Introduction:
Vacuum forming is a widely used manufacturing technique that involves shaping plastic sheets into various forms. It is a versatile and cost-effective method employed in industries such as packaging, automotive, aerospace, and more. One crucial consideration in vacuum forming is the maximum draw depth, which plays a significant role in determining the final product’s shape and functionality. Understanding the concept of maximum draw depth is vital for achieving successful outcomes in the vacuum forming process.
In the upcoming sections of this article, we will delve deeper into the concept of maximum draw depth in vacuum forming. We will explore the factors that influence it, the significance of achieving the right draw depth, and the impact it has on the overall manufacturing process. By gaining a thorough understanding of the maximum draw depth, manufacturers can make informed decisions and implement strategies to improve the quality and efficiency of their vacuum forming operations.
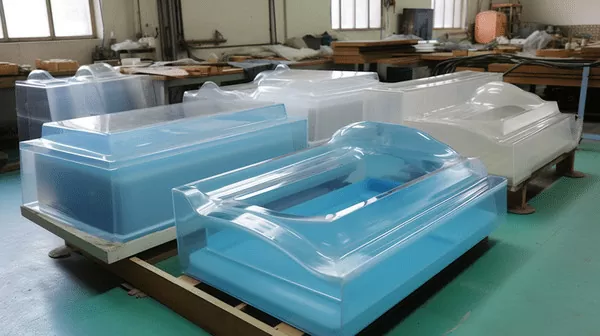
II. Understanding Maximum Draw Depth
The maximum draw depth in vacuum forming is a critical parameter that directly affects the quality and functionality of the formed parts. Let’s explore the definition of maximum draw depth and the significance of achieving the desired draw depth for high-quality results.
1.Definition of Maximum Draw Depth:
The maximum draw depth refers to the depth or height to which a heated plastic sheet can be drawn into a mold under vacuum pressure during the vacuum forming process. It represents the limit beyond which the plastic sheet may not stretch adequately to fill the mold’s features. The draw depth is determined by the material properties, sheet thickness, mold design, heating process, and other factors involved in the vacuum forming operation.
2.Significance of Achieving the Desired Draw Depth for High-Quality Parts:
Achieving the desired draw depth is crucial for obtaining high-quality, accurately formed parts in vacuum forming. Here’s why it is significant:
a. Shape and Geometry:
The draw depth directly influences the shape and geometry of the formed part. By achieving the intended draw depth, manufacturers can ensure that the formed part matches the desired design specifications and meets the required dimensional tolerances.
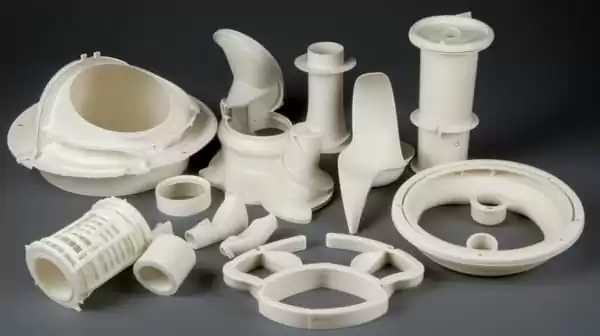
b. Material Distribution:
Proper draw depth helps in achieving uniform material distribution across the injection molding part. This uniformity ensures consistent wall thickness, minimizing variations and preventing structural weaknesses or thinning in specific areas of the formed part.
c. Mechanical Strength:
The draw depth affects the mechanical strength and integrity of the formed part. By achieving the appropriate draw depth, manufacturers can ensure that the part has sufficient excess material thickness to withstand the intended application’s mechanical stresses and requirements.
d. Surface Quality:
The draw depth can influence the tool side quality and finish of the formed part. With the right draw depth, manufacturers can achieve smooth surfaces, sharp corners, and crisp details, enhancing the aesthetics and overall appearance of the final product.
e. Functionality and Fit:
The draw depth plays a vital role in achieving the required functionality and fit of the formed part. By achieving the desired draw depth, manufacturers can ensure that flat surface of the part fits into assemblies or interfaces properly, allowing for seamless integration and optimal performance.
In conclusion, understanding the maximum draw depth and achieving the desired draw depth is crucial for producing high-quality vacuum-formed parts. It impacts the shape, material distribution, strength, surface quality, functionality, and fit of the final product. By carefully considering and optimizing the draw depth, manufacturers can ensure consistent quality, dimensional accuracy, and performance in their vacuum forming processes.
III. Factors Influencing Maximum Draw Depth
A. Material Properties:
The material properties have a significant impact on the maximum draw depth in vacuum forming. Different thermoplastics exhibit varying levels of elongation capabilities, chemical resistance, flame retardancy, and UV resistance. Some common thermoplastics used in vacuum forming include ABS, polycarbonate, PVC, and acrylic. The material properties determine the flexibility and stretchability of the plastic sheet, which, in turn, affects the maximum draw depth achievable.
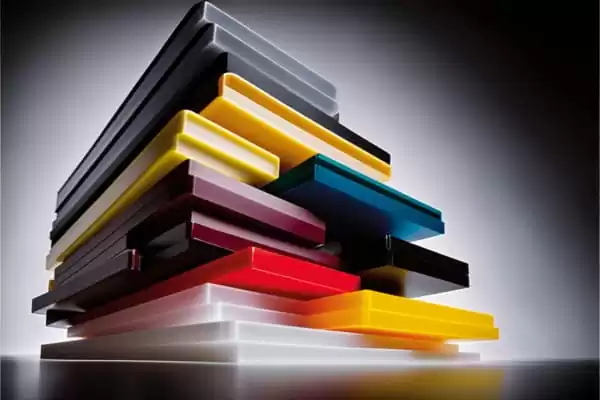
B. Sheet Thickness and Minimum Starting Gauge:
The sheet thickness directly influences the maximum draw depth. Thicker sheets have reduced flexibility and elongation capabilities, limiting the achievable draw depth. Conversely, thinner sheets offer greater stretchability, allowing for deeper draws. However, it is crucial to strike a balance to avoid excessive thinning, which can compromise the structural integrity of the formed part. Manufacturers must also consider the minimum starting gauge, which refers to the minimum thickness required to achieve the desired draw depth.
C. Heating Process:
Proper heating of the plastic sheet is essential for achieving the desired draw depth. Heating makes the plastic sheet pliable and easier to form. It ensures uniform stretching during the vacuum forming process. Achieving the right temperature distribution across the sheet is crucial to prevent uneven stretching, thinning, or overheating of specific areas. Proper heating techniques, such as preheating or using heating elements, contribute to achieving the optimal draw depth.
D. Mold Design:
The design of the mold significantly influences the maximum draw depth. Mold features like sharp corners, draft angles, undercuts, and surface area affect the stretchability and flow of the plastic sheet. Sharp corners and small draft angles may restrict the draw depth due to the risk of material thinning or tearing. Well-designed molds with appropriate features, cooling channels, and vents facilitate uniform stretching and accommodate the desired draw depth.
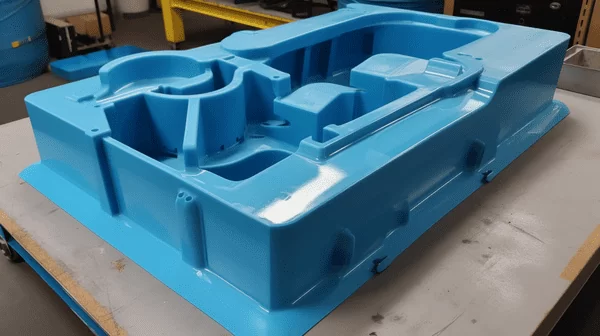
E. Vacuum Pressure and Draw Ratio:
The vacuum pressure and draw ratio directly impact the maximum draw depth in vacuum forming. Higher vacuum pressure levels and larger draw ratios generally allow for deeper draws. However, excessive vacuum pressure or draw ratios can lead to overstretching, thinning, or distortion of the plastic sheet. It is crucial to find the right balance to achieve the desired draw depth while maintaining the structural integrity and dimensional accuracy of the formed part.
By considering and optimizing these factors, manufacturers can determine and achieve the maximum draw depth suitable for their specific vacuum forming applications. Understanding how material properties, sheet thickness, heating process, mold design, vacuum pressure, and draw ratio influence the draw depth is crucial for producing high-quality, accurately formed parts.
IV. Importance of Determining Maximum Draw Depth
Determining the maximum draw depth in vacuum forming is of utmost importance for optimizing the manufacturing process and ensuring consistent part quality.
Let’s explore why determining the maximum draw depth is crucial and the benefits it brings.
1.Optimizing the Vacuum Forming Process:
Determining the maximum draw depth allows manufacturers to optimize the vacuum forming process in several ways:
a. Material Selection:
By understanding the maximum draw depth, manufacturers can choose the right material with suitable elongation capabilities and other desired properties. This ensures that the selected material can achieve the required draw depth without compromising its structural integrity.
b. Mold Design:
Knowledge of the maximum draw depth helps in designing molds that facilitate the desired draw depth. Manufacturers can consider factors such as draft angles, sharp corners, and appropriate features that allow for optimal stretching and material distribution. Well-designed molds contribute to consistent part quality and minimize the risk of defects.
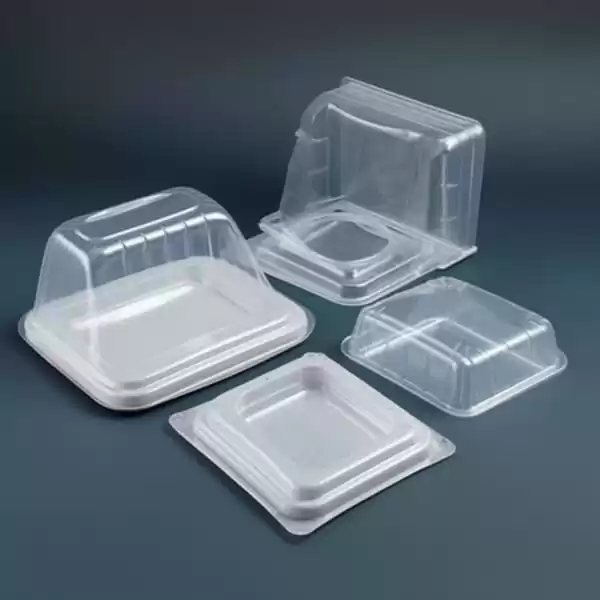
c. Process Parameters:
Determining the maximum draw depth guides the setting of process parameters such as heating temperature, heating time, cooling rate, vacuum pressure, and draw ratio. By fine-tuning these parameters based on the desired draw depth, manufacturers can achieve better control over the forming process, resulting in consistent part quality and reduced production variability.
2.Minimizing Material Wastage and Ensuring Consistent Part Quality:
Determining the maximum draw depth helps in minimizing material wastage and ensuring consistent part quality:
a. Material Optimization:
With knowledge of the maximum draw depth, manufacturers can optimize the sheet thickness and starting gauge to minimize material wastage. Using the thinnest feasible sheet thickness that can achieve the desired draw depth reduces material costs and minimizes waste.
b. Avoiding Overstretching and Thinning:
Understanding the maximum draw depth prevents overstretching and excessive thinning of the plastic sheet. By staying within the limits of the maximum draw depth, manufacturers can maintain the structural integrity of the formed part, preventing defects such as weak spots, tears, or inconsistent wall thickness pressure forming.
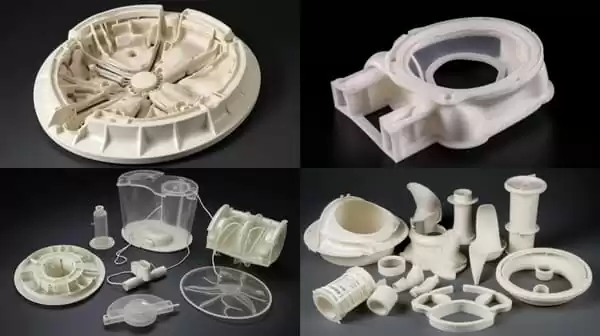
c. Consistency in Part Quality:
Determining and adhering to the maximum draw depth ensures consistent part quality across production runs. Consistency in draw depth leads to consistent part dimensions, aesthetics, fit, and functionality. This is crucial for meeting customer specifications, reducing rejections, and improving overall customer satisfaction.
By determining the maximum draw depth and using this knowledge to optimize the vacuum forming process, manufacturers can minimize material wastage, improve process efficiency, and ensure consistent part quality. It enables them to produce high-quality vacuum-formed parts that meet design requirements and exceed customer expectations.
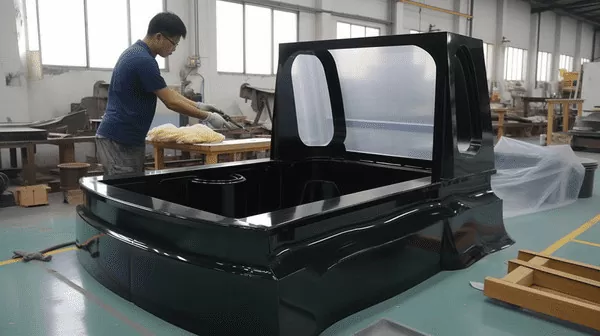
Conclusion:
In conclusion, the maximum draw depth plays a crucial role in the vacuum forming process and plastic fabrication. Throughout this article, we have explored the factors that influence the maximum draw depth and its significance in producing high-quality parts.
In the dynamic world of plastic fabrication, understanding and maximizing the draw depth in vacuum forming is essential. It empowers manufacturers to create high-quality parts with precise dimensions, optimal functionality, and exceptional aesthetics. By staying abreast of the latest innovations and continuously improving vacuum forming processes, manufacturers can achieve deeper draws, expand the possibilities of plastic fabrication, and meet the ever-growing demands of diverse industries.