Vacuum thermoforming is one of the most commonly used molding methods for plastic products. It is a secondary molding technology that uses thermoplastic sheets as the molding object. Vacuum thermoforming is an old molding process. Due to continuous development and changes, it is now highly automated and mechanized, and no waste materials are produced, and 100% of raw and auxiliary materials are turned into finished products. Fully produced on an assembly line.
Thermoforming can be divided into vacuum forming, pressure forming, twin sheet forming, male mold forming, female molding, heavy gauge thermoforming, light gauge thermoforming, etc.
Plastic protective covers are used more and more widely in industrial life, with a wide range of colors, bright colors, unique shapes and rich connotations, which fully embody the creative ideas of industrial designers. There are many types of accessories for mechanical plastic thermoforming processing, and the uses of mechanical plastic shells produced and processed from different materials are also different. During the processing of plastic casings, we must not only consider practicality, but also consider issues such as aesthetics. Therefore, the processing of plastic shells is a relatively complicated process.
So why is it so popular?

Heavy Gauge Thermoforming
Heavy gauge thermoforming is a process in which a plastic sheet is heated to forming temperature, stretched onto a mold, and then pressed against the mold using a vacuum. The final shape, once cooled and hardened, retains the shape of the mold, allowing for intricate and accurate detailing. It is a cost-effective, flexible and efficient technology that can be used in industries including medical devices, aerospace, food packaging, machine housing manufacturing and more.
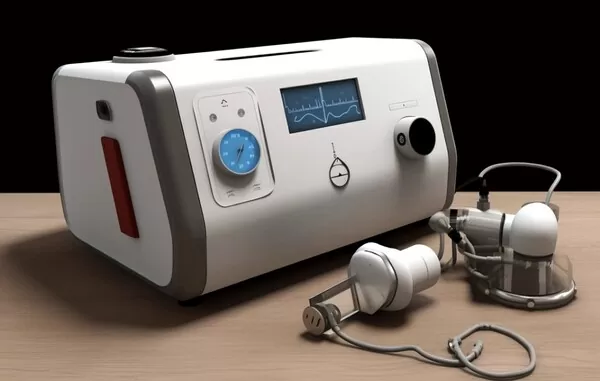
Physical Properties of Thermoforming Raw Materials
1. Most plastics have good corrosion resistance to chemicals such as acids and alkalis. In particular, polytetrafluoroethylene, commonly known as the king of plastics, is even more chemically stable than gold. It will not deteriorate after being boiled in a polytetrafluoroethylene solution for more than ten hours. It is an ideal corrosion-resistant material.
2. Plastic is a lighter material with a relative density ranging from 0.90 to 2.2. This characteristic allows plastics to be used in the production of products that require weight reduction and easy transportation.
3. Ordinary plastics are poor conductors of electricity, and their surface resistance and volume resistance are very large, which can reach 109-1018Ω in numerical terms. The breakdown voltage is large and the dielectric loss tangent value is small. Therefore, plastics are widely used in the electronics and machinery industries. Such as plastic insulated control cables.
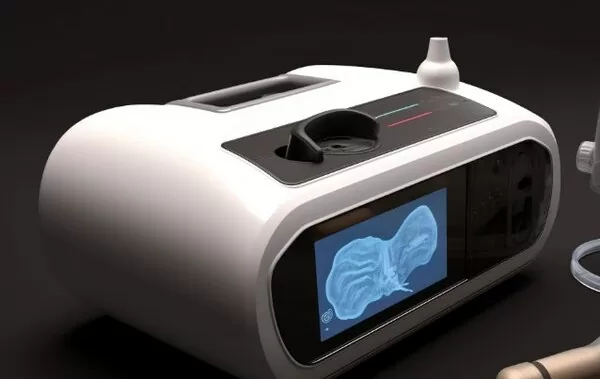
4. In terms of mechanical properties, its impact strength is excellent. Some plastics are hard and some are soft. Judging from the mechanical properties of plastics such as hardness, tensile strength, elongation and impact strength, they are widely distributed and have a lot of room for use. Because plastic has a small specific gravity and high strength, it has a high strength ratio. Excellent wear resistance and good stability.
5. Generally speaking, the thermal conductivity of plastic is relatively low, equivalent to 1/76-1/229 of steel. The micropores of foam plastic contain gas, and its heat insulation, sound insulation, and shock resistance are better. In terms of thermal insulation capacity, single-glass plastic windows are 39% higher than single-glass aluminum windows, and double-glass windows are 55% higher. After combining plastic windows with insulating glass, it can be used in residences, office buildings, wards, and hotels to save heating in winter and air conditioning expenses in summer. The benefits are very obvious.
6. Plastic products, this kind of plastic raw material, have good dyeing properties. In other words, it can be dyed quickly.
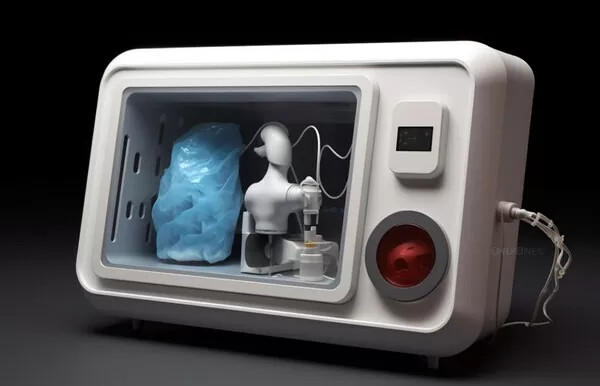
7. Another feature of plastic products, a kind of plastic material, is that it is very difficult to burn, so relatively speaking, if you use this material, it will give you a safer feeling.
8. The impact resistance of plastic materials such as plastic products can prevent chips and other sharp objects from injuring employees and protect personnel. And the appearance is beautiful and full of luster.
Engineering Economy
Thick Sheet Thermoforming Processing Offers Engineering Economics In packaging manufacturing, unless you are using cardboard as your packaging material, no other processing method can compete with thick sheet thermoforming technology. The main advantage of thick sheet thermoforming is its engineering economy. Products of composite sheet, foamed sheet and printed sheet are molded to replace the mold appropriately instead of changing the board to break the blister forming machine.
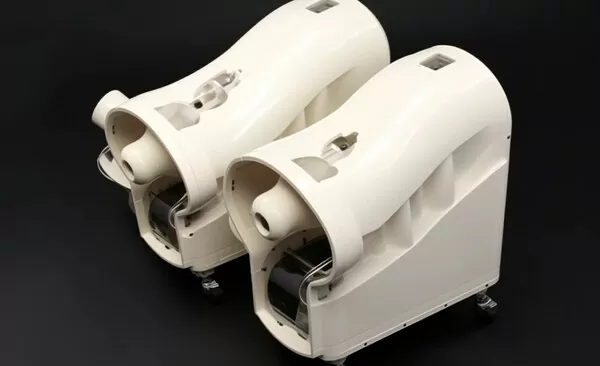
Thin gauge thermoforming products can be blister-coated with sheets of high melting point viscosity, while injection molding of the same wall thickness requires low-point viscosity pellets. For small quantities of plastic parts, favorable mold costs are another advantage of sheet-to-blister processing. For large quantities of parts, the product can achieve very good thin gauge plastic and the high yield ratio of the blister forming machine is very advantageous.
Variety of Material Choose
The smallest parts that can be produced by flat sheet processing are packaging materials for tablets or watch batteries. It can also produce very large products, such as garden pools with a length of 3 to 5 meters, and the thickness of the molding material can be from 0.05 to 15m01, and for foam materials, the thickness can reach 60mm. Any thermoplastic material or similar material can be foamed.
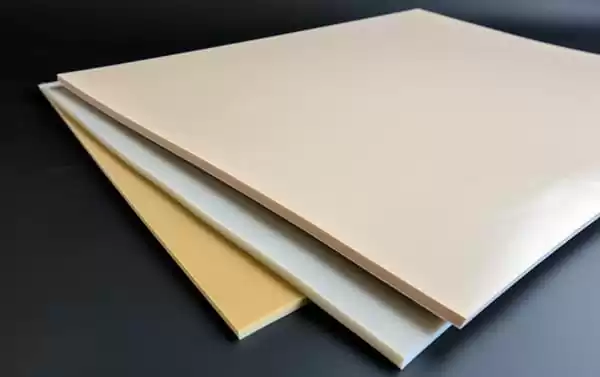
Can Create Complex Shapes
Thick sheet thermoforming allows the thermoplastic to be adsorbed on the mold surface in a heated and softened state, and maintain the desired shape after cooling and solidification. This enables thick sheet thermoforming to produce complex shapes and structures, including curves, angles, concavities and convexities, to meet the design needs of different products.
Free Design
Thick sheet thermoforming has good plasticity and can be freely designed according to product requirements. By adjusting the mold shape and parameters, the size, thickness and appearance of the product can be precisely controlled. This enables thick sheet thermoforming to achieve personalized and customized product designs to meet the needs of different customers.
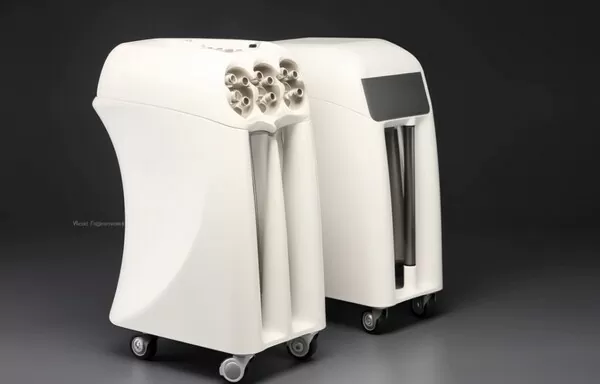
Case
Why choose PC thermoforming for the charging pile casing?
With the improvement of environmental awareness, electric vehicles and charging piles have gradually entered the lives of the public. Fashionable and elegant appearance design has become the only way for hundreds of charging equipment manufacturers to differentiate themselves. Plastic has good It has the advantages of design freedom, light weight, stable dimensions, low-cost advantage of mass production, environmental friendliness, and can fully meet the material performance requirements of the charging pile casing. It is the best choice for the product design of all charging pile manufacturers. Seeing that major charging pile manufacturers are using vacuum forming to make charging piles, they must have their own unique features. Why?
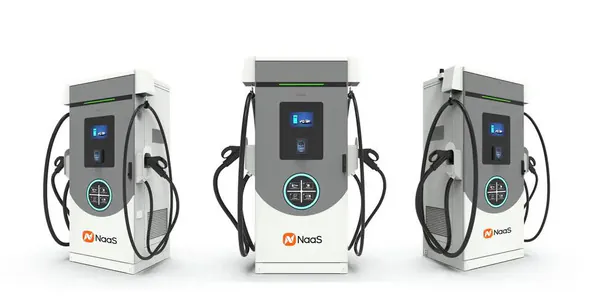
Exterior
Traditional metal-cased charging piles have good practicability, but they are always inseparable from the boxy stereotype in appearance. The regular design has long been unable to meet the needs of mass consumers for personalization, customization and differentiation. Compared with traditional metal casings, thermoforming can achieve special-shaped curved casings, light transmission, thousands of colors, high gloss or matte surface effects. Plastics provide industrial designers with a degree of freedom that metal materials cannot match. This is why Tesla and BMW choose plastic casings to ensure that charging piles remain fashionable and consistent with their streamlined models.
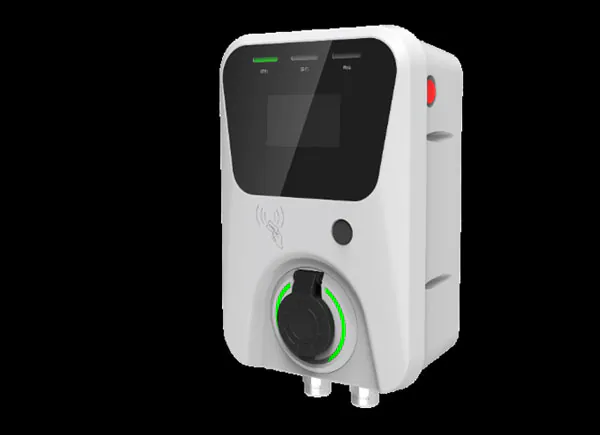
Dimensional Stability
Metal casing processing involves sheet metal, cutting, bending, welding and assembly. Most of the machine operations are done manually. Product quality has a great relationship with the operator’s experience. Poor assembly due to dimensional errors and structural problems caused by welding defects are endless. . Therefore, how to complete the layout of electrical equipment in an extremely small space places extremely high requirements on the accuracy of the chassis size. Compared with metal, the size of plastic casings is controlled by vacuum forming molds and can be predicted by the shrinkage rate of the material. Taking PC as an example, under normal production conditions, the material shrinkage is only 4 to 6 thousandths. All in all, PC enables the chassis to maintain product consistency and effectively reduce the incidence of scrapped products and production costs.
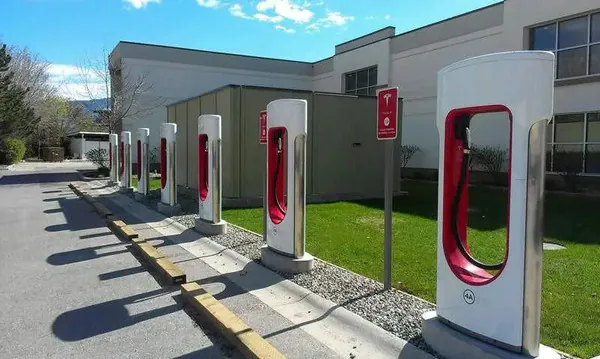
Safety: Insulation/Rustproof
Generally, metal casings must be well insulated, otherwise there may be potential risks of leakage due to corrosion due to long-term use. Plastic is an insulating material and will not rust, so the potential safety risks when used on thermoformed casings are much lower. in metal.
Lightweight
The trend of continuous lightweighting in the automobile industry will inevitably lead to the development of charging equipment. The density of plastic is much smaller than that of metal. With the same design, the weight of PC is only one-seventh of steel and one-half of aluminum, but it can still achieve the same mechanical properties as metal, and its external impact resistance is the same as that of acrylic (PMMA). 20 times, 2 times that of polystyrene (PS), lightweight and unbreakable.
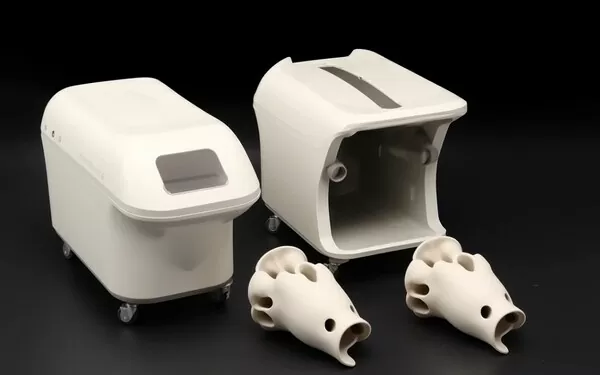
Cost
The charging pile casing accounts for only about one-fifth of the overall cost, but it has the important function of protecting the internal plastic components from failure during long-term outdoor use. Therefore, how to choose cost-effective materials is an important issue. The cost of a casing can be divided into three parts: raw material cost, processing cost, and pressure forming mold cost. Cost of casing raw materials In the past, due to the lack of reference standards for material selection, many charging piles chose over-designed materials. While meeting the performance requirements, the problem was that the cost remained high.
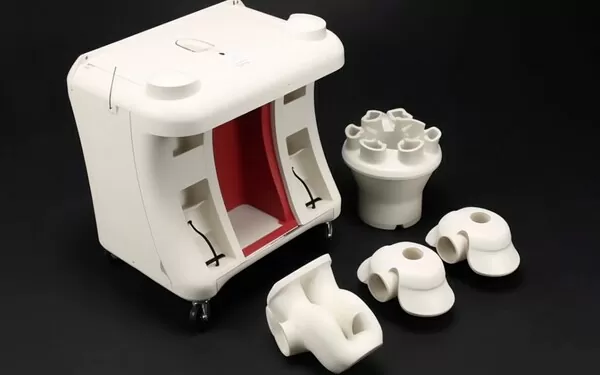
In fact, material costs can be well controlled through correct material selection. At this time, maintaining good communication with material suppliers is key. The main reason for high processing costs is mostly poor design of molds or processing parameters, resulting in long development cycles and high defective rates. These problems can be eliminated through computer simulation and analysis in the early stages of development. Therefore, we suggest that charging pile companies should choose experienced suppliers with certain computer simulation capabilities to reduce cost waste caused by detours. Then there is the mold cost. Thermoforming molds generally range from several thousand to tens of thousands. In other words, when a certain economic scale is reached, production costs can be effectively reduced. As shown in the figure below, the production quantity reached more than 2000pc that year, and the cost of a single piece has a clear cost advantage compared to metal.
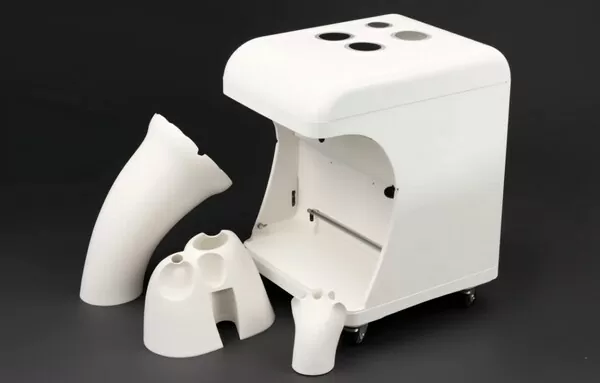
Environmentally Friendly
The energy consumed in the production and thermoforming process of plastics is much less than that of metals, and it contributes more to saving energy and reducing carbon dioxide emissions than metals. The use of spray-free plastic casings can also eliminate volatile organic compounds (VOC) emissions from metal coatings.
Conclusion
The versatile manufacturing process of heavy gauge thermoforming enriches the world of custom product design. Its adaptability, efficiency and creative potential place it at the forefront of modern manufacturing technology. Through continuous innovation, thick gauge thermoforming creates custom products one at a time, a testament to the human endeavor to shape the world around us.