Thermoforming is an adaptable method of production that takes thin sheets of plastic and uses them to create a whole host of items from basic disposable cups to medical devices with complex designs. How much do designers, engineers and manufacturers need to know about what thermoforming can achieve – and what it can’t?
Thermoforming is a widely-used process for shaping plastics. An easily-formed plastic sheet is heated until it becomes soft, then moulded over a form and trimmed to make an object which has use. There are benefits of thermoforming such as being cheap when many things are made in one go and having lots of ways to shape something you have designed – but there are also limits to what it can do; knowing about these could help companies or people who design things choose more wisely.
In this wide-ranging blog post, in addition to exploring the advantages and disadvantages of thermoforming, we will focus on the current limitations of thermoforming while examining some of the latest technological advancements in the field.
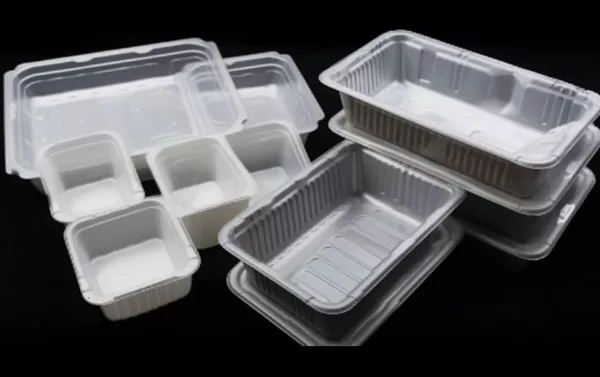
The Art and Science of Thermoforming
Thermoforming process is a technique that makes use of heat to soften thermoplastic plastic sheets in order to shape them. The heated sheet can then be placed on a surface such as a vacuum forming molds or put inside one under vacuum or pressure. Heating, shaping, and cooling are the three main stages involved here. Despite sounding straightforward at first glance, thermoforming demands an impressive combination of understanding materials, know-how when it comes operating machines and coming up with innovative designs.
There are several thermoforming methods used in actual production: differential pressure molding, cover molding, plunger-assisted molding, suction back molding, opposite mold molding, female mold and male mold thermoforming, thin gauge thermoforming, heavy gauge vacuum forming and twin sheet forming.
Material Matters: The Importance of the Right Plastic
The selection of plastic used is paramount – it needs to endure the process of heating and shaping without degradatio. Some types are more suited than others for this “thermoforming”; polystyrene (PS), polyethylene terephthalate (PET) and high impact polystyrene (HIPS) are three examples. Each one has strong points as well as drawbacks – these determine when each should be chosen in order get the best finished article possible.
Design for Success: The Role of Tooling and Mold Design
In thermoforming, tooling and mold design are extremely important(matched mold forming). A mold’s geometry decides what the finished product will look like and how complex it can be. Designs can be very intricate with thin-gauge thermoforming because this process allows for more detail in the final piece depending on how thick or thin sheets are when heated and shaped onto molds by air pressure systems.
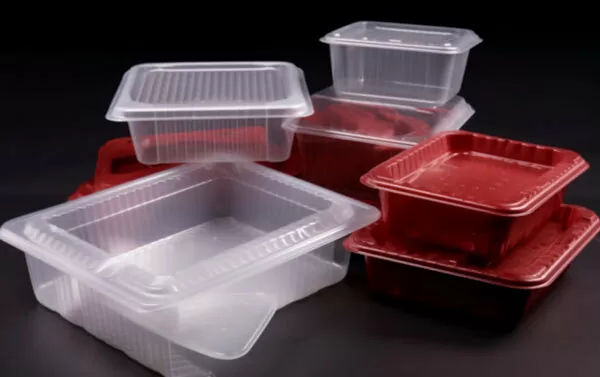
Production Efficiency: The Machines Behind Thermoforming
Thermoforming machines can be categorized into three types: vacuum forming, pressure forming, and mechanical forming. Each type has its specific use cases, with pressure forming often considered for high-volume, high-detail products, and mechanical forming for simpler, smaller jobs.
The Mechanics of Thermoforming Cut, stack and pack. If only it were that simple. While those three steps are indeed basic elements of nearly every thermoforming production process, there is much more to the big picture than meets the eye.
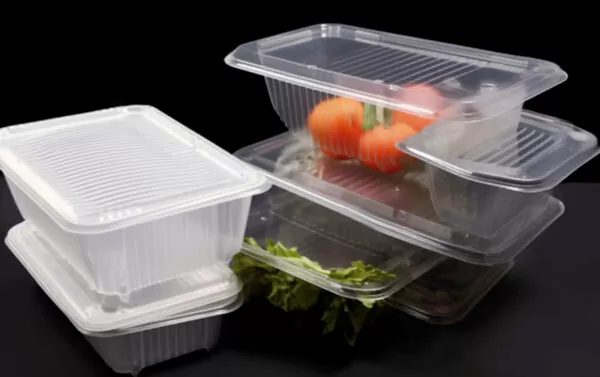
Limitations of Thermoforming
Thermoforming is a method used in different fields to mold plastic materials into many products. It’s flexible, efficient, low-cost and can be used on everything from car parts to disposable cups. Just like any other manufacturing technology, in addition to focusing on the advantages of thermoforming, there are disadvantages of thermoforming manufacturing process, so you should be aware of the following major limitations:
Material Thickness Consistency
One issue encountered in thermoforming is ensuring the thickness and no sharp corners of materials remains the same throughout a part. Particularly, when extensible plastic covers a mould there’s a danger it may become thinner – in zones where there are deep draws or complex shapes especially. This can impact the longevity and robustness of what’s produced in the end.
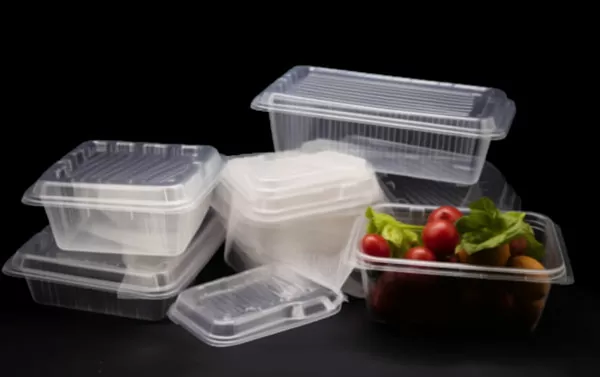
Detail Resolution
Thermoforming might not work well for items needing very fine detail. When heated plastic sheet, pulled over a mold and left to cool, it may not copy intricate features as accurately as injection molding can.
Cycle Time
Although vacuum forming process can be effective for mass production, the time it takes to create one part (cycle time) is often longer than other methods – particularly if each cycle requires warming a cold sheet of plastic. This may affect how long it takes to complete an entire order.
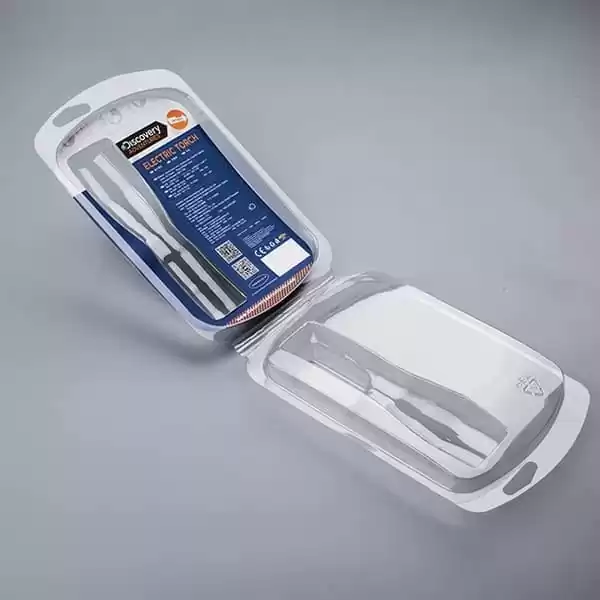
Material Limitations
Thermoforming only works with thermoplastics(high heat resistance) that soften when heated and keep their shape as they cool. Certain plastics – because of how they resist chemicals or change in response to heat – are not suitable for thermoforming.
Tooling Cost
Though usually not as high as for injection molding, the cost effectiveness of producing molds for thermoforming can still be substantial – especially if you’re creating custom designs. On small runs, it might not be worth this upfront investment.
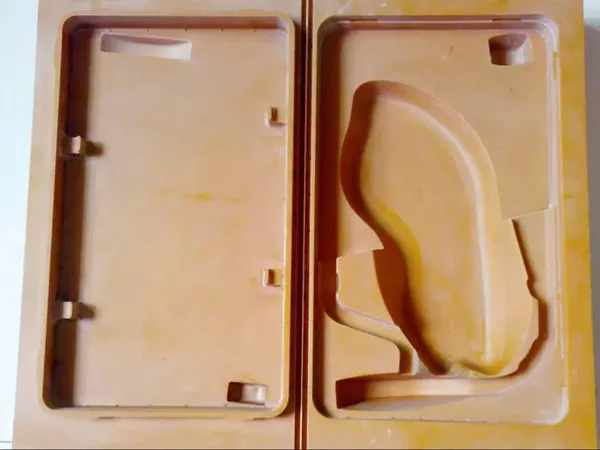
Environmental Considerations
Thermoforming shares some of the same environmental drawbacks as other plastic-making methods. Its sustainability can be affected by both the potential for waste leftover from trimming and the excess plastic themselves, which aren’t biodegradable.
Size Constraints
When it comes to making large objects, what sets the maximum size is the equipment and molds used in thermoplastic forming. It can be hard to get hold of or even make suitable machinery for really big or bulky things – which also tends to cost a lot more.
In summary, while thermoforming is a versatile and cost-effective option for many applications, it’s important to consider its limitations regarding material choice, detail resolution, cycle time, and environmental impact. By carefully assessing the requirements of the project against these factors, manufacturers can choose the most appropriate method for producing their plastic parts.
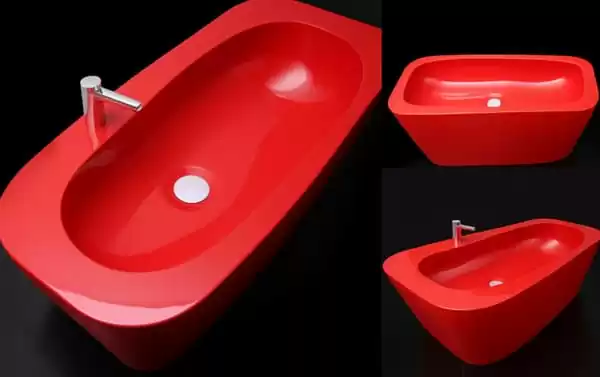
Design Constraints
While thermoforming is highly adaptable for designing purposes, some intricate elements may be challenging (e. g., sharp angles, undercuts or deep draws), necessitating costly adjustments to tools—or proving unachievable altogether. Compared with injection molding, this means designs must generally be less complex.
Surface Finish and Detail
The surface finish and detail of thermoformed parts may not meet the high standards offered by other methods. Fine details and textures might not turn out as sharp, so you could need to perform extra steps afterward to reach your desired look.
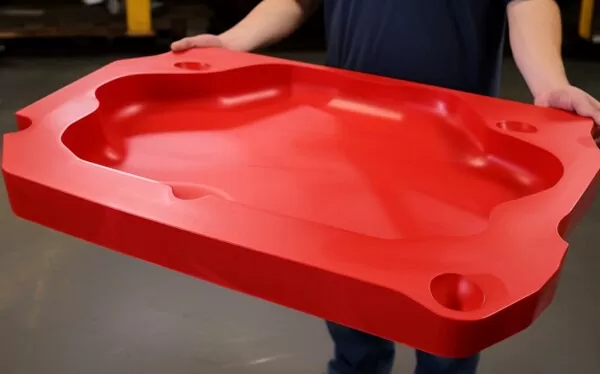
Overcoming Thermoforming Limitations
Dimensional Accuracy: Maintaining Product Consistency
It’s something every manufacturer wrestles with. Different factors affect the final size: how long things take to cool down; what kind of material you’re using; even how machines have been set up.There are measures you can take though, such as stretching the sheet in advance or getting better at cooling moulds, which should help minimise any discrepancies.
Surface Finish: Achieving the Desired Aesthetics
Achieving the desired surface finish for thermoformed parts can be challenging as they may not be as smooth as injection molded versions due to contact with the mold. Making sure tooling design is correct is key and sometimes secondary processes — such as trimming or painting — are used to make them look better.
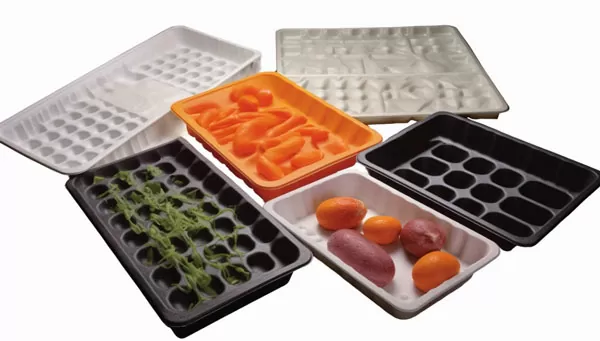
Material Selection: Balancing Cost and Performance
When it comes to selecting materials, there’s often a balance to strike between cost and performance. Those that perform better on the mechanical front or look nicer may be pricier – something product designers have to bear in mind if they don’t want their margins squeezed.
Innovations Pushing Thermoforming Boundaries
Technology and innovation are continually reshaping the thermoforming industry, expanding its capabilities and blurring the lines of what was once deemed possible.
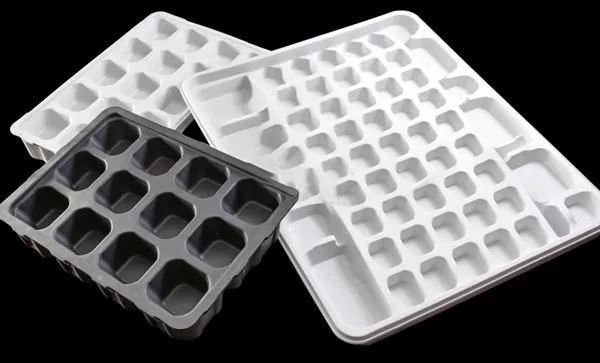
Intelligent Machine Control: The Future of Thermoforming
By using advanced machine control systems and AI applications, process precision and repeatability can be improved. It is possible for these systems to adjust instantly according to environmental factors or changes in materials so as to maintain high quality results even when faced with variability.
Sustainable Thermoforming: Eco-Friendly Materials and Processes
Driven by consumer demand and regulatory pressure, sustainable materials and practices are being adopted more frequently within the industry. This includes biodegradable plastics, recycled materials, and even plant-based polymers — all of which are gaining traction as viable alternatives.
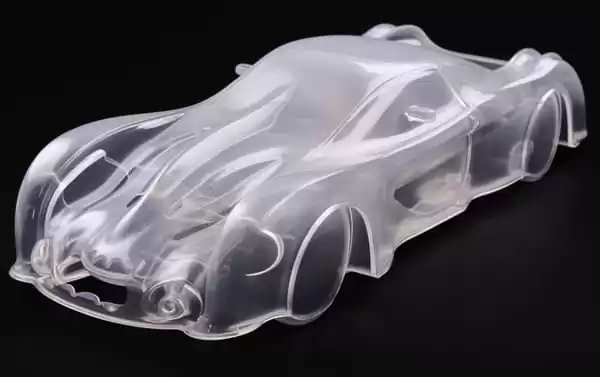
Additive Manufacturing Synergies: The Rise of Hybrid Processes
The combination of 3D printing and thermoforming is leading to exciting new opportunities in the creation of custom prototypes and tooling. This approach, which marries two different techniques, is reducing cost and time requirements – meaning thermoforming can now be used for an even greater range of applications.
Thermoforming in Future Industries
The versatility and adaptability of thermoforming position it as a key player in several burgeoning industries.
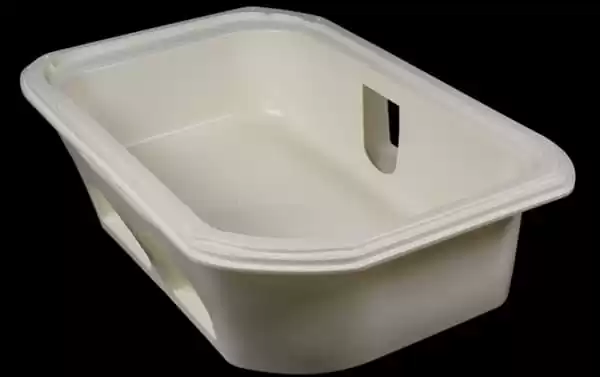
Healthcare and Medical Devices: Customizable and Disposable
When it comes to making medical devices that need to be customizable and disposable, thermoforming is a must. This process allows manufacturers to make lots of personalized things at once – from artificial limbs for individual patients, to plastic bags and packaging made just for one type of drug.
Automotive and Transportation: Weight Reduction and Design Freedom
In the automotive industry, thermoforming is helping to drive innovation by creating lighter-weight materials and more intricate shapes. This process is used to make many things for cars such as panels on their bodies or parts inside them like interiors; even items found under hoods!
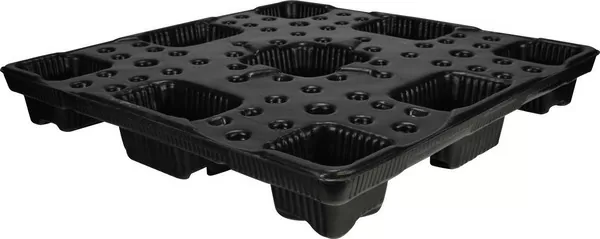
Consumer Goods: Rapid Prototyping and Mass Customization
The speed at which thermoforming can create prototypes and tailor products to specific customer demands has made it a boon for the consumer goods industry. Manufacturers of things like point-of-sale displays, packaging and items designed to withstand a lot of use all prefer it over other methods.
Best Practices for Successful Thermoforming Projects
Success in thermoforming projects is influenced by a range of best practices that ensure quality, efficiency, and innovation.

Collaboration is Key: The Design for Thermoforming Philosophy
A cross-disciplinary approach where designers, engineers, and manufacturers work closely from the project’s inception is critical. This “design for thermoforming” method makes sure that products are designed with this specific technique in mind – meaning they stay within its boundaries and possibilities.
Rigorous Testing and Validation: Assuring Product Integrity
Early detection and resolution of potential problems is possible by means of rigorous testing and validation procedures. Finite Element Analysis (FEA) and Mold Flow Simulation are two such techniques that predict material performance whilst also assisting in the design of tools for manufacturing.
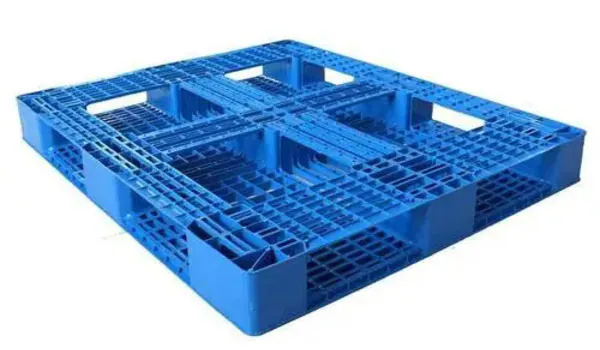
Continuous Improvement: Learning from Each Project
In every project, there is a chance to learn and get better. By asking people who use what the team makes or watching how things are made for input, those leading future efforts can get tips on how best to do things next time –– and improve designs too.
Conclusion
Thermoforming is an ongoing journey in which materials, machinery, design and human cleverness come together. It is about understanding what it can and cannot do – and then discovering just how far those limits can be stretched. To make things that will enrich our lives, drive new technologies forward and help industries move toward more sustainable practices.
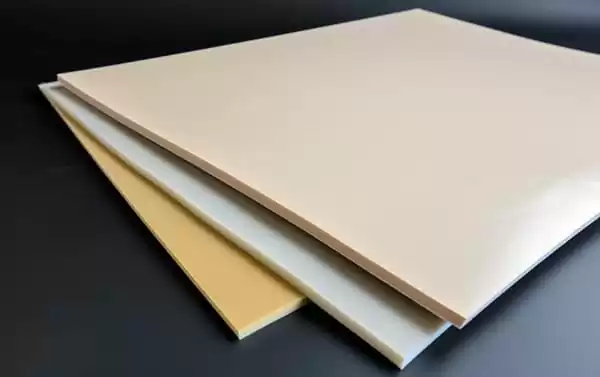
If you are a product designer who wants to bring your concepts to life in new ways, or an engineer looking for ways to make production processes better, or a manufacturer wanting to keep pace with progress then thermoforming offers endless possibilities for creative expression and technical achievement. The only limit is how much we can imagine – and how many innovations we can develop – as each new technological leap forward or successful application across different sectors shows us just what this process can do.