Introduction
Vacuum forming is a manufacturing process in which a heated plastic sheet is exposed to vacuum pressure, causing it to form around molds. This technique has become widely utilized across numerous products ranging from food packaging to automotive components; understanding this method and its applications is therefore integral for those working within manufacturing industries.
We will cover the use and benefits of vacuum forming in this article, such as its materials used, applications of vacuum formed products, common issues that arise while performing this manufacturing process and how they should be addressed, DIY vacuum forming machines as well as tips for creating your machine are also discussed in-depth.
Vacuum forming is an invaluable manufacturing process that provides excellent results at relatively low costs. Understanding its principles will enable you to take full advantage of this manufacturing technology.
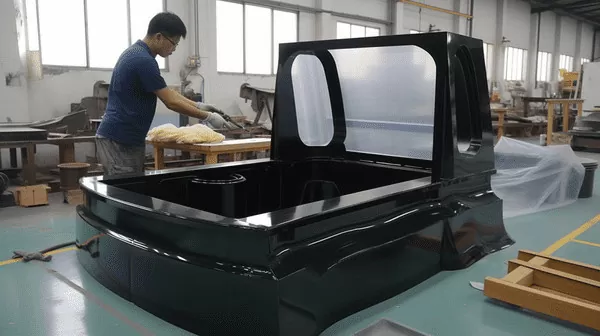
II. The Vacuum Forming Process:
Vacuum forming involves heating a plastic sheet until it becomes flexible, then using a vacuum to draw it into a mold made of wood, aluminum, or steel. Once in position, an additional vacuum application forces it into its desired shape while conforming to its form.
Vacuum forming can be broken down into several steps:
Heating the Plastic Sheet:
When heated, plastic sheets become malleable and easy to work with. This process makes molding possible.
Placement of a Plastic Sheet Over the Mold:
Once heated, a heated plastic sheet should be carefully laid over the mold, while simultaneously applying vacuum pressure.
Drawing the Plastic Sheet into the Mold:
Once the vacuum is applied, plastic sheets begin to move into their molds and assume their desired shapes.
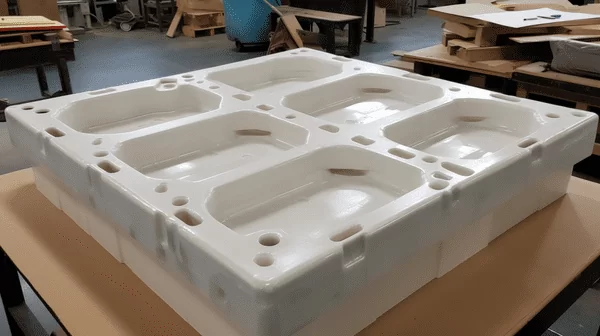
Cooling and Ejecting the Formed Product:
Once the plastic sheet has taken the form of its mold, it must be allowed to cool before being released from it and expelled from its holdings.
The vacuum-forming process can be used to produce an array of products, such as packaging, automotive parts, and consumer items. It is an efficient manufacturing method with minimal waste production that produces superior results with little waste generated during its use.
Vacuum Forming Machines
A vacuum forming plastic made machine consists of several key components that work in unison to produce plastic formed products. These components include:
Heating Element:
Heating elements are used to heat plastic sheets to their forming temperatures. Heating elements may be constructed of ceramic or quartz material.
Mold:
In some industrial vacuum forming machines, molds are used to shape the plastic sheet during its transformation. They may be constructed out of various materials including wood, aluminum, and steel.

Frame:
The frame serves to secure and support the vacuum forming machine, holding in place its mold while providing support for vacuum forming operations.
Vacuum System:
The vacuum system creates an airtight seal between plastic sheeting and molds, forcing them to conform more closely. It does this employing vacuum pressure being created between them – this causes them to adapt perfectly!
Cooling System:
The cooling system serves to quickly chill any plastic product that has been formed from its mold after removal from it.
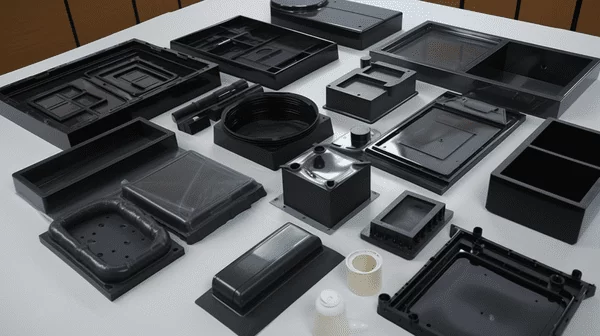
Control System:
The control system serves to regulate both heating elements and vacuum systems to ensure the plastic sheet is heated at an appropriate temperature and the vacuum is applied at an optimal time.
Material Roll Holder:
This component holds and feeds plastic sheet rolls through to the machine.
By regularly maintaining and operating their vacuum forming machine’s components, manufacturers can ensure high-quality results and prolonged machine lifespan.
The Role of Temperature and Pressure in Vacuum Forming
Temperature and pressure play an integral part in the vacuum forming material and processes. Plastic sheets must first be heated to an exact temperature before being formed into molds; then vacuum pressure must be applied at precisely the right moment to produce high-quality formed products.

Heating Temperature:
When heat treating plastic sheets before placing them over molds, its ideal heating temperature depends on both its material type and thickness. In general, though, temperatures high enough to make molding easy should also be high enough not to burn or melt them completely. The ideal heating temperature varies based on type and thickness.
Pressure:
Proper application of pressure during vacuum forming is crucial to producing quality-formed products. Vacuum pressure must be applied at just the right moment when drawing plastic sheets into molds to ensure that they conform perfectly. The too-early application could result in deformed or defective products being produced.
Vacuum forming’s success relies on the perfect balance between heating temperature and vacuum pressure, leading to high-quality products with consistent quality and minimal waste. When managed effectively, temperature and pressure controls can result in high-quality vacuum formed parts products with consistent quality while simultaneously minimizing waste.
Types of materials used in vacuum forming
Vacuum forming can utilize a wide variety of materials, such as thermoplastics, composites and synthetic materials. Common materials for vacuum forming include:
Acrylonitrile butadiene styrene (ABS):
ABS plastic is lightweight, impact-resistant material widely used by the automotive industry for interior and exterior trim components.
Polyethylene (PE):
PE is an easy to recycle thermoplastic that’s often found in food packaging or consumer products.
Polycarbonate (PC):
PC is an impact-resistant plastic used widely across both automotive and electronics industries to produce lenses and covers for application such as covers.
Polypropylene (PP):
Polypropylene is a lightweight, flexible, and durable plastic that’s frequently used for food packaging and other consumer products.
Polyvinyl chloride (PVC):
PVC is a plastic material commonly found in construction applications like pipes, siding and other building components.
Material selection depends on several considerations, such as its intended use for the formed product, desired appearance and finish preferences and manufacturing costs. Different materials require various heating temperatures and vacuum pressure settings; it’s therefore vitally important to select an appropriate material for any given application.
III. Benefits of Vacuum Forming
Vacuum forming is an extremely useful manufacturing technique with several benefits, such as:
Vacuum forming is an economical manufacturing method, using relatively basic equipment to quickly produce large volumes of products quickly and efficiently. Furthermore, it’s flexible enough to meet fluctuating customer demands.
Customizability options: Vacuum forming manufacturers to produce products with unique shapes, sizes, and finishes for specific applications – an advantage over other forms of manufacturing processes. This makes vacuum forming an excellent option.
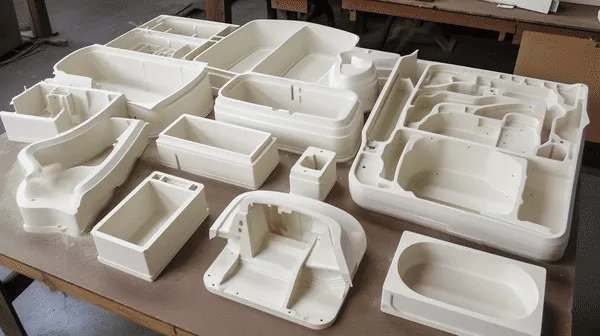
Vacuum forming provides high-quality finishes suitable for many different applications. By choosing the appropriate material and mold design, manufacturers can produce products with durable yet visually appealing surfaces such as smooth, textured or patterned surfaces that stand up against wear-and-tear over time.
Vacuum forming can accommodate both small and large production runs, making it an ideal solution for manufacturers who require the production of multiple products at once. Furthermore, it’s highly flexible; manufacturers can increase or decrease production runs according to need.
Vacuum forming has many advantages that make it an attractive option for manufacturers looking to produce customized, high-quality products quickly and cost-effectively.
IV. Applications of Vacuum Forming
Vacuum forming is an innovative manufacturing technique used in numerous industries and applications. Common vacuum forming applications include:
Automotive Industry:
Vacuum forming is widely utilized by the automotive industry for creating interior and exterior components like instrument panels, door panels and body panels. The cost-effective process enables production of complex shapes with intricate designs.
Vacuum Forming Food Packaging:
Vacuum forming is an increasingly popular technique used to produce lightweight, durable, and visually appealing packaging solutions such as clamshell containers, trays and bowls for food packaging purposes.
Medical Supplies:
Vacuum forming can be used to create medical supplies such as instrument trays and packaging for sterile supplies, making the products suitable for use in healthcare settings. This process produces products which are both sterile and durable – ideal for any environment in the healthcare setting.
Garden Equipment:
Vacuum forming can be used to produce garden equipment like plant pots and seedling trays that are lightweight, durable and visually appealing – ideal for outdoor use. This process produces lightweight yet long-lasting products suitable for this outdoor setting.
Consumer Products:
Vacuum forming can be used to craft an array of consumer goods such as phone cases, toys and storage containers that are lightweight yet durable and customizable. This process provides products with lightweight yet customizable construction.
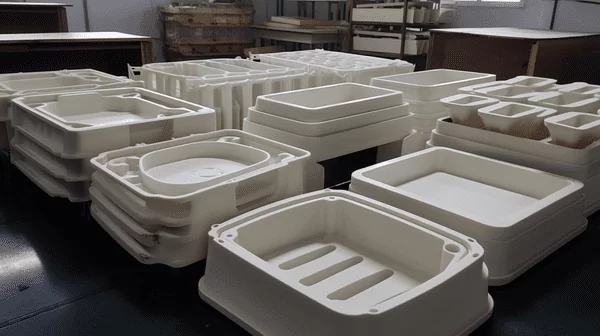
Vacuum forming’s versatility makes it the go-to method for manufacturers in multiple industries who need to create customized, high-quality products quickly and cost-effectively.
V. Comparison with Other Manufacturing Processes
As vacuum forming is an increasingly popular manufacturing technique, it is important to gain an understanding of its similarities to other processes. Some of the more popular comparisons of vacuum forming include:
Injection Molding:
Injection molding is a manufacturing process that uses injection of liquid plastic into molds in order to produce high-quality products with precise shapes and dimensions. Although injection molding produces superior results, it tends to be more expensive than vacuum forming due to more complex equipment requirements and time commitments involved.
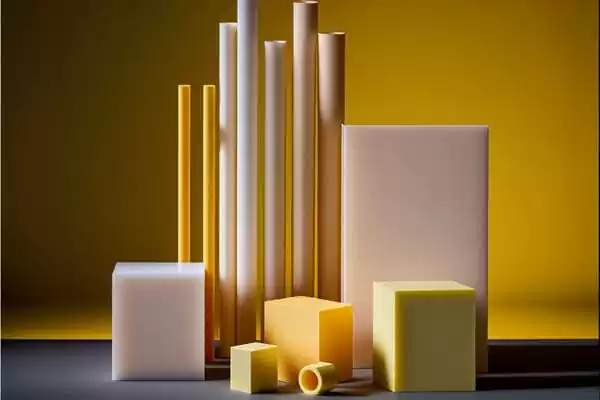
Structural Foam Molding:
Structural foam molding is a process in which an injecting agent foaming agent is added to molten plastic, producing products with both cellular cores and solid outer layers, creating products with strong yet lightweight qualities. Although structural foam molding produces superior products, this technique often costs more than vacuum forming and requires more complex equipment for production.
Thermoforming:
Similar to vacuum forming, thermoforming involves using heat to soften plastic sheet and pressure to form it into molds. It’s used for creating various products ranging from packaging and automotive components, with thermoforming often more costly and demanding more complicated equipment than its vacuum-forming counterpart.
General, vacuum forming is a cost-effective and flexible manufacturing method capable of producing high-quality products with minimal waste. While other processes may produce higher quality results, these usually require more complex equipment and are often more expensive – the decision as to which method will depend upon both manufacturer’s needs and desired end product specifications.
VI. Choosing the Right Vacuum Forming Method and Materials
When selecting a vacuum forming method and materials, there are numerous factors to keep in mind. Some of these include:
Size and complexity of product:
The size and complexity of your product will dictate which vacuum forming machine, mold type, and materials will best meet its production.
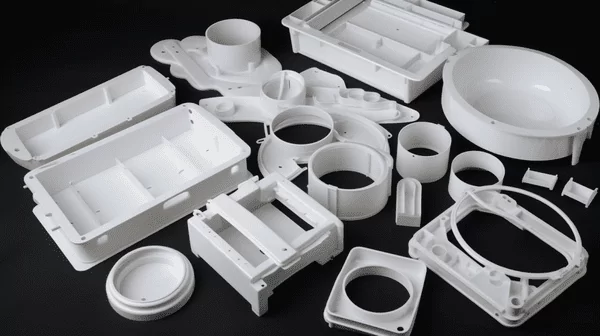
Thickness requirements:
Wall thickness requirements will dictate which plastic sheet and heating temperature will be necessary for vacuum forming processes.
Based on your desired finish and texture, a vacuum forming mold will need to be made accordingly, along with plastic sheet type and heating temperature requirements.
Mechanical Properties Needed for Vacuum Forming:
Based on your mechanical property needs – strength, durability, and impact resistance for example – this will determine which plastic sheet type you require for vacuum forming.
TIPS for Selecting Appropriate Materials:
When selecting materials for vacuum forming processes, it is crucial to take into account the unique specifications of the final product. Some tips for selecting suitable materials:
Consider Mechanical Properties:
Select a material with the required mechanical properties for your specific application.
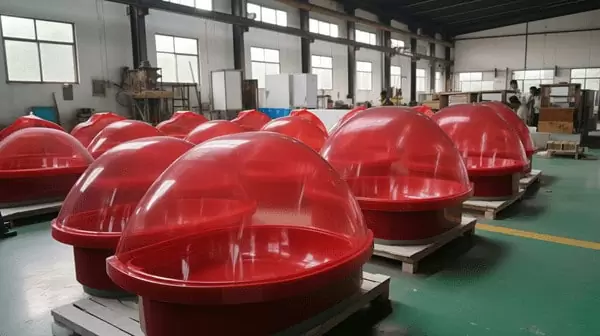
Consider Your Wall Thickness:
Select materials which can easily be formed to the necessary wall thickness.
Consider Finish and Texture Requirements:
Select materials which can create the desired finish and texture in your final product.
Consider cost:
Select materials that are cost-effective and suitable for the intended application.
By considering these factors and tips when selecting their vacuum forming tools, methods and materials, manufacturers can ensure high-quality products are produced that fulfill their unique requirements and needs.
VII. Common Vacuum Forming Issues and Solutions:
Though vacuum forming plastics can be an efficient and cost-cutting manufacturing method, it does present its own set of challenges. Some potential issues that might occur in this process may include:
Thin Walls:
When heated improperly, thin walls can result in products with weak walls that need repair. To combat this issue, manufacturers can adjust the heating temperature or choose thicker plastic sheets as an answer.
Uneven Heating:
Uneven heating can cause plastic sheets to warp or deform during vacuum forming processes, necessitating additional steps such as using an oven or heat lamps to ensure even heating. Manufacturers can prevent this issue by making use of heating ovens and heat lamps in their production process.
Warping:
Warping can occur when plastic sheets aren’t secured securely to their mold during vacuum forming, leading to uneven or distorted surfaces on a product produced. To address this issue, manufacturers can either use a vacuum pump or apply pressure on the plastic sheet so it conforms more closely to the shape of their pressure forming molds.
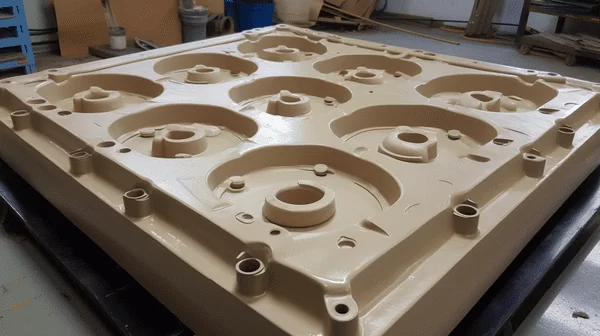
Excess Material:
Excess material can arise when plastic sheets are improperly trimmed following vacuum forming, leading to uneven or rough edges on their final product. To address this problem, manufacturers can utilize mechanical trim presses or other tools that trim off excess material such as scissors to do it for them.
By understanding these common vacuum-forming issues and their solutions, manufacturers can ensure high-quality products with minimum waste or defects.
Conclusion
Vacuum forming is an adaptable and cost-effective manufacturing process widely utilized across industries and applications. By understanding its process and selecting appropriate materials and equipment, vacuum forming allows manufacturers to produce high-quality products quickly and efficiently.
In this article, we discussed the benefits and applications of vacuum forming, including its cost-effectiveness, customization options, high-quality finishes, and suitability for both small and large production runs. Furthermore, we highlighted its significance when choosing an appropriate method and materials, along with tips for selecting materials suitable to the final product’s specific requirements.
As vacuum forming technology continues to advance, manufacturers can expect new developments in materials, equipment, and processes that further optimize its efficiency and effectiveness. By staying abreast of these advancements, they can maximize their advantages while remaining competitive within their industries.
Vacuum forming is a cost-effective manufacturing technique with numerous applications. By understanding its processes and selecting suitable materials and equipment, vacuum formers can produce high-quality products quickly and cost-effectively.