If you’re interested in how everyday objects are made-from medical devices and food packaging to car components, specialty food companies and smartphone cases-thermoforming will captivate you. Unlike injection molding, this incredible technology turns a flat piece of thermoformed plastic into almost anything!
There are several thermoforming methods used in actual production: differential pressure molding, cover molding, plunger-assisted molding, suction back molding, opposite mold molding, female mold and male mold thermoforming, thin gauge thermoforming, heavy gauge(thick gauge) vacuum forming and twin sheet forming.
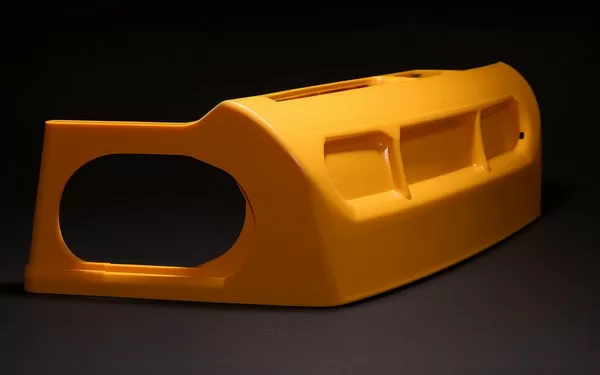
It doesn’t matter whether you work in the industry already, want to set up your own business one day or just enjoy finding out how things are done because here we have an amazing list: The Top Ten Things There Are To Know About Thermoforming. We hope after reading it not only will you understand better what goes on during this process which has so many applications but also get some ideas for cool new products too.
Versatility of Thermoforming
Discover previously unexplored industry sectors in which thermoformed products have found a place, thanks to the flexibility of the materials and processes used. This part also looks at some everyday uses for thermoformed plastics that readers may find unexpected—as well as pointing out possibilities they hadn’t thought about before!
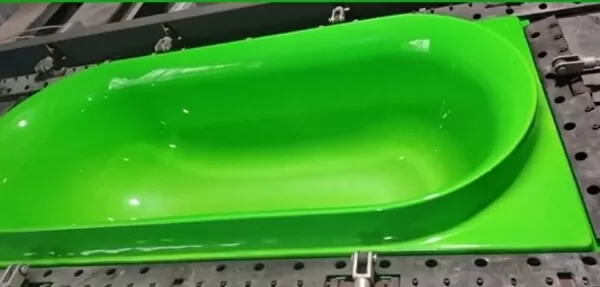
1. From Rigid to Soft—The Materials of Thermoforming
Were you aware that thermoforming has the ability to handle an assortment of materials — from rigid ones like PVC, all the way to flexible films such as TPU?
In fact, vacuum forming encompasses such a broad range of material possibilities that finished products can possess vastly different characteristics: Think along the lines of clear PET(polyethylene terephthalate) strength found in many retail packages vs. the soft stretchiness common among LDPE items including disposable medical gear and HDPE(high density polyethylene) or other inexpensive materials.
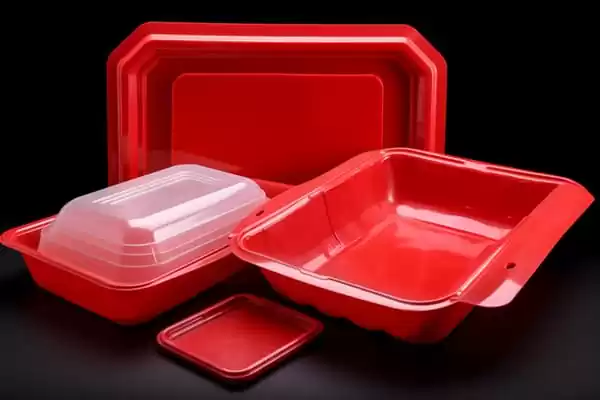
2. Customization Beyond the Mold
Contrary to popular belief, thermoforming customization involves more than just the mold. In fact, professionals in this field can tweak various factors throughout both the heating process and shaping phase –– right down to a level of intricacy which may astonish even keen-eyed onlookers!
Adjustable plastic sheets heating profiles, vacuum pressures, and cooling methods play pivotal roles in achieving aesthetics and functionality that cater to specific consumer demands.
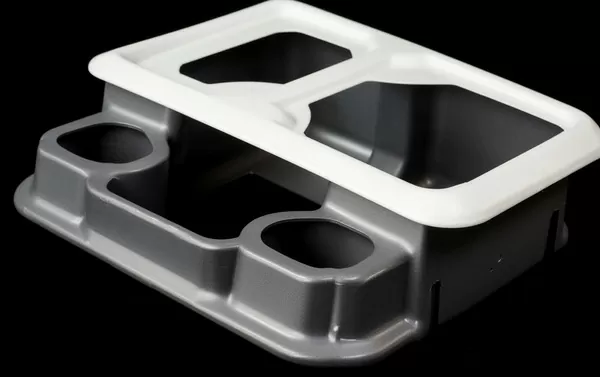
3. Thermoforming in Unlikely Places
Believing that thermoformed goods are only for consumers? Think again. The aerospace and defense industries profit from thermoformed parts’ weight savings and design adaptability. Moreover, thermoforming finds application even in architecture – such as skylights or interior panels made this way.
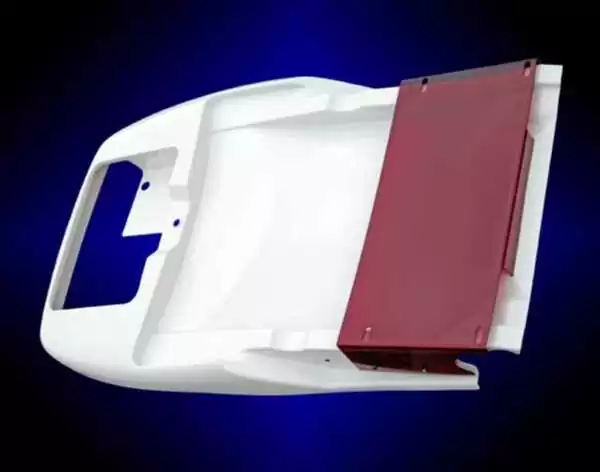
Sustainability in Thermoforming
As people become more aware of the environment, making sure things are sustainable is now a big part of how we design and make stuff. In this blog we look at thermoforming – how it’s changing to keep up with the demand for greener ways of working (and recycled plastics too).
4. The Eco-Friendly Side of Thermoforming
Thermoforming in the present day is greener than older ways of making things. Vacuum forming can cut its environmental impact a lot because it uses materials better and does energy-saving processes. Plus, it goes further towards being eco-friendly when products are made from recycled or biodegradable substances – as long as they meet tough industry rules about quality too!
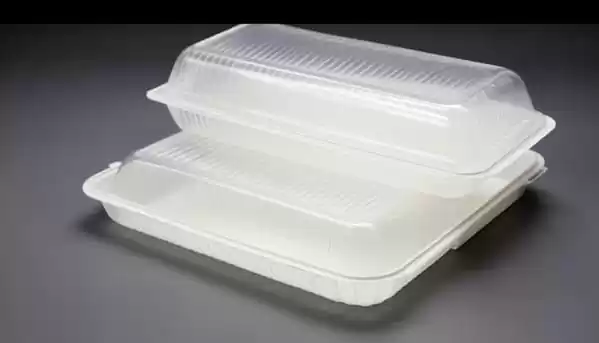
5. Durability of Thermoforming
When individuals consider single-use plastics, they usually think about things like cups, blister packaging and containers. However, thermoforming can also be used effectively for making sturdy items which last a long time.For instance, car sunroofs or fridge inner linings made through this process are tough products with extended periods of use – so they don’t fit into the throwaway image many people associate with plastic manufacturing!
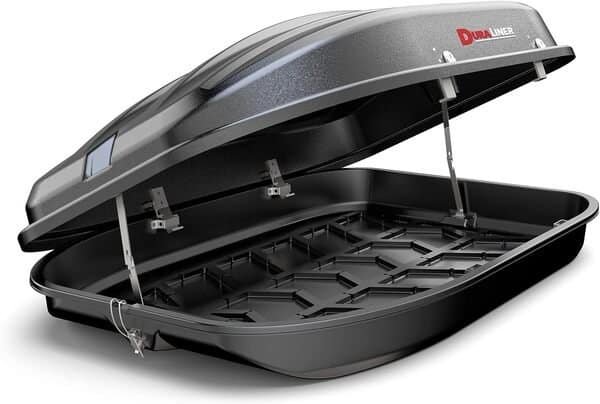
6. The Composite Future—Blending Materials for Sustainability
Thermoforming goes beyond plastics alone. By investigating composite materials that blend the durability of traditional plastics with renewable or biodegradable components, manufacturers are leading towards an eco-friendlier and sustainable sector. This opens up fresh prospects – both for how products can perform and how we can best look after our environment.
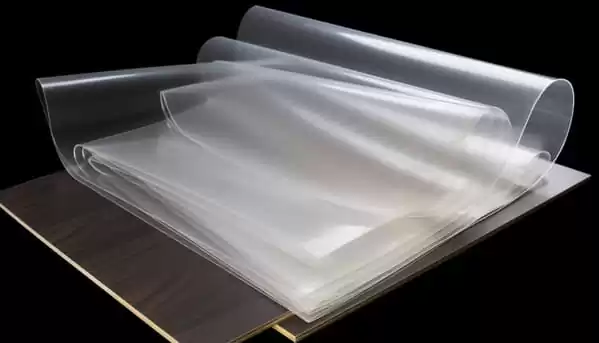
Technical Depth and Innovation in Thermoforming
The following three insights delve into the complexities of thermoforming technology. They provide a deeper understanding of how this industry is evolving, highlight some exciting advances being made – which may well have a big impact down-the-line!
7. High-Tech Thermoforming—The Role of Robotics and Automation
In the past, thermoforming relied heavily on human effort. Nowadays, though, things have changed – robots and automation are here to help us be super-accurate and do things efficiently!
We’ll explore how these technologies fit into a thermoforming job from start to finish; for example with materials management or cutting tasks. With all this in place you can have one sleek system producing top-notch items nonstop.
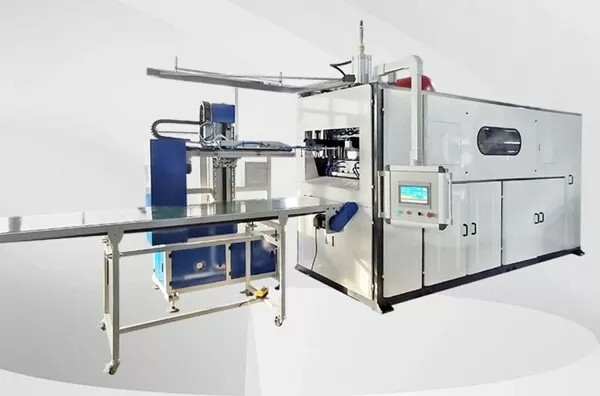
8. 3D Printing and Thermoforming
The tooling industry is undergoing a revolution thanks to additive manufacturing (3D Printing). Why? Because this process delivers molds faster than ever before with designs that were once considered impossible! Seeing how using 3D printers helps create better molds & more effective tools overall – pushing boundaries around thermoforming while also speeding up new product development.
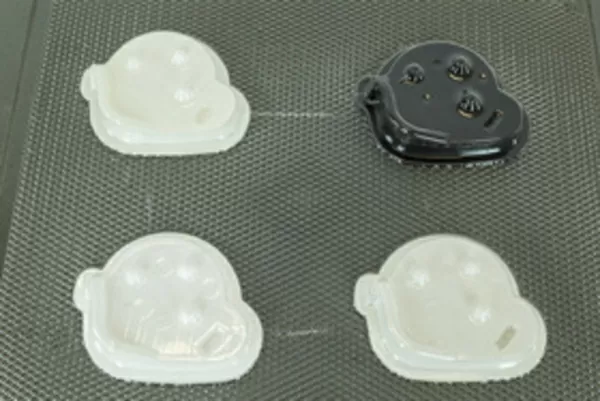
9. The Role of Simulation and Virtual Prototyping
Were you aware that an entire thermoforming process can be predicted using virtual prototypes before any sheets are heated or molds are milled?
By utilizing state-of-the-art simulation software like this, it is possible to work through any problems in advance. As a result, manufacturers can enjoy cost savings as well as increased efficiency and reliability; plus there’s no need for them spend extra time waiting around while things get sorted out!
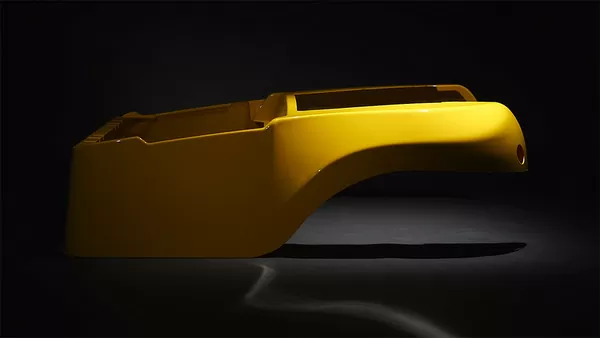
The Human Factor—Skills and Innovators in Thermoforming
Although technology plays a major role in thermoforming, it is ultimately human creativity that drives this field. We will examine the wide range of abilities needed for success in pressure forming – and profile some trailblazing individuals who exemplify them!
10. Nurturing the Next Generation of Thermoforming Professionals
In addition to technology and resources, the thermoforming sector depends on highly trained workers. Both equipment operators and engineers have important parts to play in this field.
We examine key educational courses plus schemes for continuing professional development: such initiatives are vital if the industry is to nurture the next generation of skilled staff with vision – people who can take things forward.
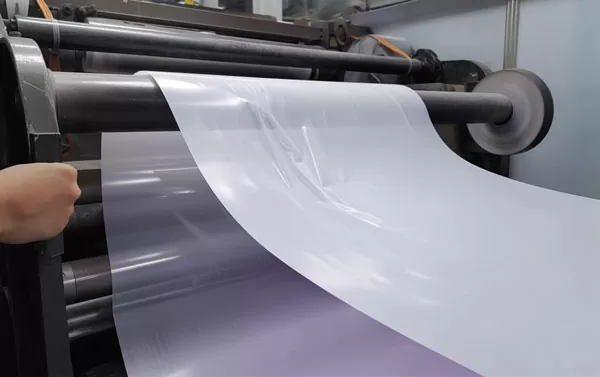
The Future of Thermoforming
Where is the future of thermoforming headed? Ancillary with this time-honored process are new technologies like 3D printing, which means there are now fresh design and production possibilities on the horizon. Furthermore, because people care about sustainability these days—they want to make sure what they buy doesn’t harm either environment or human rights—there is also progress being made when it comes to both materials usage and how things get done overall: expect more changes soon!
Thermoforming stands at an exciting point in its development. Technological advances, sustainability efforts, and changes in what customers want are all coming together to shape tomorrow’s thermoforming processes.
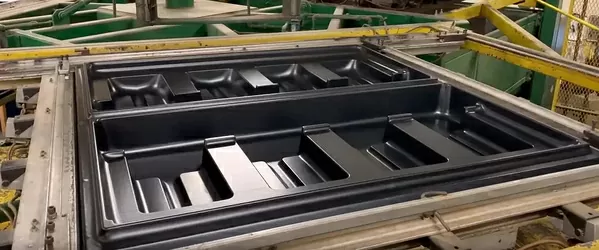
Thermoforming itself involves taking a plastic sheet, heating it until it becomes flexible enough to mould, then forming it into a desired shape inside a mould. After any necessary trimming, what comes out can be anything from packaging materials through to components for cars: no wonder so many different industries use this technique!
Conclusion
By examining the plastic thermoforming process in depth, we have discovered numerous uses, efforts towards sustainability, technical advances, and human stories that make this field fascinating. Vacuum forming doesn’t just help make things – it also offers a glimpse into non-stop creating possibilities for design concepts to become actual objects; ones moreover which can be produced sustainably over time. Whether you already know lots about plastics processing or are simply someone who wonders how things like food plastic packaging or protective packaging get made; once you’ve seen what thermoforming does up close (with its endless options) we betcha won’t look away!