Most people are often confused when facing the two processes of blow molding and thermoforming. After all, they both involve air forming, but what is the difference between them? In this blog, we’ll dive into the differences between the two processes and help you better understand their respective characteristics.
The main principle of thermoforming is to heat a flat hard plastic sheet to soften it, then use vacuum adsorption on the surface of the mold, and then form it after cooling. It is widely used in plastic packaging, lighting, advertising, decoration and other industries. It is mainly used for packaging. It can save raw and auxiliary materials, is light in weight, easy to transport, has good sealing performance, and meets the requirements of environmentally friendly green packaging. Just because of its low price and high production efficiency, it has become a manufacturing process for many products. Plastic products can be seen everywhere in our lives, so its production processes are also diverse. When selecting, you need to choose an economical and practical process based on the actual conditions of the factory.
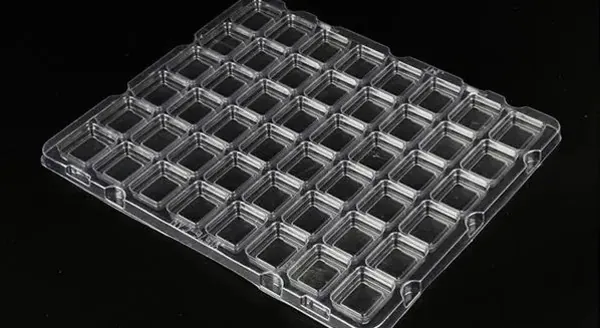
Blow molding refers to a tubular plastic parison obtained by extrusion of plastic, which is placed in a split mold while hot. After the mold is closed, air is compressed in the parison immediately to inflate the plastic parison and stick to the inner wall of the mold. After cooling and demoulding, various hollow products are obtained. Blow molding is relatively suitable for products with large hollow areas, such as bottles, buckets, etc.
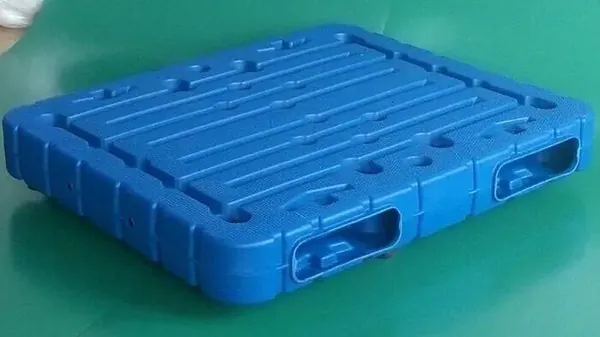
Different Manufacturing Processes
Thermoforming
Thermoforming is a plastic processing technology. The main principle is to heat a flat hard plastic sheet to soften it, then use vacuum adsorption on the surface of the mold, and then form it after cooling. It is widely used in plastic packaging, lighting, advertising, decoration and other industries. Thermoforming is further divided into sheet thermoforming and thick plate thermoforming. Sheet thermoforming refers to thermoformed packaging products including: bubble shells, trays, thermoforming boxes, thermoforming trays, and synonyms include: vacuum cover, blister, etc.
There are several thermoforming methods used in actual production: differential pressure forming, overmolding, plunger-assisted molding, suction molding, countermolding, male mold thermoforming, female mold thermoforming, and twin sheet thermoforming.
The main advantages of thermoforming packaging are that it saves raw and auxiliary materials, is light in weight, easy to transport, has good sealing performance, and meets the requirements of environmentally friendly green packaging; it can package any special-shaped products, and no additional buffering materials are needed for packaging; the packaged products are transparent and visible.
The appearance is beautiful, easy to sell, and suitable for mechanization and automatic packaging, which facilitates modern management, saves manpower and improves efficiency. Thermoformed packaging products are widely used in hardware tools, IT electronic products, sporting goods, toys, small household appliances, food, cosmetics, automobiles, medical and other industries.
Thick plate thermoforming, also known as thick sheet thermoforming, refers to a technology where the thickness of the raw materials used exceeds 2mm and cannot be thermoformed on a fully automatic machine. Semi-automatic pressure forming machines dedicated to thick plates must be used for processing and production.
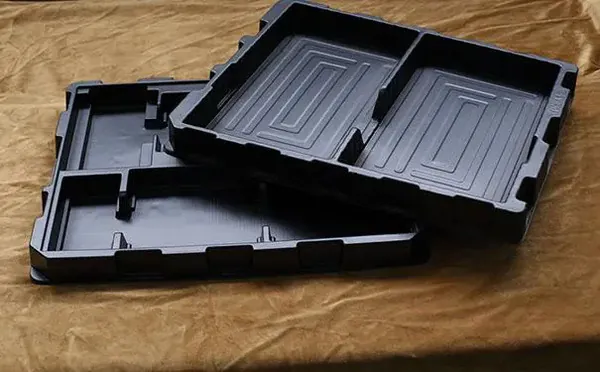
Thick plate thermoforming can be used for product design and manufacturing of rear projection TV back covers, displays, medical equipment, textile machinery, automotive accessories, and product design and manufacturing in precision electronics, medical equipment, and cosmetics industries. Thick sheet thermoforming products mainly include refrigerator liner thermoforming, PS thermoforming, ABS thermoforming, shell vacuum forming, thermoforming shell, thick plate thermoforming, thick wall thermoforming, acrylic thermoforming, PMMA thermoforming, etc.
The thick sheet thermoformed products are widely used in medical equipment, food equipment, instrument casings, electrical casings, automobile body sheaths, pet trays, advertising light boxes, lighting, refrigerator industry, air conditioning industry and home appliance accessories. Thick sheet thermoforming products can not only replace injection molding machine, saving the cost of expensive injection molds, but also replace traditional manual production. They have the advantages of exquisite production technology, fast speed, and reliable quality.
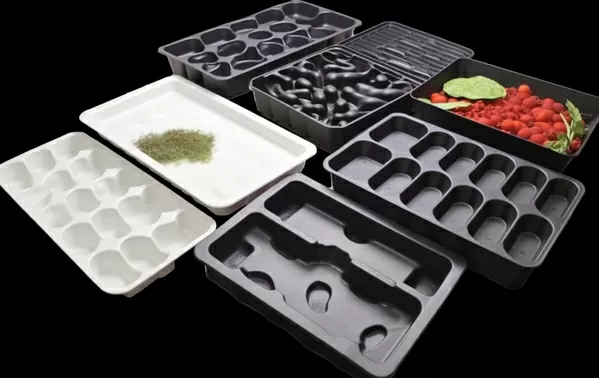
Blow Molding
Blow molding is a rapidly growing plastic processing method. The tubular plastic parison obtained by extrusion or injection molding process of thermoplastic resin is placed in a split mold while it is hot (or heated to a softened state). After the mold is closed, compressed air is immediately introduced into the parison to blow the plastic parison. It expands and adheres closely to the inner wall of the mold. After cooling and demoulding, various hollow products are obtained.
The blow molding process is divided into several steps such as melting(molten material), blowing, cooling, and demoulding.
The manufacturing process of blown film is very similar to the blow molding of hollow products in principle, but it does not use molds. From the perspective of plastic processing technology classification, the molding process of blown film is usually included in extrusion. Plastics suitable for blow molding include polyethylene, polyvinyl chloride, polypropylene, polyester, etc. The resulting hollow containers are widely used as industrial packaging containers. According to the parison production method, blow molding can be divided into extrusion blow molding and injection blow molding, and the newly developed multi-layer blow molding and stretch blow molding.
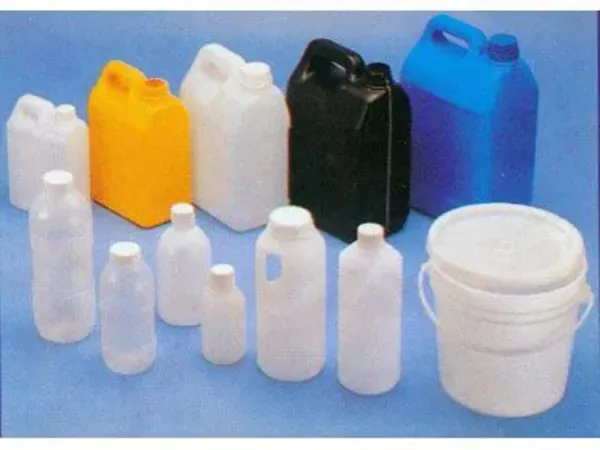
History
Thermoforming has been known as early as the beginning of the 20th century. After the 1940s, it began to be used in industrial production. It was not until the 1960s that pressure forming began to have greater development and was widely used by people. The thermoforming process has developed along the way and has become one of the important methods for processing packaging materials.
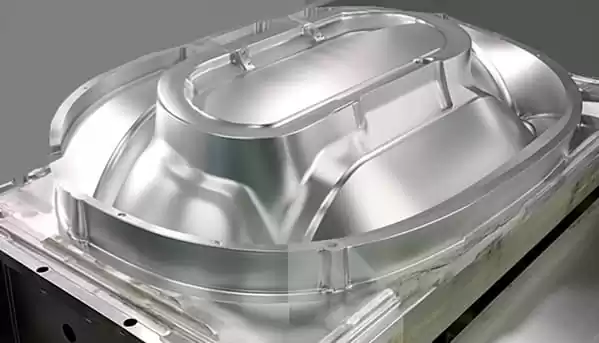
The blow molding process began to be used to produce low-density PE vials during World War II. In the late 1950s, with the birth of high-density PE and the development of blow molding machines, blow molding technology was widely used.
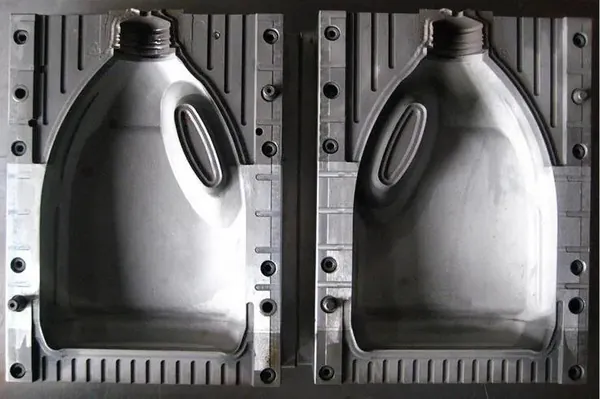
Advantages and Disadvantages
Both thermoforming and blow molding have their applicable scenarios and technical difficulties. Thermoforming is usually more suitable than blow molding for producing smaller batches of finer plastic parts and components, such as gift boxes, plastic trays, etc. Vacuum forming technology can also be used to create transparent plastic containers. But vacuum formed products are more expensive to manufacture. Blow molding is suitable for the production of large-sized hollow products, such as plastic barrels, water tanks, etc. Blow molding can simultaneously form the wall thickness and inner space of plastic products when manufacturing products, making them stronger and easier to process and produce, but the accuracy is relatively low.
Thermoforming:
Advantages: Fast production speed, tough and durable products, high precision, multiple functions and good sealing.
Disadvantages: high production cost, difficult to recycle, high energy consumption, and inability to produce seamless long tubes.
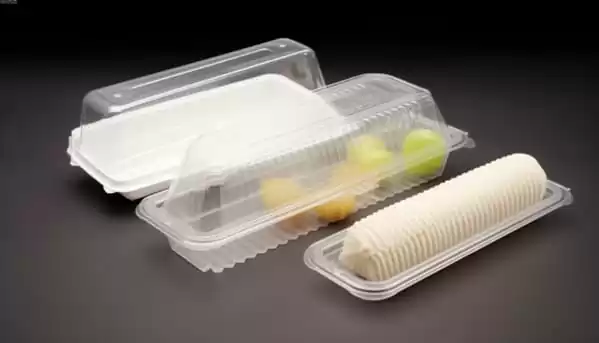
Blow Molding:
Advantages: simple production equipment, low cost, light products, good permeability, and can produce seamless pipes.
Disadvantages: The process is cumbersome, the plastic products produced by one production line are of various types, and the price bonus period is short.
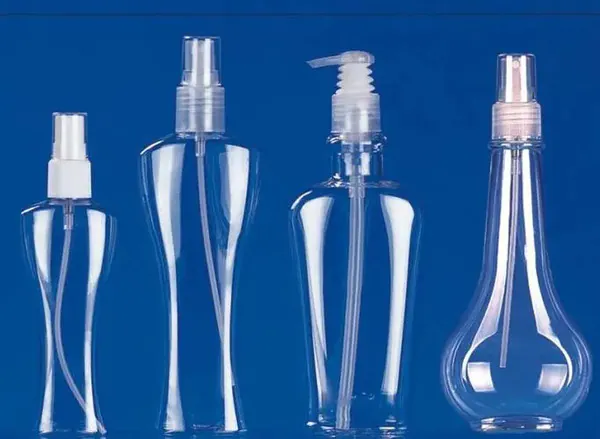
Different Cost
Thermoforming is simple, fast, and suitable for producing small batches of products, but it is greatly limited in terms of product wall thickness and material quality.
Blow molding is suitable for making small and medium-sized hollow products. The cost is relatively low and the speed is fast. However, the market competition is fierce and the design and appearance of the product are relatively limited.
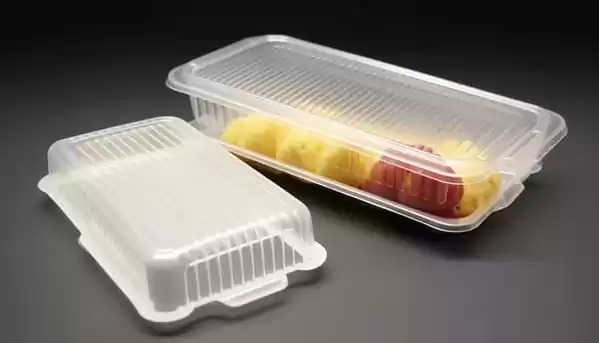
Different Speeds
The thermoforming speed is fast, the production of products with wall thickness ≤3mm is stable and efficient, and the production of multiple models of products can be completed at the same time during accounting.
Blow molding is fast and has high production efficiency, but this process focuses on products with lower requirements for appearance design, gloss and precision.
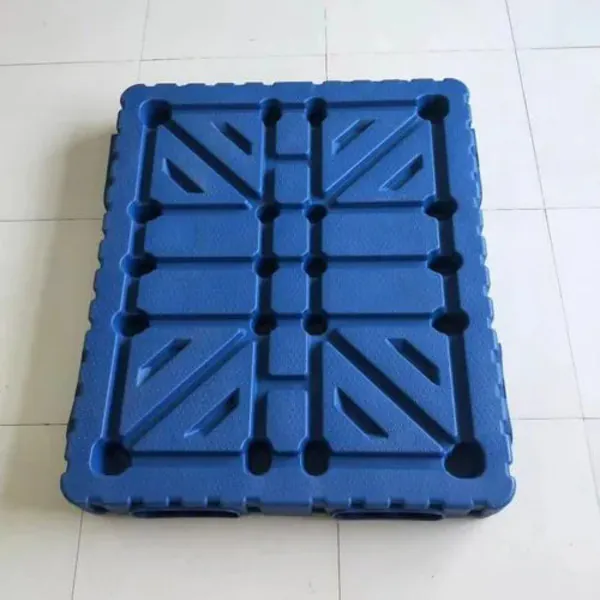
Different Product Performance
Thermoformed products are light, thin, bright in color, and have high surface smoothness, and can be used to produce three-dimensional, curved, and linear products.
The surface texture of blow molded products is better. Due to the process, the products are usually rounder and less refined in appearance.

Different Production Processes
In the thermoforming manufacturing process, product design and mold making are very important steps. First, a suitable mold needs to be made according to the shape and size of the product. The plastic sheet is then heated, sucking and blowing heat many times until it is formed.
In the blow molding manufacturing process, special machinery and equipment are required to create plastic core rods and inject them into the mold. This process requires the use of high-precision equipment and skills to ensure the accuracy of product shape and size.
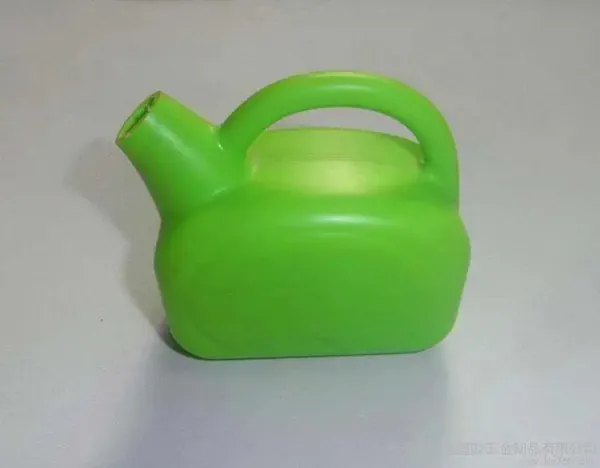
Different Product Forms
The product shapes produced by pressure forming and blow molding are also different. The products produced by vacuum forming process have various forms and can be made into plastic products of different shapes, thicknesses and sizes, such as daily necessities, packaging boxes, models, etc. Blow molding is mainly used to produce hollow containers, such as bottles, cans, boxes, etc. At the same time, blow molding can also produce difficult and high-precision special products such as stroller tires and artificial blood vessels.
1. Characteristics of thermoformed products:
The shapes of thermoformed products can be diverse. They are generally used to produce container products with a relatively large depth, height, diameter and wall thickness of the formed groove. They have excellent impact resistance, chemical corrosion resistance, high temperature resistance, and low temperature resistance. They can also be produced into Decorations with rich colors and various patterns.
2. Characteristics of blow molding products:
Blow molded products are mostly hollow cylindrical or elliptical, with thin walls, transparent, impact-resistant, and can withstand a certain amount of air pressure. Common products include plastic bottles, buckets, basins, etc. of various sizes.

Different Application
Thermoforming and blow molding also have very different practical applications. Since the products produced by vacuum forming are generally thin and light, they are suitable for the production and processing of some single-layer plastic products that do not have high quality requirements. Blow molding has great production advantages and can produce hollow and well-sealed plastic products on a large scale. Therefore, blow molding is suitable for some industries that have higher product quality requirements, such as food, medical, etc.
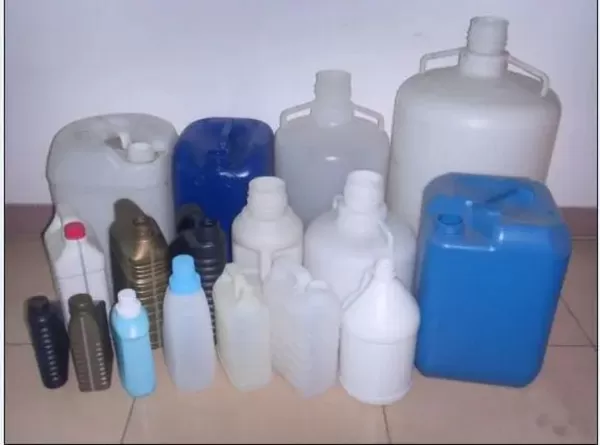
The Difference between Thermoforming Machine and Blow Molding Machine
Different Principles
Blow molding machines and vacuum pressure forming machines are both plastic processing equipment, but their working principles and final formed products are very different.
Thermoforming machine
The thermoforming machine is a device that places the heated plastic sheet in the mold, adsorbs it to the mold under the action of a suction fan, and takes it out after cooling and molding. Currently, common thermoforming machines include dual-station thermoforming machines and multi-station thermoforming machines, which are suitable for the production of plastic products of different sizes. Thermoforming machines produce plastic products at lower costs than blow molding machines, but the surface roughness is correspondingly higher.
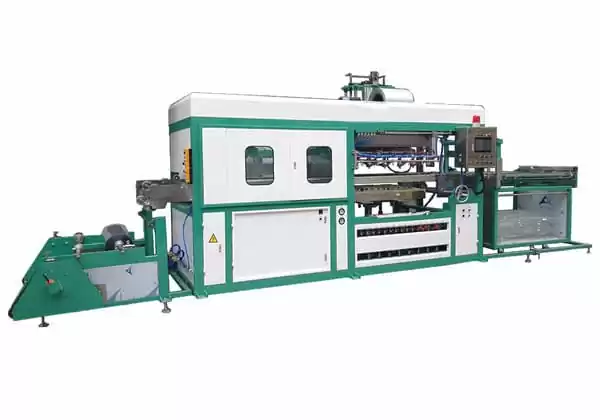
Blow molding machine
A blow molding machine is a device that blows molten plastic into shape through high-pressure airflow. It is mainly divided into two types: single-layer blow molding machine and multi-layer blow molding machine. Single-layer blow molding machines are suitable for producing simple plastic products, such as plastic bottles, food packaging bags, etc.; while multi-layer blow molding machines can produce more complex and advanced packaging materials, such as liquid packaging bags, bubble bags, etc. The plastic products produced by the blow molding machine have smooth surface, high transparency and good sealing performance.

Different Application
Due to the difference in molding processes between the two, blow molding machines and thermoforming machines each have their own advantages in making different products, so the appropriate equipment should be selected according to specific production needs. Blow molding machines are suitable for producing products with smaller volumes and higher sealing properties, such as food packaging bags, plastic bottles, etc.; while thermoforming machines are suitable for producing plastic products with slightly rough surfaces and larger volumes, such as electrical appliance casings and toys. , household items, etc.
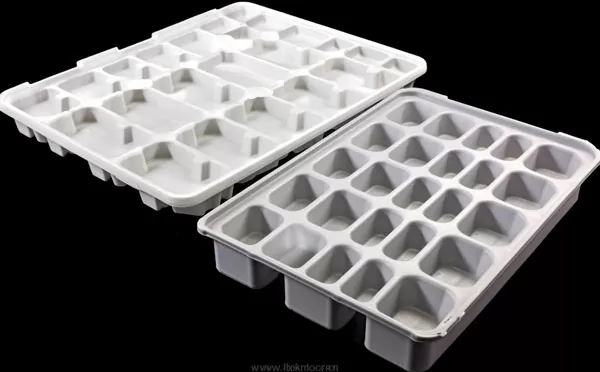
Precautions
When using blow molding machines and suction molding machines to produce plastic products, you need to pay attention to the following matters:
1. Ensure that the equipment is operating normally and check whether all parts are damaged. If any damage is found, replace it in time;
2. Operate the equipment according to the instructions, adjust air flow, temperature and other parameters to ensure product quality;
3. There are strict requirements for the use of plastic raw materials, and avoid using defective products or recycled plastics to avoid affecting product quality and service life;
4. Pay attention to the maintenance of the equipment, strengthen cleaning work, keep the equipment dry, and prevent excessive plastic moisture from affecting product quality.
In short, although blow molding machines and suction molding machines are both plastic processing equipment, they are different in production processes, product molding and applicable scenarios. Before use, it is necessary to select appropriate processing equipment according to product requirements and equipment characteristics, and operate and maintain it in accordance with the operating specifications carefully.
Conclusion
To sum up, thermoforming and blow molding are two different plastic molding technologies. They are very different in principles, processes, product forms and applications. Both molding technologies have their own pros and cons, and the appropriate technology needs to be selected based on the specific situation.
Although blow molding and thermoforming are both airflow molding processes, their characteristics and scope of application in practical applications are different. Therefore, when choosing to use blow molding or thermoforming technology, it needs to be decided based on actual production needs and product requirements.
In general, both blow molding and thermoforming have their unique advantages and application scenarios. I hope that the introduction in this article can help you better understand these two processes and make a more appropriate choice.