Plastic molding processing is an engineering technology that involves various processes for transforming plastic into plastic products, such as injection molding, thermoforming, rotational molding, compression molding, extrusion, blow molding, etc.
Amidst the sprawling expanse of contemporary manufacturing, few techniques can compete with thermoforming for sheer resourcefulness and forward-thinking. With a rich heritage matched only by its untapped potential, this art form has turned lightweight raw substances into objects of necessity that are seen everywhere – think everyday items, complicated car parts or long-lasting medicinal devices – thus cementing its position as a pivotal part of today’s industry.
Thermoforming stands as one of the most adaptable and economical manufacturing processes. It centers around heating a sheet of material until flexible then draping it over a mold. Whether you use plastics for consumer packaging or car parts, thermoforming probably played a part in making them; indeed, it has been used to shape polymers into useful objects longer than any similar method. Getting the heat right during vacuum forming is critical if things are going to turn out well—it determines the final shape.
For those already working in the industry or who are simply curious about thermoforming, our comprehensive examination of different methods used in heating for this process was made with you in mind. We’ll be looking at how to heated plastic sheet effectively so that it forms just right – making sure there’s no waste, saving time and energy too!
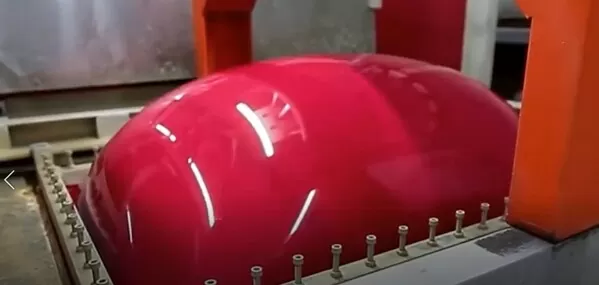
The Basics of Thermoforming
The process of transforming flat plastic sheets into three-dimensional objects using heat and air pressure is called thermoforming. This method has several advantages over older shaping techniques, since it can produce many different things – from plane interiors through to drinking cups. Broadly speaking then, the heating, forming and trimming involved in this approach combine to make pretty much whatever you need!
There are several thermoforming methods used in actual production: differential pressure molding, cover molding, plunger-assisted molding, suction back molding, opposite mold molding, female mold and male mold thermoforming, thin gauge thermoforming, heavy gauge(thick gauge) vacuum forming and twin sheet forming.

Types of Thermoforming
Three primary types of thermoforming exist, each with its nuances and applications:
Vacuum Forming: Mostly used for large, single-sided, and shallow-drawn parts such as blister packagings and inner linings for refrigerators.
Pressure Forming: Ideal for creating intricate parts with high-precision, such as automotive parts and electronic enclosures.
Twin-Sheet Forming: This type enables the production of complex, hollow shapes by joining two sheets in a single process, commonly found in pallets and containers.

The History of Thermoforming
In the early 1900s, thermoforming process technology was created and used first to fabricate small items like playthings and replicas. Back then, it depended mostly on straightforward manual processes: warm a sheet of plastic until pliable; apply suction from below to conform tightly against a die or matched mold forming ; cool down harden into final form. Although this technique may seem primitive now – just heating up plastic enough so you can bend it by hand without breaking anything! – these same basic ideas underlie all modern versions too.
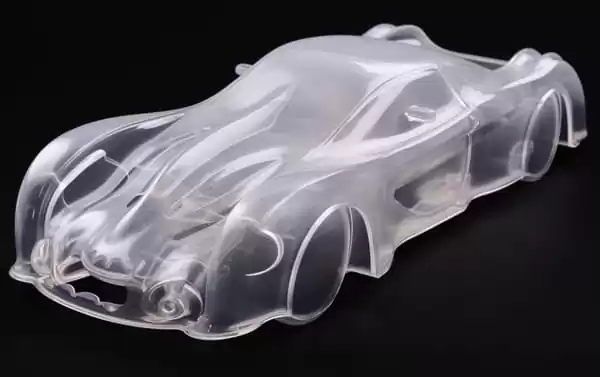
Thanks to the fast progress in plastics manufacturing, thermoforming is more popular today than ever before. Back in the 1950s, due to enhancements when it came to both properties and varieties of plastic materials accessible, it was then that complex items like auto parts and electrical casings began to be made with thermoforming methods. As time went on machines got better too – evolving from being manually operated into something we call an ‘automated production line’.
During the 1960s, advancements were made to thermoforming technology in the United States. At this time, there was an urgent demand within the U. S. aerospace sector for parts that could be both lightweight and have complex shapes – something thermoforming could provide. To meet these needs, researchers focused on various aspects of thermoforming including materials, processing equipment and techniques; expanding where this particular method might be applied.
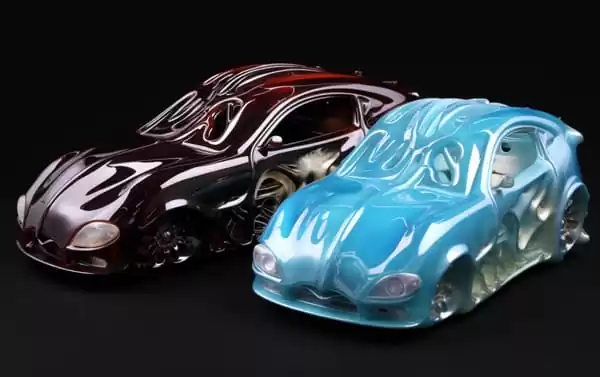
During the 1980s and 1990s, advancements in computer technology led to the integration of thermoforming with CAD/CAM systems, enabling digital design and production. This breakthrough enhanced accuracy, flexibility when designing thermoformed products and significantly increased output speed. It also opened up fresh applications for thermoforming technologies: medical equipment manufacturing; packaging materials.
As the 21st century began, vacuum forming process made even greater strides. People were becoming more and more interested in protecting nature, so specialists started using new materials like biodegradable plastics and recycled plastics when using thermoforming. This meant that the goods they created this way had less impact on the environment—or sometimes none at all. At around the same time these innovations were happening, people also figured out how to use thermoforming to make items with 3D printers. Printing stuff this way could be personalized or customized more than before—each object would have details chosen just for it—and some designers really liked this!
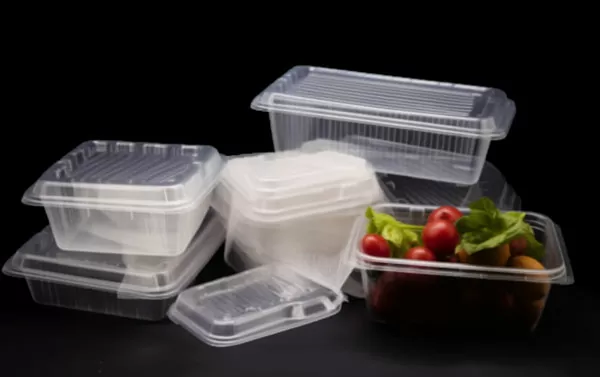
What is Thermoforming Heating?
The heating stage of thermoforming manufacturing process plays a critical role in transforming a plastic sheet into a shapeable material. Using heat to make the sheet soft and moldable is essential before moving it to the next step: forming. Here, the warmed sheet takes on the exact desired shape of whatever’s being used as a mold – but only temporarily – before cooling and turning solid again once more. How this initial heating phase happens – both technically and practically speaking – will heavily influence everything from how good your final product looks to whether or not its dimensions line up correctly with what was planned beforehand.

The Significance of Thermoforming Heating
In order to fully understand the methods, it is important to appreciate why heating in thermoforming isn’t just an initial step but a keystone of the whole process. The aim here is to get the plastic sheet into its thermoelastic state – where it’s pliable enough to be shaped by the mould and yet will stay like that even after cooling because then you can put it through subsequent production steps without it losing shape or getting damaged.

Types of Thermoforming Heating
The types of heating methods in thermoforming are diverse, each with its advantages and specific applications. Here are several methods renowned for their efficacy:
Contact Heat
The simplest way to heat a plastic sheet in pressure forming is by using contact heat. This involves putting the material onto something hot – like metal plates or cylinders – which warm it evenly so you can shape it easily later on. Typically, this approach is best suited for thinner materials as it allows for quick and efficient heating. However, there is a risk of surface imperfections on the sheet due to potential marks from the heated surfaces.

Radiant Heat
Using infrared radiation to transfer heat onto the plastic sheet is what radiant heating does. For thicker materials, this is often the preferred method as it lets the heat penetrate deeper and be distributed more evenly. Less chance of surface flaws are another reason why many companies opt for radiant heating when they want top-notch finished goods.
Radiant heating methods emit energy in the form of electromagnetic waves that travel through the air and only become heat when they come into contact with the material.
Halogen Lamps
Halogen lamps utilize a tungsten filament sealed within a transparent glass bulb filled with inert gas and a small amount of halogen gas. The combination of gases creates a cycle that redeposits evaporated tungsten back onto the filament. Halogen lamps produce intense visible and non-visible (infrared) light that provides substantial radiant heat.

Quartz Infrared Tubes
Quartz infrared tubes are another form of radiant heating that use a high-temperature resistant material to contain the tungsten filament. The tubes produce a wavelength that can be tightly controlled and directed toward the plastic sheet, allowing for a more focused heating area.
Conductive Heating
Conductive heating is the oldest and simplest method of thermoforming. It involves transferring heat to the plastic through direct contact with a heated surface.
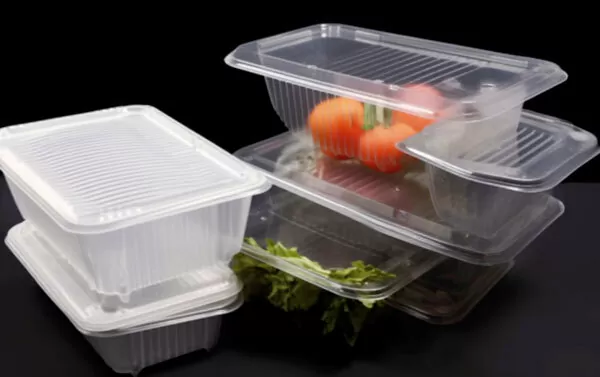
Contact Heating Plates
Metal heating plates, usually made of aluminum or steel, are brought into contact with the plastic sheet. The heat is transferred from the plate to the material through thermal conduction.
Resistance Heating
Resistive heating wires are embedded within the tooling or molds. When current passes through these wires, they heat up, in turn, heating the mold and the plastic material in close proximity.
Infrared (IR) Radiation
Infrared lamps emit electromagnetic waves that generate heat when absorbed by the plastic. IR heating is rapid and requires no physical contact, making it suitable for heat-sensitive materials.
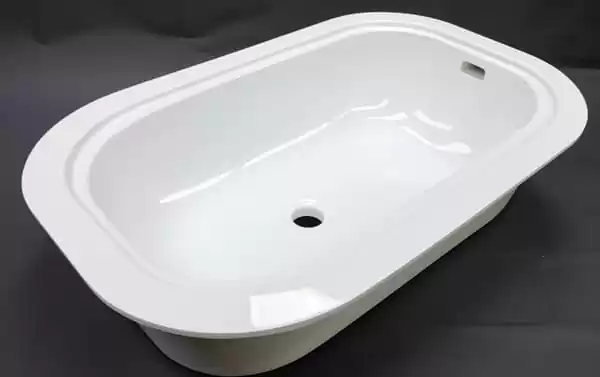
Convection Heat
Using hot air to warm plastic sheeting from all angles allows convection heat. This way works well for many kinds of plastic and heats them evenly – unlike contact or radiant heat processes, which might make some parts hotter than others. The down side is that using convection heating takes longer.
Convective heating utilizes heated air to transfer energy to the plastic.
Air Convection Ovens
Air ovens blow hot air over the surface of the plastic sheet. The convection current’s movement ensures more uniform heating by redistributing the air and prevents air stagnation or hot spots.
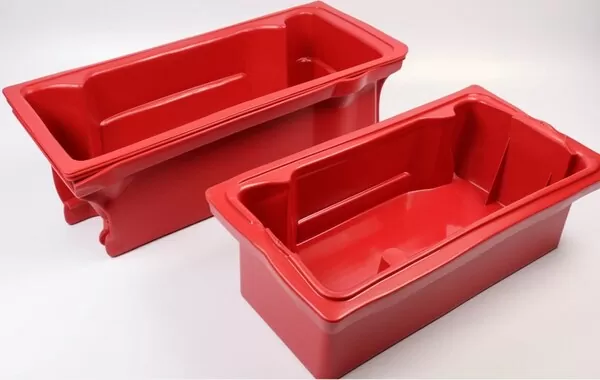
Infrared and Convection (IR/Convection) Ovens
Combining the best of radiant and convective heating, IR/convection ovens use infrared heating elements to preheat the surface of the sheet while hot air circulates beneath, providing more even heating through the material’s mass.
Infrared Heating
This method employs infrared radiation to heat the plastic. It’s fast and efficient, with almost no warm-up time.
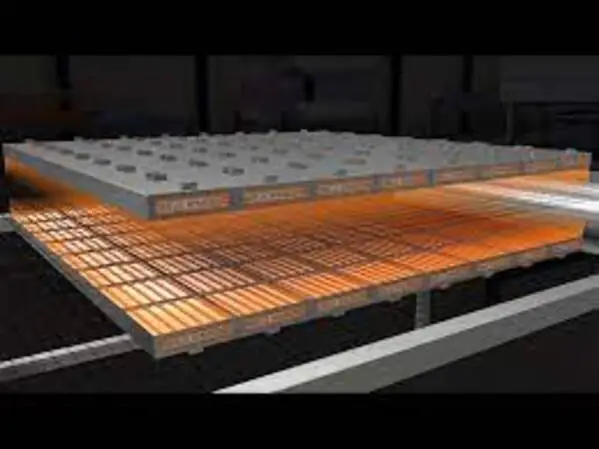
Quartz Heating
Similar to infrared, quartz heaters use electricity to produce heat, offering precise, controllable heat patterns and reduced cycle times.
Induction Heating
In this method, an alternating electromagnetic field heats a conductive metal mold, and the mold efficiently transfers heat to the plastic sheet.

Selecting the Right Method
Making a decision about how to heat something involves finding out what it’s made of, how complicated its shape is, how many you need to make – and how much energy you want to use.
Here are some things that matter when choosing the right method:
Material Sensitivity: Some substances react badly to getting very hot; using infrared may help stop this happening.
Part Geometry: If an object has a complicated shape, making sure heat goes all the way through requires different methods than if it was simpler.
Energy Efficiency: Finding ways to warm large numbers of things over time with low power consumption might be easier using convection techniques.

Emerging Trends in Thermoforming Heating
Promising Innovations in Heating Technology are Transforming Thermoforming The heating aspect of thermoforming is undergoing significant advancements across industries. With artificial intelligence (AI) and machine learning being integrated to enable precise temperature control and smart materials that adapt their heating requirements, future developments look very exciting indeed.There’s also work happening on hybrid solutions that use various methods together – which might mean better performance or energy-saving potential depending what you need most from your system!

1. AI and Machine Learning in Heating
The precision and efficiency of thermoforming heating systems could be transformed by integrating AI and machine learning. Smart technology would use data from molds and thermal sensors to forecast and control the heat profile more accurately than ever before, cutting cycle times and reducing waste.
2. Smart Materials for Self-Regulating Heating
Scientists are working on creating smart materials capable of altering how they transfer heat depending on conditions outside. If successful, these substances could make vacuum forming more energy efficient because they would automatically adjust how much they need to warm up — meaning outside energy sources wouldn’t be required as much or at all.
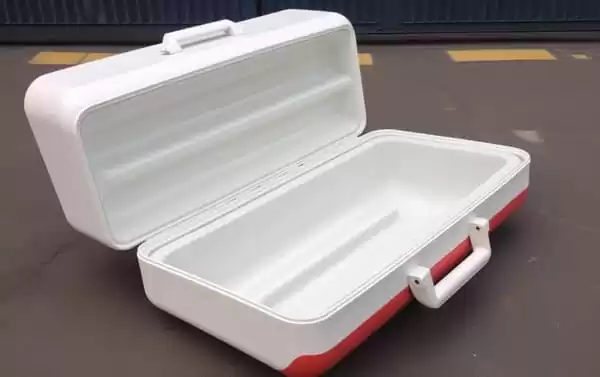
3. Hybrid Heating Technologies
Hybrid heating technologies are being experimented with to get the most out of different heating methods. This could mean mixing up infrared (IR) heating that warms up fast, and convection ovens that make sure heat is spread evenly; together these might improve thermoforming a lot.
Crafting the Perfect Temperature: Understanding Material Needs
When it comes to thermoforming, there’s nothing more important than temperature. Different plastics melt and conduct heat differently, so each one requires specific conditions in order to be shaped correctly. That’s why managing temperature ranges carefully is such an essential part of the thermoforming process.

Tailoring Temperatures to Different Materials
Polyethylene (PE): Low-density polyethylene needs a temperature range of around 190°C to 260°C, while high-density polyethylene may require a slightly higher range of up to 290°C. These common plastics need careful heating due to their sensitivity to the process temperatures.
PETG: This glycol-modified PET variant operates between 200°C and 240°C, and stable temperatures are crucial for precise forming to avoid edges that are too thin or too thick.
PVC: With a vacuum forming temperature range of 200°C to 240°C, PVC requires heating for longer durations to reach its full malleability without becoming brittle.
Polystyrene (PS): At a range of 190°C to 230°C, PS can be formed quickly but is sensitive to high temperatures and may start to degrade beyond its thermal limits.
Acrylonitrile Butadiene Styrene (ABS): Used in complex parts, ABS typically forms at temperatures exceeding 392°F (200°C).
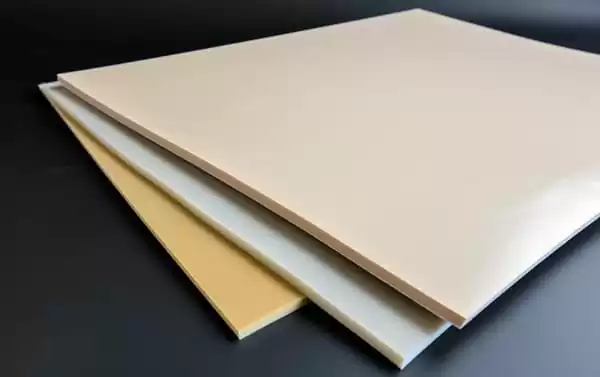
Material Thickness and Uniformity
When heating a plastic sheet for pressure forming, it’s crucial to consider its type as well as how thick and consistent the material is. That means whatever heating method you choose should be able to change depending on the size and makeup of the sheet so that every part of it gets hot enough to form correctly.
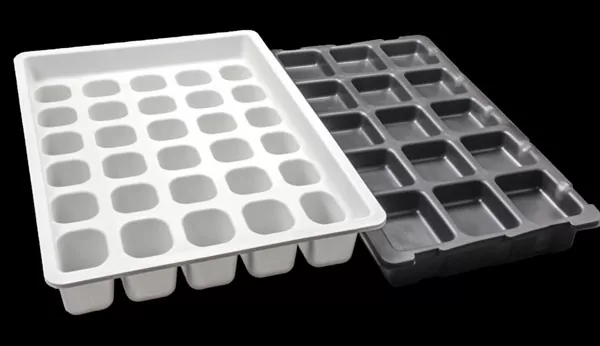
Balancing Speed and Precision: The Art of Forming
Reaching the right temperature is only part of heating; you also have to balance how fast you warm up with how accurate you are. If it gets too hot, your piece might change shape or even get worse because its material breaks down. Too little heat means not all of what you’re making forms properly and details won’t look sharp either.
Optimizing Heat Distribution
Utilizing mold design: The way your mold is made can influence how heat spreads through it. By building a mold that lets material flow perfectly into every space needed, you’ll be able to ensure even heating.
Airflow control: Convection ovens rely on consistent airflow to evenly heat the plastic sheet. If you can adjust how fast or slow this air moves—or which direction it goes in—you’ll have more control over where warmth ends up inside your plastic sheet.
Temperature monitoring: Employing sensors across the sheet and the heating elements can allow for real-time adjustments to maintain ideal temperatures.
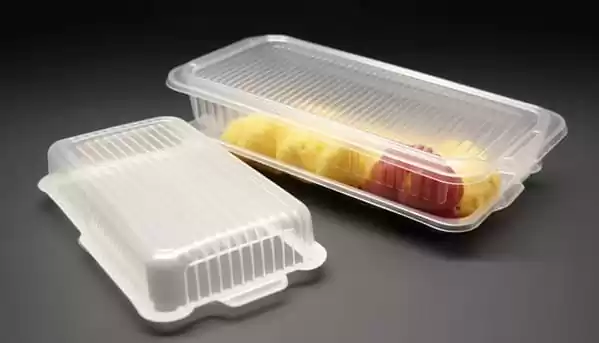
Continuous Improvement: Advanced Thermoforming Heating Techniques
In order to lead the way in thermoforming, thermoforming companies must constantly develop and implement advanced heating technologies that offer greater control, shorter cycle times and a competitive edge – while being sustainable.
Advanced Heating Technologies
Servo-driven systems: Vacuum forming machine that incorporate servo-driven ovens enable the fine-tuning of the heating process, cutting down on wastage and ensuring superior part quality.
Multi-zone heating: Dividing heating elements into zones means different parts of a sheet can be subjected to differing temperatures – advantageous when dealing with large or complex shapes.
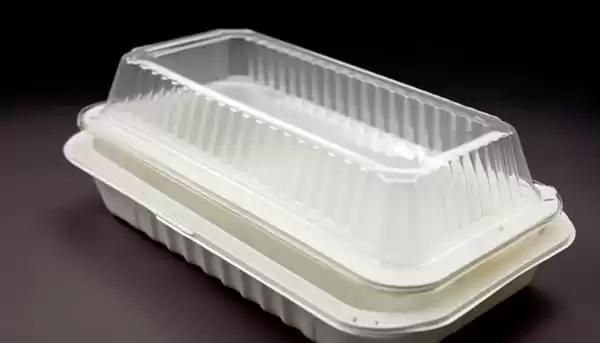
Specialized coatings: Coatings applied to heating elements in thermoforming machines stop materials sticking, reduce energy use and spread heat more evenly.
Pre-stretch heating: A preliminary stage before main heating begins, pre-stretching warms material up while simultaneously making it thinner. Doing this helps ensure what ends up being formed is consistent from start to finish.
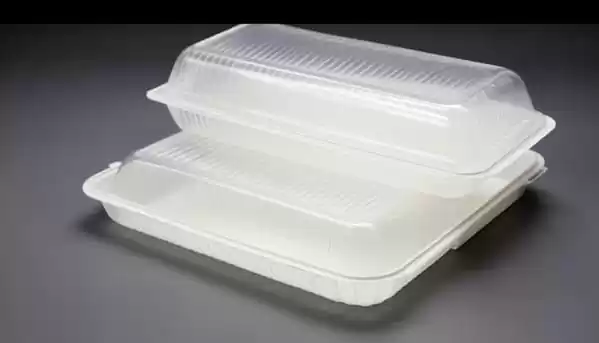
Understanding Your Tools: The Role of Equipment
The type of heating equipment used in thermoforming dictates the results. Modernization in heating equipment can lead to increased productivity and part accuracy.
Equipment Selection and Maintenance
Machine size: The size of the heating machine directly impacts the sheet size you can work with as well as production capacity.
Energy efficiency: Newer machines often come with enhanced energy-saving features, contributing to a company’s carbon footprint reduction and long-term cost savings.
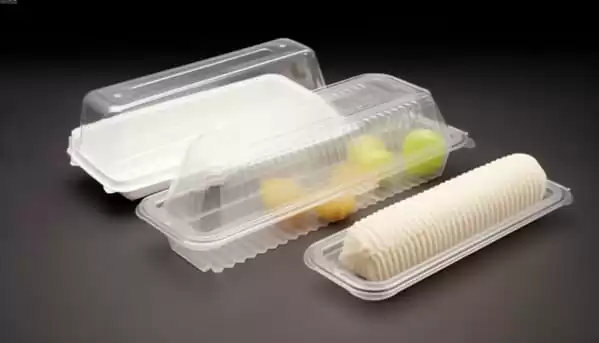
Regular servicing: Haphazard maintenance can lead to inconsistent heating, resulting in a waste of material and time. Regular servicing is critical to keeping equipment in peak condition.
Staff training: Well-trained operators can maximize a machine’s capabilities, maintain it effectively, and troubleshoot minor issues quickly.
The Path Forward: An Industry Poised for Advancement
A major innovation occurring within the thermoforming industry is the speedy progress being made around heating technologies. As manufacturers strive for greater levels of accuracy, efficiency and sustainability, the focus on this particular stage of production is growing and evolving at a rapid rate.
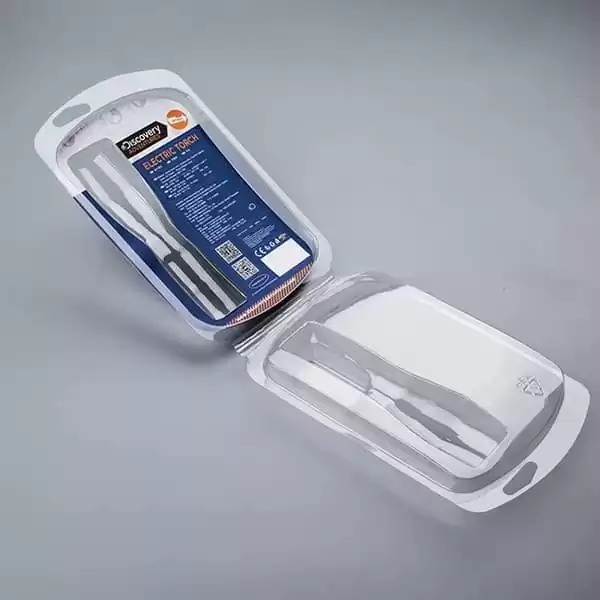
Shifting Trends and Emerging Technologies
Industry 4.0 integration: Thermoforming lines are now being integrated into wider Industry 4. 0 frameworks – allowing connected systems to make automated decisions based on data that optimises the heating phase.
3D printing molds: As 3D printing technology continues to improve, it is now possible to create moulds with complex features – specifically engineered to enhance vacuum forming – comparatively easily.
Material innovations: The ongoing development of new materials and composites means fresh products requiring different ways of being heated are always appearing in this sector – which in turn has led to research focused on finding more adaptable heating methods intensifying too.
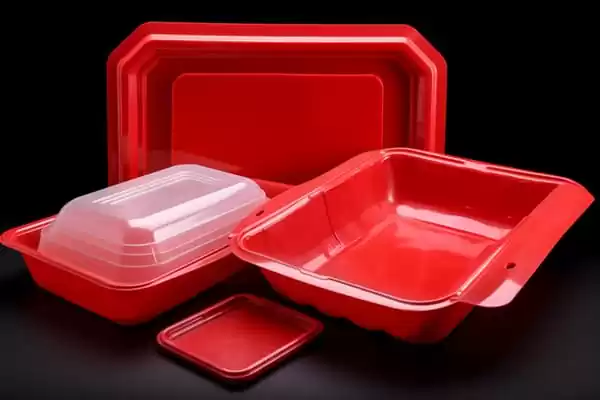
Conclusion
In order to fully unlock the potential of thermoforming processes, it’s crucial for manufacturers to recognize how material requirements, optimal temperatures, even heat distribution and innovative technology interact together.
Effective heating not only shapes the final product but also shapes a company’s competitive edge. It’s an area ripe for ground-breaking innovation, and those who master it will influence the future of thermoforming. With a commitment to continuous learning and adaptation, professionals can achieve superior outcomes, sustainable practices, and continued success in the evolving thermoforming landscape.
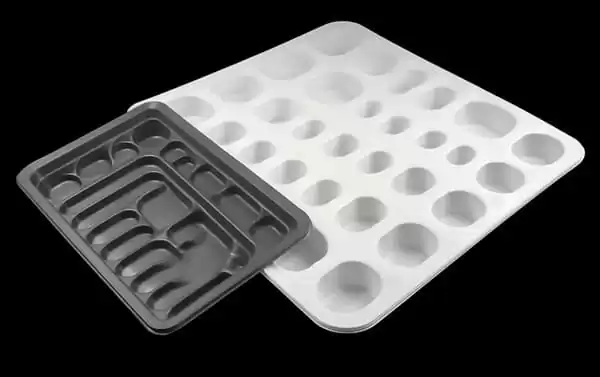
In the complex world of plastic thermoforming, heating represents the dawn before the form. It’s a critical act of sculpting the raw plastic material into a functional, beautiful, and market-ready product. With an understanding of the heating methods and the intersection of material science, machinery, and process control, thermoformers can shape the future, one heated sheet at a time.
When it comes to heating in thermoforming, there is no one-size-fits-all solution. Different methods offer different benefits, and it’s up to manufacturers to find the right balance between art and science.Get things wrong, and not only will products look subpar, they’ll also be structurally unsound or mechanically inconsistent. Get them right though – by knowing what your materials can and can’t do for you alongside working knowledge of heating techniques – then the results speak volumes: beautiful objects with uniform mechanical properties.Looking ahead; new options for moldable materials are being developed all the time while industry itself becomes more efficient thanks partly due advancing technologies