Introduction
When it comes to vacuum-formed parts, the importance of achieving the right finish cannot be overstated. The finish not only enhances the overall appearance of the many vacuum formed parts but also plays a crucial role in ensuring their durability and protection. However, with numerous finish options available, selecting the appropriate one can be a daunting task. In this article, we will delve into the significance of choosing the right finish for vacuum-formed parts and provide valuable insights to help you make informed decisions. We will explore the impact of finishes on aesthetics and functionality and discuss factors to consider when selecting the ideal finish for your vacuum-formed parts.
Throughout the article, we will cover various aspects related to finish selection. We will begin by discussing the significance of achieving the right finish and how it contributes to the overall quality of vacuum-formed parts. Next, we will explore the different factors that should be taken into consideration when choosing a finish, including material characteristics, aesthetic requirements, functional needs, and cost considerations. Additionally, we will provide an overview of the vacuum forming process and its requirements to help you understand the context in which finish selection takes place.
By the end of this article, you will have gained valuable insights into the importance of selecting the right finish for vacuum-formed parts and have a better understanding of the factors to consider when making your decision. Whether you are looking to enhance the appearance of your vacuum-formed parts or seeking finishes that offer enhanced functionality and protection, this article will serve as a comprehensive guide to help you achieve the perfect finish for your vacuum-formed parts.
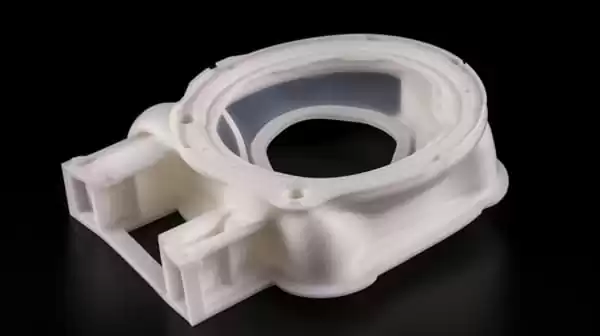
II. Understanding Vacuum Forming process
A. Explanation of the Vacuum Forming Process:
Vacuum forming is a versatile manufacturing process used to create plastic parts with various shapes and sizes. The pressure forming process involves several key steps:
Heating: A sheet of thermoplastic material, typically in the form of a flat sheet or roll, is heated until it becomes soft and pliable. Heating can be achieved using methods such as radiant heaters or hot air.
Forming: The heated plastic sheet is then placed over a mold or tool, which defines the desired shape of the final part. A vacuum is applied, removing the air between the sheet and the mold, causing atmospheric pressure to force the sheet to conform to the shape of the mold.
Cooling: Once the part has taken the shape of the mold, it is cooled to solidify the plastic and maintain its formed shape. Cooling can be done using air cooling, water sprays, or other cooling methods.
Trimming and Finishing: After cooling, excess material is trimmed away from the formed part using techniques like cutting, routing, or sawing. Finishing options such as smoothing, sanding, or adding additional features can be applied to achieve the desired final shape and surface quality.
B. Key Requirements for Vacuum Forming:
Successful vacuum forming requires specific factors to be considered:
Plastic Material: The choice of plastic material is crucial and depends on the desired properties of the final part. Common materials used in vacuum forming products include ABS, polycarbonate, and acrylic.
Mold or Tool Design: The mold or tool should be designed to accommodate the desired shape of the part, considering factors like draft angles, undercuts, and wall thickness. A well-designed mold facilitates the forming process and ensures easy release of the formed part.
Heating and Temperature Control: Proper heating of the plastic sheet is essential to achieve the desired pliability for forming. Temperature control is crucial to ensure uniform heating and prevent overheating or deformation of the material.
Vacuum Pressure: The application of vacuum pressure creates the necessary force for the plastic sheet to conform to the mold. The vacuum pressure should be carefully controlled to achieve consistent material distribution and accurate part definition.
C. Advantages and Benefits of Vacuum Forming:
Vacuum forming offers several advantages and benefits:
Cost-Effective Manufacturing: Vacuum forming is a cost-effective method for producing plastic parts compared to other molding processes, making it suitable for both prototyping and large-scale production.
Design Flexibility: The process allows for the creation of parts with complex shapes, sharp edges, rounded corners, and other customized features. It offers design flexibility and enables the production of parts with intricate details.
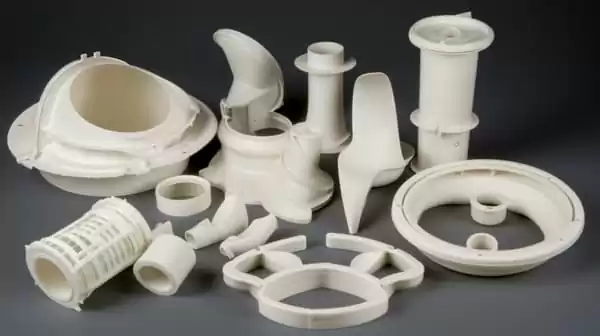
Quick Turnaround: Vacuum forming has relatively shorter cycle times compared to other molding processes, resulting in faster production and shorter lead times.
Wide Range of Applications: Vacuum forming is used in various industries, including automotive, packaging, consumer goods, medical, and more. It can produce parts for applications such as product packaging, custom components, signage, and point-of-sale displays.
III. Material Considerations for Vacuum Forming process
A. Importance of Choosing the Right Plastic Material:
Selecting the appropriate plastic material is crucial for successful vacuum forming. The choice of material impacts the properties and characteristics of the final formed part. Consider the following aspects:
Material Strength: Different materials have varying degrees of strength and rigidity. Consider the intended application of the vacuum-formed part and choose a material that provides the necessary strength and structural integrity.
Impact Resistance: Some applications may require parts that can withstand impacts or rough handling. Opt for materials known for their impact resistance to ensure the durability of the vacuum-formed part.
Transparency: Transparency may be a desirable attribute for certain applications, such as displays or packaging. Materials like polycarbonate offer high transparency and optical clarity, making them suitable choices.
Chemical Resistance: Depending on the intended use, the material should be resistant to specific chemicals or substances it might come into contact with. Evaluate the chemical resistance of the material to ensure its compatibility with the environment in which the part will be used.
B. Considerations for Design Flexibility in Vacuum Forming:
One of the advantages of vacuum forming is its design flexibility. Consider the following factors when designing for the vacuum process of forming:
Undercuts and Draft Angles: Undercuts refer to features in the design that would make it difficult to release the part from the mold. Incorporating appropriate draft angles allows for easy release and smooth ejection of the formed part.
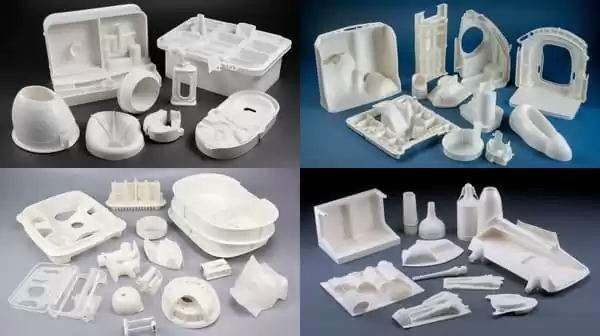
Wall Thickness: Ensure uniform wall thickness throughout the part to promote consistent forming and minimize material distribution issues.
Complex Shapes: Vacuum forming enables the creation of parts with complex shapes, including deep draws, textured surfaces, or intricate details. Leverage the design freedom and push the boundaries of what can be achieved with vacuum forming machines.
C. Introduction to Acrylonitrile Butadiene Styrene (ABS) and Polycarbonate as Suitable Materials:
Two commonly used materials in vacuum forming are acrylonitrile butadiene styrene (ABS) and polycarbonate. Here’s a brief introduction to each:
Acrylonitrile Butadiene Styrene (ABS): ABS is a popular thermoplastic known for its excellent impact resistance, rigidity, and affordability. It is widely used in various industries, including automotive, consumer goods, and electronics.
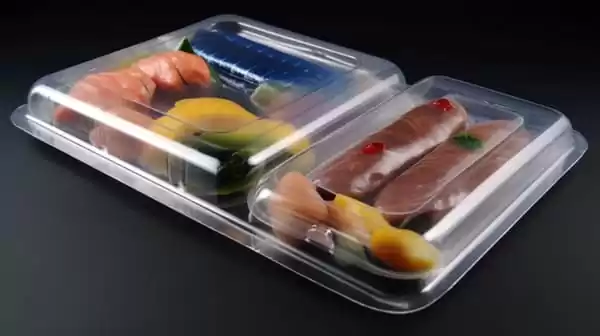
Polycarbonate: Polycarbonate is a transparent thermoplastic with exceptional impact resistance and high heat resistance. It is commonly used in applications that require optical clarity, such as protective covers, displays, or lighting fixtures.
IV. The Vacuum Forming Process
A. Step-by-Step Explanation of the Vacuum Forming Process:
The vacuum forming process involves several key steps that are essential in achieving successful vacuum-formed parts:
Heating the Plastic Sheet:
The process begins by heating a plastic sheet until it reaches its softening point. This can be done using radiant heaters or hot air. The heating makes the plastic sheet pliable and allows it to be formed into the desired shape.
Forming the Sheet over a Mold:
Once the plastic sheet is heated and softened, it is carefully placed over a mold or tool. The mold defines the shape and details of the final part. When the heated sheet is placed over the mold, a vacuum is applied, either from beneath the mold or through the mold itself.
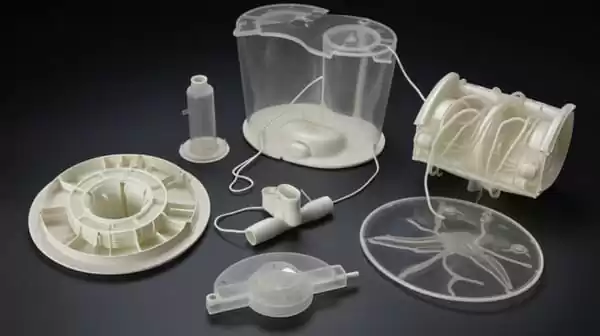
Cooling the Formed Part:
After the plastic sheet has conformed to the mold’s shape, it is cooled down to solidify and retain its formed shape. Cooling methods can include ambient air cooling, water sprays, or other cooling techniques. The cooling process helps stabilize the part and ensures it retains its intended form.
Trimming and Finishing the Part:
Once the formed part has sufficiently cooled, any excess material or flash is trimmed away. This can be done using cutting tools, such as roller cutters or press cutting tools. The part may undergo additional finishing processes, such as smoothing or adding specific features, to achieve the desired final shape and surface quality.
B. Highlighting the Importance of Each Step in Achieving a Successful Vacuum Form:
Each step in the vacuum forming process plays a crucial role in achieving a successful outcome:
Heating the Plastic Sheet:
Proper heating is essential to make the plastic sheet soft and pliable, enabling it to be easily formed and molded. Accurate temperature control ensures uniform heating and prevents overheating or deformation of the material.
Forming the Sheet over a Mold:
The vacuum pressure created during this step ensures that the plastic sheet adheres closely to the mold, capturing all the desired details and contours. The vacuum pressure helps achieve accurate part definition and eliminates air pockets or voids between the sheet and the mold.
Cooling the Formed Part: Cooling the formed part is necessary to solidify the plastic and stabilize its shape. Proper cooling prevents warping or deformation and allows for easier removal of the part from the mold without distortion.
Trimming and Finishing the Part:
Removing excess material and performing finishing processes are crucial for achieving the final desired shape and surface quality of the vacuum-formed part. Careful trimming ensures clean edges, while additional finishing options, such as smoothing or adding specific features, enhance the aesthetics and functionality of removing vacuum formed parts of the part.
V. Choosing the Right Finish for Vacuum-Formed Parts
A. Aesthetic Considerations:
When selecting the right finish for cutting vacuum-formed items, aesthetic factors play a significant role. Consider the following:
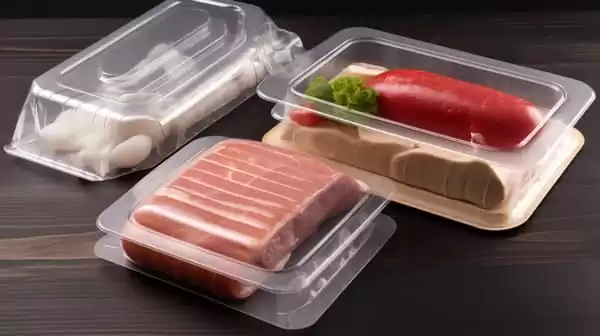
Glossy or Matte Finish Options: Decide whether a glossy or matte finish aligns with the desired appearance of the final product. A glossy finish offers a reflective and polished look, while a matte finish provides a more subdued and textured appearance. The choice between the two depends on the intended aesthetic and the specific requirements of your project.
Incorporating Finishes During or After the Vacuum Forming Process: Finishes can be applied during or after the vacuum forming process to achieve the desired visual effect. During a cost effective vacuum forming, techniques like pre-colored plastic or printed patterns can be utilized to create unique finishes. Alternatively, finishes such as painting, screen printing, or applying decals can be done after the vacuum forming process to add custom designs or branding.
B. Functional Considerations:
Aside from aesthetics, functional requirements are crucial when choosing the right finish for vacuum-formed parts. Consider the following factors:
Durability and Chemical Resistance: Evaluate the durability and chemical resistance needed for the specific application. If the vacuum-formed part will be exposed to harsh conditions, chemicals, or frequent handling, choose a finish that provides enhanced durability and chemical resistance. This ensures the finish maintains its quality and protects the part over time.
UV Resistance and Flame Retardancy: Depending on the intended use, UV resistance and flame retardancy may be important considerations. For outdoor applications or products exposed to sunlight, select a finish that offers UV resistance to prevent fading or degradation. In instances where fire safety is a concern, choose a finish that meets relevant flame retardancy standards.
C. Cost-Effectiveness and Budget Considerations:
While selecting the ideal finish, it’s crucial to keep manufacturing and cost factors in mind. Consider the following:
Cost of the Finish: Evaluate the cost of the finish itself, as well as any additional processing steps or equipment required to achieve the desired finish. Balance the desired finish quality with the project budget to ensure cost-effectiveness.
Manufacturing Compatibility: Ensure the selected finish is compatible with the vacuum forming process and the specific material used. Some finishes may require additional steps or special techniques during manufacturing. Consider any adjustments or modifications needed to accommodate the chosen finish.
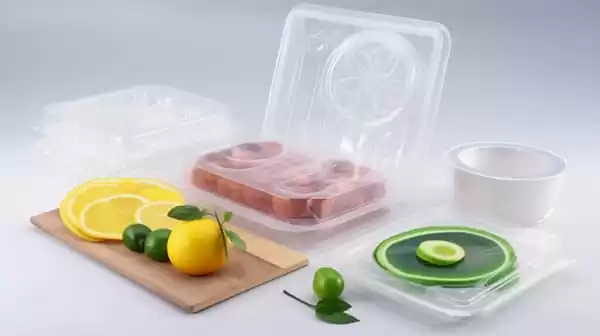
By considering aesthetic, functional, and cost-related factors, you can choose the appropriate finish for your vacuum-formed parts. Whether you prioritize the appearance, durability, or cost-effectiveness of the finish, a well-selected finish enhances the overall quality and performance of the vacuum-formed parts.
Conclusion
In conclusion, selecting the right finish for vacuum-formed parts is of utmost importance in achieving high-quality results. Throughout this article, we have explored various aspects related to finish selection, providing valuable insights to help you make informed decisions.
We began by emphasizing the significance of achieving the right finish for vacuum-formed parts. The finish not only enhances the overall appearance but also ensures durability and protection. It contributes to the aesthetic appeal and functionality of the final product.