Introduction
Vacuum forming is a key manufacturing process used in the production of plastic parts. The technique involves shaping plastic sheets using heat and vacuum pressure, producing products used across industries. We will explore both its time requirements as well as factors influencing it in this article – understanding these factors will allow manufacturers and individuals to optimize production timelines while producing efficient results.
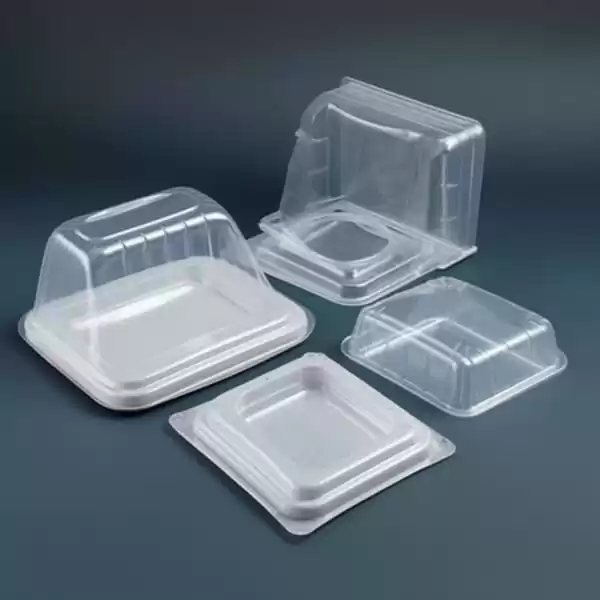
II. Understanding the Vacuum Forming Process
A. Explanation of the Vacuum Forming Process
Vacuum forming is a versatile manufacturing process used to create plastic parts with various shapes and sizes. It involves several stages that contribute to the final product.
Heating:
The process begins by heating a plastic sheet, typically made of materials like polyvinyl chloride (PVC) or acrylonitrile butadiene styrene (ABS). The sheet is heated until it reaches a pliable state, making it easier to manipulate during the forming stage.
Forming:
Once the plastic sheet is heated, it is placed over a mold in a vacuum forming machine. The machine creates a vacuum by removing the air between the mold and the plastic sheet, causing the sheet to be pulled tightly against the mold’s contours. The vacuum pressure ensures that the plastic sheet takes on the desired shape as it cools.
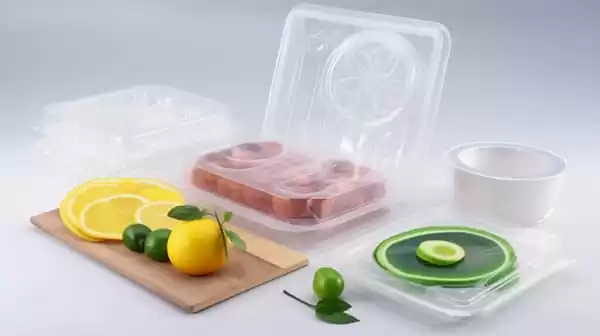
Cooling:
After the forming stage, the vacuum forming machine aids in the cooling process. The machine can have cooling mechanisms such as fans or water jets to expedite the cooling time. As the heated plastic sheet cools down, it solidifies and retains the shape of the mold.
Trimming:
Once the formed part has cooled and solidified, excess plastic known as flash may be present around the edges. Trimming is the process of removing this excess material to achieve the final desired shape and size of the vacuum-formed part. Trimming can be done manually or using automated cutting tools, ensuring a clean and precise end result.
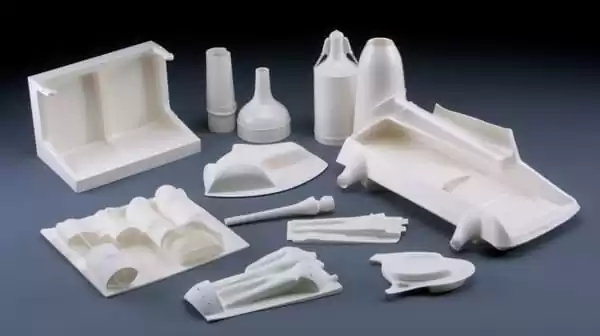
The vacuum forming process offers flexibility and efficiency in creating plastic parts of various shapes and sizes, making it a popular choice in industries such as automotive, packaging, and medical. By understanding each stage of the process, manufacturers can optimize production timelines and achieve high-quality vacuum-formed components.
III. Factors Influencing Vacuum Forming Time
A. Complexity of the Part
The complexity of the part being vacuum formed plays a significant role in determining the overall time required for the process. Parts with intricate designs, undercuts, or complex geometries may take longer to form compared to simpler shapes. Complex parts often require additional mold preparation and careful alignment during the forming stage, which can increase the overall production time.
B. Material Selection
The choice of processing plastic materials used in the vacuum forming process can impact the timeframes involved. Different plastic materials have varying properties and behaviors during heating, forming, and cooling. Some materials may require higher temperatures or longer cooling times, which can extend the overall cycle time. Manufacturers must consider the specific requirements of the part and select an appropriate material that balances performance and production time.
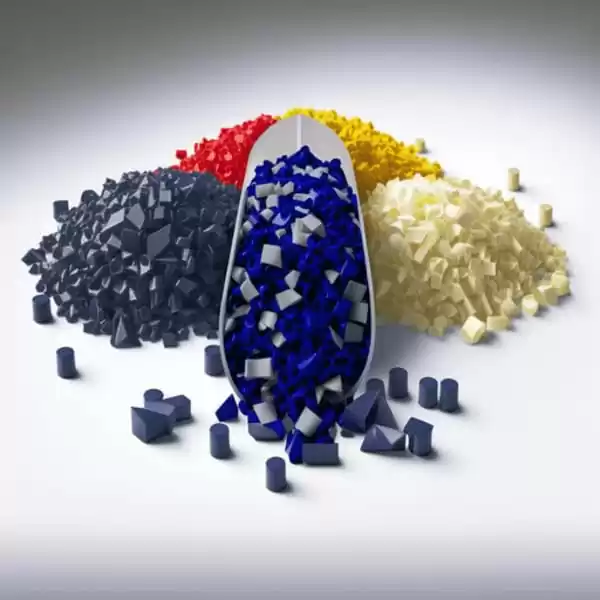
C. Thickness of the Material
The thickness of the plastic sheet being used for vacuum forming also affects the time required for the process. Thicker materials generally require more time for heating and cooling, as heat penetration and cooling rates are influenced by the material’s thickness. Additionally, thicker sheets may necessitate adjustments in using vacuum forming, temperature and cycle times to ensure proper forming and optimal part quality.
D. Equipment and Technology
1. Industrial Vacuum Forming Machines:
The type and quality of the vacuum forming machine used in vacuum forming can significantly impact the production time. Industrial vacuum forming machines often offer advanced features such as precise temperature controls, adjustable forming speeds, and automated trimming capabilities. These machines are designed for efficient and rapid production, reducing cycle times and increasing overall productivity.
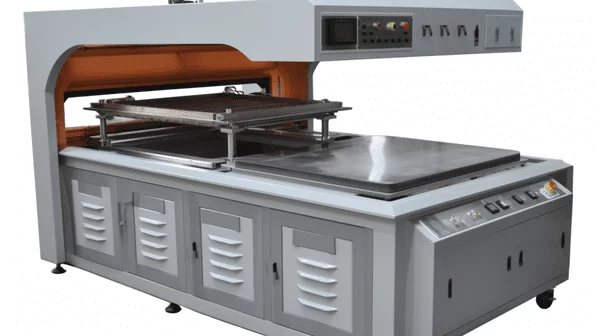
2.DIY Vacuum Forming Machines:
While industrial machines offer high efficiency, DIY vacuum forming machines are more accessible and suitable for small-scale projects. DIY machines may have limitations in terms of heating capacity, forming speed, or cooling mechanisms, which can extend the overall production time. However, they still provide a cost-effective option for prototyping and small-scale production.
Considering these factors and selecting the appropriate equipment and materials can help manufacturers optimize vacuum forming time and achieve efficient production processes.
IV. Applications and Benefits of Vacuum Forming
A. Overview of Vacuum Formed Products and Components
Vacuum forming is a versatile manufacturing process that finds application in a wide range of industries. It is used to create various products and components, including:
- Automotive industry: Interior trim panels, dashboards, door panels.
- Packaging industry: Blister packs, clamshell packaging, trays.
- Medical field: Equipment enclosures, medical packaging, prosthetic devices.
- Consumer goods: Display stands, toys, point-of-sale signage.
- Industrial sector: Equipment housings, protective covers, instrument panels.
- Food industry: Food storage containers, disposable utensils, trays.
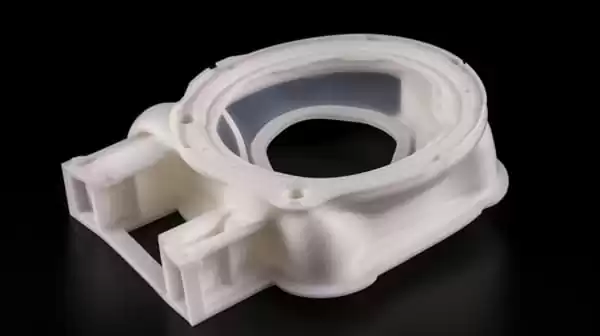
B. Detailed Vacuum Formed Applications in Various Industries
1.Automotive Industry:
Vacuum forming is extensively used in the automotive sector to create interior components such as panels, consoles, and trim pieces. It offers cost-effective solutions for achieving complex shapes and designs while maintaining lightweight characteristics.
2.Packaging Industry:
Vacuum-formed packaging is widely used to protect and display products. It provides clear visibility, product security, and customizability. Blister packs and clamshell packaging are commonly produced through vacuum forming.
3.Medical Field:
Vacuum forming plays a crucial role in medical applications, where sterile and precise packaging is essential. It is used to produce protective enclosures for medical equipment, trays for surgical instruments, and packaging for medical devices.
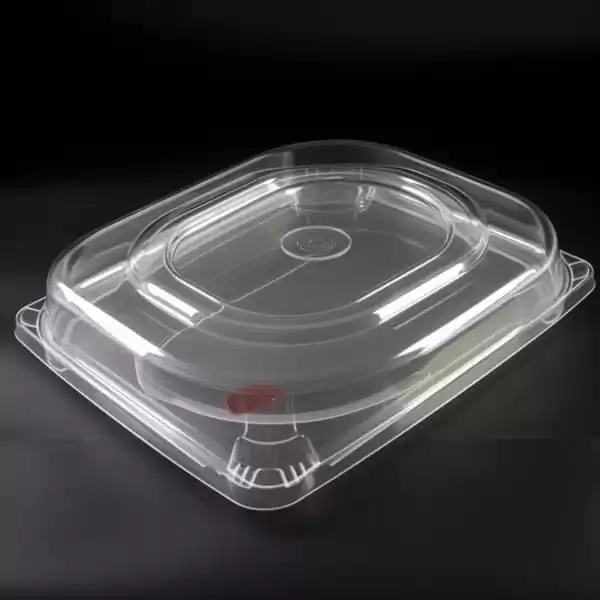
4.Consumer Goods:
Vacuum forming enables the production of a wide range of consumer goods, including toys, point-of-sale displays, and product casings. It offers a cost-effective and efficient method for creating custom-designed products.
C. Benefits of Vacuum Forming Vacuum forming offers several benefits that contribute to its popularity in manufacturing:
1.Cost-Effectiveness:
Vacuum forming is a cost-effective manufacturing process, especially for low to medium volume production. It requires less initial investment in tooling compared to processes like injection molding, making it more accessible to smaller businesses and startups.
2.Faster Production Speeds:
Vacuum forming allows for rapid production cycles, enabling higher production speeds compared to some other manufacturing processes. The ability to heat and form large sheets of plastic simultaneously enhances efficiency and throughput.
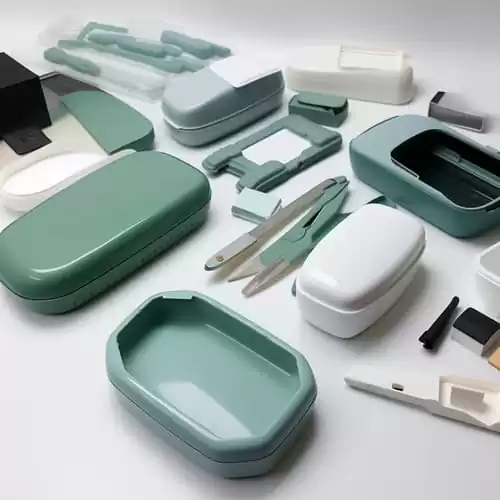
3.Versatility in Material Selection:
Vacuum forming supports a wide range of plastic materials, including polyvinyl chloride (PVC), acrylonitrile butadiene styrene (ABS), and polyethylene terephthalate (PET). This versatility allows manufacturers to choose materials that meet specific requirements for strength, flexibility, or transparency.
4.Customization and Design Freedom:
Vacuum forming allows for intricate designs and complex shapes, providing designers with creative freedom. It offers flexibility in creating prototypes, iterating designs, and producing customized parts according to specific client needs.
By leveraging the benefits of vacuum forming, manufacturers can achieve cost savings, faster production speeds, and greater design flexibility in various industries.
V. A Comparison with Other Manufacturing Processes
A. Comparison with Injection Molding and Other Thermoforming Processes
When considering vacuum forming, it is essential to compare it with other prominent manufacturing processes, such as injection molding and other thermoforming methods.
- Injection Molding: Injection molding is a widely used process for producing plastic parts. It involves injecting molten plastic into a mold and allowing it to cool and solidify. In comparison to vacuum forming, injection molding offers high precision, intricate details, and superior surface finishes. However, it requires expensive molds and is more suitable for high-volume production, making it less cost-effective for smaller runs or prototypes.
- Other Thermoforming Processes: Vacuum forming is one of several thermoforming processes. Thermoforming methods such as pressure forming and twin-sheet forming also shape plastic sheets but involve additional steps or techniques. Pressure forming, for example, applies air pressure to force the heated sheet against the mold for improved definition. Twin-sheet forming involves joining two vacuum-formed sheets to create hollow parts. These methods offer specific advantages for certain applications but may involve higher production costs or complexity compared to traditional vacuum forming.
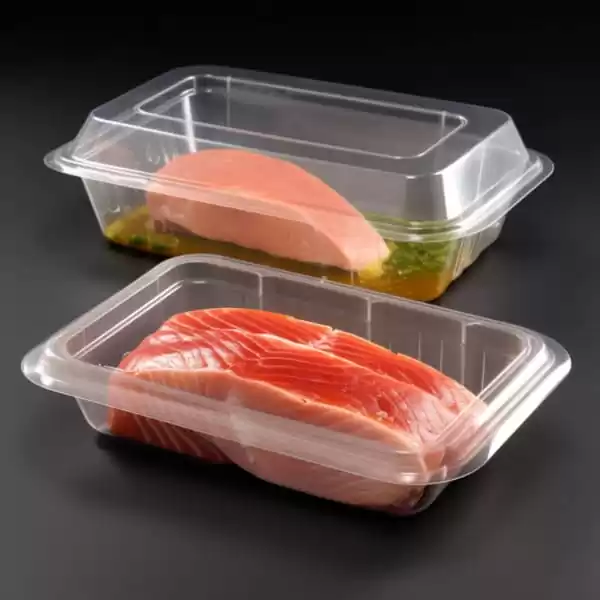
B. Highlighting the Advantages of Vacuum Forming, Including Lower Costs and Flexibility
Vacuum forming offers distinct advantages over other manufacturing processes, which contribute to its widespread adoption in various industries:
- Lower Costs: Vacuum forming requires less initial investment compared to processes like injection molding. The cost of tooling and equipment is significantly lower, making it a cost-effective option for prototyping, short production runs, and customization.
- Flexibility in Design: Vacuum forming allows for flexibility in design and the production of complex shapes, curves, and undercuts. It offers the freedom to experiment with different shapes and sizes, making it suitable for producing customized parts.
- Versatility in Material Selection: Vacuum forming supports a wide range of thermoplastic materials, including ABS, PVC, and PET. Manufacturers can choose materials that align with specific performance requirements, such as strength, durability, or transparency.
- Faster Production Time: Vacuum forming typically offers faster production speeds compared to processes like injection molding. The ability to heat and form large sheets of plastic simultaneously enables higher production throughput.
By considering these advantages, manufacturers can make informed decisions when selecting the most suitable manufacturing process for their specific requirements. While vacuum forming may have limitations in terms of surface finish and intricate details, its cost-effectiveness, design flexibility, and faster production times make it a preferred choice for many applications.
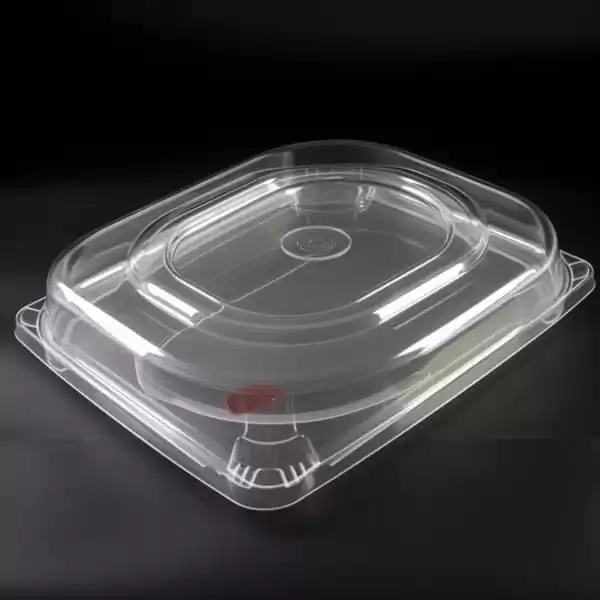
Conclusion
In conclusion, vacuum forming is a vital manufacturing process for producing plastic parts used in various industries. Throughout this article, we have explored the time required for vacuum forming and the factors that influence it. Here are the key points discussed:
- The vacuum forming process involves heating a plastic sheet, shaping it using a vacuum forming machine, cooling it, and trimming excess plastic.
- Factors that influence vacuum forming time include the complexity of the part, material selection, thickness of the material, and the type of equipment used.
- Understanding these factors allows manufacturers to optimize production timelines and achieve efficient results.
- Vacuum forming has a wide range of applications, including automotive, packaging, medical, consumer goods, and industrial sectors.
- The benefits of vacuum forming include cost-effectiveness, faster production speeds, versatility in material selection, and customization options.
It is essential for manufacturers to grasp the factors that affect vacuum forming time in order to streamline their production processes and meet project timelines effectively. With its wide range of applications and numerous benefits, vacuum forming continues to be a valuable manufacturing technique in various industries.
By harnessing the advantages of vacuum forming and staying informed about advancements in materials, equipment, and technology, manufacturers can unlock the full potential of this versatile process for their specific needs.