor Cost Reduction: Injection molding is a type of manufacturing that uses machines to do most of the work. This means fewer people are needed—and it also makes sure each product meets quality standards every time.
Material and Color Flexibility: In injection molding, you have the freedom to choose from a broad spectrum of materials and colors. You can blend various plastics together to achieve specific traits – like hue – in your finished piece.
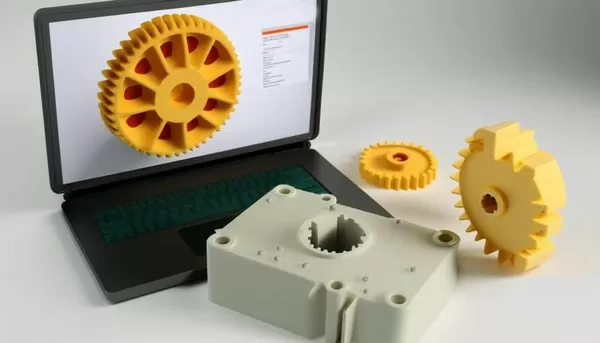
Limitations of Injection Molding
High Initial Injection Molding Cost: The cost of starting up injection molding can be steep. The creation and design of a mold are pricey since they need to be custom made for each new item, requiring precision craftsmanship.
Design Restrictions: While injection molding offers a lot of freedom, there are design limitations to consider. One is that you have to make sure your design lets you remove the part from the mold afterwards – that might mean not making it too complicated or delicate.
Part Changes are Difficult: After a mold is produced, making changes to designs or specific features of parts is hard. Making such adjustments usually means creating an entirely new mold — something that costs a lot and takes a long time.
Injection Molding Waste Material: It’s unavoidable: When you’re doing injection molding, there’ll almost always be some waste material to deal with. Runners and unused stuff left behind in sprues need recycling or disposing of – meaning extra stages in production.
Limited to Vacuum Forming Plastics: Injection molding is largely restricted to thermoplastics, meaning materials outside this category – including thermosets – are incompatible with the process.
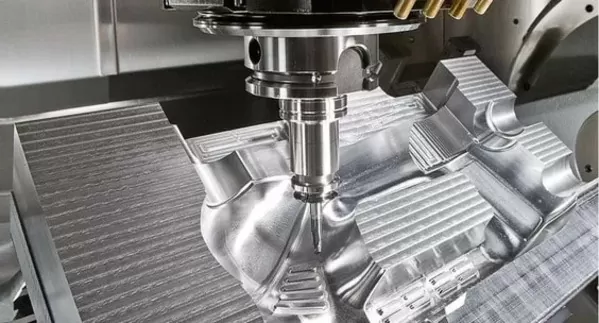
Thermoforming vs. Injection Molding
Being able to tell the difference between thermoforming and injection molding is important if you want to decide which one would work best for a particular job.
Thermoforming
Thermoforming starts with a plastic sheet of plastic, heating it until it’s flexible enough to shape; then pulling it over a form before cutting off any excess material – all things considered: this method typically quickens production times while keeping costs comparatively low making ideal those instances where short-run batches need doing quickly but either they’re bespoke items do not have strict requirements around precision or uniformity (e. g., custom molds made by hand).
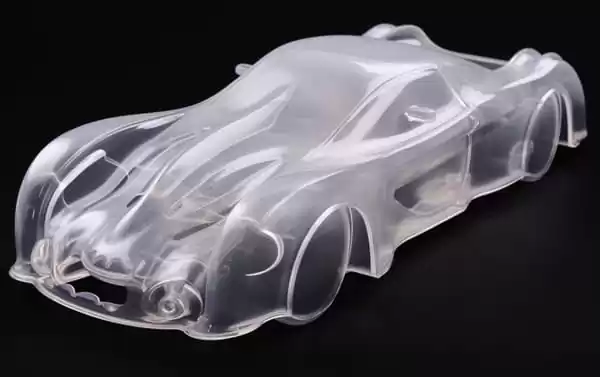
Injection Molding
Injection molding involves injecting molten liquid polymers into a injection molding tooling at high temperatures and extreme pressure; once cooled, this material takes on the desired shape. Injection plastic molding job is ideal for projects that call for tight tolerances and high precision, large numbers of identical components and expensive tooling. Injection-molded product typically have uniform wall thicknesses; they may also feature fine surface details and higher strength or rigidity.

Key Differences
Compared to injection molding, thermoforming is more energy efficient because it doesn’t need as much pressure or energy. It can also handle different materials better – even some recycled ones – which makes it a greener choice.
On the flip side, injection molding wins when parts must be exactly alike every time, or fit together precisely.
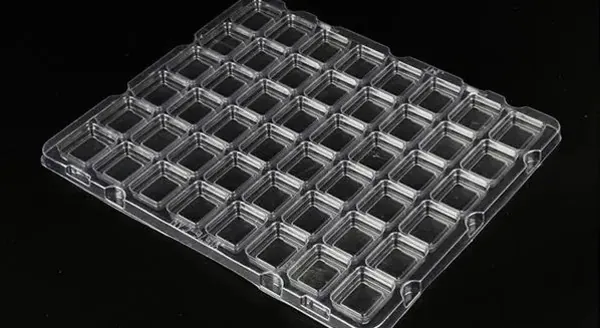
How to Choose?
When deciding on the appropriate manufacturing process to adopt, there are various vital considerations which can assist guide this process.
Lower Tooling Costs
One advantage of pressure forming is that it has lower tooling costs compared to injection molding. This happens because the molds don’t have to be as strong since there isn’t high pressure to hold them together during production – and therefore cheaper materials can be used.
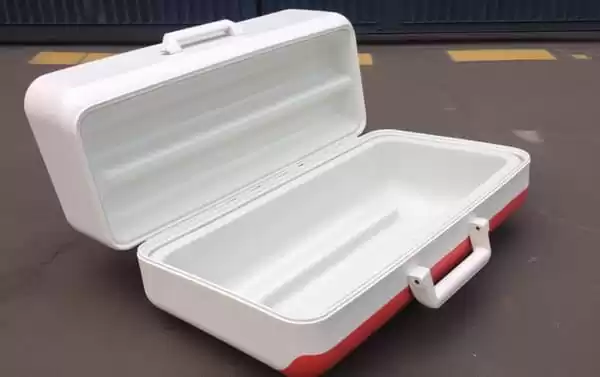
Shorter lead times
Making simpler, less expensive molds takes less time than when making more complex ones, so you’ll wait less before starting up your thermoforming line.
Design Complexity
For items with intricate forms, undercuts or expansive surface areas, thermoforming’s adaptability may render it the superior alternative; whereas injection molding could be better if your product requires exact characteristics for consistency and precision.
Production Volume
Due to the process of thermoforming and only using a one-sided mold, it is easy to make adjustments. On the contrary, injection molding requires specific molds or double sided mold for each product. Thermoforming is well-suited for low to medium production volumes, including custom or short runs, due to its lower setup cost. Injection molding processes excels in high volume, where the initial setup cost can be spread across a large number of parts.
Material Selection
Due to the nature of each process, they lend themselves to different types of materials. Thermoforming typically works with thermoplastics, while injection molding allows for a broader range, including thermosets and elastomers.
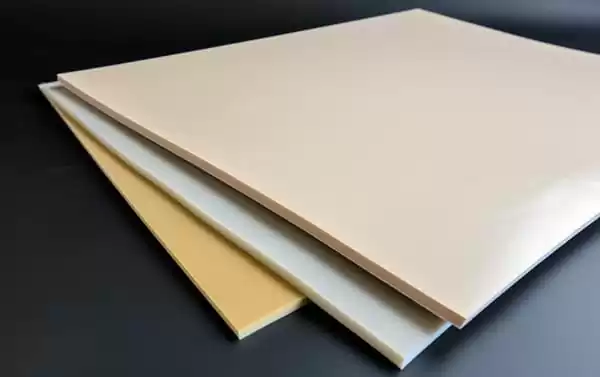
Considering these factors alongside specification needs plus budget limitations enable us make informed choices pertaining right technique use producing desired plastic item!
Case
To further demonstrate the versatility of thermoforming, it’s valuable to explore real-world examples where it has been a game-changer.
Automotive Interiors
Door panels and trays inside cars have benefited from vacuum forming as it provides lightweight solutions with design flexibility while still being strong enough for their purpose.
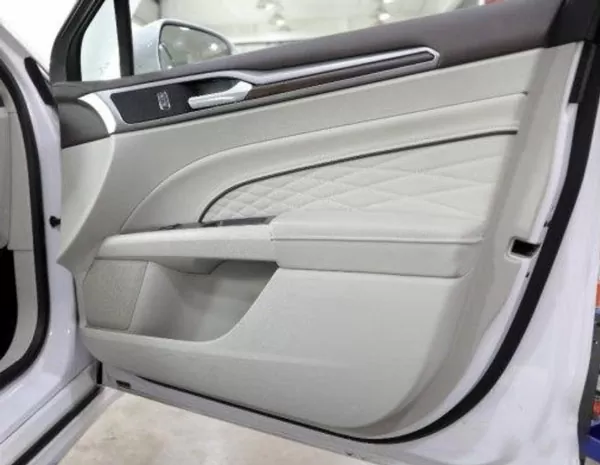
Consumer Packaging
Many disposable plastic containers and trays are made using thermoforming because it can produce custom designs at lower costs than other methods – important if you want to attract buyers in stores by having your product stand out on shelves!
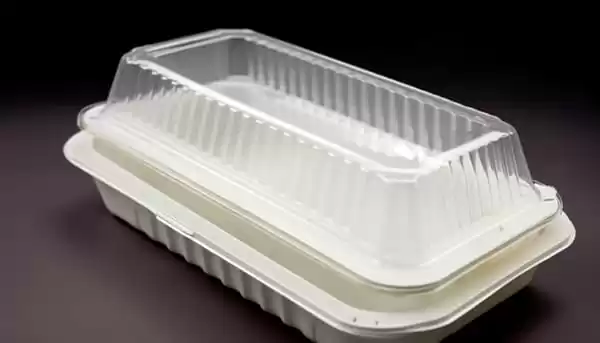
Medical Equipment
Some medical devices’ casings/housings/enclosures also rely on this process; they must meet strict cleanliness standards but may also need bespoke features.
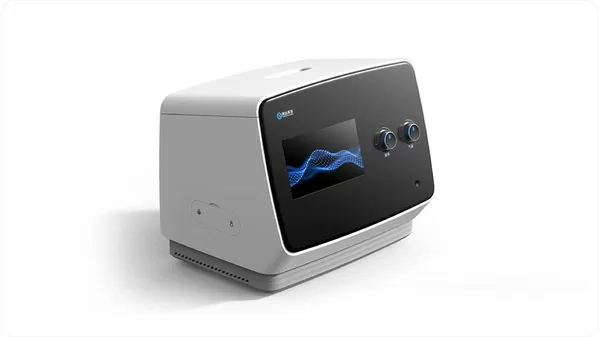
The Future of Thermoforming
The future of thermoforming looks bright thanks to ongoing progress in materials science and process automation. 3D printing, for example, is starting to combine with thermoforming in interesting new ways – opening up the potential for creating more complex products that are suited to particular specifications relatively easily. Manufacturers are already finding that thermoforming can bring benefits not just compared to injection moulding but also as a completely stand-alone technique – such as sustainability advantages or customisation options which chime with how industry wants to market finished items now.

Sustainability in Thermoforming
In the world of product design and manufacturing, being sustainable has never been more important. That’s why a growing number of companies are turning to thermoforming: it produces less waste than other methods and can use recycled materials with very little loss in quality – good for both the planet and their bottom line. Plus, customers love products that come from sustainable production processes so they may even sell better too!
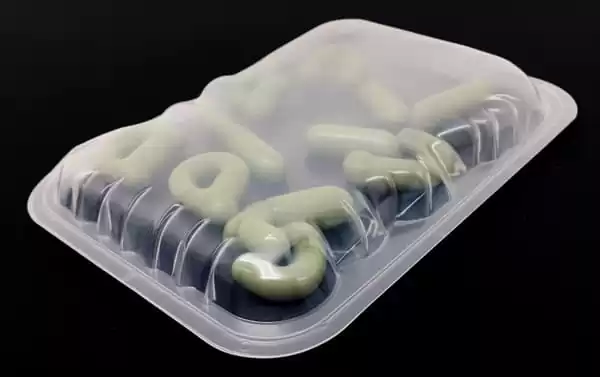
The Human Element: Skill and Craft in Thermoforming
Although automation and technology have made great strides, the art of thermoforming still relies on human know-how. Molds need to be crafted with care, materials must be chosen wisely and processes managed skillfully in order for products to meet exacting standards. As manufacturing continues to change, training people to become thermofoming experts will be key. This way, even as machines take over more tasks, humans will remain central to production lines because they possess specialist knowledge no amount of programming alone can replace.
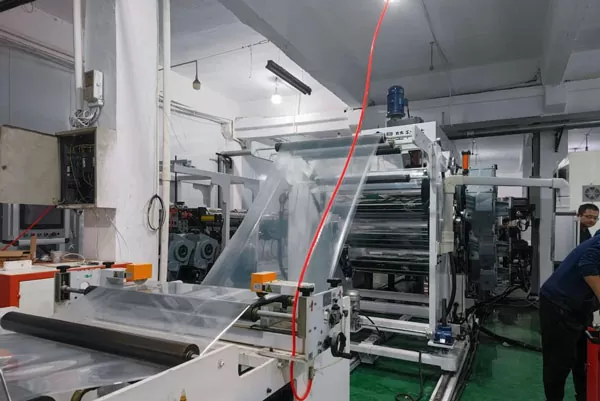
Conclusion
When deciding between injection molding and thermoforming, it’s important to consider multiple factors specific to your project – for example, how precise the finished product needs to be or its overall size. While thermoforming might be more appropriate if you’re producing large items with simpler designs and need a small number of parts quickly (and at low cost), things like complex shapes or high-volume production runs often mean injection molding is the way to go.
Understanding these differences is crucial for manufacturers wanting to select the technique that best suits their products’ demands – both come with distinct advantages and understanding those can help ensure any investment optimizes results depending on parameters such as budget available or tooling requirements among others.
In the wide-ranging world of plastics, thermoforming is making a name for itself thanks to growing demand for bespoke items, rapid prototyping and environmentally friendly production. Although it doesn’t fit all jobs, its success shows why diversity in manufacturing counts – and how markets drive innovation. In future, vacuum forming could be seen not as an alternative to injection moulding, but as the favoured method for many plastic-product applications. It’s versatile; cost-effective; adaptable to changing requirements.