Introduction
Vacuum forming plastic is an increasingly popular manufacturing technique used to craft an array of plastic products, from food containers and spare wheel covers to shower trays and more. This process involves heating a plastic sheet until it becomes malleable before stretching it over a mold using vacuum force to pull tightly against its contours and stretch tightly against them using another vacuum source. Once hardened and cool, this material can then be cut, trimmed, and finished into an end product.
Vacuum forming is an indispensable process in both manufacturing and packaging industries due to its versatility and efficiency. The technique allows for complex shapes with thinner wall thickness while being suitable for thicker materials – plus its cost-effectiveness makes it a popular choice for smaller production runs.

II. How Vacuum Forming Works
Vacuum forming is a process that involves heating a sheet of plastic until it is pliable, then drawing it over a mold and using a vacuum to force the sheet tightly against the mold’s contours. Here’s a step-by-step guide to vacuum forming plastic:
- Heating the Plastic Sheet: The first step in vacuum forming is to heat the plastic sheet until it becomes pliable. This is usually done using a heating element, such as infrared heaters or heating ovens. The plastic sheet is heated to a temperature just below its melting point to make it malleable.
- Placing the Plastic Sheet over the Mold:Once the plastic sheet is heated, it is placed over the mold. The mold can be made from a variety of materials, such as wood, aluminum, or plastic.
- Creating the Vacuum:Once the plastic sheet is in place, a vacuum is applied to the mold to force the plastic tightly against the mold’s contours. This is usually done using a vacuum pump or an industrial vacuum forming machine.
- Cooling the Plastic Sheet:After the plastic sheet has been vacuum formed, it is cooled to harden it. This can be done by blowing cool air over the sheet or immersing it in cool water.
- Trimming and Finishing:Once the plastic has cooled and hardened, excess material is trimmed away and any necessary finishing work is done to create the final product.

To perform vacuum forming, a few key materials are needed. These include a plastic sheet, a mold, a vacuum forming machine or pump, and heating elements. The plastic sheet used for vacuum forming is usually a a thermoplastic sheet material that becomes pliable when heated and hardens when cooled.
Overall, the vacuum forming process is a highly versatile and efficient manufacturing process that is used in a wide range of industries, from automotive and aerospace to food packaging and medical devices. There are many different types of vacuum forming machines available, from tabletop machines for small-scale production to large industrial vacuum pressure machines for high-volume manufacturing.

III. Types of Plastic Used for Vacuum Forming
Vacuum forming offers the chance to use various plastic materials with their specific properties and characteristics, including those most often seen used as plastic polymers in vacuum forming:
Polyvinyl Chloride (PVC):
PVC is a popular thermoplastic material known for its flexibility, durability, and chemical resistance. Due to its ease of processing and low cost; PVC often cuts when used for vacuum forming applications. With more than 70 colors to choose from and low processing costs compared to its alternatives; vacuum forming makes use of this versatile thermoplastic.
Polyethylene Terephthalate Glycol (PETG):
PETG plastic is an economical, lightweight, strong, and flexible choice, commonly found in food packaging, medical devices, and other applications requiring high transparency and impact resistance. PETG’s ease of processing and superior dimensional stability also makes it a popular choice for vacuum-forming applications.
Acrylonitrile Butadiene Styrene (ABS):
ABS is an impact-resistant plastic material commonly found in automotive, electronics, and consumer goods industries. Due to its lightweight structure and exceptional impact resistance properties, ABS makes an excellent material choice for vacuum forming applications.
Vacuum forming plastic sheets can vary in thickness depending on their intended use and material properties. Thicker materials may be necessary for parts that must withstand higher stresses or impacts, while thinner sheets may offer greater flexibility. The melting temperature of plastic materials also plays a crucial role as it will dictate what temperature the plastic must be heated to for vacuum forming to take place.

IV. Stages of Vacuum Forming
The vacuum forming process can be broken down into five key stages: heating, vacuum forming material itself, cooling, trimming, and finishing. Here’s an overview of each stage:
- Heating:In this stage, the plastic sheet is heated to its forming temperature, which is just below its melting point. This makes the plastic sheet pliable and able to stretch over the mold.
- Forming:Once the plastic sheet is heated, it is stretched over the mold, and a vacuum is applied to draw it tightly against the mold’s contours. This creates the desired shape of the final product.
- Cooling:After the plastic sheet has been formed, it is cooled to harden it and retain its shape. This can be done by blowing cool air over the sheet or immersing it in cool water.
- Trimming:Once the plastic has cooled and hardened, excess material is trimmed away from the final product.
- Finishing:The final stage of vacuum forming involves any additional finishing work that may be required, such as polishing or painting the surface of the product.
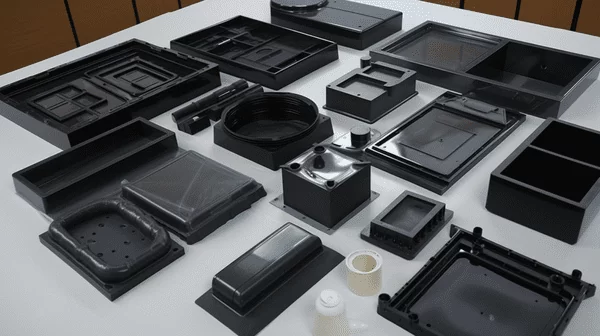
It is worth noting that there are some key differences between the vacuum forming mold, and pressure forming. While vacuum forming relies on the force of the vacuum to draw the plastic sheet over the mold, pressure forming uses air pressure to force the plastic sheet onto the mold’s contours. This results in a product with sharper corners and greater detail, but also requires a more complex mold and a more expensive pressure forming machine. Vacuum forming, on the other hand, is simpler and more cost-effective, making it a popular choice for small-scale production.

V. Vacuum Forming Tools and Machines
To perform vacuum forming, several tools and machines are needed, including a vacuum forming machine, heating elements, and various accessories. Here is an overview of some of these key tools:
Industrial Vacuum Forming Machines:
Specifically tailored for large-scale production, industrial vacuum forming machines feature automated controls, multiple heating zones, and high capacity vacuum pumps that make these machines highly productive.
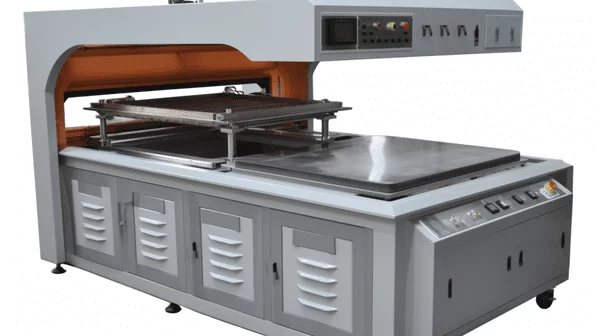
Tabletop Vacuum Forming Machines:
These smaller and more cost-effective alternatives to industrial vacuum forming machines make them an attractive option for hobbyists, prototyping, and small-scale production applications. Most models require more user input and need manual operation compared with industrial machines.
Vacuum Pump and Reservoir:
Vacuum forming requires both a vacuum pump and reservoir as integral components, with the latter serving to store vacuum pressure to maintain an even level during forming processes. The former provides the force required to draw the plastic sheet over the mold while creating vacuum pressure; both components play key roles in providing consistent vacuum levels during this step of formation.
Plug Assist:
This tool assists in the formation of complex shapes by applying additional pressure during the forming process, either manually or automatically controlled.
Mechanical Trim Press:
This tool is used to trim excess material from finished products once they have been formed. It can either be manually or automatically operated and helps ensure consistent and precise trimming.
Overall, the type of vacuum forming machine and tools required will depend on your particular application and production needs. Industrial machines tend to be best for high-volume production needs while tabletop machines or DIY kits may better meet small-scale production and prototyping.
VI. Applications of Vacuum Forming
Vacuum forming is an extremely versatile manufacturing technique used in various fields ranging from automotive and aerospace to food packaging and medical devices. Here are some common applications of the vacuum forming process:
Food Packaging:
Vacuum forming is frequently employed to craft custom shapes and sizes that can accommodate specific food products better through vacuum forming. This technique provides food companies with more space-efficient storage containers that fit better under refrigeration.
Spare Wheel Covers:
Vacuum forming is often employed within the automotive industry to produce spare wheel covers and other interior components, due to its ability to form complex shapes with thin walls that fit within tight spaces.

Shower Trays:
Vacuum forming can also be used to create shower trays and other bathroom fixtures due to its ability to create products with nonporous surfaces that are simple to maintain and keep clean.
Vacuum Forming Medical Devices:
Vacuum forming can be an excellent method for producing custom-fit orthotics, prosthetics, and other medical devices that conform closely to each patient’s body and offer light yet durable construction. This enables it to produce products that are lightweight yet sturdy – essential traits for durable medical devices that allow users to adapt them as necessary.
Some advantages of vacuum forming over other manufacturing processes are:
Cost-Effective:
Vacuum forming can often be more cost-effective than other manufacturing processes like injection molding or blow molding when applied to small-scale production runs.
Versatility:
Vacuum forming can be used to produce products of various complexity levels, from simple shapes to highly detailed components.
Speed:
Vacuum forming is a relatively fast manufacturing process that can produce parts quickly and efficiently, making it ideal for short production runs.
Reduce Waste:
Vacuum forming is capable of creating parts with thin walls and minimal extra material, leading to less waste than other manufacturing methods.
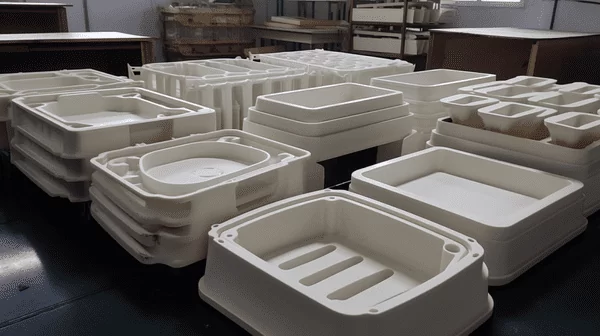
Overall, vacuum forming is a highly versatile manufacturing process used across numerous industries. It has many advantages over other production methods and can meet a wide variety of production requirements.
Conclusion
Vacuum forming is an efficient manufacturing technique used to craft plastic products from food packaging containers and spare wheel covers to shower trays and more. The process involves heating plastic sheets until they become malleable before stretching them over molds using vacuum form technology and pulling tight against their contours for tight seal.
Vacuum forming offers many advantages over conventional manufacturing techniques, including cost-effectiveness, versatility, speed and reduced waste. As such it has found use across numerous industries – automotive, aerospace, medical and packaging being among them.
Vacuum forming plays an indispensable role in modern manufacturing and packaging industries, helping produce products tailored to specific customer needs and requirements. It provides an efficient means of creating custom-fit components and producing items with pinpoint precision and accuracy.
Overall, vacuum forming is an efficient and useful manufacturing technique, one mold that will remain an integral component of modern manufacturing and packaging industries.