Introduction
Vacuum forming is a versatile manufacturing technique used to create plastic parts with various shapes, sizes, and complexities. It involves heating a plastic sheet until it becomes pliable, then stretching it over a mold while applying vacuum pressure. This vacuum pressure forming draws the heated sheet onto the female mold contours, allowing it to conform to the desired shape. Once cooled and solidified, the formed part is trimmed and ready for use.
The vacuum forming process offers several advantages, such as cost-effectiveness, fast production times, and the ability to create parts with intricate details. However, it is important to recognize the limitations inherent to vacuum forming to ensure successful outcomes. These limitations include factors such as the maximum size of parts that can be formed, the suitable material thickness, and the complexity of shapes that can be achieved.
In the subsequent sections of this article, we will delve into these limitations in more detail and explore the factors that influence the maximum size, material thickness, and complexity achievable in vacuum-formed parts. By understanding and working within these limitations, manufacturers can optimize their vacuum forming processes and create high volume production high-quality parts that meet their specific requirements.
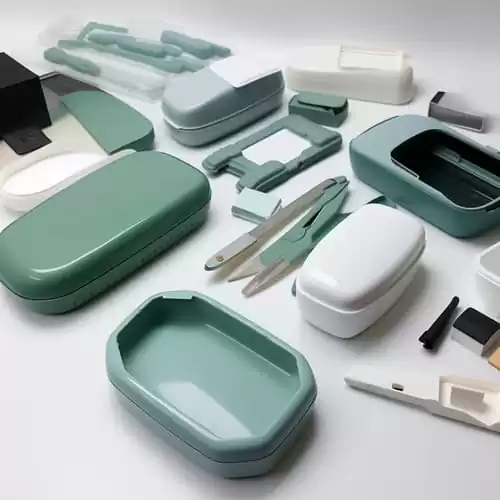
II. Maximum Size Limitations in Vacuum Forming
A. Factors influencing the maximum size of parts
The maximum size of parts that can be formed through vacuum forming is influenced by various factors. These include:
Sheet Size: The size of the thermoplastic sheet used in the process sets a limit on the dimensions of the formed part. Larger parts require larger sheets to ensure adequate coverage and stretching over the mold.
Machine Capabilities: The size and capabilities of the vacuum forming machine play a significant role in determining the maximum part size. Larger machines are capable of handling bigger sheets and accommodating larger molds, allowing for the formation of larger parts.
Mold Design: The design of the mold itself affects the maximum size of the part. The mold should have sufficient surface area to accommodate the desired part dimensions. Complex shapes or intricate details may require additional considerations in mold design.
B. Role of sheet size, machine capabilities, and mold design
The size of the thermoplastic sheet is a key factor in determining the maximum size of vacuum-formed parts. The sheet should be large enough to cover the entire mold and provide enough material for stretching and forming without excessive thinning or distortion.
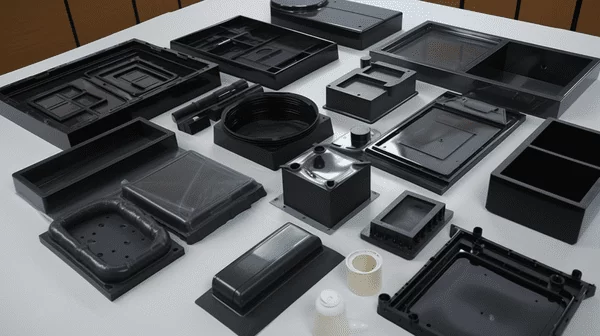
The capabilities of the vacuum forming machine, including the size of the forming area and the power of the vacuum system, also impact the maximum part size. Larger machines can handle larger sheets and apply stronger vacuum pressure, enabling the formation of larger parts.
Furthermore, mold design plays a crucial role in determining the maximum size of vacuum-formed parts. The mold should be designed with sufficient space and clearance to accommodate the desired various part sizes and dimensions. Considerations such as draft angles, undercuts, and surface area distribution should be taken into account to ensure successful forming.
C. Considerations for large parts and size constraints
When producing large vacuum-formed parts, several considerations come into play. These include:
Sheet Thickness: Thicker sheets are often required for larger parts to maintain structural integrity during the forming process and provide the necessary strength and rigidity in the final part.
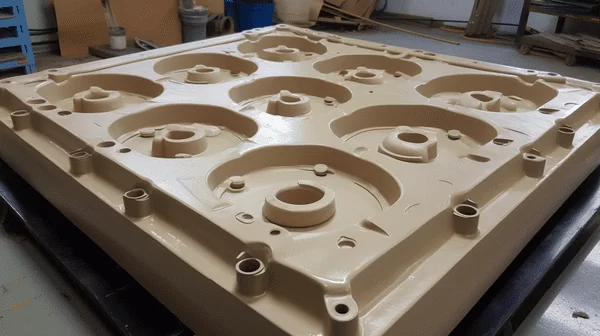
Heating and Cooling: Proper heating and cooling processes are crucial for large parts. Uniform heating ensures consistent material distribution and avoids thinning or distortion. Effective cooling prevents warping and facilitates faster production cycles.
Handling and Support: Large parts may require additional handling and support mechanisms to ensure proper positioning and prevent sagging or deformation during the forming process.
Material Choice: The selection of thermoplastic material should be considered carefully for large parts. Factors such as impact resistance, stiffness, and dimensional stability become more critical as part size increases.
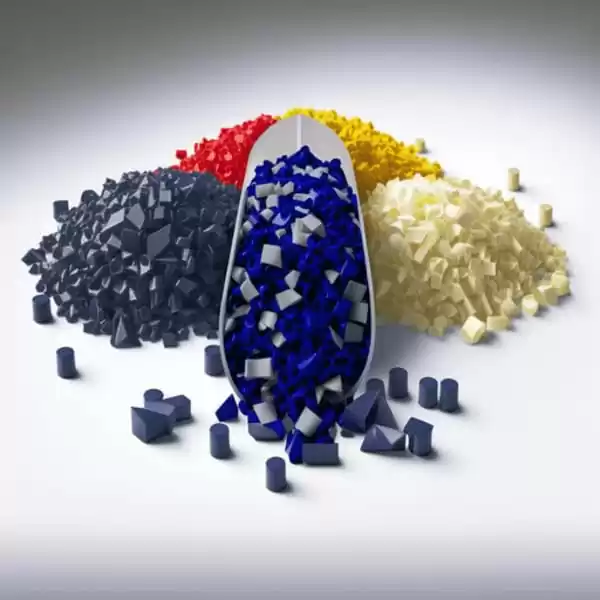
Understanding the size constraints and considering these factors in the design and production process is essential for successfully vacuum forming large parts. By optimizing sheet size, machine capabilities produce tooling, mold design, and material selection, manufacturers can overcome size limitations and produce high-quality vacuum-formed parts of larger dimensions.
III. Material Thickness Considerations
A. The relationship between material thickness and vacuum forming
Material thickness plays a crucial role in vacuum forming, as it impacts the forming process, part strength, and dimensional accuracy. The relationship between material thickness and vacuum forming can be summarized as follows:
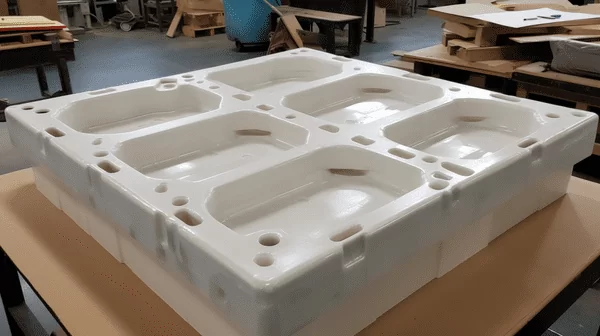
- Heat Transfer: Heat resistant materials require more time to heat evenly throughout the sheet. Effective heat transfer is essential to ensure uniform heating and pliability for proper stretching and forming.
- Forming Capability: Thicker materials have reduced stretchability compared to thinner ones. This can limit the complexity of shapes that can be achieved and may require adjustments in mold design and process parameters.
B. Suitable thickness ranges for different applications
The suitable thickness range for vacuum forming varies depending on the application and the desired characteristics of the final part. Here are some general guidelines:
Thin-Gauge Sheets: Vacuum forming commonly utilizes thin-gauge sheets with thicknesses ranging from 0.010 inches (0.25mm) to 0.080 inches (2mm). These sheets are ideal for producing lightweight parts, packaging components, and low to medium volumes parts.
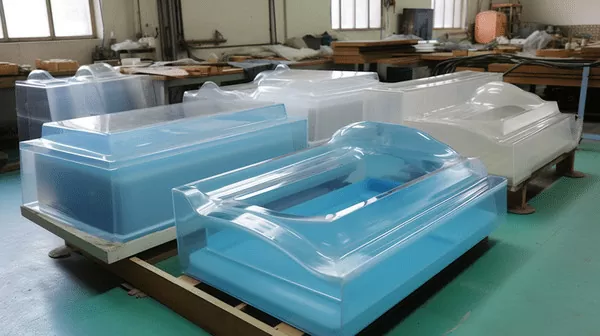
Thick-Gauge Sheets: For applications requiring more robust and structurally stable parts, thicker sheets in the range of 0.080 inches (2mm) to 0.250 inches (6mm) or even thicker can be used. These thicker sheets provide enhanced strength and impact resistance.
C. Impact of thickness on part strength and dimensional accuracy
The thickness of the material used in vacuum forming directly affects the strength and dimensional accuracy of the final part. Consider the following impacts:
- Part Strength: Thicker materials generally result in stronger parts, providing better resistance to impact and deformation. This is advantageous for applications where structural integrity is critical, such as automotive components or clamp frame industrial equipment. aluminium tools
- Dimensional Accuracy: Thicker materials are less prone to sagging or warping during the forming process, resulting in improved dimensional accuracy. This is particularly important for parts with strict tolerance requirements.
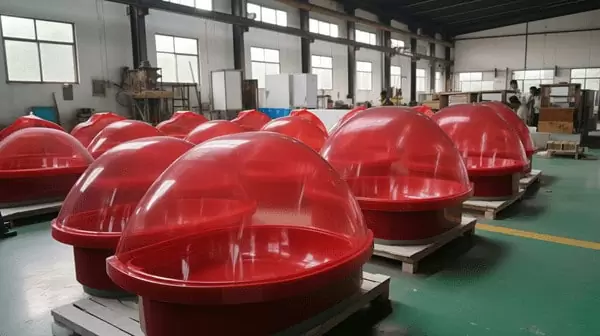
It is important to note that excessively thick materials may present challenges in terms of heating, cooling injection moulding, and forming. Adjustments to the process parameters, mold design, and machine capabilities may be necessary to accommodate thicker sheets effectively.
By considering the specific application, desired part characteristics, and the interplay between material thickness and vacuum forming, manufacturers can select the appropriate sheet thickness to achieve the desired strength and dimensional accuracy in their vacuum-formed parts.
IV. Complexity and Shape Limitations
A. Constraints in achieving complex shapes in vacuum forming
While vacuum forming offers versatility in part design, there are constraints when it comes to achieving complex shapes. Some limitations include:
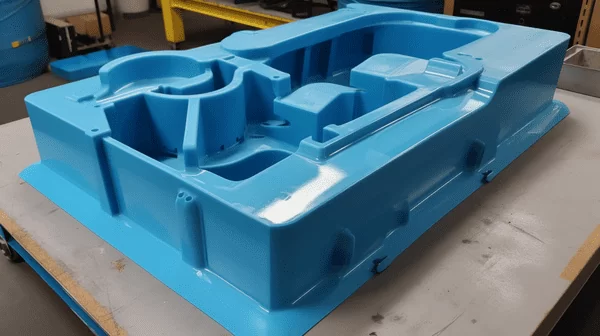
- Draw Ratios: The depth of draw, which refers to the depth of the mold cavity, affects the ability to form complex shapes. Parts with deep draws or intricate features may encounter limitations due to material stretchability and potential thinning in certain areas.
- Wall Thickness Variations: Maintaining consistent wall thickness throughout a complex shape can be challenging. Variations in material distribution may occur, resulting in thinning or thickening in specific regions of the part.
B. Draft angles and undercuts: considerations for mold design
Draft angles and undercuts play a crucial role in the injection molding and design for vacuum forming. Consider the following:
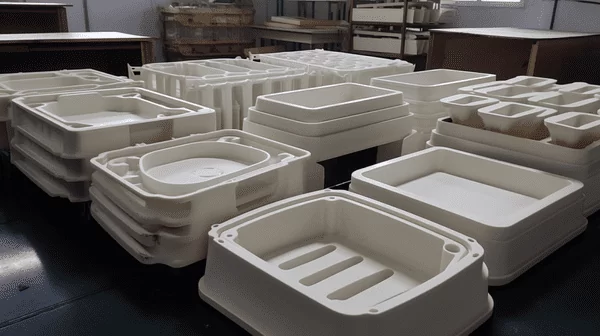
- Draft Angles: Draft angles are tapered angles incorporated into the walls of the mold. They facilitate easy removal of the formed part from the mold by allowing it to release smoothly. A minimum draft angle of 3 to 5 degrees is generally recommended in vacuum forming.
- Undercuts: Undercuts are features in a part design that prevent it from being easily released from the mold. Undercuts pose challenges in vacuum forming as they can lead to part distortion or difficulty in demolding. To accommodate undercuts, additional mold features such as side actions or mechanical or hydraulic actions may be required.
C. Balancing complexity and manufacturability in vacuum-formed parts
When designing vacuum-formed parts with complex shapes, it is crucial to balance complexity with manufacturability. Consider the following:
- Design Optimization: Work closely with mold designers and engineers to optimize the part design for vacuum forming. Simplifying complex features or adding split lines can aid in achieving the desired shape while ensuring proper material distribution and demolding.
- Prototyping and Testing: Utilize prototyping and testing to validate the manufacturability of complex designs. Iterative testing allows for adjustments and improvements to ensure successful vacuum forming.
- Material Selection: The choice of thermoplastic material can impact the ease of forming complex shapes. Certain materials have better stretchability and are more suitable for intricate designs.
By understanding the constraints associated with complex shapes in vacuum forming and considering mold design factors such as draft angles and undercuts, manufacturers can strike a balance between design complexity and manufacturability. Collaborative efforts, prototyping, and material selection play crucial roles in achieving successful vacuum-formed parts with intricate shapes.
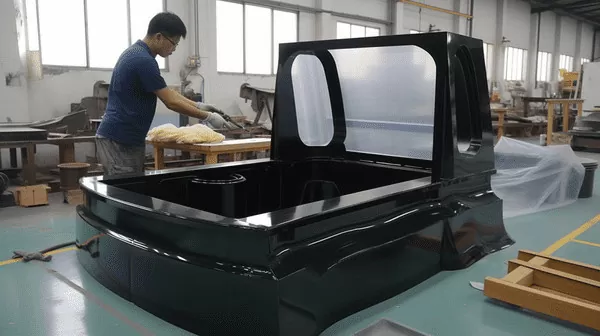
Conclusion
In conclusion, understanding the limitations of vacuum forming is crucial for manufacturers and designers aiming to optimize their production processes. By comprehending the boundaries of vacuum forming, they can make informed decisions regarding part size light weight, material thickness, complexity, and cost considerations. Maximizing the potential of vacuum forming requires careful attention to design and material choices.
First and foremost, recognizing the importance of understanding the limitations of vacuum forming is essential. By being aware of the constraints and challenges inherent in the process, manufacturers can set realistic expectations and develop appropriate strategies to overcome them.
Key considerations in vacuum forming include size, material thickness, complexity, and cost. Understanding the maximum size limitations allows manufacturers to select appropriate equipment, optimize sheet size, and design parts accordingly. Material thickness plays a significant role in achieving desired strength, dimensional accuracy, and manufacturability. Balancing complexity and manufacturability requires careful mold design considerations such as draft angles and undercuts.
Additionally, cost considerations are vital in vacuum forming. By optimizing design and material choices, manufacturers can strike a balance between cost-effectiveness and desired part quality.
Maximizing the potential of vacuum forming is achieved through informed design and material choices. Collaboration between designers, engineers, and mold makers is crucial in optimizing part design, mold design, and material selection. Prototyping and testing aid in validating designs and making necessary adjustments.
By understanding the limitations, considering key considerations, and making informed choices, manufacturers can harness the full potential of vacuum forming. The process offers cost-effective solutions, design flexibility, and fast production times, making it an attractive option in various industries. With careful attention to design and material choices, vacuum forming can deliver high-quality parts that meet specific requirements.