In addition to injection molding in the plastic molding industry, thermoforming is a cost-effective and versatile method for forming flat plastic sheets into different shapes, making it invaluable in plastic manufacturing. Currently, a variety of plastic materials dominate this field: polycarbonate (PC), acrylonitrile butadiene styrene (ABS), high molecular weight polyethylene (HMPWE), acrylic, polyethylene terephthalate (PET), polyethylene terephthalate glycol (PET-G), polyvinyl chloride (PVC), polypropylene (PP) etc. Each material has its own unique properties and applications. What are their differences in terms of thermoforming? In this article we focus on the differences in thermoforming between polycarbonate (PC) and acrylonitrile butadiene styrene (ABS).
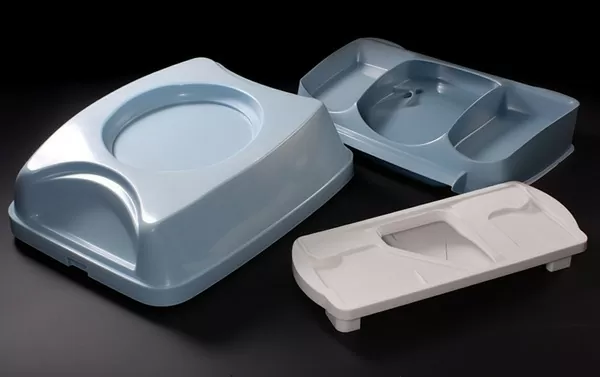
In the industrial sector, material selection is extremely important, and intensive manufacturing processes can have a huge impact on performance. This is especially true for thermoforming, both PC and ABS have unique qualities that make them excellent choices for pressure forming process applications; however, each substance also has some disadvantages, such as how these properties affect the finished product and its overall Durability. For anyone involved in making or designing items using one (or both) of these substances, it pays to understand exactly what makes them different from each other.
In this comprehensive breakdown article, we’ll explore the salient characteristics of PC and ABS in the context of thermoforming, revealing how these thermoplastics perform under the intense conditions of molding and molding. as well as these differences and how they affect the process itself; and which industries benefit most from the use of both substances.

Thermoforming Process
In order to better understand PC and ABS, it is important to first fully understand what thermoforming is all about. Thermoforming refers to a manufacturing process that involves taking a flat plate of thermoplastic material, heating it until it reaches a temperature suitable for molding to soften it, and then adsorbing it to a mold through vacuum or pressure and allowing it to cool and form into the desired shape. The process stands out for its speed, cost-effectiveness and ability to create shapes large and small, simple and complex, with special details.
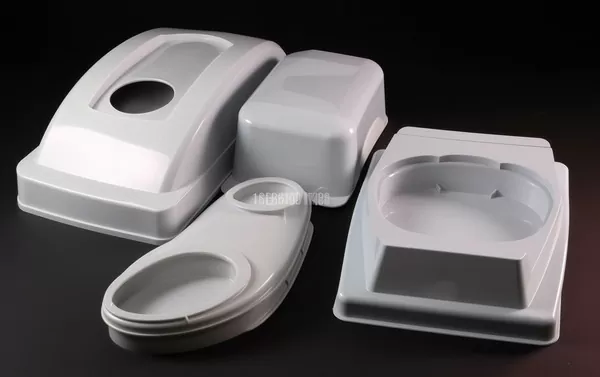
Exploring Polycarbonate (PC)
Polycarbonate is a durable, lightweight thermoplastic known for its excellent electrical properties and high impact resistance: Polycarbonate has it all.
Also belongs to the family of linear polymers; this transparent material not only provides transparency, but also has excellent dimensional stability – two qualities that make PC perfect for making items like lenses (which need to be transparent) and windows, because even with heavy objects They won’t break easily if hit!

Thermoforming Qualities of PC
In the field of thermoforming, PC has many desirable qualities: it is very easy to form when heated plastic sheet and is transparent. Once formed, it also maintains its appearance – even if that involves a lot of pressure or strain.
But there are downsides: PC’s high-temperature requirements and tendency to crystallize can create challenges during the molding process, making them tricky to use in the molding process because workers have to make sure each product cools at exactly the right rate – which requires skill.

The Allure of ABS
ABS is made up of three different polymers: acrylonitrile, butadiene, and styrene. This combination results in a material that is both tough and resistant to impact and heat resistance; these properties mean ABS can be used in many consumer products such as toys (such as Lego bricks), car parts and more.
ABS in the Thermoforming Ring
When ABS is heated, it has several advantages over PC in thermoforming. On the one hand, it can be formed at a lower temperature during processing, thus saving energy overall.
It is also highly resistant to chemical attack and scratching – two important factors for components that may be in contact with harsh materials along their entire length and still function properly after installation.
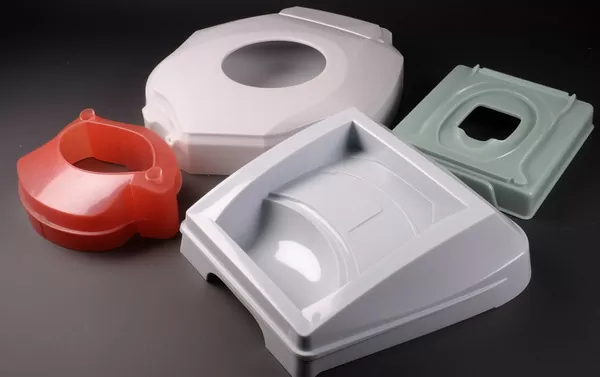
The Basic Composition
PC: Strength and Clarity
Polycarbonate (PC) is a versatile material with extremely high strength and excellent transparency. It is often chosen when shatter resistance or transparency are important features. PC can be used for many purposes: from riot shields to bullet-proof windows because it is so strong!
If you need something that looks good even in temperatures of 149°C, look no further than our old friend polycarbonate – it’s heat-resistant up to around 300°F (149°C) , there is nothing better than plastic.

ABS: Flexibility and Durability
Acrylonitrile butadiene styrene (ABS) is a thermoplastic that stands out because it is equally tough and flexible – thanks to its three monomers. The material can be easily formed and is resistant to a wide range of chemicals: properties that have long made ABS a favorite in the automotive parts, consumer goods, and craft industries.
It also performs well under pressure; in fact, it’s a tough sell when it comes to handling impacts and external pressure, meaning parts that are prone to rough handling can benefit from products made from ABS Very shallow.

Thermoforming Methodology
PC: The Transparency Champion
The thermoforming process benefits from the use of PC as it has impressive deep drawing capabilities, meaning it can stretch a lot without tearing. Being optically clear, it also provides good visibility during inspection.
However, these positives also bring some challenges: polycarbonate can cool quickly (which can sometimes be desirable), but also requires careful heating control to avoid deforming the object.

ABS: The Shapeshifter
ABS thermoforming is known for its excellent formability and stability, which means it can maintain sharp corners and complex structural designs during the molding process – ideal for creating parts with a large amount of detail.
Also, since ABS has a wider processing window than PC, you will often find thermoformed parts made from this material easier to work with.
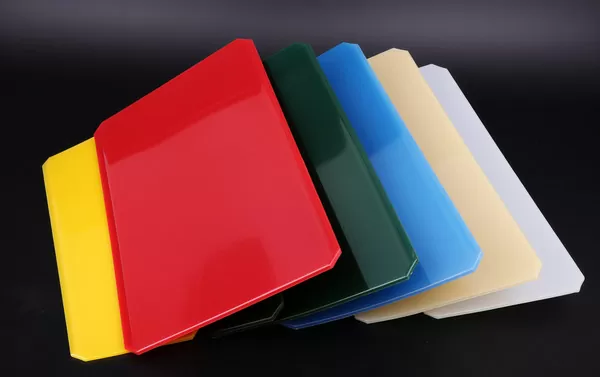
Considerations in Product Design
PC: Mechanical Precision
When manufacturing PC thermoformed products, engineers value accuracy and complexity above all else. This is because the material’s high strength-to-weight ratio and dimensional stability under load make it ideal for structural parts with tight tolerances. Corrosion and flame resistance also means it can also be used in safety equipment as well as harsh environment settings.

ABS: Aesthetic Appeal
ABS material is highly sought after by designers who want their products to look good as well as function. This is because this plastic can be polished very well or painted any color you like; there are also tons of surface finishes to choose from, including patterns, if that’s your thing! Additionally, ABS is not only able to withstand, but resist creep (deformation) when exposed to extreme heat/cold, making ABS an excellent housing for electronics and home appliances.

Industries Served by PC and ABS
PC: From Aerospace to Medical
PC’s superior performance means it can be used in industries that require transparent materials and very precise engineering. These include aerospace – particularly things like cockpit components and cabin interiors – as well as medical products (such as clear casings that can be sterilized) and even automotive parts with headlight lenses and reflective casings.
But the material doesn’t stop there, with applications spanning a variety of consumer products such as protective eyewear and DVD manufacturing.
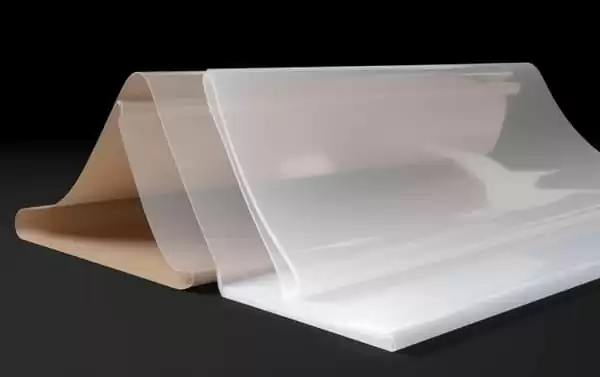
ABS: The Consumer’s Material
ABS is in high demand for a reason: it has all the qualities demanded by today’s consumer market. When you buy a home appliance, computer accessory, or consumer electronics kit, there’s a good chance that ABS will make it both strong and beautiful.
Car manufacturers also use ABS extensively – for trim (interior and exterior) and structural components, among others.

The Market and Material Costs
PC: Premium Material
PC generally costs more than ABS because it performs better in terms of impact resistance and light transmission. PC can do things ABS can’t do (which is sometimes very important). But if you don’t need those special abilities, then maybe ABS will do just fine and be cheaper.
ABS: A Cost-Effective Choice
ABS is widely used in various industries due to its combination of economical and physical properties. It can be found everywhere from consumer products like toys or phone cases, all the way to automotive parts, as it offers both high quality and low prices when large quantities of products are needed.
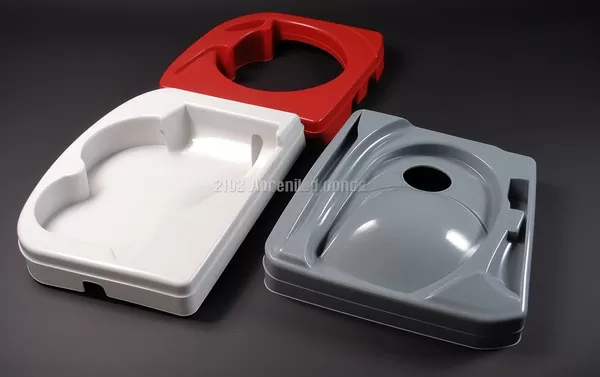
Environmental Considerations
PC: Recyclable But Complex
While polycarbonate (PC) can be recycled, it’s not as simple as recycling other plastics – it must first be separated from other plastics. This creates a problem for widespread PC recycling: It has such useful qualities that it often ends up in multi-layered plastics along with materials that cannot be recycled.
ABS: Versatile in Recycling
ABS is considered highly recyclable because it is widely used in products that can be easily sorted from other waste materials. The fact that ABS can also be recycled repeatedly and made into 3D printing feedstock suggests that a more circular model can be applied to this common plastic (at least for some uses), making them overall more environmentally friendly.
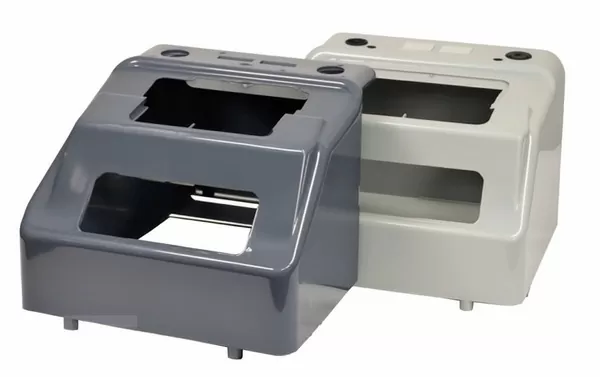
A Comparative Analysis
While both PC and ABS offer unique benefits, how do they compare to each other when considering the main factors that manufacturers care about?
Thermoforming Process: During the thermoforming process, PC requires a higher heat deflection temperature than ABS, about 300°C, while the ABS molding temperature is about 204-238°C. As a result, molding cycles for thermoplastic polymers may take longer, but the overall energy consumption per cycle may be lower because they use relatively little heat.
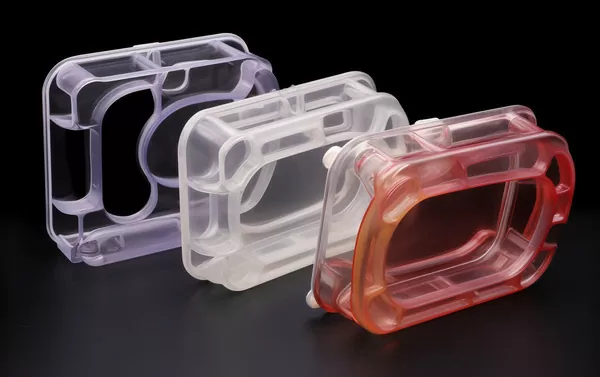
Impact Resistance: While standard ABS is not as impact-resistant as PC, there are options such as ABS/PC hybrids that combine the benefits of both materials.
Chemical Resistance: When it comes to environments exposed to chemicals; higher resistance levels mean that the PC will also perform better than a PC made solely from ABS, again.
Transparency: One of the advantages of PC over ABS is its optical clarity. Unlike ABS, which is known for being opaque, PC can be transparent.
Cost and Considerations: When it comes to price, ABS often wins, and it tends to be less expensive than PC. That’s why so many companies use it to make consumer products. That said, there are many situations where durability is more important than cost in the long run (like car parts or phone cases). In these cases, you may be able to find a PC, albeit at a higher upfront cost.
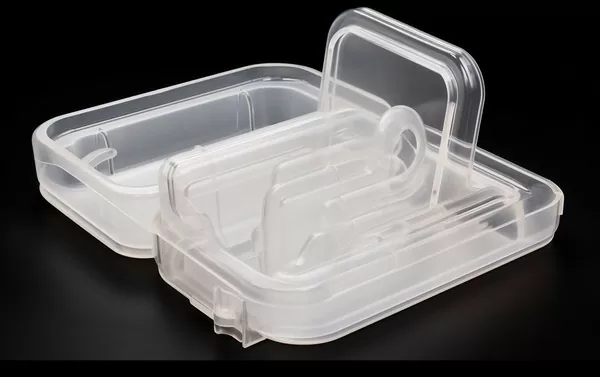
The Verdict: PC Versus ABS in Thermoforming
Choosing between PC and ABS ultimately comes down to the specific needs of your project. If transparency and electrical performance are particularly important (for example, for lampshades or medical devices), then PC may be the best choice, as it tends to outperform ABS in these two areas.
On the other hand, if you need a product that is both durable and easy to use, such as car trim or machine guards, then ABS may be ideal. It performs well, is wear-resistant, is easy to process (whether you need thick or thin plastic sheets) and is also suitable for many thermoforming techniques.
Manufacturers must weigh the benefits of each material against various factors, including cost, production volume, thick plastic sheets or thin plastic sheets, thin gauge thermoforming or heavy gauge thermoforming and end-use, to make an informed decision that maximizes efficiency and quality.
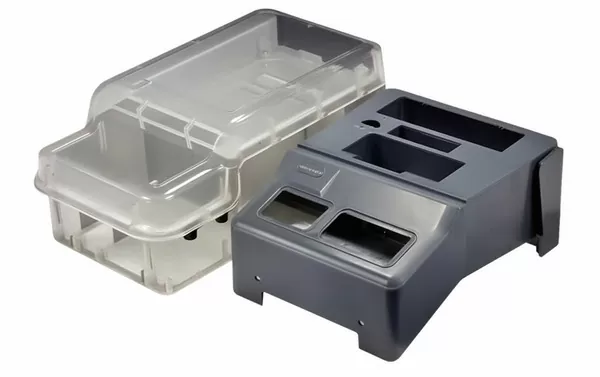
Considerations Beyond Thermoforming
After thermoforming, there are other important steps to consider. PC and ABS allow for operations such as CNC trimming, painting or assembly.
But it’s important to remember that these changes can have a large impact on product properties – enough to make them no longer suitable for certain purposes after use!
Conclusion
When it comes to thermoforming, two materials take center stage: PC and ABS. Each has its own unique qualities that make it ideal for certain jobs – but understanding these qualities will help ensure you get results from your molded parts that are both impressive and reliable.
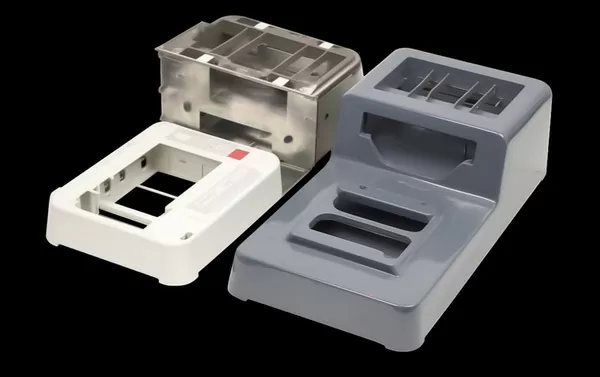
Deciding on either option isn’t always easy, as there can be some overlap in suitability based on factors such as how the item needs to look and whether the item can withstand heat or chemicals (or both!). Luckily, there are plenty of options out there, so customizing things exactly won’t be difficult either way. When you need to choose a thermoforming material, it helps to know how PC and ABS compare. Each has its own advantages, so they are often used in different industries or applications – sometimes alone.
In some cases, one simply needs to choose between polycarbonate (PC) or acrylonitrile butadiene styrene (ABS). PC has high transparency and impact resistance; if toughness and ease of molding are more important than transparency properties, choose ABS. Designers need to know there is logic behind their decisions, and choosing one over the other must be because it offers something unique that provides the look/function (or both) required when the project is completed.
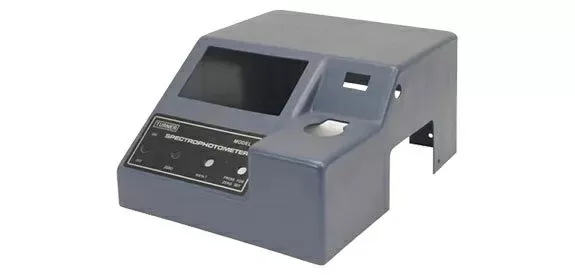
The decision to use PC versus ABS is more than just engineering; it is a strategic choice that takes into account factors ranging from design goals and manufacturing needs all the way to disposal issues. When manufacturers understand the role of these materials and how they will affect factors such as vacuum forming process technology or finished product quality, they are better able to achieve the overall success of the project. Plus: Competition among plastics manufacturers is so fierce today (not to mention increasingly stringent environmental regulations) that any company seeking an advantage must stay on top of the latest developments in product formulations and make products more environmentally friendly.
In the end, knowledge of the differences between PC and ABS in the thermoforming process is not just informed decision-making – it’s the groundwork for crafting a future that’s molded to perfection.