Thermoforming, a process for converting plastic sheets into items ranging from automotive parts to packaging materials, is popular for two reasons. One can be found in the length of time it takes to complete each cycle – that is, heating them so that they are malleable enough to be shaped, shaping them to their new use, and finally cooling everything down again to prepare them for further use.
Thermoforming plays a key role in the production of many common goods because it allows manufacturers to quickly and cheaply transform plastic sheets into a variety of items. However, as manufacturers seek greater control over thermoforming, how long the production process takes (called “cycle time”) is a critical issue. The shorter the cycle time (including mold closing/opening and part ejection), the faster the manufacturing speed; increasing overall output levels while further increasing efficiency! In the following in-depth study, we’ll explore the various factors that influence these cycle times, particularly during vacuum forming; revealing some surprising facts as well as not-so-obvious ones.

This in-depth blog post focuses on discovering the factors behind thermoforming cycle times and how they impact production efficiency and throughput. Armed with knowledge of what makes things faster or slower in manufacturing; you can not only make your own processes more efficient, but you can also save money.
Whether you are a beginner trying to learn about plastics manufacturing, or a professional in the field committed to operational excellence, this article is for you! We’ll explore how everything from material selection to mold design affects thermoforming cycle times. If they’re interested in getting better at something, then keep reading because later we’ll reveal some tips on how to best achieve optimal performance when thermoforming.
Material Selection: The Building Blocks of Thermoforming
1. Understanding Your Plastics
The thermoforming process is associated with its use of a range of thermoplastic materials, which all require a customized approach to control cycle times. The speed and effectiveness of molding largely depends on the choice of material – from flexible polyethylene to rigid polystyrene, for example.

2. The Thickness Challenge
Material thickness is directly related to heating and cooling time. Thinner materials heat and cool faster so they can be formed faster, which means the overall process is shorter. In contrast, thicker plastics usually need to be heated longer before anything happens, and then may also need to be cooled in a special way, which essentially lengthens the cycle time.
3. Properties that Matter
The natural properties of a plastic, such as melt flow, crystallization rate and whether the structure is amorphous or semi-crystalline, determine whether it can be recycled quickly enough. Understanding these fundamentals of materials allows engineers to calculate optimizing cycle time for thermoforming in advance.
4. Material Matters
Thermoforming cycle times are greatly affected by the type of plastic material used. This is because different resins have different melting points, thermal conductivities and viscosities – all factors that affect how much heat needs to be applied and how quickly it cools down again afterwards.

5. Melting and Cooling Rates
Polymers with lower melting points, such as polystyrene, tend to have shorter cycle times than high-temperature plastics such as polycarbonate. However, their cooling rate (determined by thermal conductivity) can also be slowed or accelerated. For example, copper- or graphite-filled polymers typically cool faster than unfilled polymers, affecting the time it takes for a molded part to fully cure.
6. Sheet Thickness and Uniformity
Another important factor to consider is the thickness of the plastic sheet. If it is thicker, the heat distribution will take longer; likewise, cooling afterward will take additional time. Additionally, there is the issue of ensuring that all parts are heated equally, which may mean adjustments need to be made mid-production, which also adds minutes or hours to each cycle and very high volume jobs.
Mold Design
1. The Mold’s Role in Success
There is a critical step in the thermoforming process that is often overlooked, and that is mold design. It plays a huge role in cycle time. Molds with better heat distribution and faster cooling capabilities or has a smooth mold surface can greatly minimize cycle time.

2. Complexity vs. Efficiency
Creating complex parts requires using more complex molds, which can also increase cycle times because they require more time to be pressurized or have complex cooling systems. Striking the right balance between mold efficiency and complexity is what experienced professionals are constantly striving to get better at.
3. Designing for Speed
Optimizing the mold design for swift action, including minimizing the distance parts must travel, can contribute to significant time savings. Incorporating features that facilitate quick part release and tool movement is key.
The Heating System
1. The Heart of Thermoforming
The heating system softens the plastic sheet through high temperatures, making it a critical part of the thermoforming cycle and marking the beginning of the pressure forming cycle. In fact, how you go with the first step affects everything that follows!

2. The Battle Against Inefficiency
Traditional heating methods can cause a lot of trouble for manufacturers because heating and cooling take a long time, which means the molding process takes longer, which affects the manufacturing speed of the product. However, newer technology offers better control, so this won’t happen as often: cycle times will be more regular.
3. Advances in Technology
Infrared radiant heating and Rapid Heat & Cool (RH&C) systems are among the innovative technologies that aim to revolutionize thermoforming by significantly reducing heating times.
In contrast to contact heating technology, infrared heaters provide fast, even heat without the need for direct contact with the plastic itself. However, it should be noted that although the infrared heating method sometimes takes longer to heat up the whole compared to contact heating, its heating uniformity will be better, preventing local areas from overheating or burning.
Ultrasonic heating can significantly reduce cycle times. Ultrasonic heating systems convert electrical energy into heat inside the resin, so the process runs faster. Whether they will be affordable (or even feasible) at scale is another matter entirely!
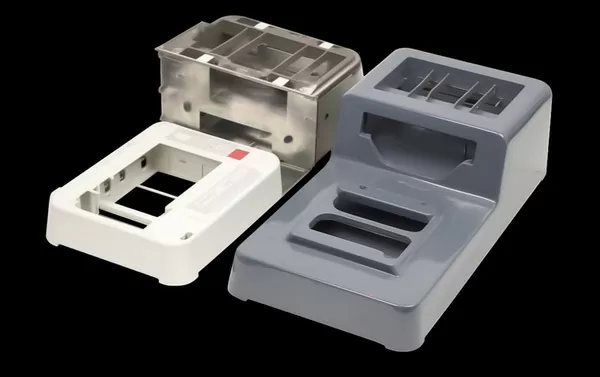
Cooling System and Methods
1. Cooling Completes the Picture
The temperature difference between the mold and the cooling medium, as well as the effectiveness of the material used for the mold, influences cooling times. Additionally, the practicalities of implementation, such as cycle complexity, play a role in determining cooling efficiency.
2. Factors Affecting Cooling
Cooling time can be affected by a number of factors: the temperature difference between the mold, the mold temperature, and its cooling medium; how efficiently the material used to make the mold conducts heat; plus whether anything else is happening during the injection molding cycle that could also be slowing it down (e.g. turning on/off additional parts).
3. Striving for Rapid Reduction
Quenching, compressed air, and water cooling are prominent options for accelerating the cooling process, often resulting in a dramatic decrease in cycle times when implemented correctly.
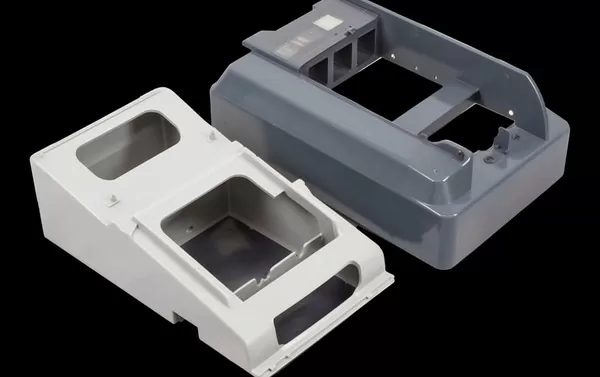
Machine Type and Automation
1. The Role of Automation
When comparing manual operations to automated operations, it is obvious that the former takes more time. By looking at how much of a process can be automated, and how this affects its duration, there seems to be strong evidence in favor of automation if speed is your thing!
2. Comparing Machines
Depending on the type of pressure forming equipment used, machine cycle times can vary significantly. Fully automatic machines always outperform manual and semi-automatic machines in this regard – as shown in the few real-life examples below that provide concrete evidence of the advantages of automation.
3. The Human Element
No matter how complex a piece of equipment is, its productivity always depends on the people who use it. The operator’s level of attention, proficiency and instruction can change cycle times so drastically – that this factor deserves serious consideration (and expense if necessary).
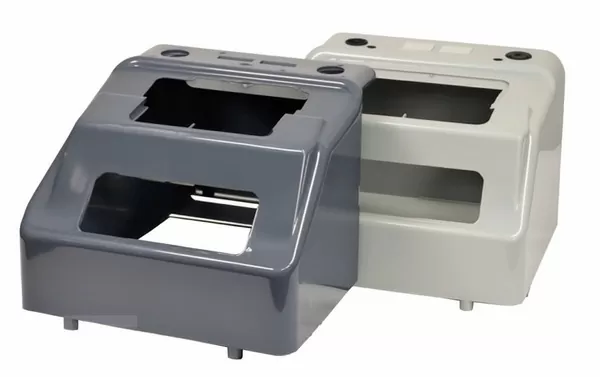
Operator Expertise and Training
1. Realizing the Human Potential
Automated systems also have their own limitations. They cannot make split-second adjustments and decisions or make fairly accurate prediction(cycle time estimate or estimated cycle time) like a skilled operator, so each cycle takes longer. If you want to improve your cycle time, one way to do this is to invest more in employee training, as their skills can help them shorten the time on each task.
2. Strategies for Mastery
If you want your employees to consistently get their work done faster, regular refreshers on what works, advanced techniques, and constantly learning more are key.
3. The Path to Efficiency
By mentoring people, training them on different things, and learning and leveraging industry best practices in creative aspects. The human element in thermoforming can evolve from a variable to a reliable source of efficiency in shortening cycle times.

Environmental Conditions
1. The Invisible Hand
Oven temperature and humidity levels have a subtle but profound effect on cycle times in a thermoforming plant. When these metrics fluctuate too much, it can cause the carefully tuned heating-cooling protocols to fail, resulting in inconsistencies and longer than planned production cycles.
2. Managing the Environment
By using state-of-the-art climate control systems, equipment that tracks conditions, and a well-thought-out facility layout, any problems caused by changes in the surrounding environment can be reduced – meaning a vacuum forming environment is suitable for rapid prototyping and reduced cycle times.
3. Strategic Timing
Strategically scheduling operations during times of optimal environmental stability can further streamline the thermoforming process, especially when working with highly sensitive materials.
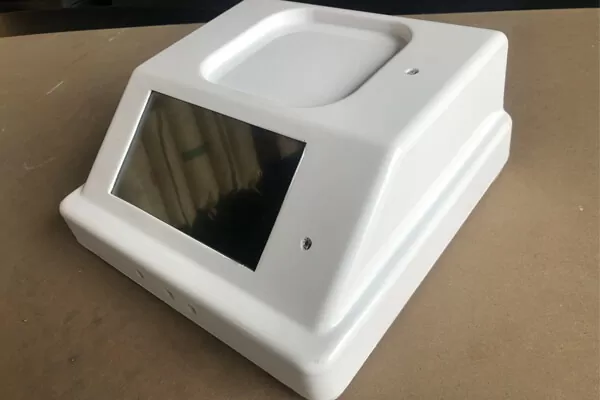
Conclusion
Efficiency in thermoforming cycle times can be achieved by carefully coordinating a variety of factors such as material selection and properties, mold design, heating/cooling methods, level of automation/type of machines used, operator skill/experience level using those machines, and even Environmental conditions surrounding production. Everyone plays an important role!
Effectively reducing thermoforming cycle times involves many factors that must be carefully examined and thoroughly understood. Manufacturers need to analyze each step—material selection, heating, cooling and forming—and the people who use the equipment. Once you’ve identified areas with potential for improvement, you can begin in earnest to improve efficiency and productivity.
Reducing thermoforming cycle times is not just about only the cycle time and speeds, it also means precision and consistency. Because any time you save in each cycle can be used to manufacture other products, this step alone has potential benefits for the manufacturer’s overall bottom line, as well as their competitiveness in the market!
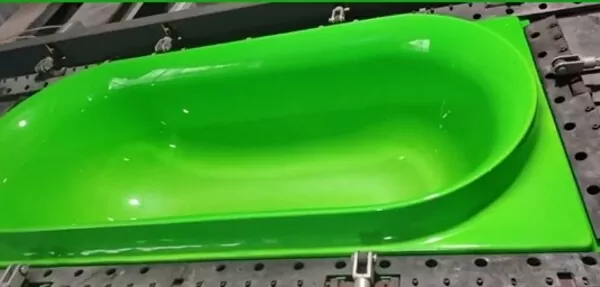
In our in-depth analysis, we have only begun to explore the myriad of factors that can affect thermoforming cycle times. The quest for manufacturing efficiency will always continue – being able to understand and control these elements will be absolutely critical if a company wants its thermoforming operations to be successful for many years to come.
When exploring the factors that affect thermoforming cycle times, as with the injection molding process, there are various factors to consider, such as the type of thermoforming and injection mold, sell estimated press time, insights from John’s Plastics Technology Columns, and the specific characteristics of injection molding. Thermoformed parts and injection molded part, especially an older model.