Thermoforming technology is plastic sheet (plate) thermoforming processing technology. It is one of the plastic secondary processing industrial technologies. The main principle is to heated sheet to soften it and then use vacuum to adsorb it to the surface of the mold formed after cooling, widely used in plastic packaging, lighting, advertising, decoration and other industries. Thermoforming can be divided into male mold and female mold according to the different contact surfaces between the molding material and the mold.
Ⅰ. Positive Mold and Negative Mold
Positive mold thermoforming and negative mold thermoforming are both plastic processing methods, which are a method of using thermoplastic plastics to form products through a vacuum forming process. The characteristic of female mold thermoforming is that the bottom of the mold is concave, and the workpiece is heated and softened above the mold and then adsorbed to the bottom of the mold to form the product. In the male mold thermoforming, the bottom of the mold protrudes, and the workpiece is heated and softened below the mold and then adsorbed above the mold to form the product.
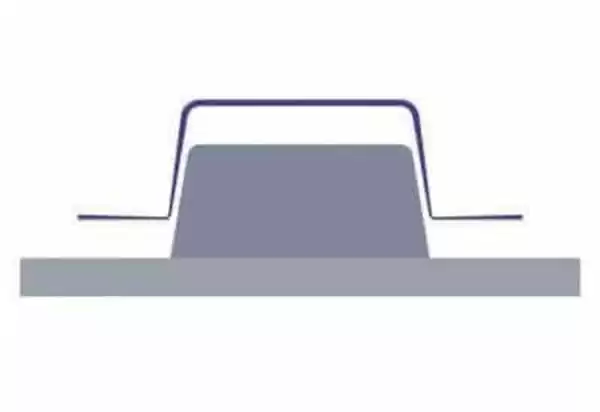
Negative mold thermoforming is to place a hot soft plastic sheet in the mold, then apply negative pressure (pull it outward) to make it close to the surface of the mold, and heat and soften it before forming. Positive mold thermoforming places a hot soft plastic sheets outside the mold, and then applies positive pressure (that is, inward pressure) to allow it to swell into the mold and form.
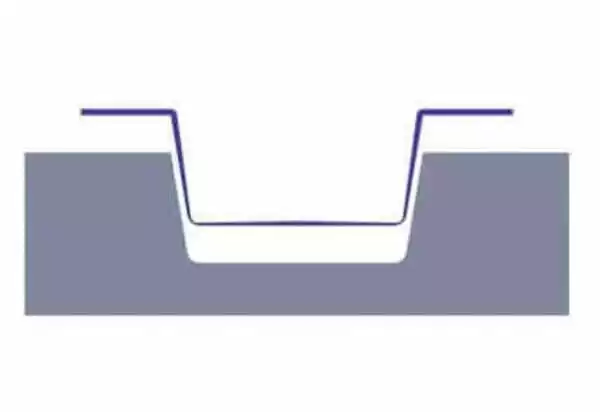
Positive and negative forming for vacuum forming, only one side of the heated material is in contact with the forming tool. In this way, the surface where the material meets the mold has exactly the same sheet surface profile as the forming mold. The contour and size of the non-contact surface of the molded part only depends on the thickness of the material.
Ⅱ. Thermoforming Process
Positice Mold Thermoforming Process
The positivee mold thermoforming process is more advantageous for manufacturing products with larger wall thickness and depth. The main features of the product are: like the vacuum female molding method, the side of the mold cavity wall that fits is of higher quality and has a more distinct and detailed structure. The largest part of the wall thickness is at the top of the positive mold, while the thinnest part is at the junction between the side and the bottom of the positive model. This part is also the last part to be formed.
Drawing and cooling stripes often appear on the side of the product. The reason for the stripes is the sheet material. There is a sequence when each part fits the mold surface. The part that is in contact with the mold surface first is cooled by the mold first, and in the subsequent related processes, its drafting behavior is weaker than that of the uncooled part. This streak is usually highest on the sides near the top of the mold face.
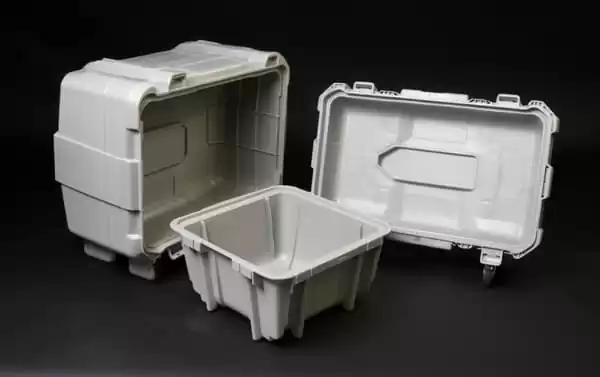
Negative Mold Thermoforming Process
The side of the product produced by the vacuum negative molding method that fits the mold cavity wall is of higher quality, and the structure is more distinct and detailed. The largest part of the wall thickness is at the bottom of the mold cavity, and the thinnest part is at the junction of the side and bottom of the mold cavity, and As the depth of the mold cavity increases, the wall at the bottom corner of the product becomes thinner. Therefore, the vacuum negative molding method is not suitable for producing products with a large depth.
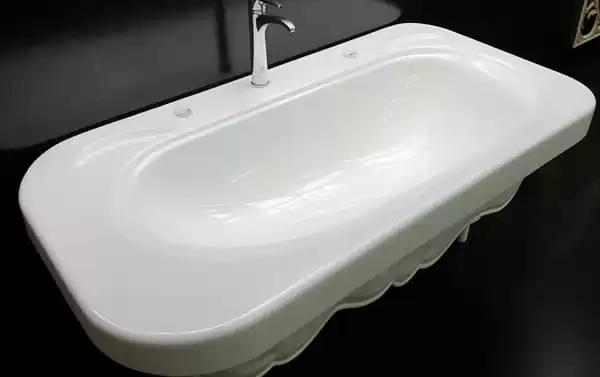
For positive molding, the inner dimensions of the part are very accurate because it is the side that interfaces with the vacuum thermoforming tool. In contrast, with negative molding, the outer dimensions of the product are very precise because the outside is in contact with the vacuum thermoforming mold.
Ⅲ. Advantages and Disadvantages of Positive and Negative Mold
Positive Mold Thermoforming
Advantages:
1. The product has a smooth surface and good quality.
2. The mold investment cost is low and the service life is long.
3. The molding cycle is short and the adaptability is strong.
Disadvantages:
1. The molding accuracy is low and is only suitable for manufacturing simple geometric shapes.
2. Unable to manufacture larger size workpieces.
3. The surface quality is relatively poor. Since the pattern is premade, the pattern effect will be lost during the stretching process of the skin. Where the amount of stretching is large, the pattern will become very shallow or even disappear.
4. There are restrictions on the R angle of the parts.
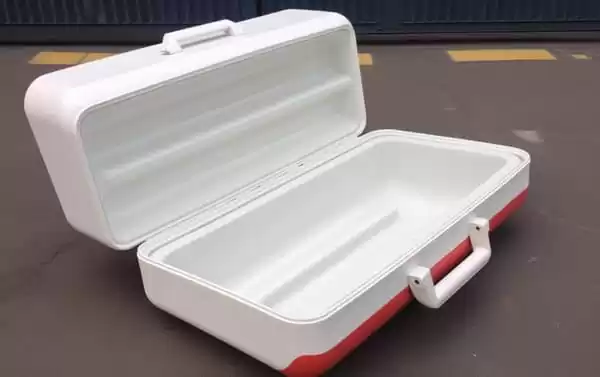
Negative Mold Thermoforming
Advantages:
1. The molding precision is high and more detailed and complex workpieces can be manufactured.
2. Larger size workpieces can be manufactured.
3. Mold production and use costs are low.
4. The surface is smooth and the surface pattern effect is relatively good
5. High production efficiency and reduced reprocessing costs.
Disadvantages:
1. The plastic material utilization rate is low.
2. There may be problems with the surface quality of the product.
3. Mold investment costs and equipment requirements are high.
4. The molding cycle is long and the molding cost is high.
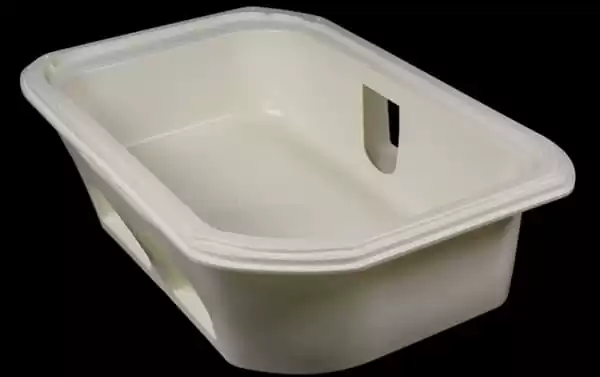
Ⅳ. Attention Should be Paid to the Production Process
Positive Mold Thermoforming
1. When using high angle molds for processing, especially when the distance between the mold and the clamping frame is large, wrinkles are likely to occur.
2. Cooling strips are easily produced at corners.
3. Uneven wall thickness at the flange.
4. It is difficult to demould due to insufficient slope of the side wall.
5. A small gap will occur between the insert and the lower holder of the multi-cavity mold in the molding area (clamping mold frame).
6. Positive mold forming molds are usually cheaper than female molds.
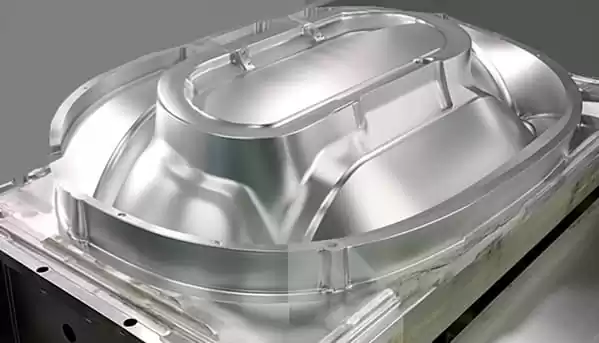
Negative Mold Thermforoming
1. Thick edges.
2. Uniform edge thickness.
3. Thin corners.
4. The single female mold has good demoulding properties.
5. Female molds are usually more expensive than male molds.
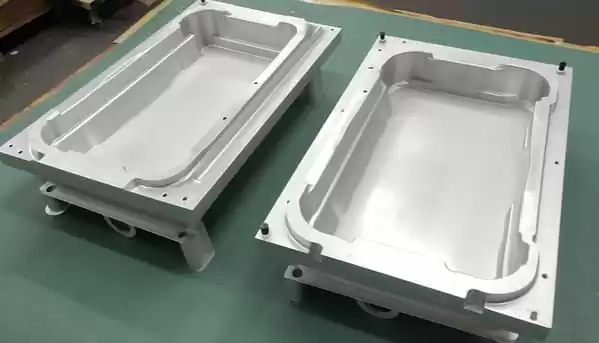
Ⅴ. Application
Thermoforming negative and positive molds are widely used in color TVs, automobiles, electrical appliances, communications, aerospace, medical equipment, toys, sporting goods and other fields. Common thermoformed products include automobile body parts, remote control casings, medical braces, aircraft models, etc.
Negative molds vacuum forming is usually used to produce products with convex and concave surfaces, complex shapes, and precise dimensions, such as automotive interior parts, medical equipment, electronic product casings, etc., and is suitable for mass production.
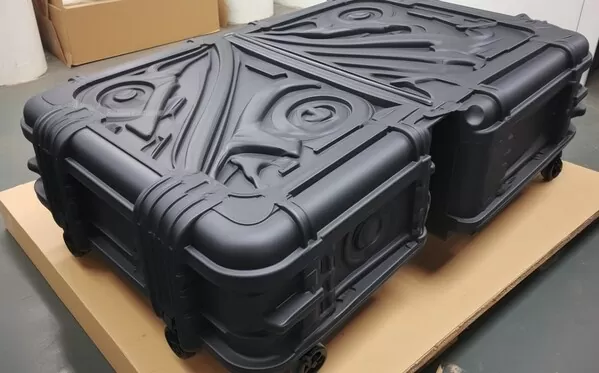
Positive mold thermoforming is suitable for producing flat and simple curved products, such as daily necessities, toys, display items, etc., and is suitable for small batch production.
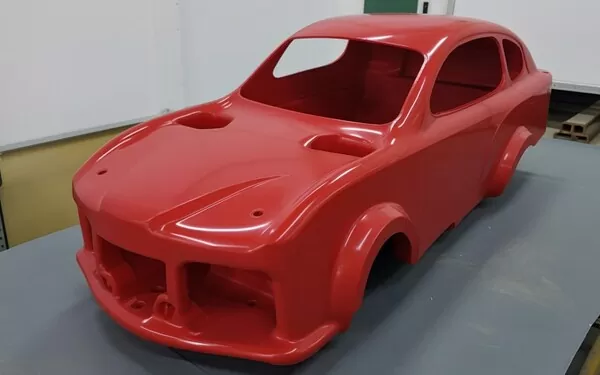
Ⅵ. How to Choose Positive or Negative Mold
The choice of negative mold thermoforming or positive mold thermoforming depends on production needs. If complex workpieces or larger-sized workpieces need to be manufactured, negative mold thermoforming is more suitable. If you need to produce simple geometric shapes or products that require high surface quality, or require high production efficiency, then positive mold thermoforming is more suitable.
Generally speaking, both negative mold thermoforming and positive mold thermoforming have their own advantages and disadvantages. Choosing different processing methods under different circumstances can better meet production needs.
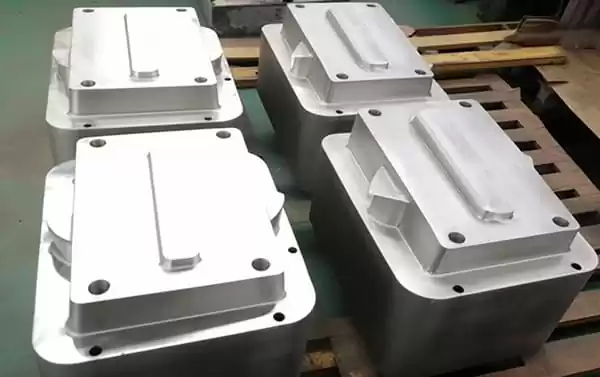
Ⅶ. Thermoforming Mold Materials
Plaster Molds and Glue Molds
The plaster mold is mainly made of yellow thermoformed hand plaster gypsum powder. If there is a drawing, the gypsum material will be made into a mold according to the data on the drawing and relevant requirements, if there is a physical object, the outline of the mold must be completed according to the actual object. First use handmade clay to make it, and then use vacuum forming to make a vacuum cover. Then there is a plaster mold, and then it is slightly trimmed.
This process only takes 2-4 days to complete, the comparison of making plaster molds It is easy, takes less time, is convenient to modify the product packaging, and its price is not high, but it does not take long to use, and after a period of time, it is easy to damage, and its transparency is not good, so it is mainly Used for products with low transparency requirements or first board confirmation.
The rubber mold is generally based on the design requirements of the product. After the plaster mold is made, a vacuum cover is produced from the plaster mold, and then high-temperature resistant resin material is injected into the vacuum cover.
After the mold is dry, holes can be drilled and polished. It takes a total of 3-5 days to complete, the price of resin molds is higher than other molds, but its use effect is similar to that of copper molds. It takes a long time to use, and some copper molds and plaster molds cannot be processed. Technical problems can be solved, so it is mainly used in electronics, food, toys and other products.
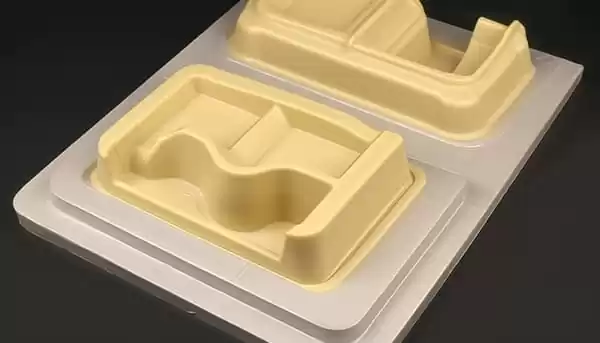
Knife Mold and Punching Mold
Mainly used in punching and drilling (airplane holes, round holes and butterfly holes).
Electroplated Copper Mold
The appearance and transparency of products produced with electroplated copper molds are relatively good, and their prices are not high and they are widely used. This is the first choice mold in general. It is used in products with higher requirements, such as electronics, stationery, toys, etc.
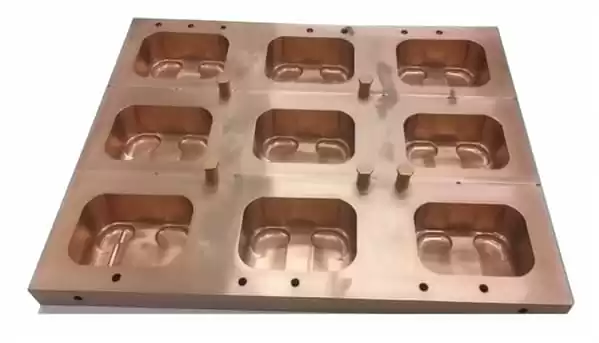
Bakelite Mold
The production of various bakelite molds is completed with imported heating materials, high-quality copper nails and Japanese high-temperature tape. Its characteristics include uniform heating and good sealing effect. It can be used in various disc machines and fully automatic chains. Machines and tractors made in Taiwan, it is mainly used in heat-sealing packaging of paper cards and bubble shells.
Aluminum Alloy Mold
According to the drawings or templates you have, input the data into the computer and let the computer lathe complete it automatically. Then you will complete the other holes manually and polish the mold smooth. The mold is ready for use. It will take 5-7 days. time. It is widely used in products with high requirements on appearance and size, such as electronics, toys, medicine, etc.
In fact, alloy aluminum mold is the first choice mold for the production of many high-demand air pressure forming products. For plaster molds and copper molds, glue The mold lasts longer, the production efficiency is not low, and it can save time and electricity, which are its advantages.
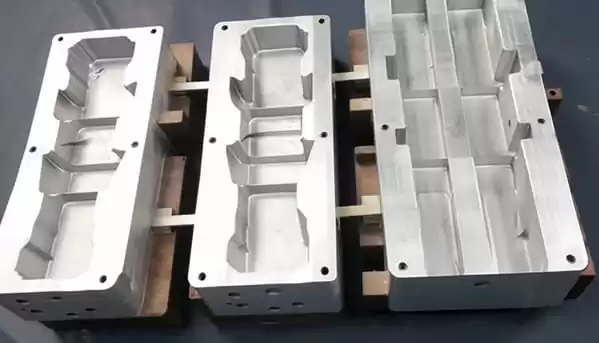
Heat Sealing Mold
Use high-quality copper or alloy aluminum to make heat-sealing molds, which mainly solve the problem of difficult sealing of PET with high-frequency heat. Its surface is treated with Teflon, which is also suitable for PET molding, the pattern on the pressed edge can be engraved by computer, with clear lines and uniform size, and various patterns can be customized according to user needs .
High Frequency Mold
The materials of the high-frequency mold have high-quality crimping lines, cutters, and very smooth cutting edges without any burrs or tearing edges. The pattern of the pressed edge is also engraved by computer. Its texture is also very clear and the size is uniform. It is also customized according to the user.
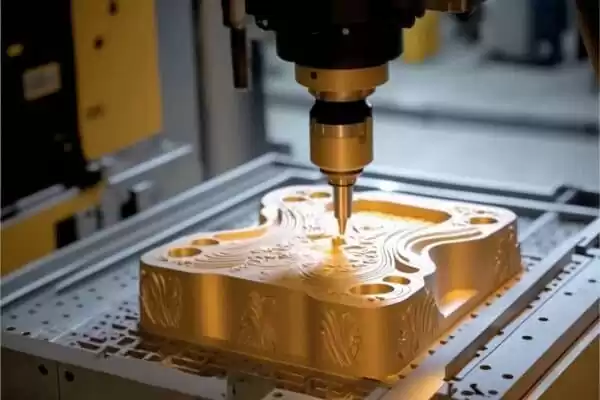
Concusion
The characteristics of thermoformed materials include strong three-dimensional effect and long-lasting green and environmentally friendly effect. With the rapid economic development around the world, thermoforming mold technology has diversified products and lower production costs. At the same time, thermoforming packaging technology is also relatively simple, so the demand in the market will be very strong in the future. In the manufacturing process, vacuum forming is employed in conjunction with medium density fiberboard to create durable and precisely shaped products. There will be more and more products manufactured by injection molding and vacuum forming molds in the future, and the scope of applications will be broader. Its future development will be better and better.