With the continuous emergence of new materials and new technologies, multi-layer heavy gauge thermoforming is used in the field of hospital medical equipment shell molding and manufacturing, opening a new chapter in structured products for hospital medical equipment shells.
To this end, it is necessary to explore the relevant elements of heavy gauge thermoforming products for hospital medical equipment casings, consider the optimization path of the thick gauge thermoforming process for medical equipment casings, and improve the quality of hospital medical equipment casing products.
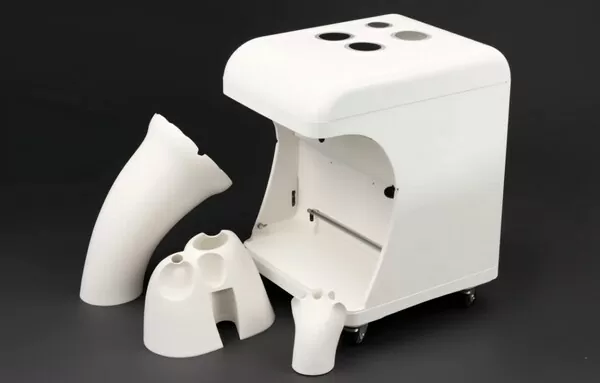
As a plastic processing technology, the main principle of pressure forming is to heat a flat hard plastic sheet to soften it, then use vacuum to adsorb it to the surface of the mold, and then cool it into shape. It is widely used in plastic packaging industry, pharmaceutical packaging sectors, healthcare sector, medical device packaging trays, food packaging industries, pharmaceutical industry, advertising, automotive industry decoration and other industries.
After a whole product is produced, it must be separated into individual small products, and then there will be some leftover edges of the product. Commonly used materials in blister packaging factories include PP, PET, PVC, PE, etc. As a sterile barrier system, medical packaging blister boxes are accepted by more and more medical devices, and PETG material used in medical applications is favored due to its strong. The market growth is significantly.
Ⅰ. Analysis of Design Elements of Medical Equipment Shells
Geometry and Accuracy
The geometric dimensions of the thermoformed shell include: the dimensions from the cutting surface to the molding surface of the thermoformed product, and the dimensions from the cutting surface to the cutting surface, which are directly related to the plate thickness, material properties, and molding process.
Draft Angle
The thermoforming mold consists of a concave mold and a convex mold with different demoulding angles. Generally speaking, the demoulding angle of the concave mold is 0.5°-1°, and the demoulding angle of the convex mold is 2°-5°.
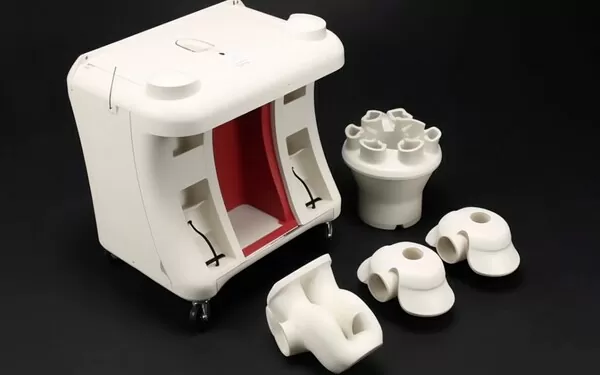
Shell Rounded Corners
The thermoformed shell should be designed with as large rounded corners as possible, and should not be designed with sharp corners and should be chamfered to ensure that the stress of the thermoformed shell product is appropriate.
Aspect Ratio
The width-to-depth ratio of thermoformed products for medical equipment shells is an important indicator to measure the ease of thermoforming. It represents the ratio of the minimum width to depth of the product. The larger the value, the easier it is to form the thin gauge thermoformed plastics product. The smaller the value, the easier it is to form the thermoformed product. It shows that the thermoformed products are more difficult to form.
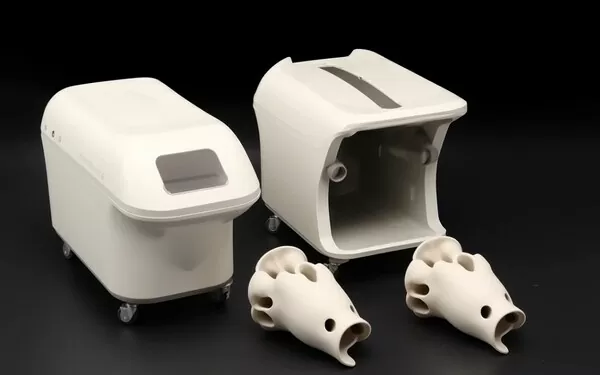
Ⅱ. Defects
1. Partial Molding of the Product is Insufficient.
The main causes of defects that lead to insufficient local molding of thermoformed shell thick plate products are:
The plasticity of the board itself is poor. There is insufficient vacuum between the sheet and the mold. The sheet has stretched too much. The mold temperature is low, etc.
2. Product Surface Color Defects.
The main causes of product surface color defects include:
Insufficient heating. Overheating. The mold heating temperature is not high.
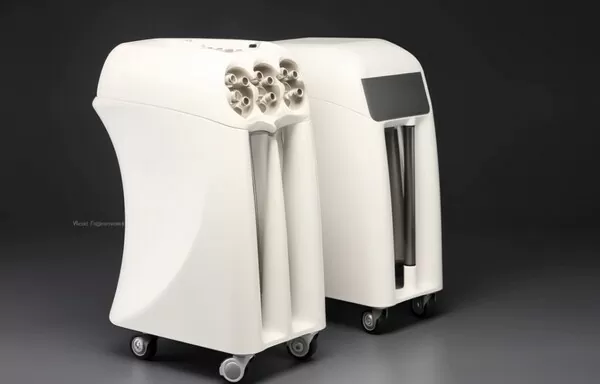
3. Product Flow Mark Defects.
The main causes of flow mark defects in products include:
The temperature of the mold and plate is not high. Poor mold temperature control. There is a deviation in the molding process.
4. Product Wrinkle Defects.
The main causes of wrinkle defects in products include: The board sags too much. The plate heating time is too long. The molding angle of the mold is too large.
5. Product Surface Flatness is Insufficient.
The main causes of uneven surface defects on products are as follows:
Insufficient cleanliness of the sheet or mold. The mold vacuum hole is too large. The mold does not have enough vacuum holes. There is a lamellar structure on the mold.
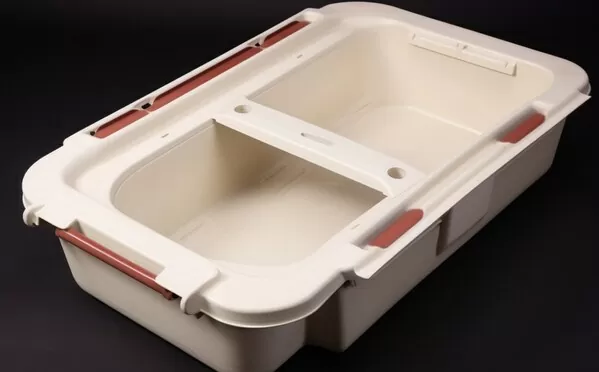
Ⅲ. How to Optimize the Production of Medical Device Shells
Optimization of Product Structure
The shell of hospital medical equipment has a large volume and surface area, so it can be designed in a curved shape to maintain the external beauty of the product structure and better avoid the defects of the thermoforming manufacturing process. The optimization of its structure mainly includes the following aspects:
1. Optimize the depth of the product.
Since there are many products with large barrel depths in hospital medical equipment, this brings great challenges to medical device manufacturers. In order to optimize the product molding effect, concave molding and punch-assisted pressing can be used to make the product sheet The material is heated between the upper and lower molds and a small amount of air is sucked out of the punch and the sheet, so that the sheet is adsorbed on the punch, and then the punch is gradually pressed down so that the sheet is completely adsorbed on the concave mold, and finally demoulded. Through this concave and convex mold-assisted molding method, the draft angle of the equipment shell product can be increased and the width-to-depth ratio of the shell product can be reduced.

2. Optimize the rounding of corners.
Based on the actual requirements of assembly, the corner rounding can be optimized at the junction of medical equipment shell products.
3. Adopt assembly bonding.
For thermoformed shells of hospital medical equipment, assembly bonding can be used instead of undercut designs. Double-layer thermoforming technology is used to replace the optimized process of single-layer thermoforming plate bonding to enhance the strength of the shell product.
Optimization of Process Parameters
Since the materials for hospital medical equipment shells are mainly ABS and ABS/PC, and assembly materials such as PC, HIPS, PET, and PP are used, it is necessary to analyze and optimize the process parameters of these different materials, including the following:
1. Sheet drying time.
This is the shrinkage characteristic parameter of the thermoformed sheet in the dry state, which is directly related to and affects the thermoforming of thick plates for medical equipment shells. When the drying times of different materials are: HDPE is 8 hours, PE is 6 hours, ABS is 8 hours, PC is 6 hours, and ABS/PC is 8 hours, it indicates that the performance of the medical equipment shell thick plate thermoforming product is relatively Stablize.
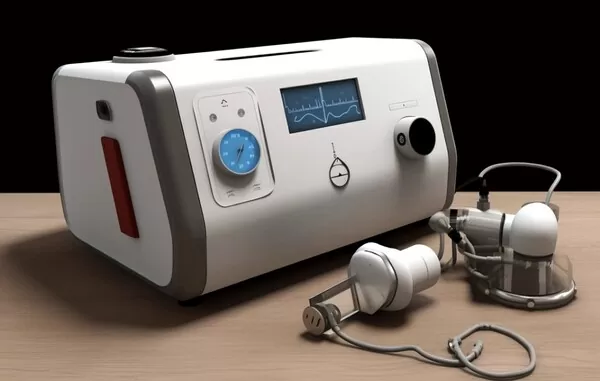
2. Thermoforming temperature. This is mainly analyzed and optimized from the two aspects of sheet heating temperature and pressure forming mold temperature. Among them: double-sided heating is usually used to heat the plastic sheet, and different molding temperatures are set according to different shapes of products. , making the product consistent with the design requirements. The temperature of the thermoforming mold should be kept appropriate and should not be too high or too low. If the mold temperature is too high, the product will adhere to the mold, causing the product to demould and deform. If the mold temperature is too low, the plate will be deformed. Improper molding may cause defects such as black spots, wrinkles, and cracks in the product. Generally speaking, when the medical equipment shell is thermoformed, the mold temperature is controlled at: HDPE is 50°C, PE is 50°C, PVC is 50°C, ABS is 70-80°C, PC is 120°C, and ABS/PC is 110°C. , indicating that the temperature of the thermoforming mold is appropriate.
Optimization of Mold Design
1. Optimize high-pressure thermoforming mold.
The high-pressure frame thermoforming mold structure can be used to fully form the thick plate thermoforming products of medical equipment shells.
2. Add upper mold to assist molding.
You can add an upper mold to assist in molding to produce cylindrical medical device packaging with large depth and complex shapes to avoid defects such as surface breakage or wrinkles on the surface of thermoformed products.
3. Add mold core-pulling structure.
By adding hinges, bonding blocks and cylinders to the design, the demoulding of thermoformed products can be better assisted.
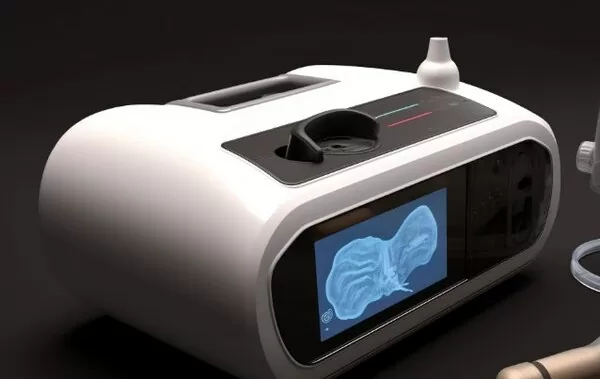
Raw Material Selection
The selection of raw materials is the basis for ensuring quality. From particles to thermoformed finished products, its requirements are much higher than those of food grade and industrial grade. The material selection of medical-grade vacuum forming boxes must meet ROHS requirements, and meet the requirements of IS010993 “Biological Evaluation of Medical Devices” and ISO11607 “Packaging of Terminal Sterilized Medical Devices” to achieve a complete sterile barrier system and microbial barrier function.
At present, there are many categories of food packaging materials produced in our country, with varying degrees of good and bad, and there are many hidden safety hazards. In particular, industrial PVC replaces PETG (material characteristics, usually medical blue), RPET (a recycled PET material) replaces APET, etc. After high-temperature molding and sterilization, a large amount of harmful substances will be precipitated, including pain-causing substances. , causing the device that was originally used to save lives and heal the wounded to eventually become a “killing” weapon. Therefore, we must choose materials carefully. At present, the main medical PETG include American Eastman 6763 and Korean SKS2008.
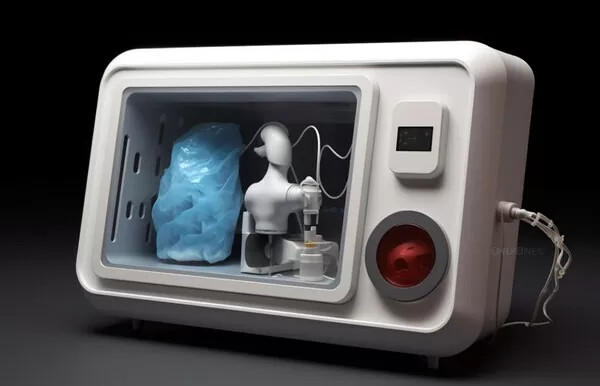
Thermoformed Box Structural Design
Before design and development, comprehensive factors such as demand for thermoformed plastics, forecast period, raw material selection, packaged equipment, sterilization methods, and clean opening by medical staff should be fully considered. And ensure the ability of sterilized medical device packaging to maintain sterility levels during the validity period. Therefore, details such as the design of edge banding width, hand tearing position, buckling method, etc. all need to be considered in the design stage.
Thermoforming Mold Selection
Medical thermoforming boxes use aluminum alloy molds. There are many kinds of aluminum materials. However, in terms of overall mold processing accuracy and various performance, 6061 is a better aluminum material. The aluminum material is processed into a mold by CNC. Since the inner core is aluminum, it is easy to achieve thermal balance. Cold water flows around it, which allows the mold to cool down quickly and improves the production efficiency of the vacuum forming box. Because the inner core is aluminum, it is easy to achieve thermal balance and cold water flows around it. Let the mold cool down quickly, increase the speed of goods production, and increase the smoothness of the thermoformed box. Because the cost of aluminum molds is high and the general service life is long, Martin Medical Packaging promises customers that the aluminum molds can be used for 10 years and can be produced repeatedly. can maintain high accuracy. There are many master molds on the thermoformed plastics market made of gypsum powder with a layer of copper on the outer electroplating surface. Not to mention the accuracy and appearance of the finished product, the cleanliness cannot meet the requirements of medical device packaging. The quality of the mold making of the thermoformed box directly affects the details of the finished thermoformed box, so it is recommended to choose carefully.
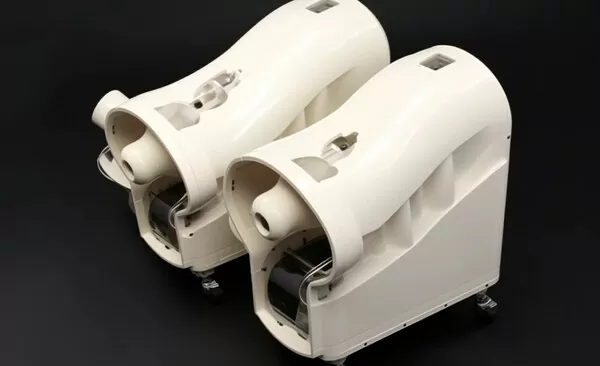
Conclusion
To sum up, the production of hospital medical equipment shells and medical thermoforming boxes is inseparable from the efficient and advanced thick plate thermoforming process. Vacuum forming must be better adopted by optimizing product structure, molding process parameters, mold design, etc. technology to meet the needs of hospital medical equipment shell use.