Introduction
When it comes to manufacturing plastic parts and components, vacuum forming stands out as a cost-effective and versatile technology. This process, also known as thermoforming, involves the transformation of a heated sheet of plastic into a three-dimensional shape using vacuum pressure. From custom packaging and automotive interior components to intricate prototypes, vacuum forming plays a pivotal role in various industries.
The significance of vacuum forming lies not only in its affordability but also in its ability to cater to a wide range of applications. However, one common goal unites manufacturers across industries: creating a seamless vacuum-formed part. The seamless finish is more than a matter of aesthetics; it’s a mark of quality and functionality. In this article, we will delve into the intricacies of vacuum forming, exploring the steps and techniques required to achieve the elusive goal of creating a seamless thermoformed plastic parts.
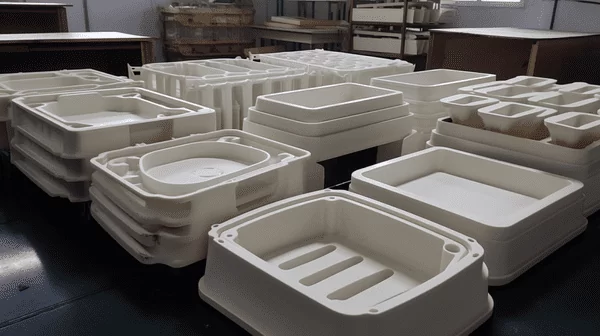
II. Understanding Vacuum Forming process
A. What is Vacuum Forming?
Vacuum forming is a plastic manufacturing process that involves the transformation of a heated sheet of plastic into a three-dimensional shape by using vacuum pressure. This process, sometimes referred to as thermoforming, is widely used in industries such as packaging, automotive, signage, and beyond.
In simpler terms, vacuum forming begins with a sheet of plastic that is heated until it becomes pliable. This heated plastic sheet is then carefully stretched and molded over a mold or pattern. The vacuum is activated, creating suction that pulls the plastic tightly against the mold’s surface. As the plastic cools and solidifies, it retains the shape of the mold, resulting in the final product.
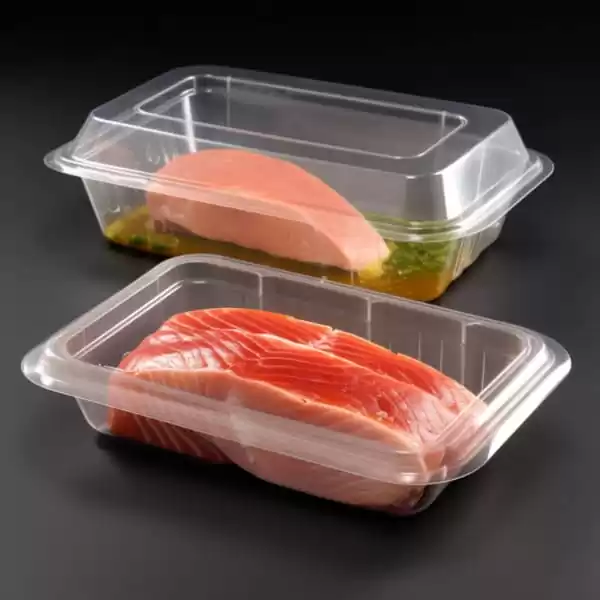
B. Advantages of Vacuum Forming
Cost-Effective Manufacturing
One of the standout advantages of vacuum forming is its cost-effectiveness. Unlike some other manufacturing processes, vacuum forming requires minimal initial investment in tooling and equipment. This makes it an accessible option for both small-scale and large-scale production. Additionally, since it doesn’t involve high-pressure molding or intricate machinery, the production costs are generally lower than alternative methods like injection molded parts.
Versatility in Applications
Vacuum forming is incredibly versatile and can be applied to a wide range of industries and product types. Whether you need to create custom packaging, intricate automotive interior components, or functional prototypes, vacuum forming has the flexibility to meet your needs. The process can handle a variety of materials, including different types of plastics, making it adaptable to various project requirements.
Understanding these key aspects of vacuum forming sets the stage for exploring how to create a seamless vacuum-formed part, a goal that combines precision and craftsmanship with the advantages this manufacturing costs has to offer.
III. How do you create a seamless vacuum-formed part?
Achieving a seamless vacuum-formed part is a meticulous process that involves several crucial steps, each contributing to the end result. Let’s explore these steps in detail:
A. Design and Prototype
The foundation for creating a seamless vacuum-formed part begins with design and prototyping. This phase serves as the blueprint for your project and plays a pivotal role in achieving a flawless finish. Here’s how it contributes:
- Role in achieving seamless results: A well-thought-out design and prototype help ensure that your final part will meet your specifications with precision. This step allows you to anticipate challenges and plan for solutions, minimizing errors in the production process.
- Utilizing CAD software: Computer-Aided Design (CAD) software is an invaluable tool in this phase. It allows you to create detailed, digital prototypes that can be refined and optimized before moving to the manufacturing stage. CAD software enables accurate measurements, intricate designs, and adjustments as needed.
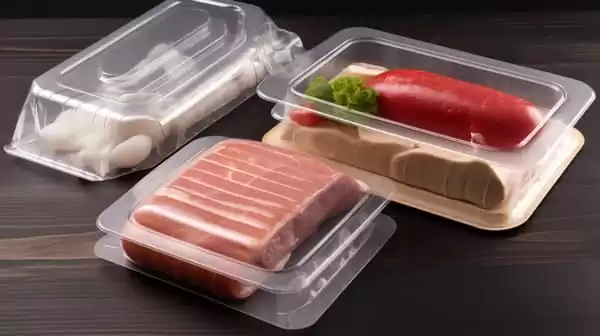
B. Mold Creation
The mold is a critical element in the vacuum forming process, particularly when aiming for a seamless finish. Consider the following factors:
- Importance of mold design: The design of your mold can significantly impact the quality of the final product. Smooth, rounded edges and minimal undercuts are essential for achieving a seamless appearance. The mold should match the desired shape of your part precisely.
- Elements contributing to a seamless finish: A well-designed mold should eliminate the need for excessive post-forming work. The absence of sharp edges and intricate features simplifies the vacuum forming process and reduces the chances of imperfections.
C. Material Selection
Selecting the right plastic material is pivotal in creating a seamless vacuum-formed part:
- Impact on the final appearance: Different materials have distinct characteristics, including transparency, texture, and heat resistance. The material you choose should align with your project’s requirements to ensure the desired appearance and functionality.
- High-quality materials for seamlessness: Opt for high-quality plastic materials. Lower-grade materials may result in inconsistencies, blemishes, or warping during the vacuum forming process, undermining your goal of seamlessness.
D. Heating the Plastic Sheet
The heating of the plastic sheet is a critical step to ensure pliability and a smooth forming process:
- Ensuring pliability for smooth forming: The plastic sheet must be heated evenly to the correct temperature, making it pliable and ready for forming. Inadequate heating can lead to uneven stretching and potential defects.
- Role of a heated sheet: The heated sheet allows the plastic to conform precisely to the mold’s shape during vacuum forming, contributing to a seamless finish.
E. Vacuum Forming
The vacuum forming process itself is where the magic happens:
- Step-by-step process: Vacuum forming involves positioning the heated plastic sheet over the mold and activating the vacuum. The vacuum pressure pulls the plastic tightly against the mold’s surface, shaping it into the desired form.
- Importance of avoiding wrinkles and air bubbles: Careful execution during vacuum forming is crucial. Any wrinkles or air bubbles in the plastic can result in imperfections on the final part, making it essential to maintain a smooth, uniform surface.
F. Cooling
After the initial forming, it’s time to cool the part:
- Setting the plastic in its final shape: Proper cooling helps the plastic solidify in its intended shape, ensuring the final product meets your specifications.
- Cooling methods: Various cooling methods, such as fans, cool air, or water baths, can be employed to expedite the cooling process and maintain the desired shape.
G. Trimming and Finishing
Once the part is fully cooled, trimming and finishing are essential for a polished appearance:
- Post-forming steps for a polished look: Carefully removing any excess material and sanding or finishing the edges contributes to a seamless appearance. Attention to detail during this phase is crucial.
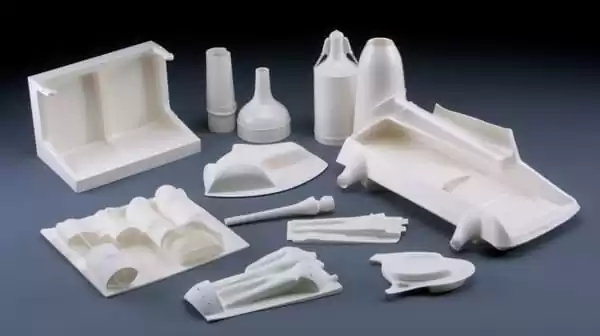
IV. What Material Can Be Used for Vacuum Forming?
In the world of vacuum forming, the choice of material is a critical decision that directly impacts the appearance, functionality, and characteristics of the final finished product. Let’s explore the range of materials that can be used for vacuum forming, the factors that influence material choice, and the characteristics of some common options:
Overview of Various Plastic Materials for Vacuum Forming
The versatility of vacuum forming is evident in its ability to accommodate various plastic materials, each with its unique properties and applications in vacuum form. Here’s an overview of some of the plastics commonly used in vacuum forming:
- Acrylic: Known for its transparency, durability, and UV resistance, acrylic is an excellent choice for products that require a clear finish, such as display cases and signage.
- Polyethylene: This widely used plastic is known for its flexibility, impact resistance, and suitability for applications like packaging and containers.
- Polypropylene: Lightweight and resistant to chemicals, polypropylene is often selected for products like medical trays and automotive components.
- Polystyrene: Offering good rigidity and ease of forming, polystyrene is a popular choice for products like food packaging and disposable utensils.
- PVC (Polyvinyl Chloride): PVC is valued for its chemical resistance and flame-retardant properties, making it suitable for electrical enclosures and plumbing components.
- PETG (Polyethylene Terephthalate Glycol): PETG combines clarity with impact resistance, making it an ideal choice for items like retail displays and protective packaging.
- ABS (Acrylonitrile Butadiene Styrene): ABS plastics are durable and offer good impact resistance, making them a suitable option for automotive interior parts and consumer goods.
Factors Influencing Material Choice
The selection of the most suitable material for vacuum forming is influenced by several factors:
- Application Requirements: Consider the specific demands of your application. Does it require transparency, flexibility, durability, or other specific characteristics?
- Material Properties: Evaluate the inherent properties of the plastic material, such as its strength, chemical resistance, and heat resistance.
- Cost: Factor in the material’s cost, as it can significantly impact your project’s budget.
- Aesthetics: Think about the desired appearance and finish of the final product. Some materials offer a clear finish, while others may have textures or colors.
Listing Common Materials and Their Characteristics
To assist you in selecting the right material for your vacuum forming project, here are some common options along with their key characteristics:
- Acrylic:
- Transparency
- UV resistance
- Durability
- Polyethylene:
- Flexibility
- Impact resistance
- Chemical resistance
- Polypropylene:
- Lightweight
- Chemical resistance
- Stiffness
- Polystyrene:
- Easy to form
- Rigidity
- Clarity
- PVC (Polyvinyl Chloride):
- Chemical resistance
- Flame retardant
- Durability
- PETG (Polyethylene Terephthalate Glycol):
- Clarity
- Impact resistance
- Versatility
- ABS (Acrylonitrile Butadiene Styrene):
- Durability
- Impact resistance
- Versatility
Choosing the right material ensures that your vacuum-formed part meets the specific requirements of plastic parts for your project while delivering the desired appearance and performance. Understanding the characteristics and applications of these plastics is key to making an informed decision.
In the next section, we will further explore the advantages of vacuum forming and how it can be leveraged in various industries and applications.
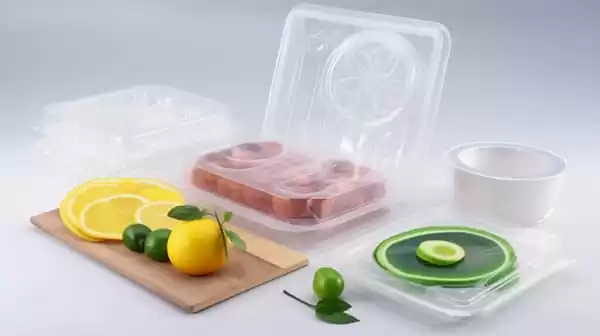
V. Conclusion
Creating a seamless vacuum-formed part is an art that combines precision, meticulous planning, and a deep understanding of materials and processes. Throughout this journey, we’ve explored the intricacies of vacuum forming, from its definition to the crucial steps involved in achieving seamlessness.
In closing, we invite you to apply the knowledge and insights gained from this article to your manufacturing endeavors. By embracing the art of vacuum forming and adhering to the principles of quality and precision, you can consistently create seamless, high-quality products that make a positive impact in a wide range of industries and applications.