In the manufacturing industry, the visual characteristics of a product not only play a role in product display, but also have an additional dimension in displaying the quality and functionality of the product. Among them, the gloss and transparency of the product are the two most critical aspects.
Both features can add value when items such as high-end electronic displays, protective masks worn by medical personnel, or luxury packaging boxes appear smooth and reflective but also allow people to easily see through them.
One way to completely change the look and feel of a product is to use thermoforming. This versatile manufacturing process is growing in popularity because it can make items look shiny and smooth – a quality that is both attractive and practical.
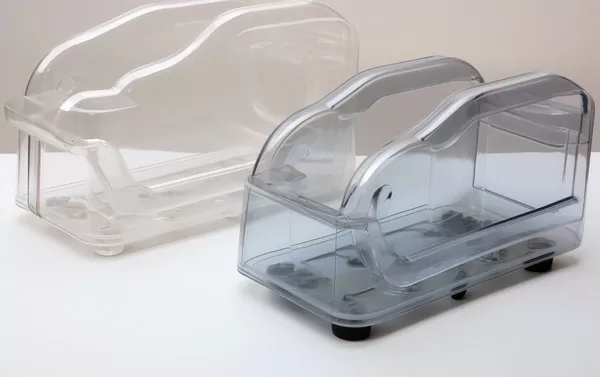
Thermoforming has many uses; a key example is creating clear features with a glossiness that customers also like for added credibility.
Whether you need an eye-catching design element or just make people believe “Yes! I can see through this packaging,” thermoforming can change the way we think about transparency—and give off more sparkly vibes along the way!
Manufacturing professionals often turn to vacuum forming when they need an efficient way to make many different things out of plastic. You can use this technique for everything from car parts to packaging.
One reason people like vacuum-formed products is because they look good: They can be see-through and shiny. But these aren’t just superficial qualities – how transparent or glossy something is affects how well it works, what customers think of it and even whether they buy again later.
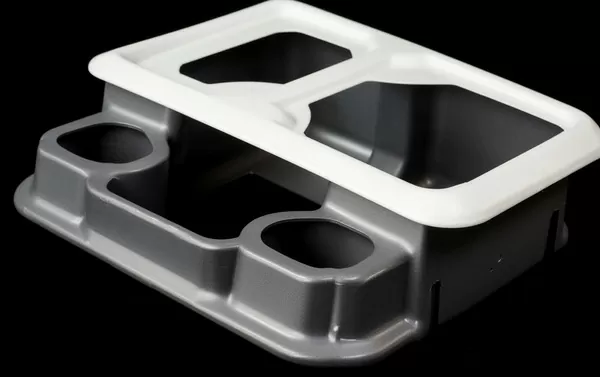
This post will explore some of the ways manufacturers can increase both transparency levels as well as overall glossiness for items made via vacuum forming; readers will gain insight into materials selection along with various processes that may be employed during production (plus finishing touches) so as elevate outcomes even further!
Are you interested in learning more about thermoforming?
If so, this article is for you! We will discuss various factors in thermoforming, from optimizing thermoforming techniques to produce products with better transparency and gloss to what factors affect its transparency/glossiness (and why it is sometimes difficult), and demonstrate with some examples For real-life use, manufacturers can benefit greatly from just using these methods.
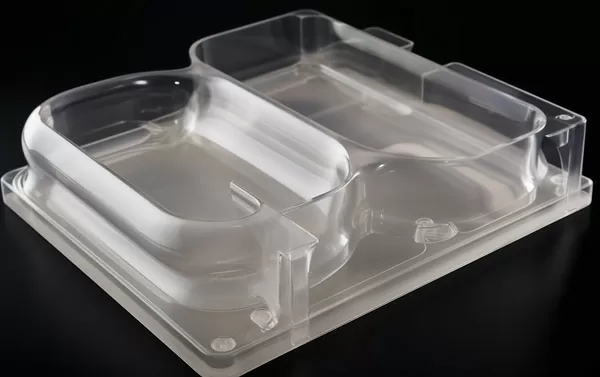
Thermoforming Process
The thermoforming process involves heating a plastic sheet to make it pliable enough and then forming it into a specific shape in a mold. Then trim as needed to final complex shapes. Thermoforming has applications in many areas, including the production of packaging and other plastic products.
Thermoformed products offer significant advantages, such as temperature resistance, good chemical resistance, sharp corners, and thick gauge, which make them ideal for applications requiring high transparency and gloss, unlike traditional methods like injection molding, which often involve material costs mold making and materials chemical resistant.
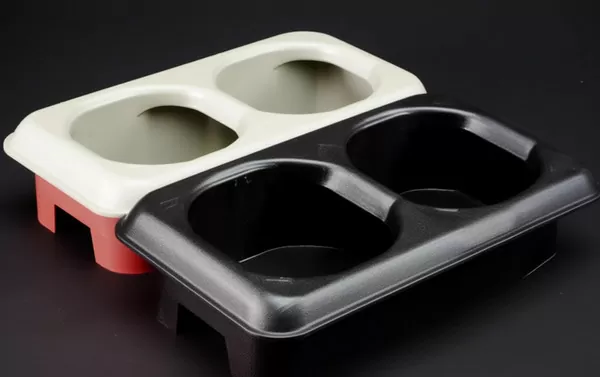
Two Main Types of Thermoforming
There are two main forms of thermoforming: vacuum forming and pressure forming. Vacuum forming involves heating a sheet of thermoplastic, stretching it over a mold, and then sucking out the air between the sheet and mold so they take on the shape of each other.
In contrast, pressure forming relies not only on suction but also on applying pressure to the other side of the sheet to form.
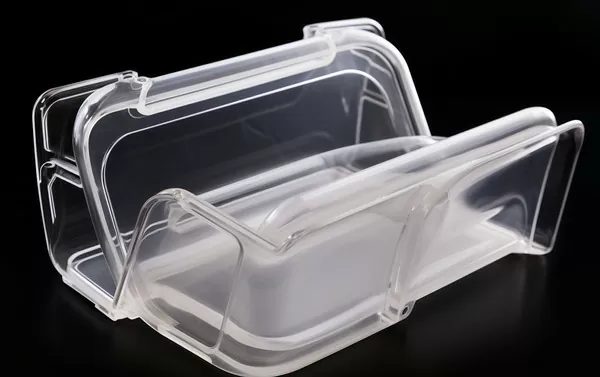
Materials Commonly Used in Thermoforming
Acrylics, PETG, and polycarbonates are three common thermoplastics that offer high-impact strength, optical clarity, light transmission – making them excellent choices when manufacturers want thermoformed items with a glossy finish or see-through quality.
The Importance of Transparency and Gloss
Transparency refers to a substance’s ability to let light pass through it, while glossiness refers to a substance’s surface’s ability to reflect images and light with great contrast.
In thermoformed products, these factors combine to make the finished product look beautiful—just like glass or polished metal!
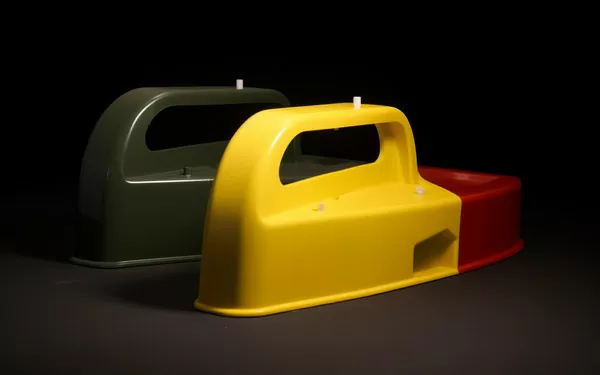
Industrial Applications
Transparency and gloss are important in many different fields for many reasons. For example, medical device components with better transparency and gloss can be cleaned more easily and have better visibility, both of which contribute to better care.
The same is true in car design, where incorporating clear or glossy materials into lampshades as well as some interior parts can help give the car a stylish overall look.
Good transparency is also beneficial when used on food packaging because shoppers want fresh merchandise!
At the same time, the gloss adds an attractive shine that makes the packaging stand out from competitors’ merchandise displayed in stores.
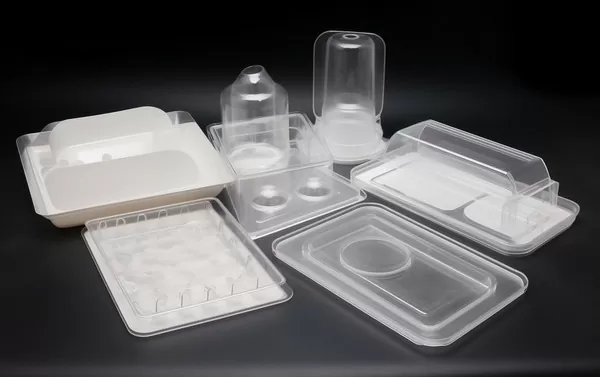
Consumer Perception
Products with high gloss and transparency are generally considered to be of better quality. These features can help an item stand out when many similar items are on sale, meaning shoppers are likely to buy it.
The Science Behind the Clarity
In situations where it is important for objects to be seen clearly, makers use specific polymers including PET (Polyethylene Terephthalate), PVC (Polyvinyl Chloride) and RPET (Recycled Polyethylene Terephthalate). These plastic materials are not only see-through but also strong.
Scientists have designed their molecules so that light can travel through them easily over long periods without causing damage – something that does happen when beams pass through old-style plastics.
Thermoforming has the potential to revolutionize the transparency of product packaging. Because thermoforming involves using air pressure and heat to shape plastic, packaging can be created using materials such as PVC or PET that are not only transparent but can also rival glass in clarity.
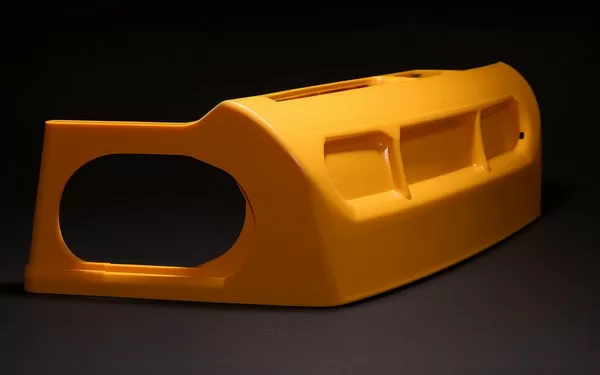
The seamless design and the choice to use anti-fog materials ensure that the interior products are not only light-transmissive but also do not cause visual obstruction even in environments that may be wet or have high humidity.
In addition, thermoformed packaging allows for a more efficient extraction method. This means the material used for packaging purposes does not become stretched during this process – nor does it develop any defects that may affect how clearly someone can see through it.
Indeed such intricacies extend even towards designing aspects; each curve or groove is thought about meticulously so as little distortion as possible occurs from them- giving people an unobstructed view into what lies within!
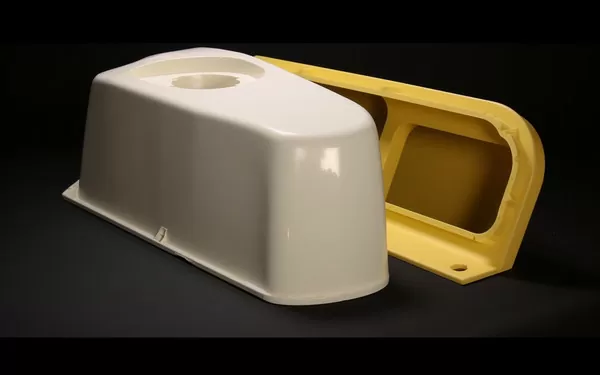
Optimizing Thermoforming for Better Transparency and Gloss
Material Selection
If you want the final product to have good transparency and gloss, you must first choose the materials used in the product. But not all materials have good transparency and gloss, so specific material selection is very important.
Common materials with transparency and gloss include acrylic, polycarbonate (PC), polyethylene terephthalate (PET), and glycol-modified polyethylene terephthalate (PETG).
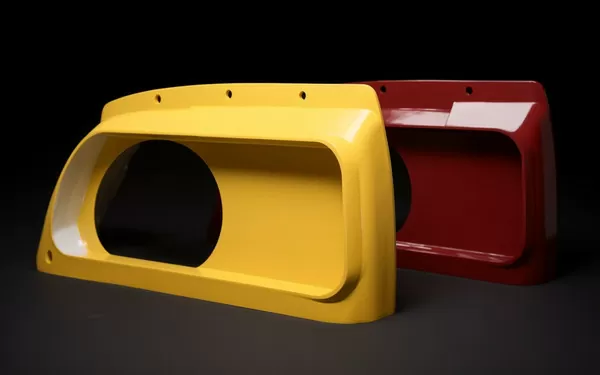
1. Acrylic (PMMA – Polymethyl Methacrylate)
Transparency: Acrylic is renowned for being incredibly transparent – sometimes even more so than glass! This means it lets light through without much bending (or distorting) of rays; an important quality when something has to be seen clearly.
Glossiness: If you want shiny objects then look no further than this material’s surface! The degree of glossiness can vary depending on the finishing process applied.
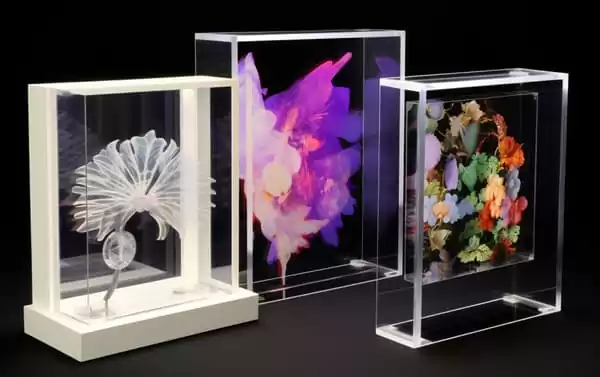
2. Polycarbonate (PC)
Transparency: Polycarbonate is transparent, but not as optically clear as acrylic. It does transmit light though, so can be used when both clarity and impact resistance are needed – like for spectacle lenses.
Glossiness: You can polish polycarbonate to a high shine, much like acrylic! However because its chemical makeup is slightly different, the surface may not achieve the same level of clarity and may be more prone to scratching.
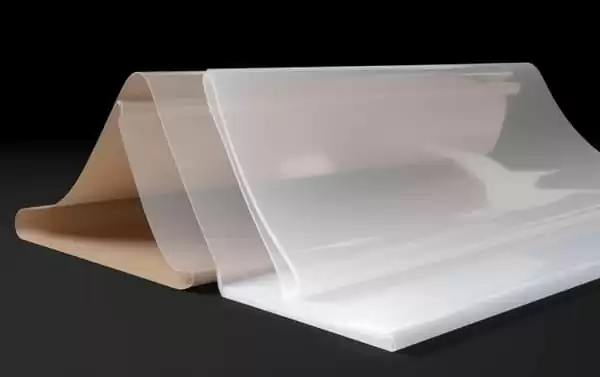
3. Polyethylene Terephthalate (PET)
Transparency: PET is see-through, although it might not be quite as clear like acrylic or polycarbonate. It’s good for things like water bottles and food packaging.
Glossiness: When made into surfaces, they can have a shine – but not as much as items made from acrylic or polycarbonate. If more gloss is needed then treatments can be added; these change the way that light behaves when it hits the surface (for example making reflections look sharper).
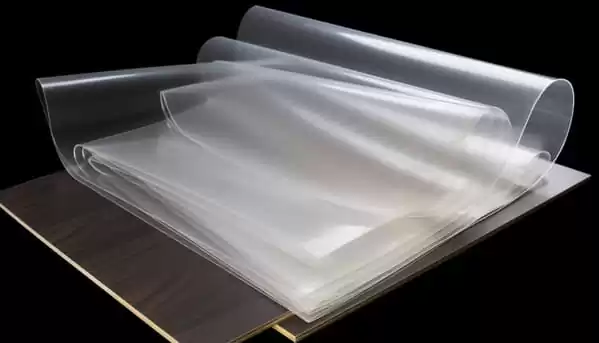
4. Glycol-Modified Polyethylene Terephthalate (PETG)
Transparency: PETG has transparency properties similar to PET, but in many cases it offers improved clarity and impact resistance over its close relative.
Glossiness: While PETG surfaces can indeed be glossy (again, much like those of PET), they may not quite reach the same level of gloss that acrylic or polycarbonate ones do. If increased glossiness is desired then surface treatments or coatings can always be applied post-extrusion.
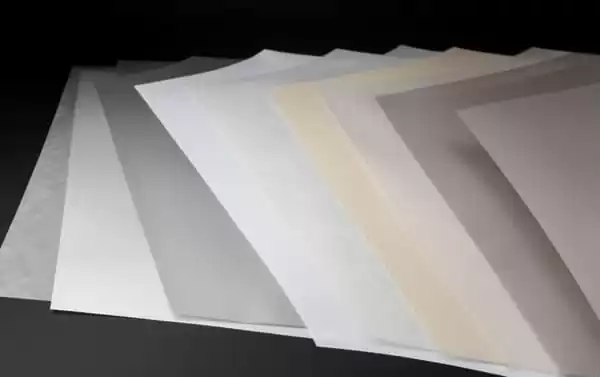
In summary, acrylic is usually the clearest and shiny of these plastics, although all allow light through well. PC and PETG are also good at this, though not quite as glass-like; PET may be slightly less transparent or glossy. If needed, surface treatments can improve things further – on any plastic -– for certain uses!
Tooling and Mold Design
The final appearance of the product depends largely on the design of the molds and tooling used in thermoforming. If you want the final product to have fewer defects and better gloss, choose the appropriate mold(mold surface) and draft angle.
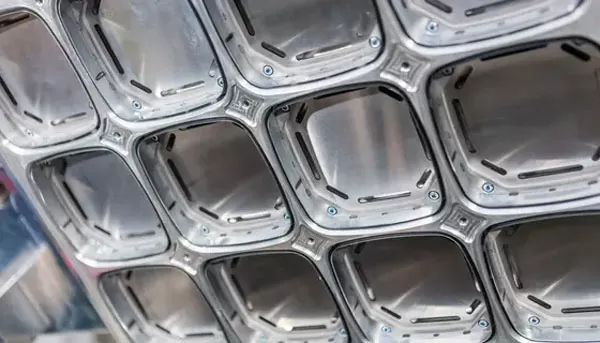
Temperature Control
Accurate temperature control is vital in order to achieve the best possible material flow and prevent defects that could affect transparency. Heating the plastic evenly helps to create a uniform surface – something that’s very important if both clarity and gloss are key requirements.
The Vacuuming Process
The use of a powerful vacuum is necessary to make sure the plastic sheet adheres closely to the mold and takes on all of its textures and details. This step is crucial if one wants designs with lots going on not look blurry thanks to air bubbles messing things up.
Processing Conditions
During the thermoforming process, clarity and gloss are affected by many variables: temperature, pressure, and heating/cooling rates. You want your finished product to be of high quality both aesthetically and functionally, which means these factors need to be closely controlled.
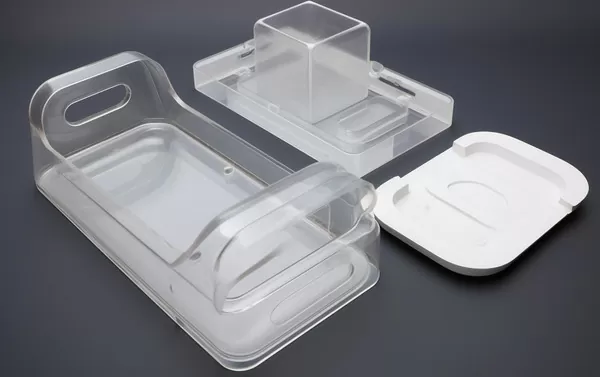
Post-Processing Techniques
To further enhance the gloss and clarity of thermoformed products, thermoforming manufacturers often rely on post-processing techniques including flame polishing, polishing or clear coat applications. These methods can help eliminate imperfections, further enhance visual appeal—or both!
Finishing Touches
Other techniques can be used after vacuum forming to improve the transparency and glossiness of products. Coating, polishing, and flame treating are some common methods for achieving this.
1. Polishing
Polishing – either manually by hand or using a machine – eliminates small imperfections while also enhancing shine levels; if you want your item looking top-notch with no compromises then polishing becomes especially crucial!

2. Coating
Coating has the ability not just to make things clearer but shinier too!! Additional advantages include increased lifespan due to protection against scratches plus those nasty UV rays from sunlight (which could otherwise yellow objects over time).
3. Flame Treating
Flame treating is a technique used to achieve a high-gloss finish on certain plastics. It involves passing a flame over the surface, melting the very top layer and allowing it to cool into a smoother, glossier finish.
The Science of Gloss Enhancement in Thermoformed Products
The goal of adding sparkle to packaging isn’t just to catch the shopper’s eye. This is also how the brand creates a high-end look, with packaging giving a luxurious impression that hints at the premium goods inside.
Thermoforming is able to achieve this in part thanks to materials with built-in gloss and strict quality control measures throughout the manufacturing process.
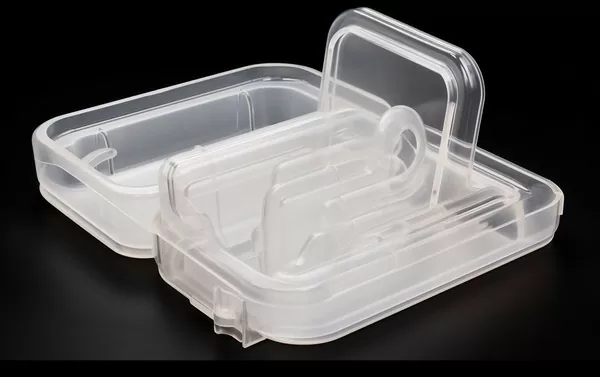
Thermoforming enhances the natural reflectivity of glossy materials such as certain types of PVC, PP and PET. By applying heat and shaping, you can eliminate creases and ensure an even shine throughout your packaging job.
It’s not just about making things look pretty – when shoppers are browsing in a store, their choice is often (almost entirely) based on whether a given item is good value for money; so something special needs to be happening here, too!
Thankfully, thermoformed packaging once again excels, as their smooth surface doesn’t just reflect surrounding light sources like a normal shiny object, on the contrary, these films appear to be more radiant overall, which is sure to help convince potential buyers.
Furthermore, the practical benefits of good surface gloss extend beyond its attractive appearance. For one thing, that sheen helps with maintenance—cleaning products are more likely to be purchased on smooth surfaces than on rough ones—which means whatever you encapsulate in thermoformed plastic will last longer Keep it shiny and new!
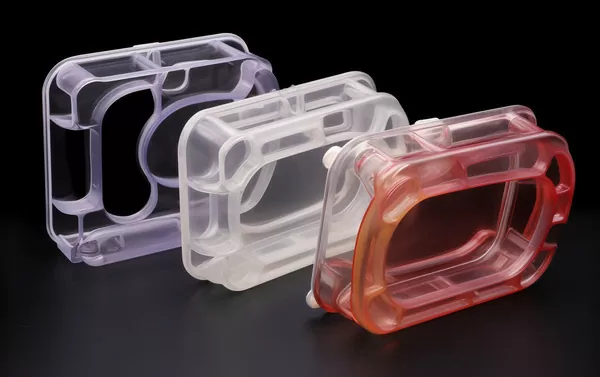
This is especially useful if the items need to be displayed for a long time (such as items in a cosmetics retail store); no one wants the items in their store to look less fresh to all visitors (especially potential buyers).
Case Studies
To illustrate the practical application of these principles, let’s explore a few case studies where enhanced transparency and gloss were critical to the project’s success. These examples demonstrate how material selection, processing techniques, and finishing touches come together to create superior vacuum formed products.
Case Study 1: High-End Retail Packaging
For luxury brands, packaging plays a crucial role in the customer experience. A high-end cosmetics company sought vacuum formed packaging that not only protected the product but also showcased it elegantly.
By selecting acrylic for its exceptional clarity and applying a high-gloss finish, the packaging achieved a luxurious look that aligned with the brand’s image.

Case Study 2: Automotive Headlight Covers
Automotive components require precision and durability, alongside aesthetic appeal. Polycarbonate was chosen for headlight covers due to its excellent transparency and impact resistance.
The vacuum forming process was meticulously controlled to ensure a defect-free surface, and a UV-resistant coating was applied to maintain clarity and gloss over time.
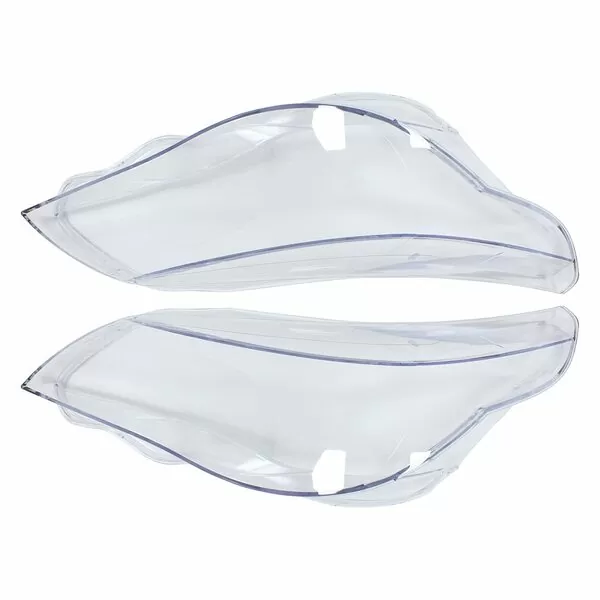
Conclusion
Careful design and material selection, controlled processing, and specialized post-processing techniques all contribute to the transparency and gloss of thermoformed products.
When manufacturers achieve high levels of transparency and gloss in these products, not only are technical requirements met, but they also allow the final product to stand out in the market with its aesthetic appeal and perceived value.
Improving the clarity and shine of vacuum formed items is a complex task that involves thinking carefully about materials, techniques and finishes.
By getting to grips with plastics’ properties as well as learning how to vacuum form expertly, manufacturers can make products that are both good-looking and practical – meeting exacting standards in terms of their quality too.
Having covered the basics of obtaining high-quality finishes in vacuum formed products, let us now turn our attention towards more sophisticated approaches, environmentally friendly production concerns as well as what tomorrow holds when it comes to this amazing technology!
Be sure not miss out on any upcoming posts where we will explore how you can further refine your own vacuum forming processes – all while achieving outstanding levels transparency with ease.