Introduction
Plastic vacuum forming stands as a remarkably versatile manufacturing process, offering the ability to transform flat plastic sheets into intricate shapes and forms. This adaptable technique is employed across numerous industries, from packaging to automotive manufacturing. Yet, the key to unlocking its full potential lies in a fundamental choice: the selection of the right materials. In this introductory segment, we will shed light on the concept of plastic vacuum forming and underscore the pivotal role that material selection plays in ensuring the success of this manufacturing method.
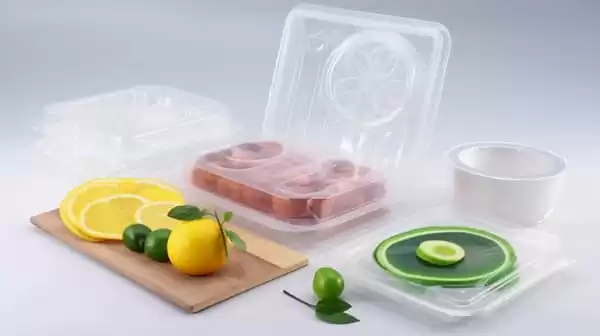
II. Understanding the Basics of Vacuum Forming
For those new to the concept, vacuum forming is a manufacturing process that transforms flat plastic sheets into three-dimensional shapes. It relies on heat, pressure, and suction to achieve its results. To gain a better understanding, let’s delve into the key components and steps involved in vacuum forming:
1. Plastic Sheet Selection: The process begins with the selection of a plastic sheet, typically made of thicker materials such as acrylic, ABS, PVC, or polycarbonate. The choice of material depends on the intended application, as each offers unique properties.
2. Heating: The selected plastic sheet is heated until it reaches a pliable state. This is typically done using heaters or ovens, softening the plastic parts for the forming process.
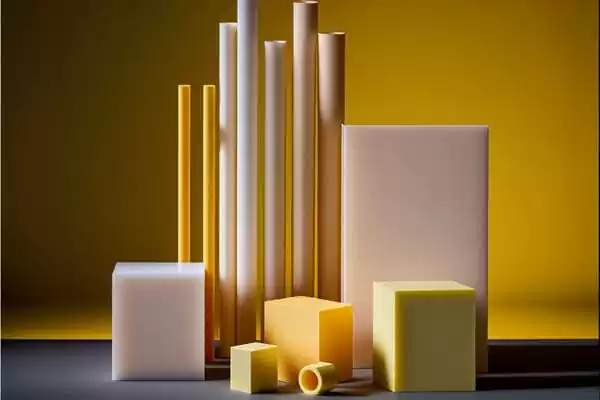
3. Molding: Once the plastic sheet is sufficiently heated, it is draped over a mold or placed between male and female molds. The mold defines the final shape of the product.
4. Vacuum Pump Activation: A vacuum pump comes into play at this stage. It creates a vacuum between the heated plastic sheet and the mold. This vacuum exerts suction on the sheet, pulling it tightly against the contours of the mold.
5. Cooling: After the plastic has assumed the desired shape, it is rapidly cooled to solidify the form. Cooling can be achieved using chilled air, water, or other cooling methods.
6. Trimming: Any excess plastic is trimmed away, leaving behind the vacuum-formed product. This trimming ensures a clean and precise final result.
In essence, vacuum forming is a process that marries heat, pressure, and vacuum forces to mold plastic sheets into various shapes. Understanding these fundamental steps is crucial for grasping the intricacies of the vacuum forming process and its significance in manufacturing.
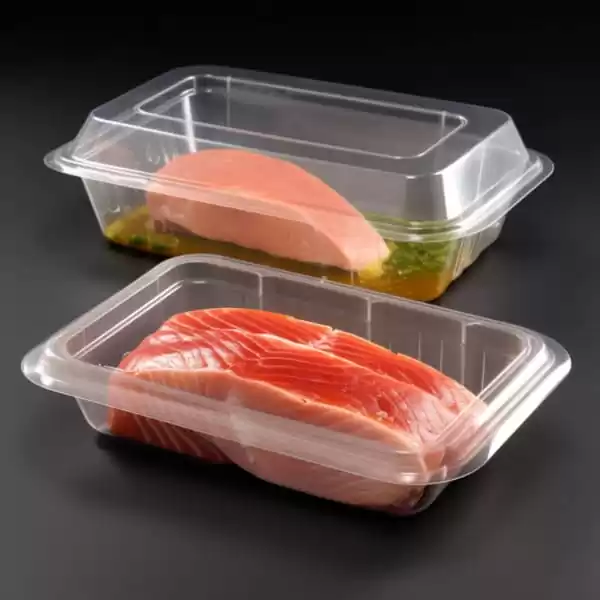
III. The Role of Material Selection
Material selection serves as a pivotal and often underestimated factor in the success of the vacuum forming process. It plays a critical role in determining the quality, functionality, and overall performance of the final product. Here, we explore why material selection is of paramount importance in the vacuum forming process and how it can significantly impact the end result.
1. Aesthetic and Functional Properties:
The choice of material profoundly influences the visual aesthetics and functional characteristics of the vacuum-formed product. Different plastics offer distinct properties such as transparency, color options, surface texture, and resistance to wear and tear. For instance, opting for transparent acrylic may be ideal when creating display cases, while ABS with its toughness may be a better choice for automotive components.
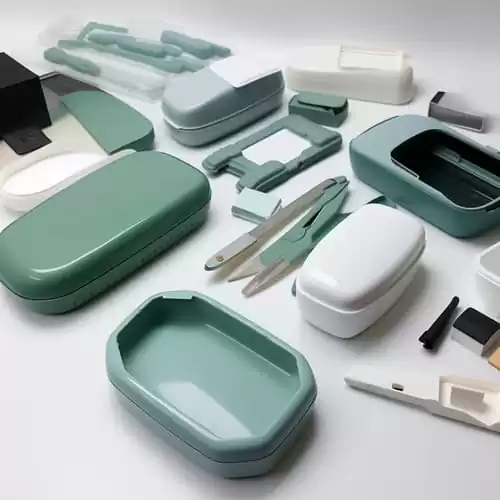
2. Durability and Longevity:
Depending on the intended application, durability and longevity can be critical factors. Some plastics are highly resistant to impact, UV radiation, and chemicals, making them suitable for outdoor use or in harsh environments. Material selection must align with the expected lifespan and environmental conditions the product will encounter.
3. Temperature Resistance:
Certain applications may require vacuum-formed products to withstand high temperatures, such as automotive components in the engine compartment. In such cases, selecting a plastic with good temperature resistance is paramount to prevent deformation or degradation.
4. Cost Considerations:
Material cost is a practical aspect that cannot be overlooked. Some materials are more affordable than others, which can significantly impact the project’s budget. However, cost should be balanced with the required performance and quality standards.
5. Versatility and Formability:
Different plastics have varying degrees of formability, and some may be better suited for complex shapes than others. Material selection should take into account the ease of forming and whether the plastic can achieve the desired shape without compromising structural integrity.
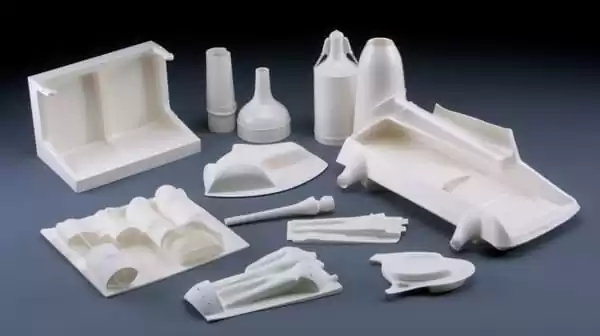
6. Compatibility with Regulations:
In specific industries, such as medical or food packaging, regulatory compliance is paramount. Material selection must align with industry-specific regulations, ensuring the product’s safety and suitability for its intended purpose.
In summary, material selection is far more than a routine decision; it is a strategic choice that can significantly impact the outcome of the makes vacuum forming process. By carefully considering the properties, characteristics, and intended use of the plastic materials, manufacturers can optimize the quality and functionality of their vacuum-formed products, ensuring they meet both aesthetic and performance expectations. Ultimately, the right material selection is a key determinant of a successful vacuum forming project.
IV. Wide Range of Materials
The versatility of plastic and vacuum forming machines is inextricably linked to the extensive array of materials that can be harnessed for this manufacturing process. The diversity of available materials allows manufacturers to tailor their selections to meet the precise requirements of their projects. In this section, we will delve into the wide-ranging options of materials used in plastic vacuum forming and highlight the importance of aligning material choices with specific project needs.
1. Acrylic (PMMA):
Acrylic, also known as polymethyl methacrylate (PMMA), stands as a popular choice for its exceptional transparency and impact resistance. It finds applications in creating clear or translucent products like display cases, signage, and light fixtures. Its aesthetic appeal and high visibility make it ideal for showcasing products.
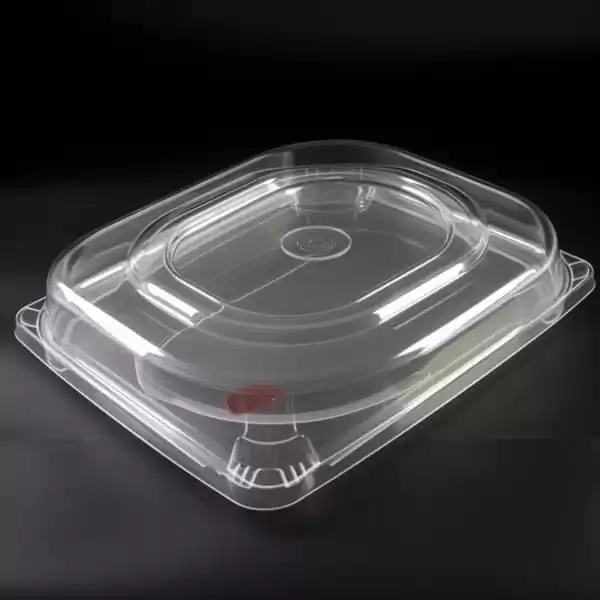
2. ABS (Acrylonitrile Butadiene Styrene):
ABS combines toughness with versatility. It is frequently employed in automotive parts, electronics housings, and industrial components. ABS can withstand a wide range of temperatures, rendering it dependable for both indoor and outdoor applications.

3. PVC (Polyvinyl Chloride):
PVC is recognized for its durability and chemical resistance. It exists in rigid and flexible forms, catering to diverse applications. Rigid PVC finds use in packaging and containers, while flexible PVC is employed in medical devices and inflatable structures.
4. PETG (Polyethylene Terephthalate Glycol):
PETG boasts transparency, impact resistance, and chemical resilience. It serves well in packaging, point-of-purchase displays, and medical equipment. Even after forming, PETG retains its properties, making it a reliable choice.
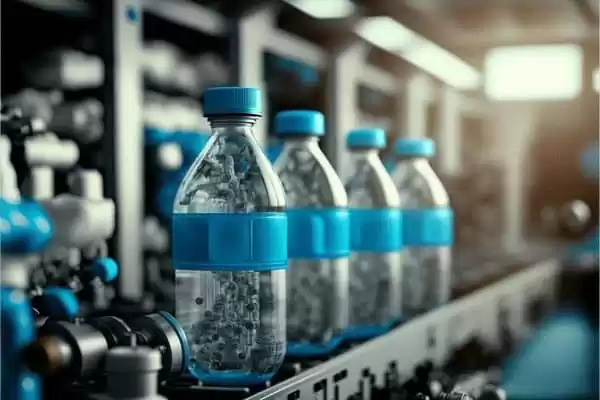
5. Polycarbonate:
Polycarbonate is renowned for its strength and optical clarity. It finds applications in protective eyewear, machine guards, and automotive components. Its exceptional durability and optical quality remain intact post-forming.
6. Polyethylene and Polypropylene:
Cost-effective and chemically resistant, polyethylene (PE) and polypropylene (PP) offer functional solutions. They are utilized in packaging inserts, automotive interior components, and disposable containers.
7. High-Density Polyethylene (HDPE):
Although less common than other materials, HDPE can be used in vacuum forming. Its lower melting point makes it suitable for simpler forms and applications where impact resistance is not the primary concern.
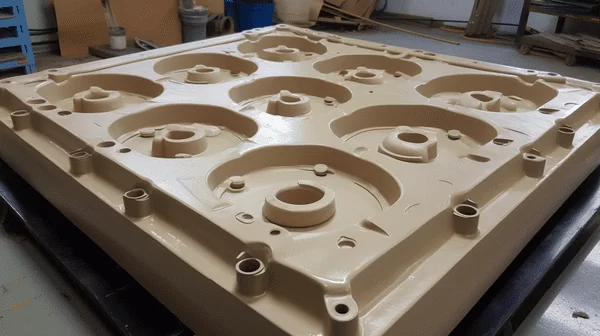
8. Specialty Materials:
Depending on the project’s requirements, other specialty materials may be considered. These could include plastics with self-extinguishing properties for fire resistance, ceramics for precise heating control, or specific formulations for medical or food-grade applications.
Tailoring Material Choices to Project Requirements:
The key takeaway is that the material selection should align with the specific needs of the project. Whether you prioritize aesthetics, durability, versatility, or cost-effectiveness, there is a material within the vast spectrum of options that can be finely tuned to meet your vacuum forming requirements. By carefully assessing the project’s objectives and material properties, manufacturers can optimize the outcome and performance of their vacuum-formed products.
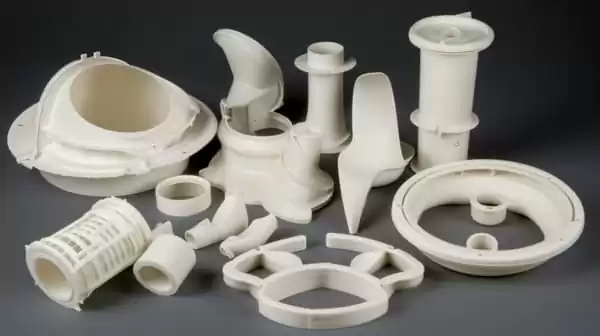
V. Commonly Used Materials
In the realm of vacuum forming, several materials have earned their place as commonly used options due to their versatile properties and suitability for various applications. In this section, we will delve into some of these frequently chosen materials, providing descriptions of each material, highlighting their key properties, and offering examples of typical pressure forming applications where they excel.
1. Acrylic (PMMA – Polymethyl Methacrylate):
Properties: Acrylic is celebrated for its exceptional transparency and high impact resistance. It offers excellent optical clarity and weather resistance.
Applications: Commonly used in applications where aesthetics matter, such as display cases, signage, light fixtures, and outdoor enclosures. Its transparency makes it ideal for showcasing products.
2. ABS (Acrylonitrile Butadiene Styrene):
Properties: ABS is known for its toughness, versatility, and ability to withstand a wide range of temperatures. It exhibits good impact resistance and dimensional stability.
Applications: Frequently employed in automotive parts, electronics housings, consumer goods, and industrial components. Its robustness makes it suitable for both indoor and outdoor use.
3. PVC (Polyvinyl Chloride):
Properties: PVC offers durability, chemical resistance, and electrical insulation. It is available in both rigid and flexible forms.
Applications: Rigid PVC is used in packaging, containers, and construction materials, while flexible PVC finds its place in medical devices, inflatable structures rigid pipes, and wire insulation.
4. PETG (Polyethylene Terephthalate Glycol):
Properties: PETG provides transparency, impact resistance, and chemical resilience. It is known for its ease of processing and recycling capabilities.
Applications: Widely used in packaging, point-of-purchase displays, medical equipment, and disposable containers. Its post-forming properties remain consistent.
5. Polycarbonate:
Properties: Polycarbonate is characterized by its exceptional strength, impact resistance, and optical clarity. It offers good dimensional stability.
Applications: Finds applications in protective eyewear, machine guards, automotive components, and products where durability and optical quality are essential.
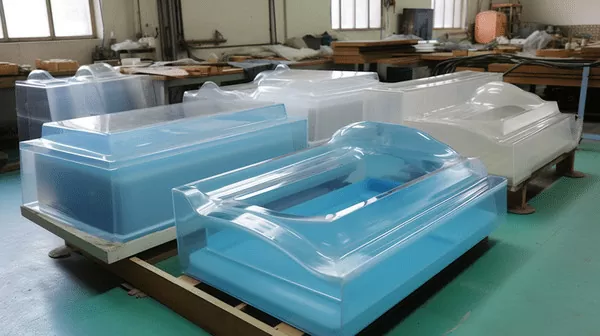
6. Polyethylene (PE) and Polypropylene (PP):
Properties: Both PE and PP are cost-effective and chemically resistant. They are lightweight and exhibit good moisture resistance.
Applications: Used for packaging inserts best plastics, automotive interior components, disposable containers, and various consumer products. Their versatility and affordability make them popular choices.
7. High-Density Polyethylene (HDPE):
Properties: HDPE boasts a lower melting point compared to other materials. It is known for its toughness and ease of processing.
Applications: While less common than other materials, HDPE can be used for simpler forms and applications where impact resistance is not the primary concern.
These commonly used materials in vacuum forming cater to a wide range of applications, from aesthetically driven displays to rugged automotive components. The selection of the most suitable material depends on the specific requirements and performance characteristics desired for the project at hand.
VI. Acrylic (PMMA)
Acrylic, scientifically known as Polymethyl Methacrylate (PMMA), is a versatile material celebrated for its distinct properties and suitability for various applications in vacuum forming.
Properties of Acrylic:
Transparency: One of acrylic’s most remarkable features is its exceptional transparency. It allows light to pass through with incredible clarity, making it an ideal choice for applications where visibility and aesthetics are paramount.
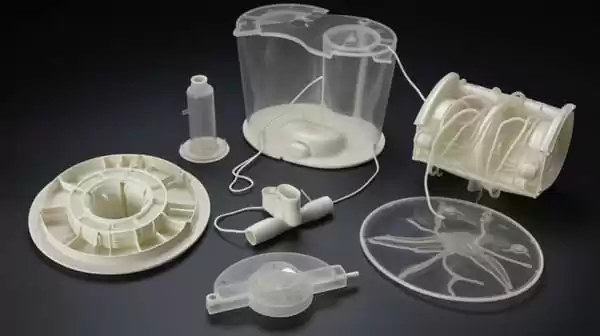
Impact Resistance: Despite its transparency, acrylic boasts impressive impact resistance. It can withstand moderate to heavy impacts without shattering, which contributes to its durability.
Applications of Acrylic in Vacuum Forming:
Display Cases: Acrylic is a favored choice for crafting display cases, whether in museums, retail stores, or exhibitions. Its transparency showcases the enclosed items with unparalleled clarity, creating an attractive and unobstructed view for viewers.
Light Fixtures: Acrylic’s ability to transmit light effectively makes it a top choice for light fixtures. It acts as an excellent light diffuser, evenly distributing and softening the light emitted by bulbs or LEDs. This makes it valuable in creating aesthetically pleasing and well-lit spaces.
Signage: Acrylic is often used to produce various types of signage, including illuminated signs and directory boards. Its transparency allows for the integration of lighting elements, resulting in eye-catching and easily visible signage.
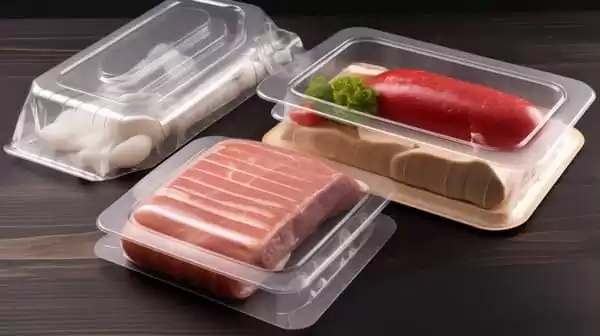
Outdoor Enclosures: Acrylic can be utilized in outdoor enclosures for protecting valuable equipment or displays. Its weather resistance ensures that it can withstand exposure to the elements without yellowing or losing transparency over time.
Architectural Features: In architecture and interior design, acrylic is employed to create decorative elements such as wall panels, partitions, and even artistic installations. Its transparency and adaptability allow for the realization of innovative and visually striking designs.
Acrylic’s unique combination of transparency and impact resistance makes it a sought-after material in vacuum forming plastics for applications where visual appeal and robustness are prerequisites. Whether it’s illuminating a retail space, protecting valuable artifacts, or enhancing the aesthetics of architectural features, acrylic stands as a versatile choice that consistently delivers outstanding results.
VII. ABS (Acrylonitrile Butadiene Styrene)
Acrylonitrile Butadiene Styrene (ABS) is a widely used thermoplastic polymer renowned for its combination of toughness, adaptability, and ease of processing, making it a valuable material choice in vacuum forming.
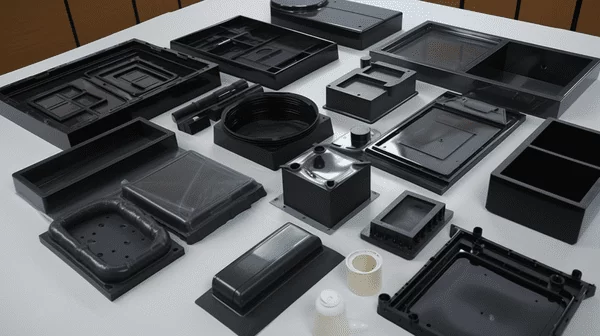
Properties of ABS:
Toughness: One of ABS’s standout features is its toughness. It can endure significant impacts without breaking or shattering, making it highly durable.
Adaptability: ABS is known for its versatility and ease of processing. It can be molded into various shapes and forms, making it suitable for a wide range of applications.
Temperature Resistance: ABS exhibits good resistance to both high and low temperatures, making it reliable in diverse environments.
Common Uses for ABS in Vacuum Forming:
Automotive Parts: ABS is extensively used in the automotive industry to create components such as interior trim, dashboards, door panels, and exterior body parts. Its toughness ensures that these parts can withstand the rigors of daily use and potential impacts.
Consumer Goods: ABS is prevalent in the production of consumer goods, including toys, appliance housings, and electronics casings. Its adaptability allows for the creation of intricate and aesthetically pleasing designs.
Industrial Components: Vacuum-formed ABS finds applications in manufacturing and industrial settings. It is utilized for producing protective covers, enclosures, machine guards, and housing for various machinery due to its robustness and ease of customization.
Luggage and Cases: ABS is a popular choice for manufacturing luggage, travel cases plastic boxes, and protective containers. Its combination of toughness and resistance to impact ensures that these items can withstand the stresses of travel.
Point-of-Purchase Displays: In the retail industry, ABS is employed to create point-of-purchase displays and fixtures. Its adaptability allows for the fabrication of eye-catching and functional displays that can showcase products effectively.
DIY Projects: ABS sheets are often used in do-it-yourself (DIY) projects. Hobbyists and makers find ABS easy to work with for creating custom enclosures, model parts, and various prototypes.
Prototyping: Designers and engineers use ABS in prototyping due to its ease of machining and formability. It allows for quick iterations and modifications during the design phase.
ABS’s toughness, adaptability, and resistance to temperature extremes make it a reliable choice in vacuum forming for a broad spectrum of applications. Whether it’s enhancing the interior of a car, creating durable consumer goods, or constructing industrial components, ABS’s versatility makes it a top contender for manufacturers seeking a robust and customizable material solution.
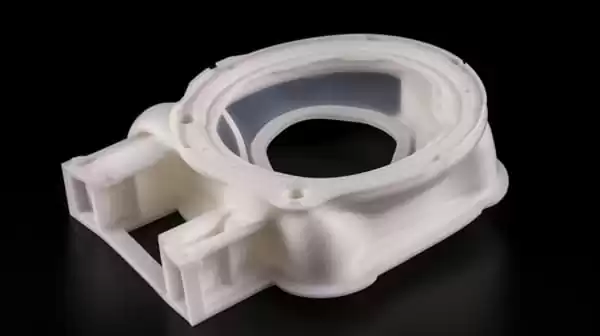
Conclusion
In conclusion, the process of plastic vacuum forming presents an array of possibilities for transforming flat plastic sheets into three-dimensional shapes. However, the success of vacuum forming hinges on a crucial factor—material selection. Throughout this article, we’ve explored the diverse materials available for vacuum forming and how they can significantly impact the final product’s quality, functionality, and aesthetics.