Thermoforming is a plastic processing technology. The main principle is to heat a flat hard plastic sheet to soften it, then use vacuum adsorption on the surface of the mold, and then form it after cooling. It is widely used in plastic packaging, lighting, advertising, decoration and other industries.
The so-called vacuum forming refers to relying on a vacuum pump to draw a vacuum state between the mold 1 and the heated thermoformed plate (sheet), causing a pressure difference between the upper and lower parts of the plate (sheet), thereby making the plate (sheet) tightly adhere to each other. A method of forming on the surface of a mold. Vacuum forming can be divided into several forms such as single male mold (convex mold), single female mold (concave mold), and no mold.
There are several thermoforming methods used in actual productio: differential pressure molding, cover molding, plunger-assisted molding, suction back molding, opposite mold molding, and twin sheet thermoforming. This blog will introduce you to what twin sheets thermoforming is.

Twin Sheet Thermoforming Principle
Twin sheet thermoforming involves placing two plastic sheets that have been heated to a sufficient temperature and clamping them on a half-closed mold frame, with a blow pin inserted between the two sheets. Compressed air is blown through the blowing needle, and at the same time, the two halves of the mold are evacuated and evacuated to fit into the inner cavity of the two halves of the mold, and the product is obtained after demoulding and trimming.
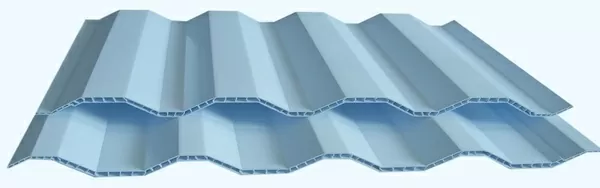
Twin Sheet Thermoforming Process
Twin sheet thermoforming is to heat two plastic sheets separated by a certain distance to a certain temperature, place them on the mold frames of the upper and lower molds, and clamp them. A blow pin is inserted between the two sheets, and the compressed air is blown from the blow pin. Introduce the hollow area between the two sheets, and evacuate the walls of the two closed molds at the same time, so that the sheets fit into the inner cavities of the two closed molds. After cooling, demoulding and trimming, the hollow product is obtained.
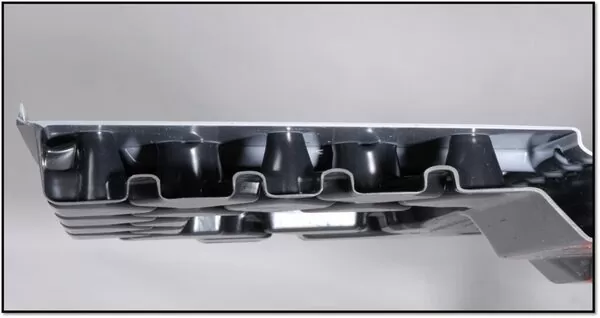
Twin sheet forming involves heating, forming and simultaneous welding of two sheets. The thermoforming machine has a preheating section and two heaters in the device. The two sheets can be heated in both directions. After heating, the sheets are transferred together to a forming device for forming and welding.
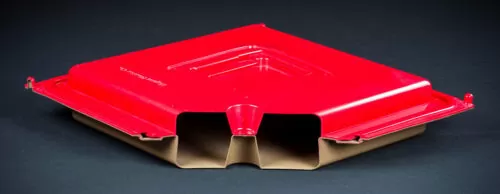
Machinery and equipment: Vacuum passes into the auxiliary plunger, as well as into the double female mold, workbench and lower auxiliary plunger. During the molding process, the middle plate must have at least one ventilation hole for air intake, as a large molding surface, sag must be controlled during the heating process.
Twin Sheet Thermoforming Operation Process
1. Place the lower piece on the lower mold frame.
2. Move the upper mold frame with the middle plate to the insertion position.
3. The top piece is placed on top of the middle panel and closed.
4. Move the heater forward to heat each sheet individually.
5. Move heater back.
6. Move the workbench with the mold up and assist in moving the plug down.
7. Vacuum the table and auxiliary plunger.
8. Cool down.
9. Remove from the mold.
10. Remove the mold frame and take out the product.
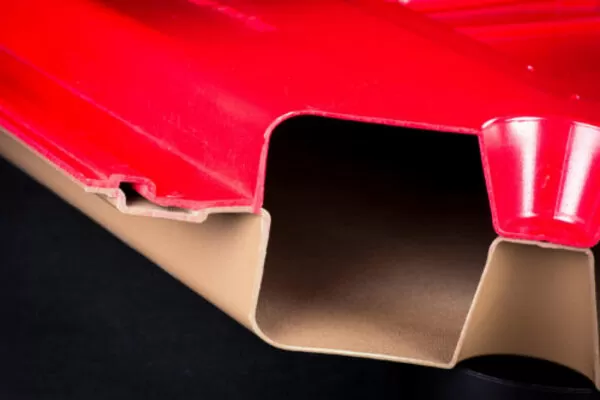
Advantages and Disadvantages
Advantage
1. High strength to weight ratio.
2. Mold cost is cheaper than blow molding.
3. Good rigidity and complete structure.
4. The closed cavity makes the twin sheet parts suitable for a wide range of applications.
5. Compatible with most thermoplastics.
6. The two pieces can be joined without snapping or welding.
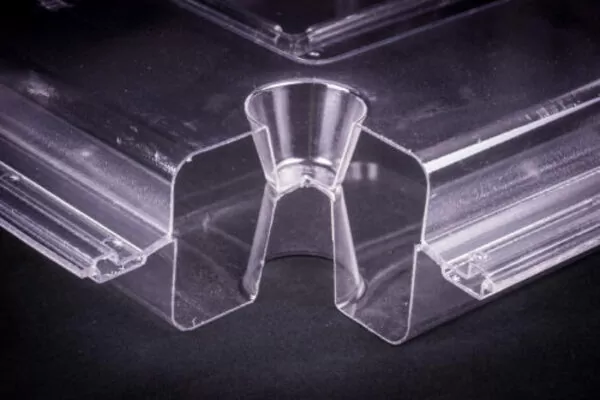
Disadvantage
1. Design is limited.
2. Auxiliary plungers cannot be used on ordinary thermoforming machines.
3. At large draw ratios, the wall thickness distribution is uneven.
4. Due to the high molding temperature, the toughness of the finished product decreases.
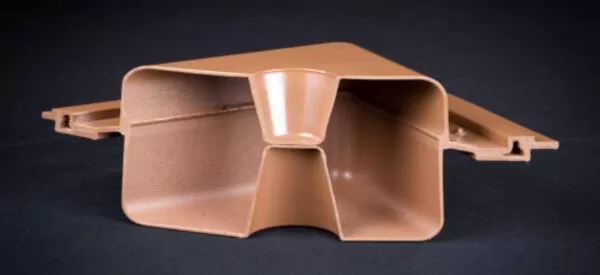
Application
Automotive Industry
In the automotive sector, twin sheet thermoforming is employed to manufacture twin sheet part that require a strong bond and a hollow structure, such as fuel tanks, dashboard components, and door panels. These parts benefit from the process’s ability to produce complex shapes with a high-quality finish, contributing to lighter vehicles with improved fuel efficiency and aesthetics.
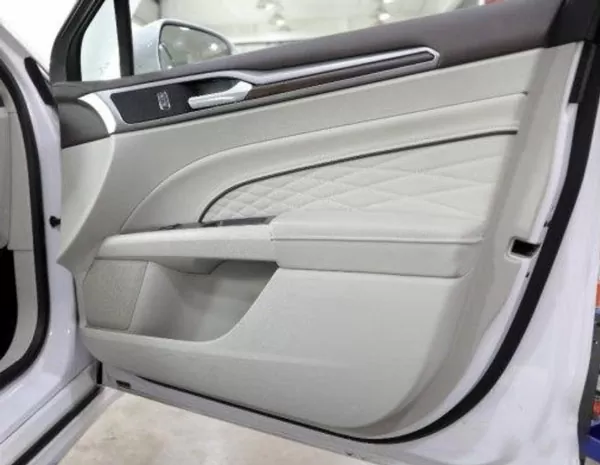
Material Handling and Packaging
For material handling, custom plastic manufacturing, and packaging solutions, twin sheet thermoforming is utilized to create pallets, dunnage trays, and containers. These products are designed to be robust and durable, capable of withstanding the rigors of transportation and storage. The process allows for the integration of features such as handles, latches, and reinforcement ribs without the need for additional assembly, enhancing functionality and strength.
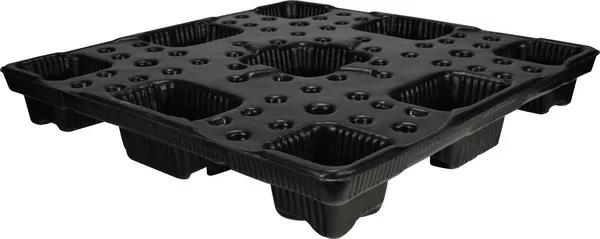
Medical Devices
The healthcare and medical device industries also take advantage of twin sheet technology for its ability to produce sterile, lightweight components such as surgical tables, enclosures for medical equipment, and trays for medical instruments. The ability to form complex shapes ensures that products meet the strict requirements and standards of the medical field, while the hollow structures support ergonomic and lightweight designs.
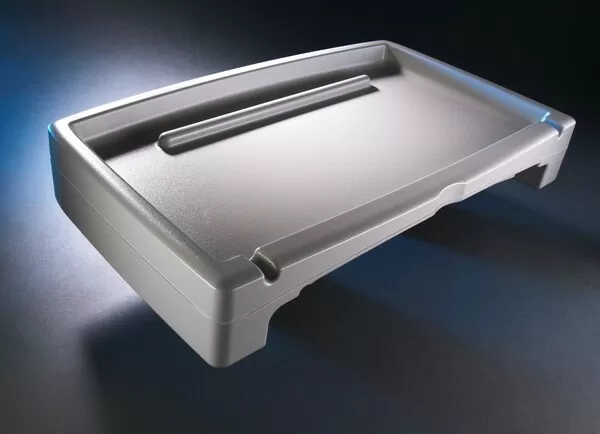
Recreational Products
In the world of recreational products, twin sheet thermoforming is applied in the creation of kayaks, surfboards, and bodies for all-terrain vehicles (ATVs). The process offers a superior strength-to-weight ratio, ensuring that these products are not only durable and able to withstand impact but also lightweight for ease of use and transportation.
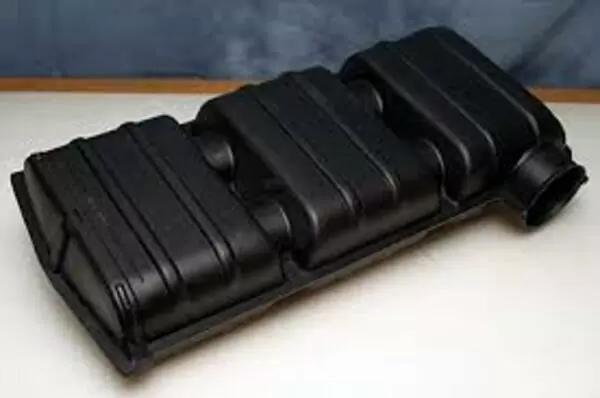
HVAC Systems
Components for heating, ventilation, and air conditioning (HVAC) systems, such as ductwork and venting parts, are also produced through twin sheet process pressure forming. This technique provides the necessary precision and strength for HVAC applications, along with the ability to integrate insulating properties by incorporating foam between the sheets, enhancing energy efficiency.
Twin sheet thermoforming products also have many applications. For example, filling the hollow space of two sheets with polyurethane hard foam can give the product very good thermal insulation function, and is very suitable for use in large refrigerated displays in supermarkets and ice cream shops. On the cabinet. Or add steel pipe to increase the weighing weight.

Case
Twin Sheet Thermoforming: Dedicated Thermoforming Pallets for the Automotive Industry
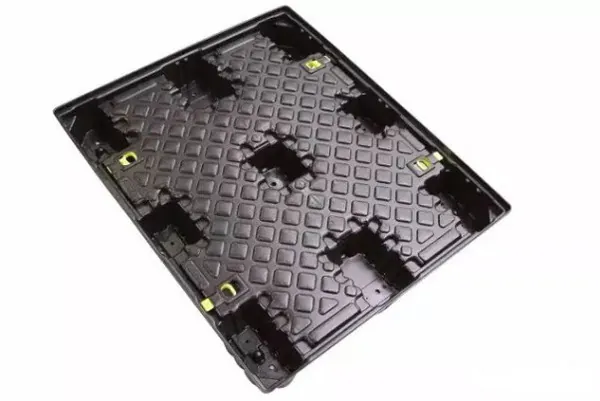
This is a high-density polyethylene (HDPE) pallet produced using twin sheet thermoforming services. The so-called twin sheet thermoforming technology is to combine two different HDPE sheets during the forming process. There is a hollow structure in the middle of the two HDPE sheets, which can carry a lot of weight and avoid hitting these mechanical assembly parts during transportation and handling.
Molding process:
First, two sheets are placed at designated positions on the orifice plate of the vacuum forming machine, and then the clamp automatically lowers and a moving intermediate frame brings in the other two sheets. Two sets of halogen lamp heaters will quickly heat the four sheets according to the heating path set by the computer. Precise temperature control is achieved through a fine-hole grid of photocells. During this process, it is necessary to ensure that the twin sheet thermoforming materials is flat when heated.
Then, the mold is closed. Under the action of a clamping force of hundreds of thousands of Newtons, the two sheets are combined into a strong structural panel. By introducing a certain pressure of air between the two layers of sheets, the sheets and the mold can fit more closely, and it can also have a certain cooling effect. After the mold has cooled, immediately open the moving middle frame and remove the two formed pallets.
Finally, the robot takes the formed product out of the mold, and then puts the next set of four preheated sheets into the mold to start the next production cycle. One product can be produced every 5 minutes.
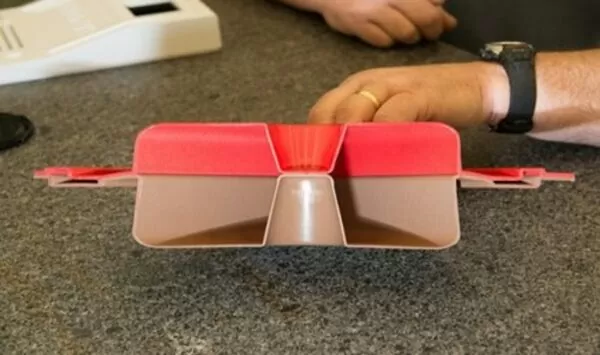
Conclusion
In the field of plastic molding, whether it is thicker sheet or thinner sheet, thermoforming can provide a good solution. Compared with injection molding, rotational molding, and blow molding, twin sheet thermoforming offers a diverse range of applications due to its unique ability to create strong, lightweight, and complex parts. With advancements in technology, the possibilities for twin sheet thermoformed products continue to expand, driving innovation across multiple industries. This manufacturing process provides a cost-effective solution for producing high-quality, durable components that meet specific design and functional requirements.