The field of plastic manufacturing offers a variety of methods for making products with plastics, such as injection molding, blow molding, 3D printing, extrusion, etc. Thermoforming is also a method: it is versatile, which means you can use thermoforming for many different things, cost-effectiveness, production efficiency, etc. thermoforming can be satisfied. But how does a designer or manufacturer know if thermoforming is the right production route for their product? Knowing what types of items are best for this process can help both parties achieve the desired results without any problems! So come with us to explore in depth what exactly these things are (products) and why type shapes work so well with thermoforming – all explained in detail right here!

Thermoforming Process
Thermoforming works by heating a plastic sheet until it is moldable, then adsorbing the heated sheet to a mold and then cooling it so that it retains the desired shape. Trim excess material after cooling is complete. There are two types of thermoforming; thin gauge thermoforming which includes items such as disposable cups/trays/lids, and heavy gauge thermoforming which is mainly used for car parts or durable goods like refrigerators.
Thermoforming offers several key advantages, including high production rates, lower tooling costs compared to injection molding, and the ability to manufacture large products with seamless detail.
To determine which products or shapes can be thermoformed, it is important to first grasp the manufacturing process and its types. There are three main kinds of vacuum forming process:

1. Vacuum forming: heated plastic sheets is pushed against a mold by vacuum pressure.
2. Pressure forming: like vacuum forming but with extra pressure applied to make the material fit tightly against the mold.
3. Twin-sheet forming: two sheets of plastic are formed individually then joined together (fused) so both sides show.
Each of these techniques has its unique strengths, and the choice among them is often dependent on the specific requirements of the part being manufactured.

Products Ideal for Thermoforming
Packaging Solutions
Thermoforming is often used for retail packaging. Typically consisting of blister packs, clamshell packs and trays, these packages securely hold items while allowing them to be clearly visible to shoppers. This type of packaging looks beautiful on the shelf or hanging behind a store window; in addition, it provides best-in-class product safety at a low unit price. In addition, manufacturers can design these containers with features such as stackability for efficient storage after production, and can rely on their designs to provide tamper-evident evidence – all factors that can be considered from both logistics and logistics perspectives Consumer perspective.
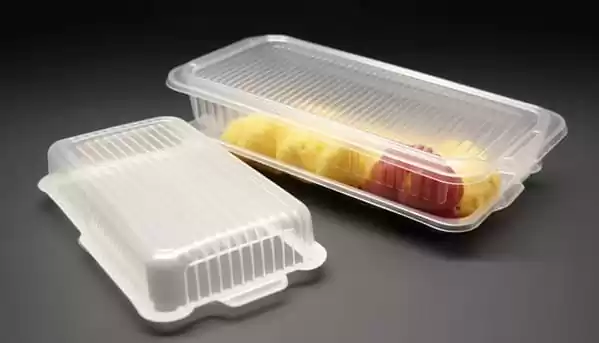
Automotive Components
The automotive industry often relies on thermoforming to manufacture a range of parts. Door panels, dashboards and interior trim are all ideally suited to this process, helping the industry achieve the twin goals of vehicle lightweighting while reducing costs. There’s an added benefit: Thermoformed parts can often incorporate multiple different functions into a single part (as per our previous example) which means they require less assembly once they arrive at the automaker.
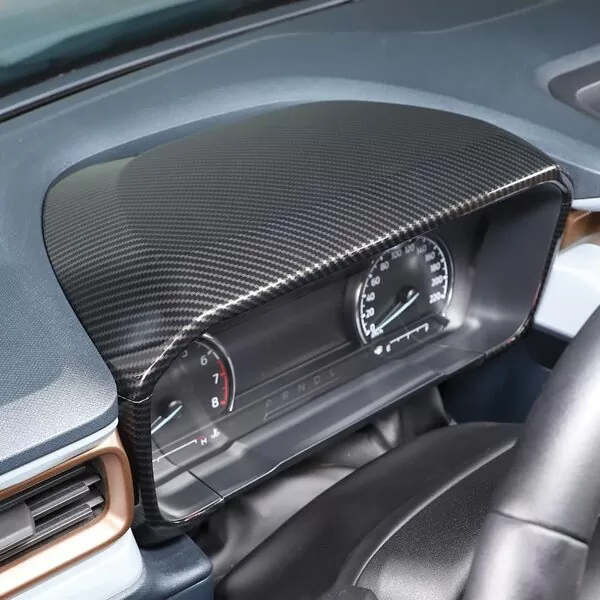
Medical Devices
The medical industry relies heavily on thermoforming to create sterile, disposable containers for medical devices. The strength and weight of these containers make them ideal for securely storing and transporting critical equipment, while being thin enough to reduce costs by improving fuel efficiency.
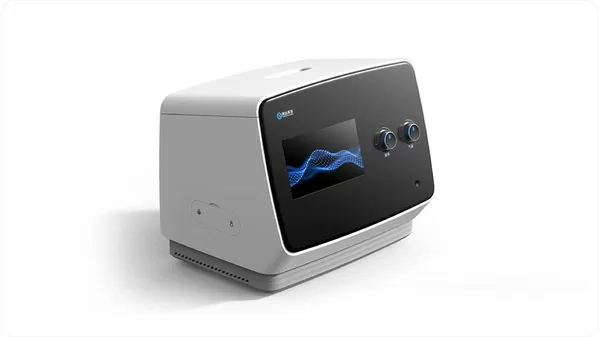
Consumer Goods
Thermoforming is a popular choice for manufacturing consumer goods such as point-of-purchase displays and electronic housings. This process enables the production of precise details and provides options for customization through coloring or branding techniques.
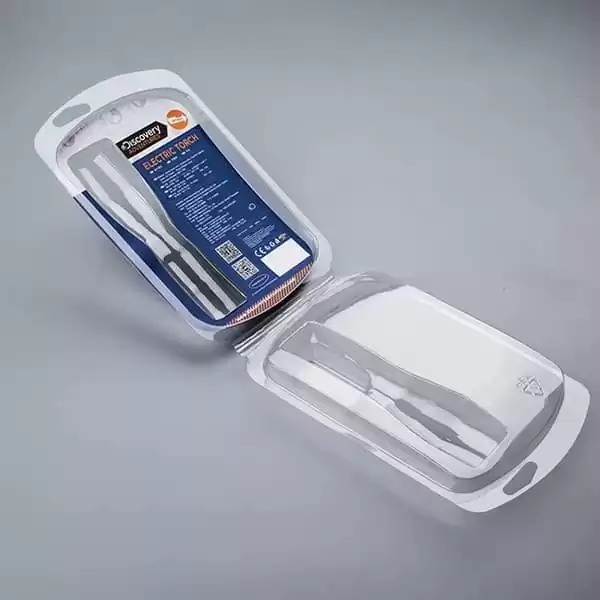
Aerospace and Defense
Thermoforming plays an important role in aerospace and defense industries by producing casings for delicate machinery, interior elements for planes, and multiple parts used in military applications. The ability to create big components with strong structural integrity is crucial here too!
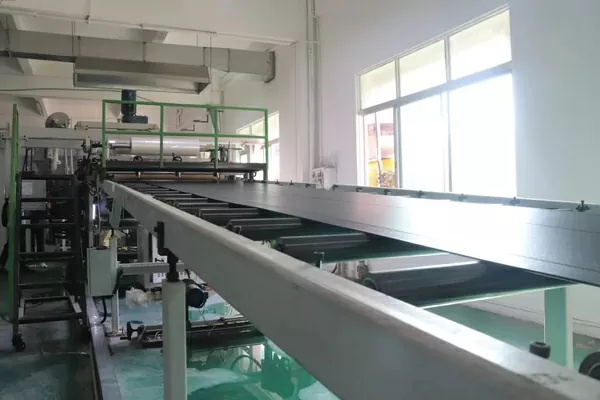
Shapes and Designs Well-Suited for Thermoforming
Complex Geometries
Thermoforming is ideal for manufacturing complex shapes and geometries that would be difficult or expensive using other techniques. Because vacuum forming molds a heated sheet of plastic onto a mold, detailed designs with undercuts can also be created.
Large Parts
Thermoforming is a good option for larger items that require strength and smoothness, such as aircraft parts or panels used in construction projects. When you use thermoforming to make large items, the individual parts have fewer places to join together; not only does this look better, but it also makes anything you make less likely to break because there aren’t as many weak points overall, This improves the aesthetics and durability of the final product.

Thin-Walled Designs
Thermoforming is particularly effective at producing thin-walled parts that are strong and durable, making it an excellent choice for electronic enclosures, display housings and similar items. Even though they are made from relatively fragile materials, thermoformed products are often tough enough to maintain their shape and function under a variety of stresses and environments.
Detailed Textures and Finishes
Designers are able to incorporate specific textures and finishes directly into the thermoforming mold itself, meaning products can be created with bespoke and intricate surface details such as leather textures, wood grains or logos, all of which help to enhance the overall attractive without any additional post-production work.
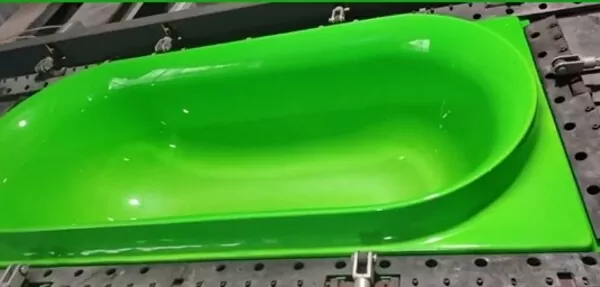
Product and Shape Considerations
Complexity of Design: Thermoforming is best suited for parts that are relatively shallow or have a uniform cross-section. This doesn’t discount more complex designs, but generally, the simpler the geometry, the more cost-effective the process.
Material Choice: The type of plastic material used in thermoforming can greatly influence the types of products and shapes that are feasible. Different plastic materials have varying degrees of flexibility, heat tolerance, excellent chemical resistance and other important properties.
Size of the Part: Typically, the larger the part, the better it is suited for thermoforming. The process can be incredibly efficient for creating large, light-weight products.
Product Volume: While thermoforming can handle both small and large production volumes, it excels in the medium to high production range — often over 1000 annually.

Undercuts and Draft Angles: Undercuts and sharp angles can make the part more challenging to form. By adding draft angles and considering the placement of undercuts, parts become more thermoforming-friendly.
Surface Finish Requirements: Thermoforming can produce parts with a range of surface finishes. If high gloss or textured finishes are required, consider the tooling and processes that can achieve this.
Factors Influencing Suitability for Thermoforming
Several factors must be considered when evaluating the suitability of products for thermoforming, including:
Material Type
Material selection plays a vital role in the thermoforming production process. Commonly used materials are ABS (acrylonitrile butadiene styrene), polystyrene, HDPE (high density polyethylene) and PETG (ethylene glycol-modified polyethylene terephthalate) and other materials or high temperature grade material, foamed or rigid plastic, each of them has different properties from each other and different uses.
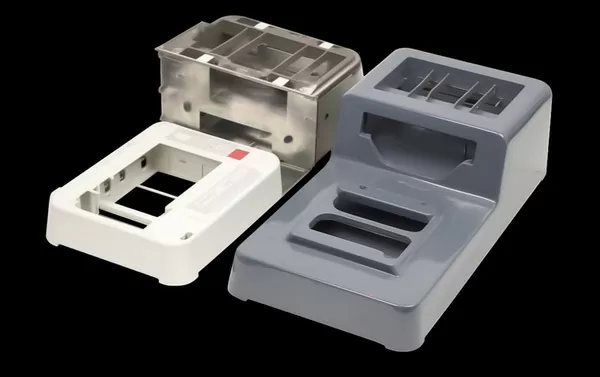
Design Considerations
Optimization of the thermoforming process is inherently related to design specifications. Factors such as draft angle (making it easier to release the mold), wall thickness (necessary for optimal strength/flexibility ratio), and undercut (allowing for greater shape complexity) all play a role in determining the final result.
Cost Implications
Thermoforming is a cost-effective method of high-volume production. But be sure to compare the cost with other manufacturing methods – just to confirm that thermoforming will always be the cheapest for your particular project.
Real-World Applications and Case Studies
To show what thermoforming can accomplish in action, let’s take a look at how it’s used in various fields. In each case, we will explain why thermoforming was chosen over other methods and outline the advantages that this technology brings.

Consumer Electronics
Thermoforming has become an integral part of the consumer electronics industry due to its ability to produce inexpensive, durable housings to protect delicate electronic components. Whether it’s a phone case, laptop sleeve or tablet stand, many of these products are affordable not only because they’re made that way, but they also fulfill a need to look good!
Point-of-Purchase Displays
Thermoforming is particularly suitable for producing unique designs and products that require a good surface finish, which is why it is ideal for product display displays. Help your product close the sale by presenting it effectively; thermoforming can do it better than almost any other manufacturing technology!
Aircraft Interiors
Thermoforming has become attractive for the aircraft industry to produce interior parts due to its lightweight properties and ability to shape objects, allowing it to be integrated seamlessly into cabin designs. This combination means greater comfort for those on board, while fuel efficiency is also improved.
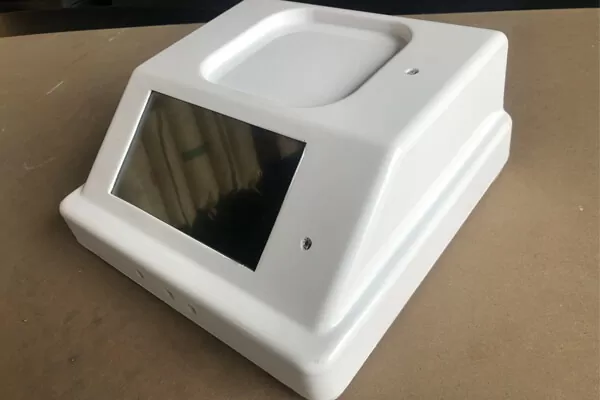
Bumper
In the automotive industry, a popular model-specific modification involves creating a new bumper design that meets three key criteria: consistent with the appearance of the entire range, complying with strict safety rules, and not raising the price. Thermoforming is capable of producing complex bumper shapes that include built-in technical elements, such as indicator lights or fog lights, and can therefore meet all these design needs as well as functional requirements.
Food Packaging
Food containers manufacturers are looking for a creative and cost-effective way to package their new ready-to-eat meals. Not only does thermoformed packaging keep products looking great on store shelves longer, it also reduces the amount of waste produced per product, and it also allows them to be packaged faster!
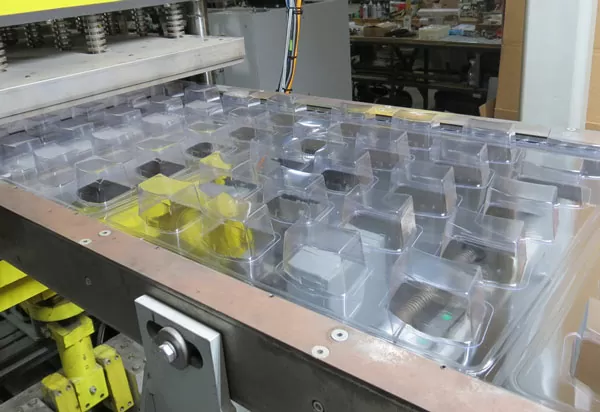
Conclusion
Thermoforming is a versatile, valuable process that offers unique advantages in the production of various products and shapes. By understanding the nuances of what works well with pressure forming, designers and manufacturers can harness the full potential of this manufacturing technique.
Thermoforming is a proven and reliable manufacturing technology that can be used to create many different shapes and objects. By understanding how the process works and what is required to work correctly, manufacturers can make an informed decision about whether thermoforming is the right choice for their specific needs.
While thermoforming may not be suitable for every occasion, it does excel when making products that require custom shapes, larger sizes, and don’t have to be made to ultra-tight tolerances. Due to its cost-effectiveness and versatility, there is no doubt that this process will continue to play an important role in our product development moving forward.
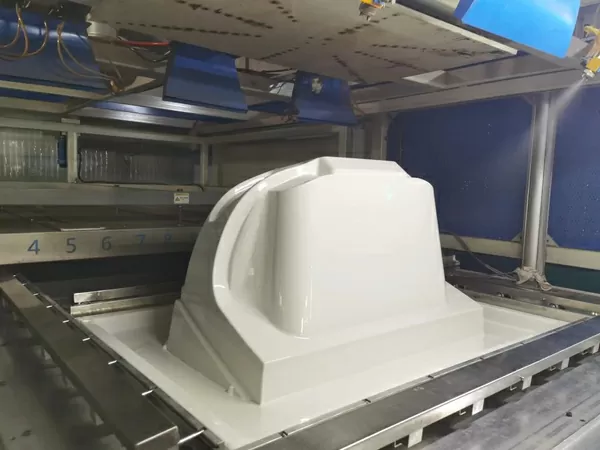
For businesses considering thermoforming, it’s critical to work with experienced manufacturers and thermoformers who can guide the entire process from design to production. With the right approach and collaboration, thermoforming can bring new possibilities to product design and manufacturing.