Thermoformed trays are also called plastic inner trays. Thermoformed trays are plastics that use thermoforming manufacturing process to make hard plastic sheets into specific grooves. The products are placed in the grooves to protect and beautify the products.
Thermoformed trays also have material handling trays. Thermoformed trays are mostly used for convenience.
Compared with other types of packaging on the market, thermoformed plastic trays are hygienic, environmentally friendly, low-cost, and easy to clean.
They are widely used in electronics, pharmaceuticals, food and other industries to play the role of anti-static, foil, shockproof, separation and fixation.
The types of thermoforming trays mainly include plastic drip trays, plastic shipping trays, disposable shipping trays, foam trays, automation trays recycling thermoformed trays, vacuum forming trays, etc. This article will take you to learn more about thermoforming plastic trays.
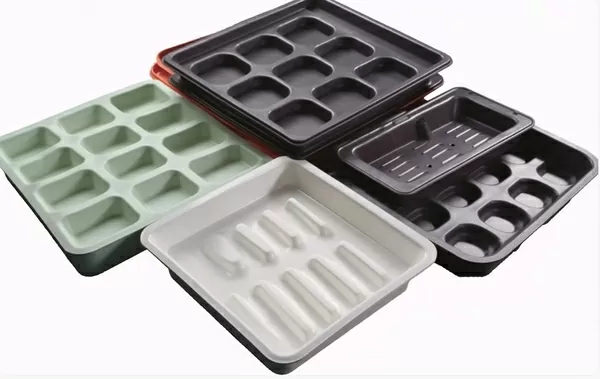
Thermoforming Trays Materials
The raw materials of thermoformed products are only plastic sheet, and the thickness of the film generally does not exceed 1.5mm. Commonly used sheets include: PVC, PET, PP, PS and based on this, flocking sheets, gold-plated sheets and anti-static sheets.
Environmental advantages of thermoformed trays
Reusable
Most thermoformed trays are made of environmentally friendly plastic materials, which greatly reduces environmental pollution and resource consumption, and meets the environmental protection requirements of modern society.
Reusable trays are used frequently in corporate logistics, so recycling within the company is a common method.
Enterprises can reuse used recyclable vacuum forming trays after cleaning, disinfecting and other procedures. In addition to recycling within the company, it is also a common method to send recyclable thermoformed trays to other factories for recycling.
Enterprises can classify and package used recyclable thermoformed trays and send them to other factories that have cooperative relationships with the enterprise for recycling.
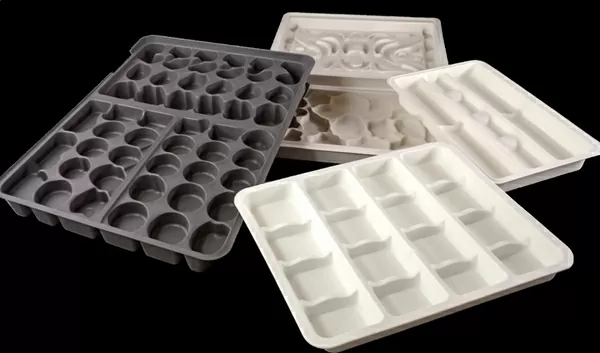
Environmentally Friendly
Recyclable thermoformed trays are made of degradable materials, which will not cause pollution to the environment and comply with the environmental protection requirements of modern society.
Save Costs
Recyclable thermoformed trays adopt a reusable design, which can reduce logistics costs and save enterprises’ operating costs.
High Reliability
Recyclable thermoformed trays have strong carrying capacity, light weight and good durability, which can meet the logistics needs of enterprises and bring greater value to enterprises.
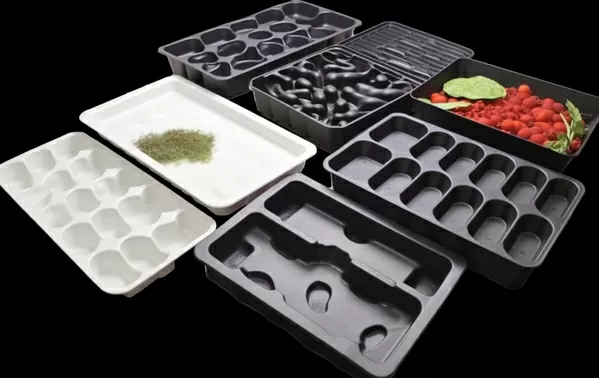
Twin Sheet Thermoformed Trays
The twin sheet thermoformed tray consists of a top cover and bottom bracket with a lock and a foldable enclosure to form a complete set of combined plastic trays. The top cover and bottom bracket are made of HDPE.
It is formed using a one-time twin sheet thermoforming process. The middle hoarding can be made of PP (polypropylene resin) plastic hollow board or seven-layer corrugated cardboard to make a foldable hoarding.
The entire series is designed to be recycled, and the top cover and bottom bracket can be recycled for up to ten years.
Plastic hoardings and corrugated paper hoardings can also be recycled multiple times and replaced.
This design can greatly reduce customers’ logistics operations and warehousing costs.
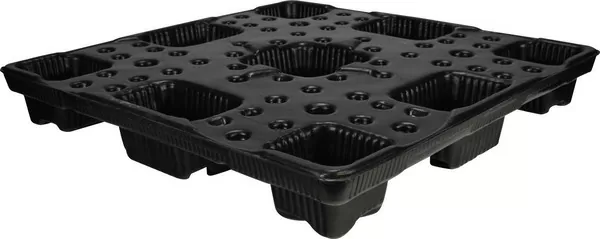
The middle panels of the tray are designed to be foldable, and the top cover and bottom bracket can be embedded or stacked, which can save 50% of storage space compared with traditional packaging.
The thermoformed top cover and bottom bracket are both thermoformed from two HDPE sheets at one time, which is strong and durable.
Is the assembly or disassembly of thermoformed trays extremely convenient?
One person can complete the disassembly or assembly in a few minutes without using any tools. The top cover and bottom bracket are each designed with four quick locks, which can lock the hoarding, so there is no need to bundle it, saving packing materials and labor costs.
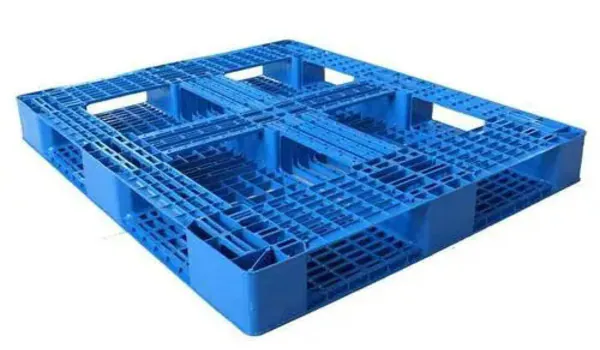
Constraints on the Development of Thermoformed Trays
The Usage Method is Backward
The advantages of thermoforming trays cannot be fully utilized. The thermoformed tray itself is a unitized logistics device born to cooperate with efficient logistics.
It can be said that the tray is the connection point throughout all aspects of the modern logistics system.
However, in our actual use, due to the inconsistent specifications, trays cannot be circulated and used in the logistics operation chain, and are only limited to within the enterprise.
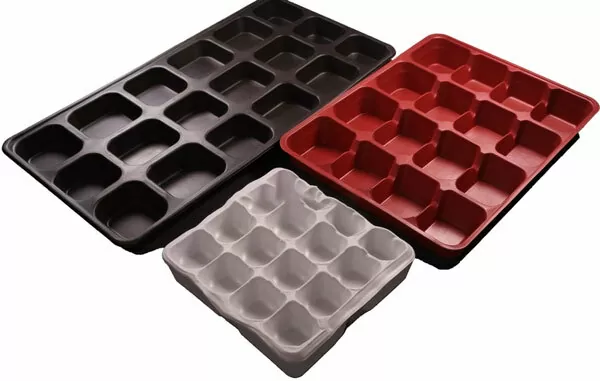
The Cost of the Circulation Process is Too High
From the survey, it can be found that the vast majority of companies’ PVC pressure forming trays are recycled within the company, so that the company’s products undergo manual handling and loading and unloading many times, which greatly reduces work efficiency and correspondingly increases the circulation cost of the products, thus Reducing the competitiveness of the product in the market.
Difficult to Conform to International Standards
Due to the inconsistent specifications and standards of PVC thermoformed trays, the use of trays in various countries cannot match international transportation equipment (such as international containers, etc.).
In order to adapt to relevant international transportation tools, companies have to order trays from tray manufacturers that are inconsistent with the company’s turnover specifications, thereby increasing the company’s export costs and reducing the international competitiveness of its products.
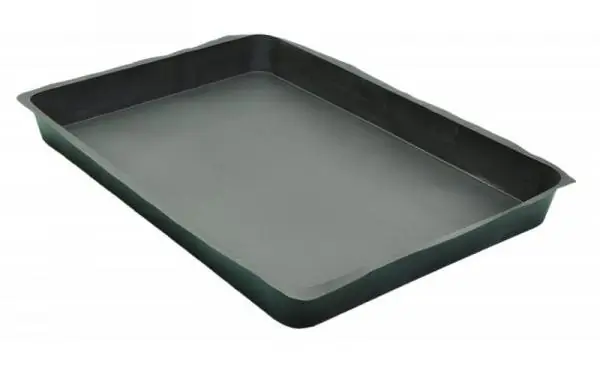
Application of Thermoformed Trays
There are many types of thermoformed trays. Trays are one of the types of thermoforming in the thermoforming industry. This type of tray has a strong bearing capacity.
According to the shape, structure and weight of the item, thermoforming tray is suitable for withstanding the force. There are also many thicknesses of materials used.
The choice depends on the packaging material needs of the packaged items. This type of thermoformed tray is commonly used in the electronics industry, toy industry, stationery industry, technology product industry, cosmetics industry, health care products industry, etc.
In terms of use, the commonly used materials for this type of trays include PVC and PS hard film. Generally, transparent thermoformed trays are more commonly used in thermoformed packaging. Other colors can be selected according to individual needs.
Thermoformed trays are widely used in food, medicine, electronics, chemicals, logistics and other industries. They have the advantages of light weight, beautiful appearance, moisture-proof, shock-proof, and anti-oxidation.
Compared with traditional wooden trays, thermoformed trays are more hygienic, durable, easy to clean and disinfect, and meet the environmental protection and hygiene requirements of modern enterprises.
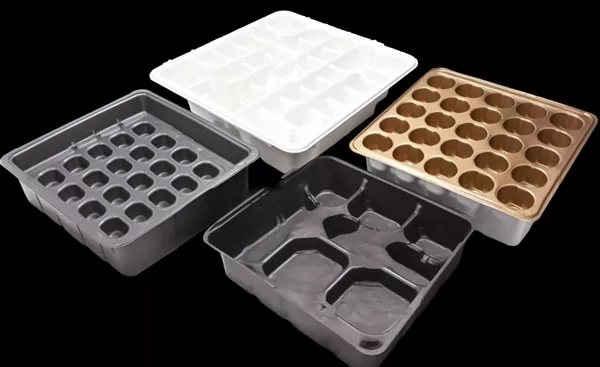
How to Choose High-Quality Thermoformed Trays
When choosing a high-quality thermoformed tray, you need to comprehensively consider the actual needs and choose the tray that suits you.
At the same time, it is also very important to choose a regular thermoformed tray manufacturer.
Thermoforming Trays Material
Thermoformed trays are typically made from polyethylene (PE) or polypropylene (PP), both of which are highly durable and recyclable. You can choose according to your specific needs when choosing.
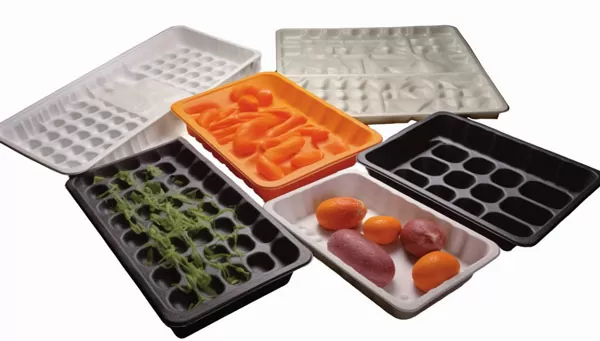
Tray Size and Shape
The size and shape of thermoformed trays should be determined based on the cargo required to be loaded.
The size of the tray should be slightly larger than the size of the goods so that the goods can be placed stably on the tray.
Tray Load-Bearing Capacity
The load-bearing capacity of a thermoforming tray is determined by its material and construction. When selecting a tray, you should consider whether its load-bearing capacity can meet the requirements of the goods.
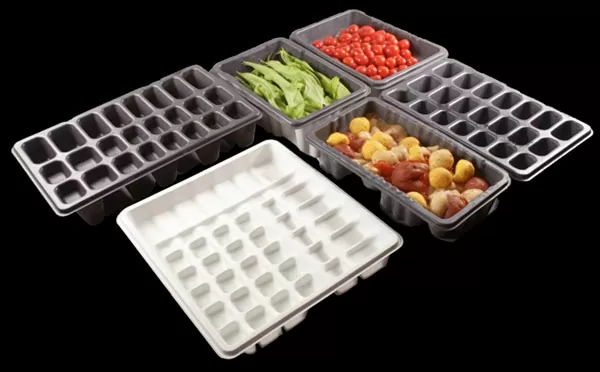
Tray Price
The price of thermoformed trays varies based on factors such as material, size, shape, and load-bearing capacity.
When choosing a tray, you should consider its cost performance and choose a tray that suits you.
Cases
Automobile Industry
Twin sheet thermoforming: dedicated thermoforming trays for the automotive industry
For Tier 1 automotive suppliers, in the process of transporting those large mechanical parts or bulk small parts from their factories to the OEM automotive assembly line, they usually need to use large customized trays in order to stack the goods in an orderly manner. Avoid collision damage.
For example, the custom-made tray below is very suitable for transporting those precision mechanical parts to the OEM’s automobile assembly line. The forminging process includes the following processes:
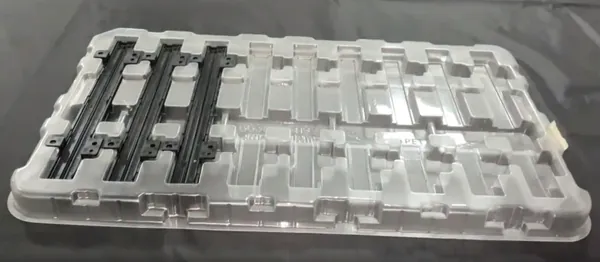
First, two sheets are placed at designated positions on the orifice plate of the thermoforming machine, and then the clamp automatically lowers and a moving intermediate frame brings in the other two sheets.
Two sets of halogen lamp heaters will quickly heat the four sheets according to the heating path set by the computer. Precise temperature control is achieved through a fine-hole grid of photocells.
During this process, it is necessary to ensure that the sheet is flat when heated.
Then, the mold is closed. Under the action of a clamping force of hundreds of thousands of Newtons, the two sheets are combined into a strong structural panel.
By introducing a certain pressure of air between the two layers of sheets, the sheets and the mold can fit more closely, and it can also have a certain cooling effect.
After the mold has cooled, immediately open the moving middle frame and remove the two formed trays.
Finally, the robot takes the formed product out of the mold, and then puts the next set of four preheated sheets into the mold to start the next production cycle. One product can be produced every 5 minutes.
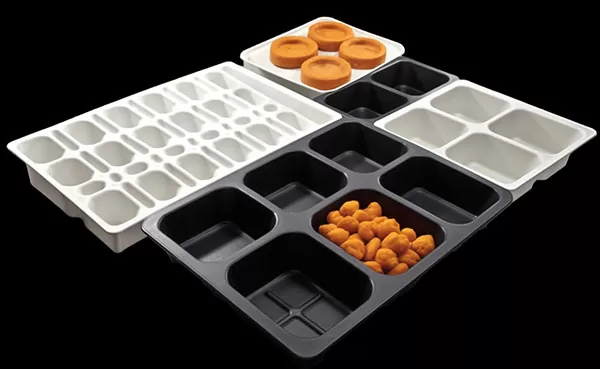
Chemical Industry
For the chemical industry, the issue of safe transportation of goods is very important. Thermoformed trays solve this problem with their natural advantages and improve the safety and stability of cargo transportation. The advantages of thermoformed trays include the following:
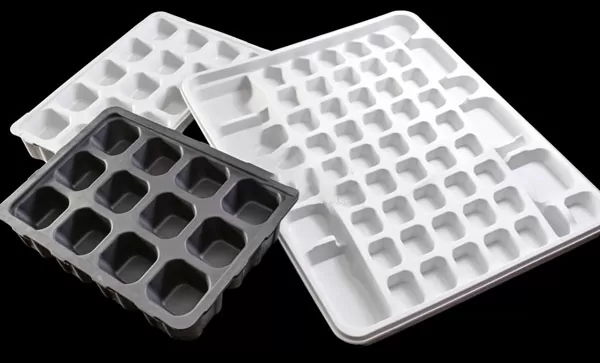
1. Durability
Thermoformed plastic trays are more sturdy and durable because they can not only bear a large weight but also avoid corrosion by chemical products, so they are widely used in the chemical industry.
2. Lightweight
The main materials of thermoformed trays are thermoplastics, so they are lighter. Whether in cargo transportation, stacking, or storage, labor intensity is greatly reduced. At the same time, it also brings great convenience to the logistics industry.

3. Environmentally friendly materials
Compared with traditional wood or paper materials, thermoformed trays are a more environmentally friendly material. Using thermoformed trays reduces logging and felling of trees and reduces the impact on the environment.
4. Recyclability
The thermoformed plastic tray is made of ultra-high molecular weight polyethylene and can be recycled. Used thermoforming trays can be recycled into new trays, reducing the waste of resources and better protecting the environment.
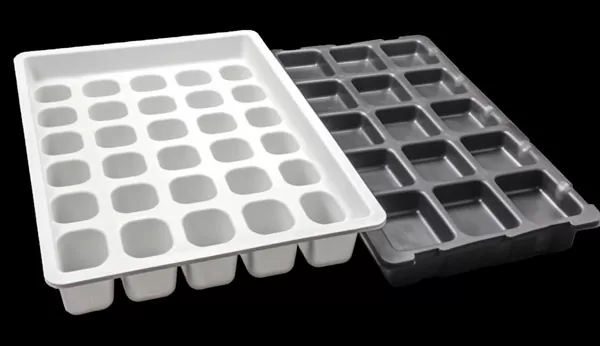
5. Hygiene
Product transportation in the chemical industry often requires attention to the hygienic environment. The surface of the thermoformed tray has almost no pores and gaps, so it will not accumulate bacteria and viruses, and is highly safe. It is also easy to keep clean and has a long service life.
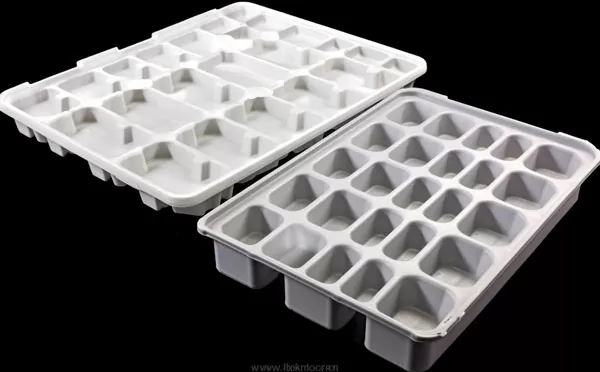
Conclusion
As an important logistics packaging tool, thermoformed trays play an important role in logistics, manufacturing and retail industries. Its lightweight, durable, easy to clean and environmentally friendly features make it an ideal alternative to traditional wooden and metal trays.
At the same time, with the development of science and technology and the increase in demand, the application prospects of thermoforming trays will be broader. We believe that in the future development, thermoformed trays will have more applications and innovations.