When it comes to manufacturing and packaging, thermoforming really stands out for being versatile, inexpensive and innovative. Picture that clear plastic bubble that lets you see a product in a store or the plastic cup you drink hot coffee from without scalding your hands – thank thermoforming. And what about those cool packages made specifically for each electronic device they hold? You guessed it: thermoformed.
For those intrigued by plastics used in their daily lives, this piece may prove enlightening: thermoforming — which turns a flat plastic sheet into a 3-D object via heat and trimming — is widely employed across fields as varied as vehicle manufacture and medicine or food packaging. This exploration of the technique’s many forms and uses could open fresh vistas for designers, craftspeople and others keen to probe further into materials shaping our world.
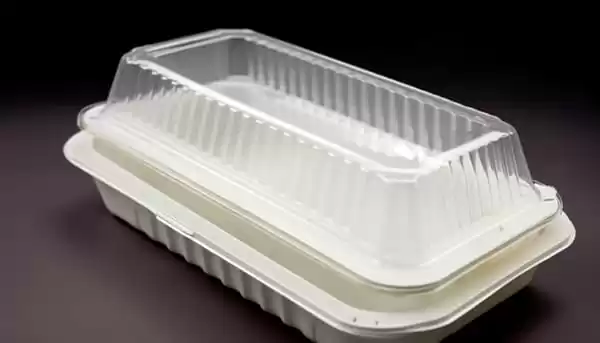
What is Thermoforming?
To truly grasp thermoforming’s various applications and types, you first need to appreciate its fundamentals. The process involves transforming a 2D sheet of plastic – heating it until soft (pliable) – then using a mould to shape it into something 3D. Since this method comes in different forms depending on how you plan to use it or what kind of result you’re hoping for, there are many shapes and sizes possible with thermoforming; one reason why experts love working with this flexible technique is because prototypes can be made quickly while tools cost less money than alternatives plus production lines move fast too.
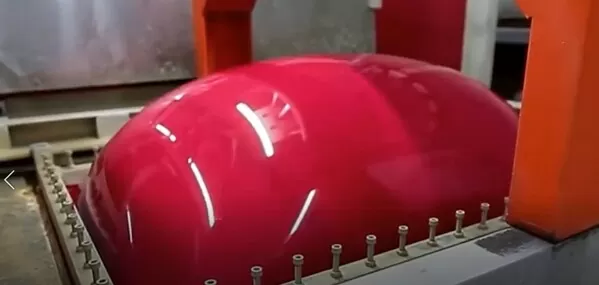
The Basic Process
For every type of thermoforming, the basic steps remain the same:
Heating: A flat sheet of thermoplastic material, which is made flat from the extrusion process or buying it from suppliers, is heated until it reaches a pliable forming temperature where it can be elongated and formed.
Forming: The heated sheet is stretched over or into a mold to take on the desired shape.
Cooling: After the sheet has been shaped, it is cooled in the mold to retain the form.
Trimming: The excess plastic material is trimmed from the formed product to produce the final shape.
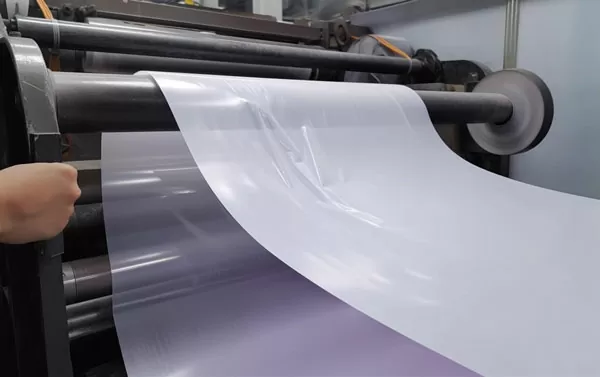
Types of Thermoforming
There are several thermoforming methods used in actual production: vacuum forming, pressure forming, twin sheet forming, thin gauge thermoforming, heavy gauge thermoforming, female mold and male mold thermoforming, differential pressure molding, cover molding, plunger-assisted molding, suction back molding, opposite mold molding.
Vacuum Forming
One of the most fundamental ways to shape plastic is vacuum forming. A 2D piece of thermoplastic is heated so that it can be bent, then pulled around a mould by emptying the air from behind it.This technique works well for making large, flat objects with straightforward contours – things like trays or covers. Because you can create lots of them quickly – and at a price more businesses can afford than some other methods – industries needing to box up products often use vacuum-formed parts.
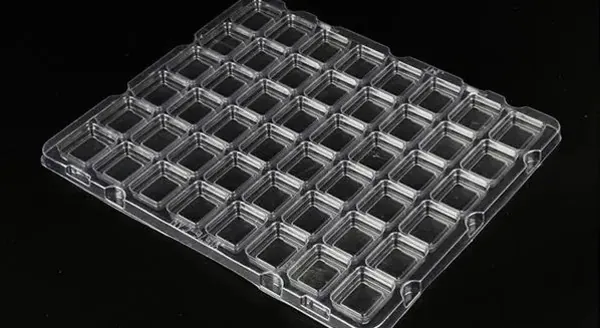
Pressure Forming
Pressure forming – also called blow or pressure vacuum forming, pressure forming is an upgrade to thermoforming. Think of it like vacuum forming, but using air on one side of the material in combination with suction from the other side; that way, you get intricate shapes with less variation in how thick each part is, and no loss of strength.Some things made this way are light covers for cars or enclosures for equipment – anything that needs to be both very tough and shaped just right. Pressure-formed products often have finer details than if they’d been done by vacuum alone; they can also end up being stronger overall because there’s more control over how all parts come out.
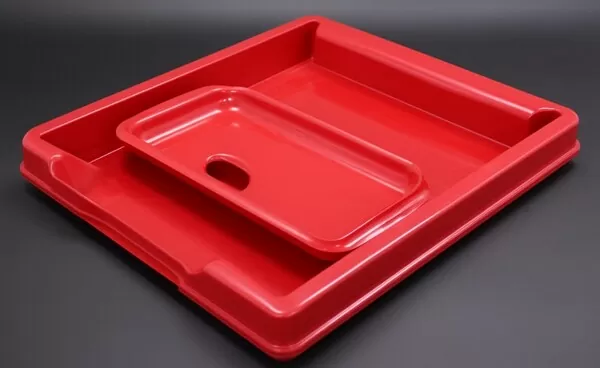
Twin Sheet Forming
When it comes to twin sheet forming, you’ll be working on two sheets of plastic at the same time. Heat them so they get soft and squishy. Then push those hot sheets into a mold. When everything cools down again, you’re left with a solid object that’s really strong because its insides are made up of two walls instead just one!
This process lets people make things like boxes for medicine or car parts – big stuff with space inside it. What’s special about twin sheet forming is how good the results turn out compared to other ways you might try making something similar. Objects end up tougher than if they were made from a single sheet too. They also have better insulation properties because there’s more air between layers when finished!
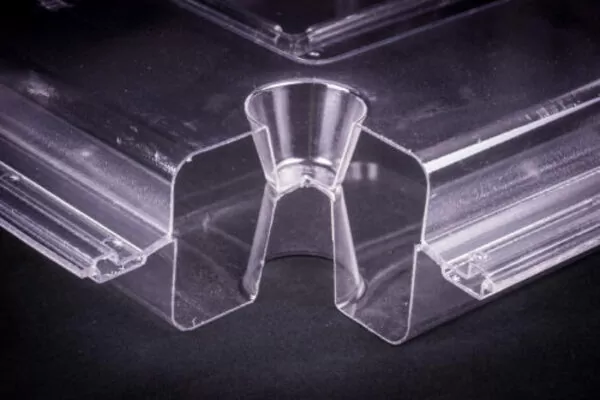
Thin Gauge Thermoforming
The process of thin gauge thermoforming includes warming plastic sheets until they are flexible, and then molding them across a template. The term “thin” applies to the thickness of these sheets: usually 0. 001 to 0. 060 inches. Businesses commonly use this technique for producing uniform items in large quantities – like packaging (blisters, clamshells), plastic bags, plates, trays or cups you might find at parties – because it is efficient.
Key characteristics of Thin Gauge Thermoforming include:
1. High Speed & Volume: Designed for rapid production cycles, making it ideal for creating vast quantities of products.
2. Material Efficiency: Often uses roll-fed systems that minimize waste.
3. Cost-Effectiveness: Due to its efficiency and the use of thin materials, the process can be more cost-effective, lower tooling costs, especially for large runs.
4. Precision: Capable of producing parts with fine details and tight tolerances.
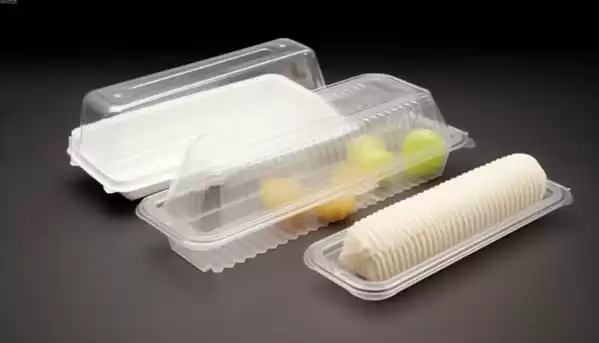
Heavy Gauge Thermoforming
Utilize heavy gauge thermoforming, geared towards working with plastic sheets that are thicker than usual – typically ranging from 0. 060 inches right up to almost half an inch. This technique helps produce more robust items such as vehicle dashboards, machine enclosures, equipment covers and kiosk casings: parts that have a definite structural function or need to withstand knocks better. Because the sheets are chunkier, each cycle takes longer overall; there is also often increased manual intervention compared with other methods too.
Key characteristics of Heavy Gauge Thermoforming include:
Durability: Products are more robust and can withstand harsher environments or mechanical stresses.
Versatility in Size: Can produce larger and more complex shapes, which thin gauge thermoforming might not handle well.
Lower Production Rates: The processing time per piece is longer due to thicker material and often more intricate moulding requirements.
Secondary Operations: Products might require additional processes like trimming, drilling, or assembly, which can add to the production time and cost.
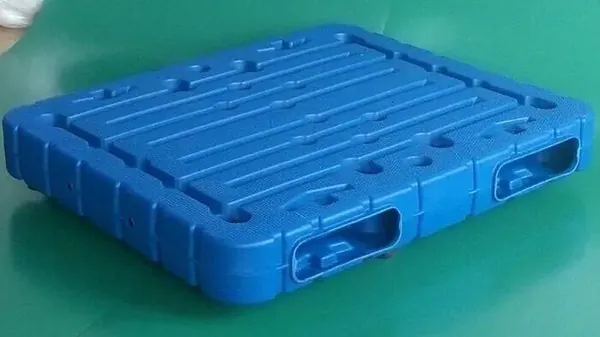
Female Mold Thermoforming
The female mold thermoforming technique involves pulling a plastic sheet over or into a hollow mold shape. Sometimes air pressure or vacuum forces the sheet to fit the mold’s inner curves better. Once cooled, the material will always have that same surface inside it. This process is great at making parts with lots of details – especially ones that go inwards instead of sticking outwards as overall shapes do! When this type of forming happens there isn’t much stretching going on outside so thickness remains uniform throughout everything – even if it’s deep! Female molds are also more conducive to achieving detailed textures or intricate designs on the surface of the molded part.

Male Mold Thermoforming
On the other hand, male mold vacuum forming manufacturing process uses a convex mold to shape heated plastic. Air pressure or mechanical force are then applied to form the sheet around the mold. After cooling and conforming to the external shape of the mold, the formed plastic is taken off. This approach usually suits items with less depth and complexity.With male molds, plastic gets stretched over them so material thickness might vary; however, this method often lets you make parts faster and affordably versus female versions – popular in shaping bigger shallow things too!
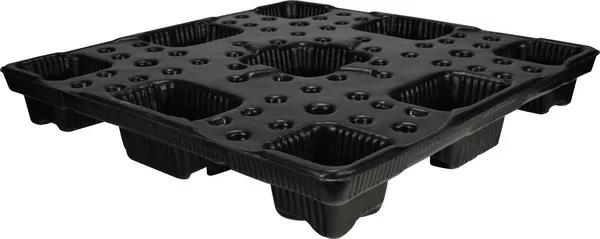
Differential Pressure Thermoforming
The way this is done is by heating a sheet of plastic and then applying different air pressures to it. By using higher pressure on one side while sucking air out on the other, you can make the plastic take up shapes with lots of details or very clear lines – even if they’re difficult to shape. This gives you lots of control over how thick something’s walls are too; which makes it perfect if what you want to make has lots of bits sticking out all over (like car instrument panels) or needs some parts that are quite big but still need others right next door looking really slim and delicate.
Cover Thermoforming
Thermoforming, a widely-used technique in the packaging sector, involves heating a plastic sheet until it becomes easily shaped. Next, the material is placed over a mould and subjected to vacuum pressure: this sucks the sheet into shape against the mould. Once cooled and set hard again, the newly formed plastic is trimmed and finished as required.The process works especially well if you want products with even wall thicknesses all over – for example disposable cups or trays.
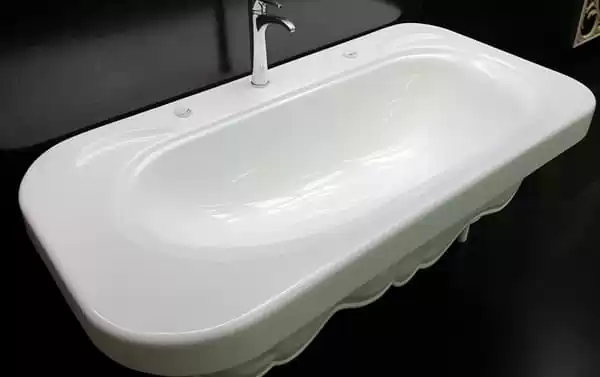
Plunger-Assisted Thermoforming
Utilizing both vacuum pressure and mechanical force, this technique forms a plastic sheet. Here’s how it works: The mold is located below a heated sheet of plastic, which then gets pushed into the mold cavity via a plunger; at the same time, suction from a vacuum draws the material against both sides of the mold so that it takes on its exact shape. Deep-drawn items having intricate features — fridge liners are one example — often call for plunger-assisted thermoforming because it lets manufacturers make them with high precision.
Suction Back Thermoforming
A specialized version of the vacuum forming process, suction back forming involves fine-tuning how material is dispersed and its thickness across a given part. After vacuuming first shapes the sheet to fit a mold, air pressure behind that same tool is dynamically adjusted so that it gently pushes the material backward; in doing so, this approach can address areas in which thinning may have taken place during deep draws — resulting in more uniform wall thicknesses throughout. One might choose to utilize suction back forming when making products necessitating substantial structural integrity (e. g. casings for medical devices).
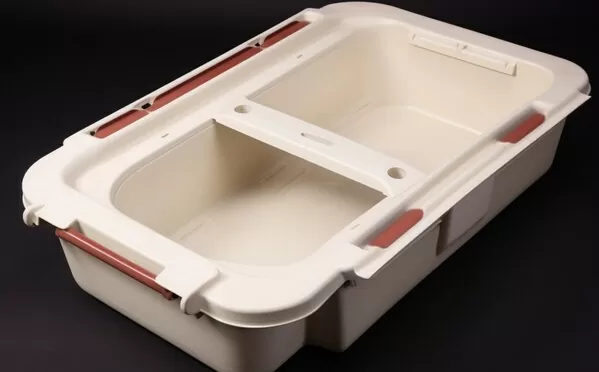
Opposite Mold Thermoforming
Known also as twin-sheet thermoforming, this technique employs two plastic sheets that are heated and formed at the same time over two different molds. These molds eventually meet up, with the edges of—or sometimes certain points on—the sheets becoming fused together and resulting in a hollow object. It’s a great way to produce lightweight structures with strong internal cavities; applications include double-sided panels, air ducts and fuel tanks for vehicles.There are specific advantages associated with each of these thermoforming methods — which you choose will depend on what you need your final product to do best (whether it’s looking fantastic, lasting for ages or being absolutely precise).
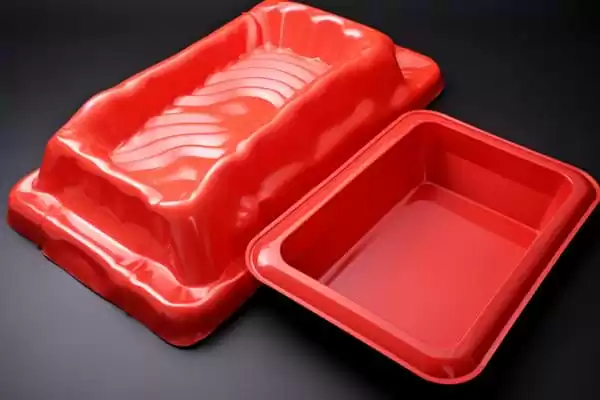
Applications of Thermoforming
Thermoforming is a versatile process that can be used in many industries and for many things. It makes it easier than injection molding or extrusion molding(extruded plastic sheet) to create tough, cheap plastic products that meet specific needs – from personalized packaging to large industrial components.
Consumer Packaging
Thermoforming is most commonly seen being applied to consumer packaging. Pretty much all of our food containers, the clamshell boxes that hold electronics, cosmetic packaging and even the trays tools come in are made using this technique. One reason for its popularity: thermoforming can create custom shapes that would be hard or impossible using other methods. It also allows use of clear, foamed or rigid plastic, or colored plastic materials – perfect if you want your product to stand out on a shelf!
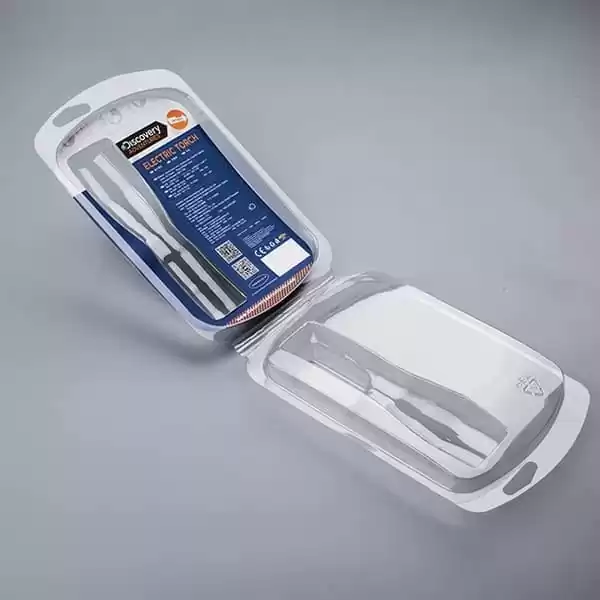
Medical Devices
In the medical device production field, thermoforming has a big role. Being able to create sterile packaging that items used just one time go in is important for healthcare. It keeps things clean and safe from getting spoiled or dirty. Lots of different kinds of medical stuff — like syringes, pill dispensers, machines that check your blood — can all be protected perfectly by special packaging made through thermoforming.
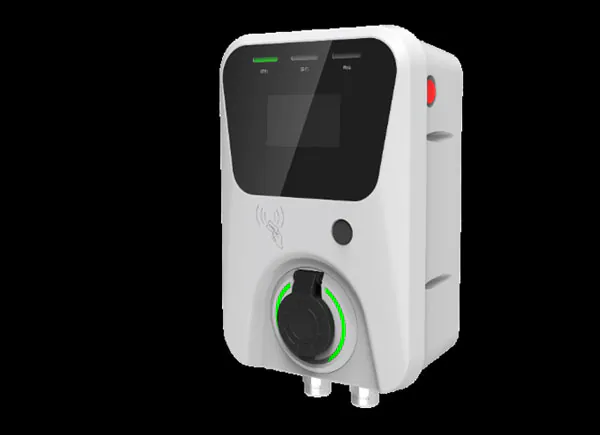
Automotive Industry
Thermoforming plays a key role in automobile manufacturing, producing everything from car interiors and dashboards to bodywork like bumpers and indicator light covers. Because it can handle tricky shapes, work with extra-strong substances and make both inside parts and outside ones, vacuum forming is crucial for all makers of cars and motorbikes.
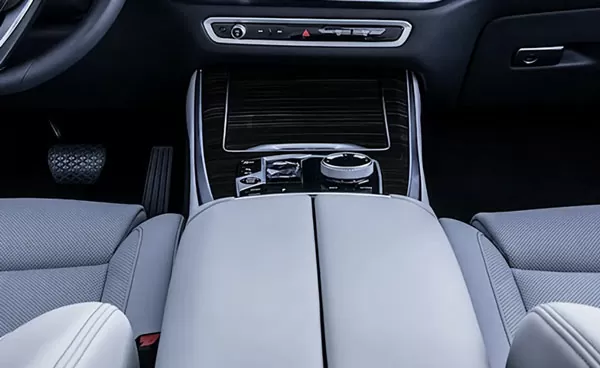
Custom Industrial Components
Thermoforming is not just for consumers – industrial applications can benefit too. Making big, tricky things like machine housings or transport equipment components – even furniture – works brilliantly with thermoforming. They need to be strong but also need careful attention to detail and weight too. Only thermoforming delivers it all.
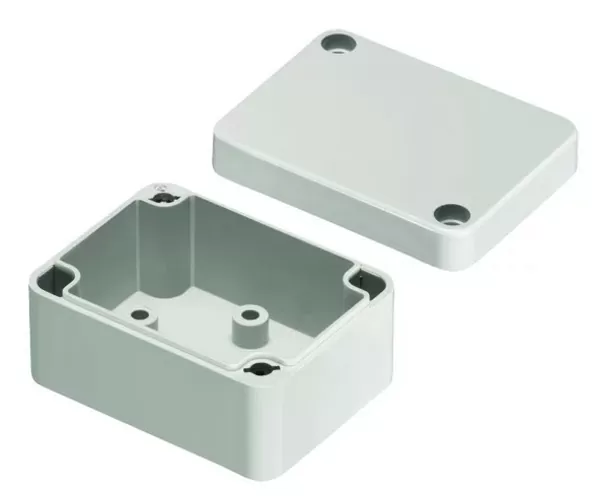
The Future of Thermoforming
The world of thermoforming is always changing. It moves forward via improvements in materials and technologies. Think additive manufacture. Take 3D printing – it’s being used with thermoforming to develop prototypes more quickly and make moulds faster. There are also new plastics around now that give a green boost to thermoforming.
Sustainable Thermoforming
In all sectors, the importance of sustainability is growing. Because thermoforming uses recyclable materials, creates less waste by using only what it needs and makes products that are easier to recycle or composed of biodegradable substances, it’s a method well-suited to change with the times.
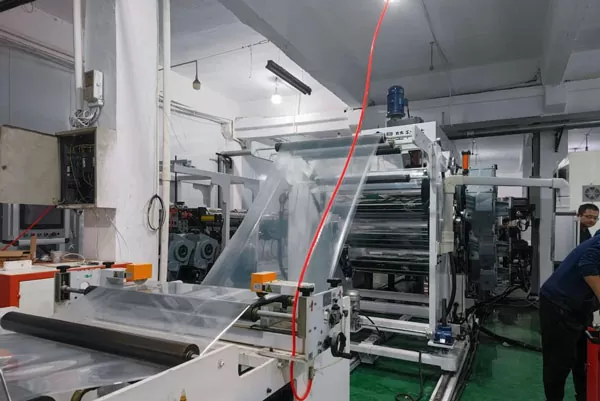
Advanced Thermoforming Equipment
Thermoforming machine technology is advancing rapidly, giving manufacturers the ability to exert more influence over their production processes. The result: increased productivity, better-quality goods and less energy consumed. Machines are becoming easier to operate too, thanks partly to automation and robotics – a development that could make thermoforming lines even cheaper and more efficient in future.
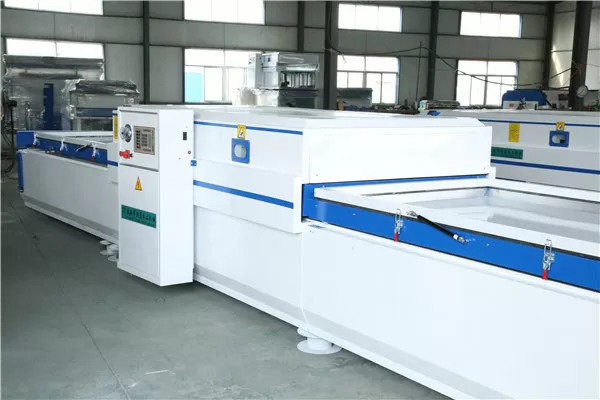
Conclusion
Thermoforming is not just another ordinary manufacturing method. Instead, it serves as an important foundation for a range of industries across the globe. This technique’s ability to manufacture customized plastic items that are tough, inexpensive and perfect for many uses highlights its significance in everyday life, design and global economies. As thermoplastic materials keep improving alongside technology itself, so too will this process continue shaping – quite literally – our entire world while making sure it remains innovative as well as sustainable going forward.