Thermoforming is a highly adaptable manufacturing method used to produce many different items – from packaging for everyday consumer goods such as blister packs to complex components used in medical devices. One of the major challenges for anyone working with thermoformed products is achieving and maintaining a wall thickness distribution of material.
A single flaw can destroy the strength or aesthetics of the finished product, which means understanding the cause of thickness variation is crucial for designers and manufacturers themselves.
In manufacturing, maintaining product consistency is critical. If products vary too much in size or quality, it can have a negative impact on how users view the product itself and the brand that makes it.
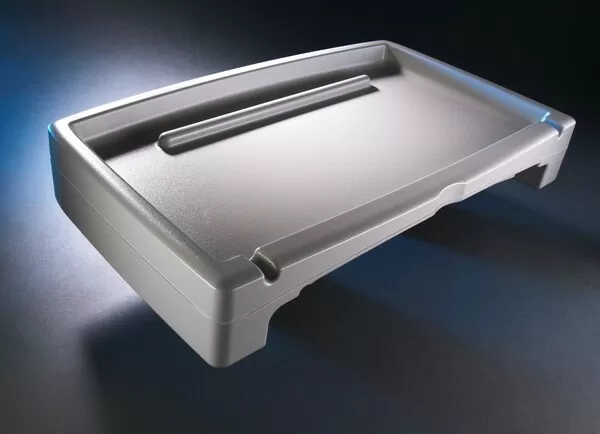
With thermoforming (which is used to make many different products we use every day), it’s not always easy to get a uniform thickness. In this blog post, we’ll explore why changes occur during production runs and what companies can do about them.
This blog post reveals the complexity behind thickness variation in thermoformed products and provides an understanding of how to solve this little-understood manufacturing problem.
We’ll break down the different causes of thickness variation and provide practical tips for reducing their impact – so you can be confident that your thermoformed products always meet high standards.
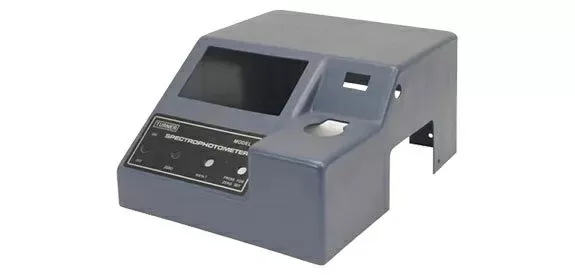
Thermoforming Process
Thermoforming is the name of a manufacturing process that involves heating a plastic sheet to make it malleable and then pressing it against a mold using vacuum suction (vacuum forming) or air pressure (pressure forming) to shape it.
There are so many different things you can create using this extremely adaptable technology – from basic pallets all the way up to complex parts used in cars! However, there is one thing that people who work with thermoforming absolutely want: consistency in thickness. why is it like this?
In addition to the appearance itself being important, uniform layers also affect how strong these objects are; their ability to withstand heat and much more.
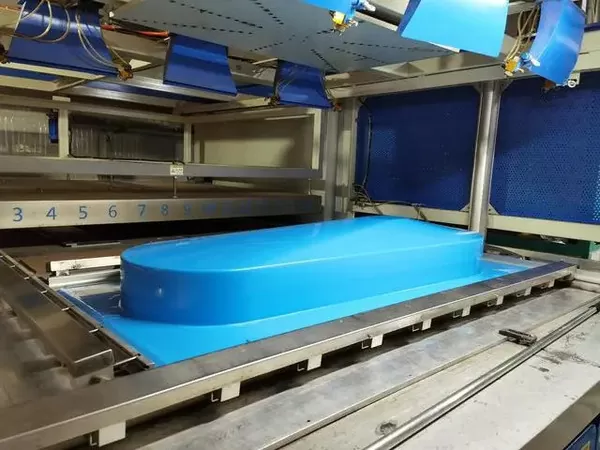
Demystifying Thickness Variation
The thermoforming process begins by heating a piece of thermoplastic material until it becomes pliable. After heating, the plastic piece is placed over the mold so that it conforms to its shape – thus creating an object using only the plastic piece! However, sometimes after cooling, thickness irregularities may occur, causing the product to not meet the manufacturer’s specifications.
On the other hand, the causes of thickness changes in thermoformed products, such as those formed through the plug-assisted thermoforming process using extruded sheet material, are intricately linked to factors including the glass transition temperature, mechanical properties, and elastic deformation.
The Heat Factor
The temperature of the sheet plays a vital role in thermoforming. Heat softens materials and affects their behavior. If the heating is uneven, some parts may become softer (and therefore stretch more) than others. Most importantly, this stretching action causes thickness changes.
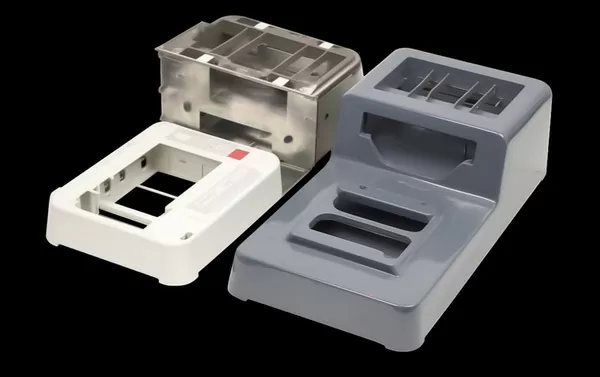
Material Variation
Different thermoplastic materials have different material properties, including how they respond to heat and force. This can cause them to behave very differently when thermoformed: some may become thicker in places when heated; others may become thinner in places.
Tooling Tensions
Having well-designed and properly maintained molds and trimming tools is crucial. If there are any defects, deterioration, or misalignments in it, the material will not be compressed evenly, so some areas may become thinner while others may become thicker than needed.
Choosing the right equipment is also important: you need equipment that is suitable for the specific material and ensures that all components perform optimally.
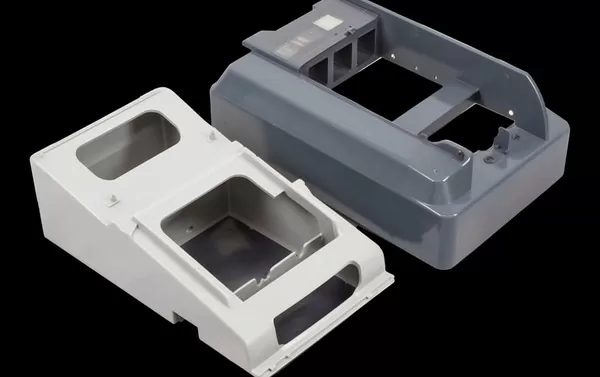
Processing Steps
Throughout the entire process, from heating to forming to cooling, operators must ensure consistency. Any delays, sudden temperature changes, or operating errors can cause thickness issues. These steps require tight control and skilled supervision to avoid deviations.
Major Causes of Thickness Variations
There are many factors that cause variations in the thickness of a thermoformed product, which can be divided into four broad categories: the way the material is distributed during the molding process; the shape and structure of the mold; the temperature range, pressure, or time settings at each stage; and the overall material quality.
Material Distribution
Even distribution of the plastic sheet during thermoforming is crucial: any unevenness will show up as uneven product thickness. Various factors – among them the sheet temperature, the stretching force of the mold and the speed of the molding process all affect whether the material is evenly distributed here!
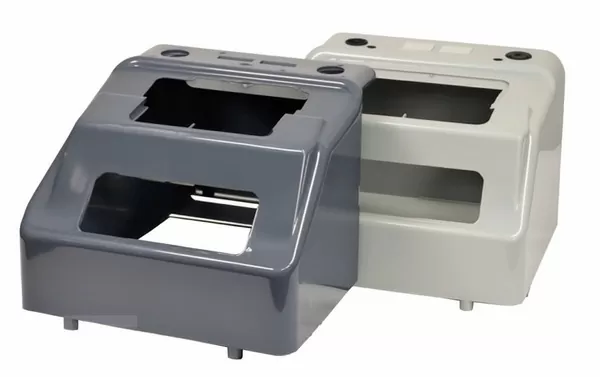
Mold Design
The design of the mold also affects the thickness of the thermoformed product. If the mold is not designed properly, the material may stretch too much and become thin in some places, while it may be too thick in other places. Symmetry, material flow and radii in the mold play an important role in ensuring even distribution.
Process Parameters
Thermoforming is a precise fit and delicate balance between time, temperature and pressure. One incorrect operation in these processes can cause significant changes in the thickness of the product.
For example, too high a temperature can cause over-stretching, and insufficient cooling time can cause warping and dimensional instability.
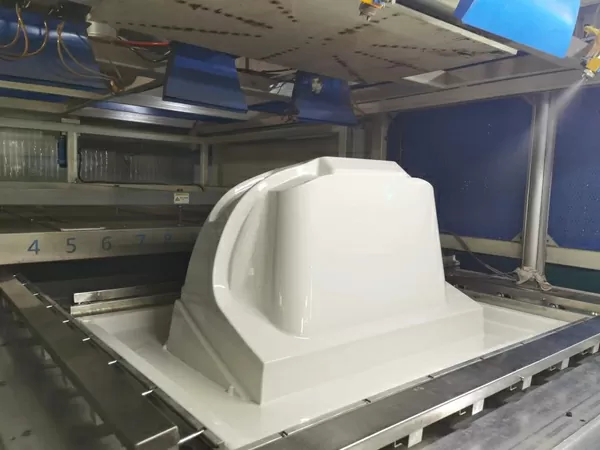
Quality of Material Used
The thermoforming process is directly affected by the quality of the material chosen. When raw materials are not of the same thickness as they originally were, it means that the product ends up being of different thicknesses as well.
Inferior materials can also cause differences in the degree to which they flow, stretch, or cool during production. Such materials can cause differences from one item to another.
Strategies to Minimize Thickness Changes
Resolving thickness issues in thermoforming requires a multifaceted approach. It involves a combination of process optimization, mold design improvements, and careful material selection and preparation.
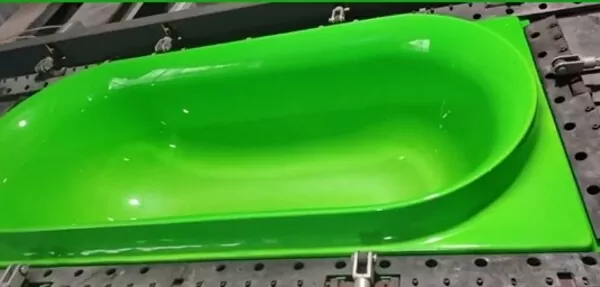
Process Optimization
Careful fine-tuning of the thermoforming process is a critical step in the forming process. This may involve changing forming temperature, vacuum or pressure levels, or cycle times.
If the heating is precise and controlled, it helps ensure that the material doesn’t stretch too much, but it’s just as important to maintain the same condition during cooling if consistency is to be maintained throughout the process.
Mold Design Improvement
Revisiting mold design can have a profound impact on thickness consistency. When trying to get material distributed more evenly throughout an object (or objects), changing things like geometry, surface texture, and even ventilation can all be helpful.
Software simulations will show what will happen with different modifications so that designers can pick the modifications that are best suited to reduce any unwanted changes.
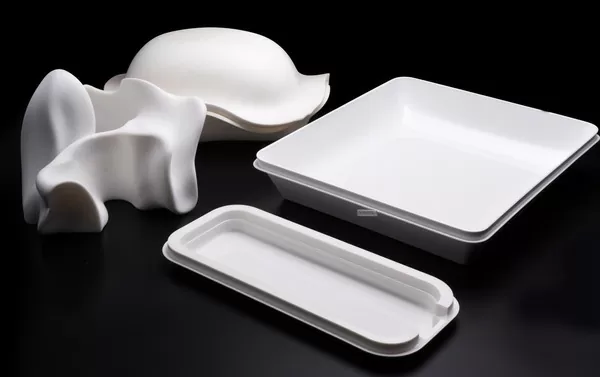
Material Selection and Preparation
Choosing the right materials and ensuring proper preparation are very important steps. The material must be consistent and of uniform thickness throughout.
If you heat or condition the material beforehand, it’s less likely to change overall – meaning it should work better when you thermoform it.
Addressing the Root Causes
Understanding the causes is just the first step. In this section, we look at how to mitigate the issues that lead to thickness changes in thermoformed products.

Mastering the Art of Heating
If you want a high degree of consistency in the final product, you need to try to make sure everything is the same throughout the process. To ensure even heating, consider purchasing a heating system with a radiant or infrared heater, which distributes heat more evenly.
Preheating the sheet is also a necessary step to prevent severe temperature gradients that can lead to uneven heating patterns.
Material Selection and Preparation
The final thickness of the product will be affected by the material chosen. If the material has high melt strength, it is less likely to thin during processing. Those materials with a denser molecular structure also resist stretching better, so they are less likely to thin out excessively.
Another factor that affects consistency is making sure the moisture is removed from it beforehand: when heated, these molecules may produce steam, which can form bubbles or change its thickness.
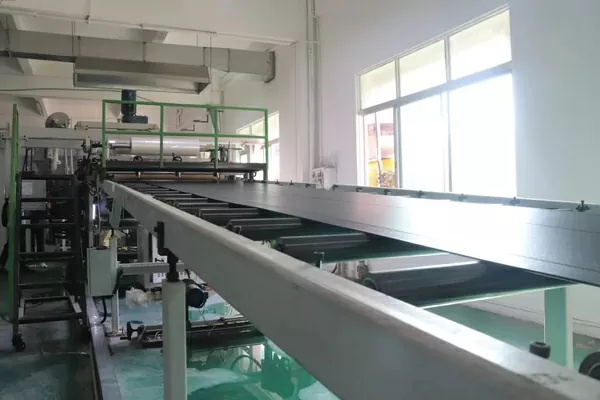
Fine-Tuning the Mold
Routine maintenance of molds is very important, making sure they are not damaged or worn too much, and repairing or replacing parts as needed. Invest in high-quality, precision-made tooling, and consider using adjustable molds to help balance thickness during the molding process.
Perfecting Process Control
Develop a robust control system that monitors and adjusts process parameters in real time. These systems can range from simple alarms that sound when a parameter goes out of range to complex computer-integrated setups that allow for automated adjustments.
Operator Expertise and Training
The importance of people in the operational process cannot be overstated. It is critical to train your employees so that they can identify and deal with possible thickness-related issues.
They need to be able to make changes as needed during the job to resolve any issues arising from changes in the materials used or the way the work is done.
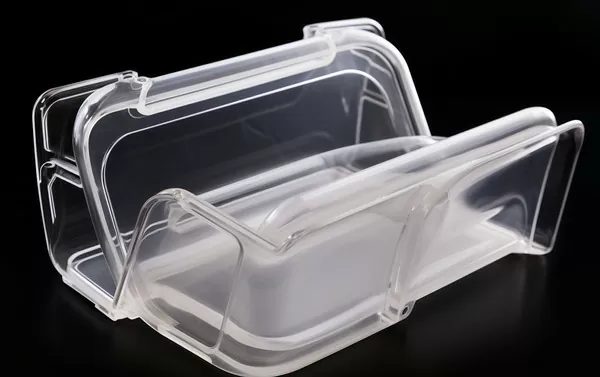
Quality Control in Thermoforming
Ensuring consistency in your thermoformed products is an ongoing process. Implementing rigorous quality control measures can catch thickness deviations before they become costly defects.
1. In-line Thickness Measurements
In order to monitor the thickness of a product during the manufacturing process, it is important to use sensors or meters. This will allow any problems in the process to be identified and corrective measures to be taken immediately – something that would not happen if measurements were only taken at the end.
2. Regular Product Sampling
By regularly taking samples from different points within a batch or between batches, you can learn not only what may be happening within each batch, but also whether there are overall changes worth noting (such as wear and tear on tools).
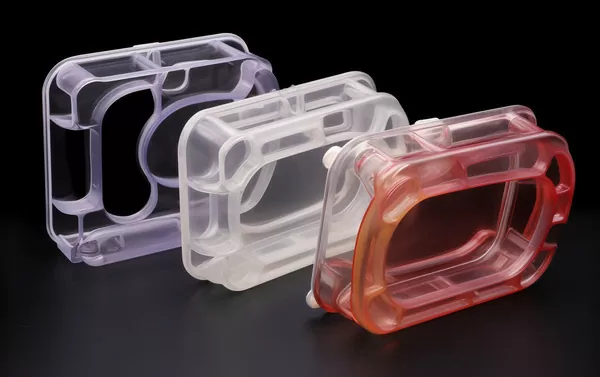
This analysis also allows for better control: if adjustments prove necessary after a sample test has revealed a result, all available information can be used (i.e. readings taken through continuous monitoring plus results obtained to date following inspection/sampling exercises) ) to examine them further.
3. Record-Keeping and Analysis
Make sure to keep complete documentation of every production run you make, such as the process parameters used and any issues encountered along the way. Take the time to review this information regularly so you can spot correlations and be able to make informed choices about how best to improve your processes.

Conclusion
Manufacturers should not be discouraged by the complexity of thickness variation in thermoformed products; rather, they should see this as reason to take action. Through thorough preparation, close process management, and continuous development of mold technology, it is possible for companies to produce uniform products of superior quality.
In an industry that seems real, companies have no choice but to ensure that their customers receive consistently reliable products that don’t suffer from negative side effects, such as thickness-related defects or aesthetics, from order to order (see stand up). If enough attention is given, thermoforming can become something akin to a rigorous scientific discipline.
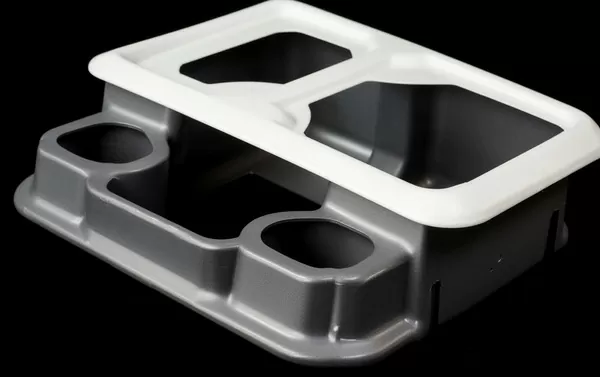
Thickness fluctuations are a common problem with thermoformed products, but they don’t have to be a damaging factor. Careful consideration of the nuances involved in air pressure thermoforming; taking proactive steps with material selection/preparation; honing tools for best results; exercising strict control throughout the machining process and keeping quality control measures at the forefront can maximize Reduce or completely eliminate such variations in the product.
This precision will help ensure compliance with regulations and meet customer needs/expectations; it will also reduce waste while streamlining the manufacturing process.
When you encounter thickness variation issues with your thermoformed products, with this guide, you’ll be prepared to address the issue head on. Remember, reliable thermoforming requires uniformity first – if you take the time to double-check everything, there’s no reason why every product shouldn’t be beautiful!