The world of manufacturing is constantly being pulled in two different directions: on one side there’s the need for new technology; on another, consumers wanting things done faster than ever before. Heavy gauge thermoforming has managed to bridge these competing demands well enough that it now offers unparalleled benefits like adaptability alongside speediness – all while keeping costs low!
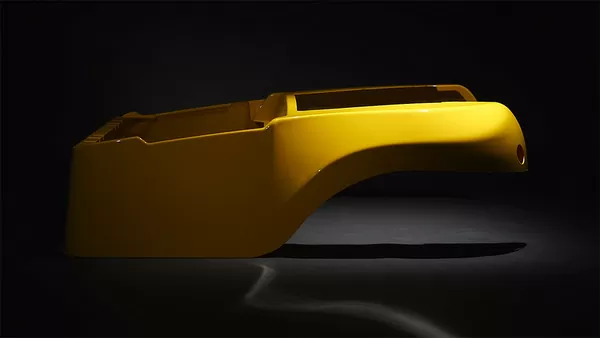
If you’re not familiar with what heavy gauge thermoforming does exactly; don’t worry because we’re about tell ya: This process involves heating up a piece plastic sheet until it becomes malleable enough then adsorption this heated plastic over top an object (or into its hollowed-out shape) by vacuum adsorption… or else adding some extra umph via air pressure too if necessary. Choosing whether or not invest money into adopting heavy-gauge-thermoform manufacturing processes shouldn’t just be seen as something that’ll impact finances today–instead realize making such commitment might end altering overall path taken by your firm altogether. But what exactly makes heavy gauge thermoforming so advantageous, and why should manufacturers take a closer look at integrating it into their operations?
In today’s fast-paced world of manufacturing, being efficient and adaptable is key if you want to do well. There’s a new technique that has got people excited: heavy gauge thermoforming. It can be used in many different types of industry because it makes things quickly – but what sets this way of working apart from others like it?
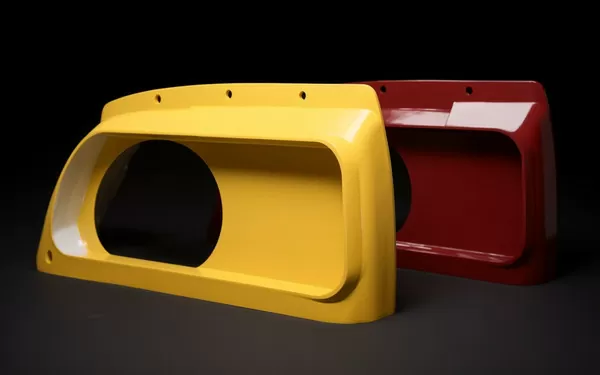
In this blog, we’ll explore why manufacturers are avidly investing in heavy gauge thermoforming, understanding its benefits, and the potential it holds for those looking to step ahead in the race to better production processes.
Thermoforming Process
Thermoforming is an incredibly useful manufacturing process where a moldable flat thermoformed plastics sheet (or thermoplastic material) gets heated to become pliable. It’s then formed into a specific shape, cooled and trimmed to make stuff like packaging trays or blisters for any industry.
There are several thermoforming methods used in actual production: differential pressure molding, cover molding, plunger-assisted molding, suction back molding, opposite mold molding, female mold and male mold thermoforming, thin gauge thermoforming, heavy gauge(thick gauge) vacuum forming and twin sheet forming.
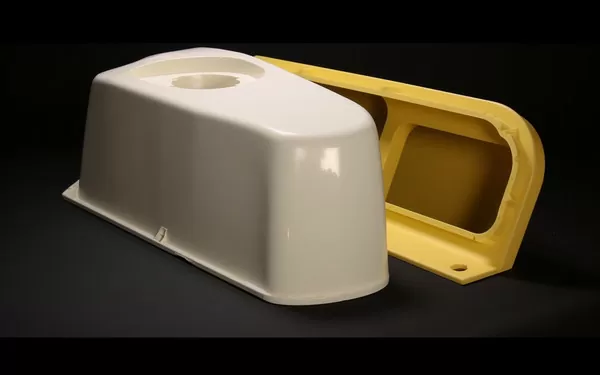
Heavy Gauge Thermoforming
When we talk about “heavy gauge,” we’re not just talking about how big a piece of plastic is. We’re also referring to how strong it is once it’s been made into something. Heavy gauge pressure formed products works well when you need to produce big pieces that will be used in tough conditions, and which will last a long time.
Thick-gauge thermoforming makes items that have thick walls and are stable within their dimensions: These are properties that can make them structurally sound enough for use in automotive industry, hospitals and custom thermoforming – areas where thin gauge thermoforming items simply would not be up to job because they lack robustness overall.
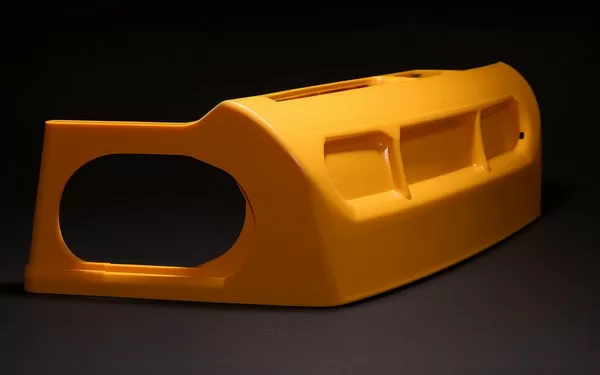
Heavy gauge thermoforming stands out in terms of material thickness. When it comes to sheets, heavy gauge thermoforming uses ones that are usually between 0. 060 inches and 0. 500 inches thick. This type of thermoforming is ideal for creating strong and long-lasting products like car panels, pallets or fridge linings.
Thermoforming Design Possibilities
Before the development of heavy gauge thermoforming, intricate shapes could only be made using costly and time-consuming methods like metal forming or fiberglass lay-up. Heavy gauge thermoforming changed all that: now manufacturers can create custom configurations affordably. This opens up new possibilities – designing plastic components specifically to improve how they work (or how good they look) compared with rivals’ products.
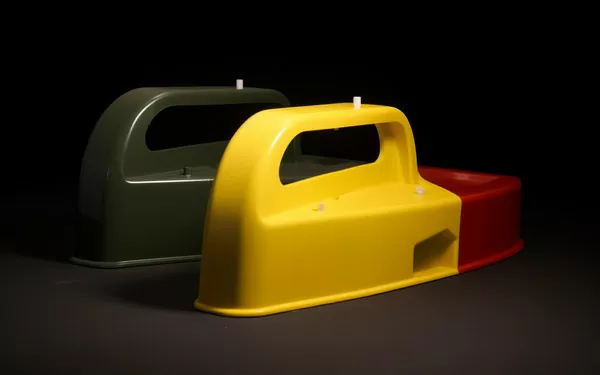
Streamlined Production and Rapid Prototyping
Heavy gauge thermoforming allows for an impressive decrease in the time it takes to complete a job. In sectors where it is crucial to get products out quickly, this method shaves hours or days — sometimes both — off the development cycle.
Plus because prototypes can be made fast and accurately too thanks again to heavy gauge thermoforming designers have more opportunity than ever before for refining things; they no longer need wait ages just see if their tweak worked! So when tests have been passed with flying colours there’ll be nothing stopping production lines from going into action straight away either.
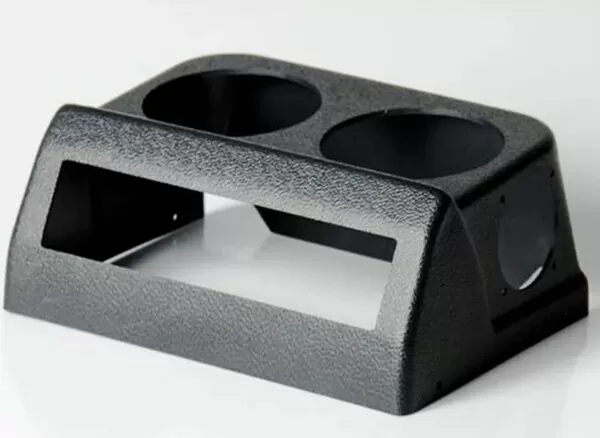
Cost-Effectiveness Through Reduced Tooling
Heavy gauge thermoforming offers a major benefit: a substantial decrease in tooling expenses. Compared to molds used in blow molding or injection molding, those used in this process are usually cheaper. As a result, manufacturers can make changes more affordably and easily after their initial investment—something that appeals to companies looking for ways control expenditures while still maintaining high standards of quality design.
Strengthening Sustainability Efforts
The world manufacturing sector is more and more focusing on sustainability – with heavy gauge thermoforming playing its part. Not only does this technique have substantial material utilization rates, but it also produces hardly any waste materials; plus it can employ recyclable plastics too.
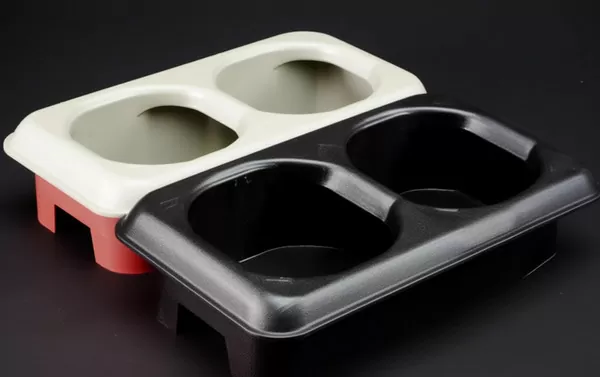
By choosing this method firms can therefore support sustainable procedures while still making high-quality products capable of competing performance-wise: good news all round for profits as well as the planet!
Durability and Strength
There is no comparison to the durability offered by items made using thick-gauge thermoforming. This technique enables the production of components with different levels of thickness—customizable features that are necessary in order for them stand up under duress or continual use. Such resilience is vital when these plastic parts are placed within demanding settings such as those seen with cars (both inside/out) plus industry too!
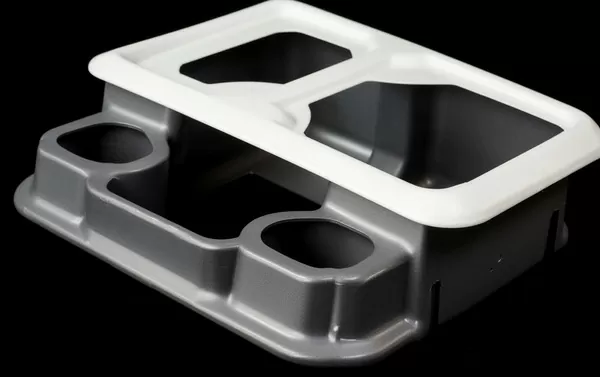
Navigating Material Selection for Optimal Performance
In heavy gauge thermoforming, selecting the right material is vital because it affects how well the finished product works. There are lots of different plastics to pick from – like ABS, polycarbonate or HDPE – and each one has its own strengths, each offering unique strengths including impact resistance, chemical tolerance, and UV stability. By choosing carefully which sort of plastic best suits their needs, manufacturers can make sure their products do exactly what they’re meant to.

The Human Element in Thermoforming
While technology plays a significant role in heavy gauge vacuum forming, it cannot guarantee success on its own. The operation of experienced human operators is invaluable here: by making subtle adjustments throughout production, they can control how materials are dispersed, how thick they become and even their texture. It is this human element which guarantees not only that every single part will be of the very highest quality, but also identical to all others too – something very hard indeed for alternative manufacturing process (no matter how sophisticated).
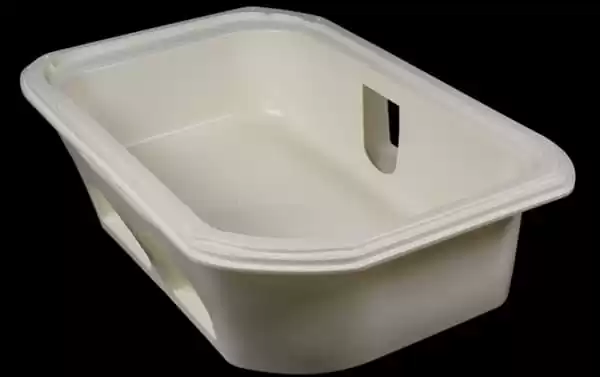
Market Flexibility and Customization
Manufacturers can use heavy gauge pressure forming to meet the current desire for customization and personalization in the market. They are able to be flexible with both the size and shape of parts –– even making things that use multiple materials at once if they have appropriate machinery. This is important because being able to customize products lets companies react quickly when there are changes in what people want to buy: It keeps them competitive as trends shift towards ever-more personalized goods across all industries.
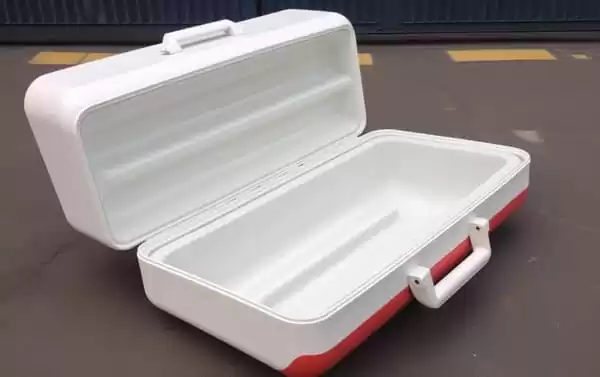
Heavy Gauge Thermoforming and the Digital Thread
Even as Industry 4. 0 technologies transform the field of manufacturing, heavy gauge thermoforming is keeping pace. The digital thread idea–that data should flow seamlessly through a product’s development–fits this type of thermoforming well. Indeed, digital tools can help streamline and fine-tune each step in making something from heavy plastic sheets: from designing it using CAD/CAM software to checking for flaws once production is underway.
Case Studies and Success Stories
There is no better way to understand the benefits of thick gauge thermoforming than by looking at the success stories of companies that have used it. Many different industries have published case studies showing how this method can help businesses grow: by getting products to market faster, making them better and more cheaply than before or other ways entirely. By examining these examples, manufacturers can gain insight into how heavy gauge thermoforming might benefit their own operations.
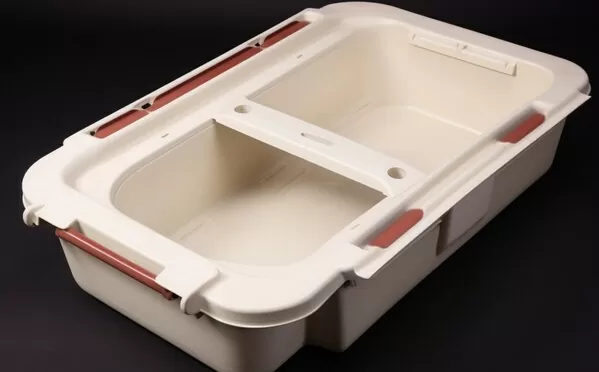
Overcoming Challenges in Thermoforming
Although there are numerous benefits to implementing heavy gauge thermoforming, it does come with its own set of obstacles. Companies looking to adopt this technology will have to think about things like purchasing new heavy gauge thermoforming equipment; training their staff how use it correctly (which could mean bringing in outside experts); possibly even changing around some aspects of how products get made altogether! But don’t fret too much because if approached strategically–and with an eye towards the future benefits for all involved parties–each barrier can be overcome successfully: paving a path toward boosted manufacturing prowess.
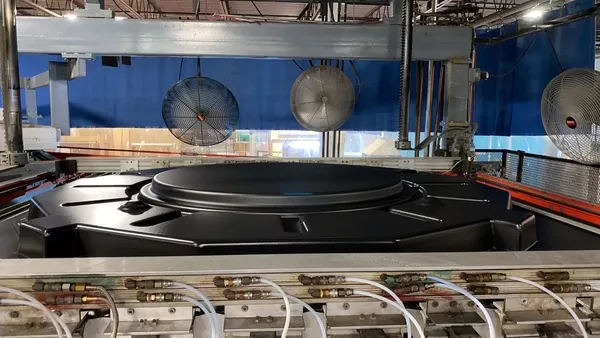
Implementing Thermoforming in Your Strategy
If you’re considering incorporating heavy gauge thermoforming into your manufacturing strategy, these are the key steps to take:
1. Analysis of Product Requirements: Review your part’s specs and determine whether heavy gauge thermoforming aligns with its desired characteristics and volume needs.
2. Selecting the Right Material: Material choice is critical to product performance; work closely with suppliers to pick one that meets criteria.
3. Mold Design and Fabrication: Work with thermoforming experts on designing/fabricating tooling that best suits production needs.
4. On-Demand or Batch Production: Decide if it’ll be more beneficial for you to produce items on an as-needed basis or by batches.
5. Quality Assurance: Implement stringent quality checks so all parts meet high standards; this will help prevent costs associated with defects later downstream.
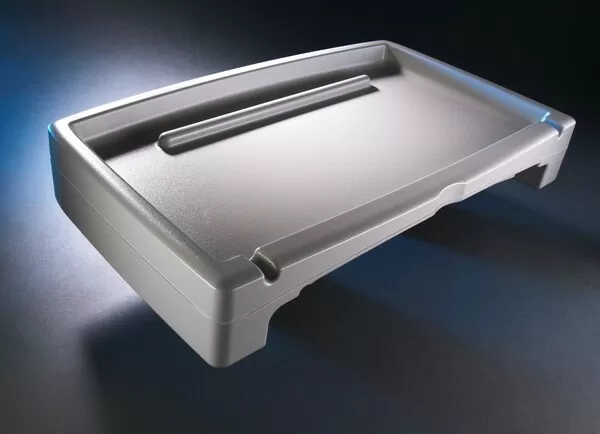
The Future of Manufacturing with Heavy Gauge Thermoforming
As we look to the future, it is clear that heavy gauge thermoforming will become even more important in manufacturing. Thanks to progress in materials science, controlling processes better and using robots more often, this technique is developing further all the time. As a result, its users can make things with an amazing level of accuracy as well as speed – not to mention coming up with new ideas too! Any manufacturer which understands these possibilities now (and takes advantage) should be leading their field in years to come.
To sum up, manufacturers should view heavy gauge thermoforming as more than just a process. It opens up new possibilities for them. Such efficiency! Such flexibility! This technique enables companies to make strong, top-quality components quickly—something no factory should be without these days. Manufacturers who grasp this concept will be able to completely transform how they operate: giving them an edge when competing worldwide – and ensuring their prosperity over time too!
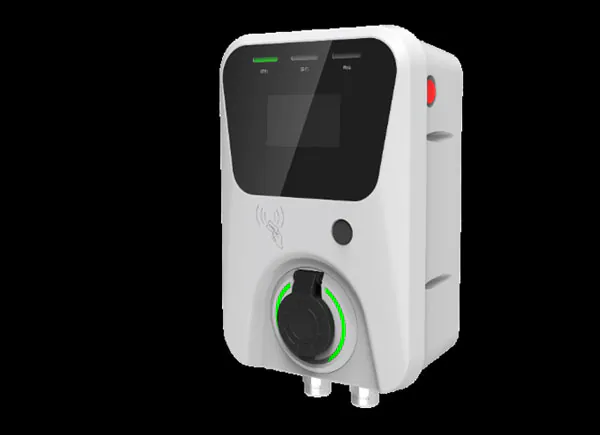
Conclusion
It’s not just a passing fad – heavy gauge thermoforming offers lasting solutions for resilient, agile manufacturers looking to tackle industry challenges head-on. This innovative process keeps costs down and opens up design possibilities too: no wonder it has become such an integral part of modern-day production methods!
If a manufacturer is considering their choices, they can’t afford to overlook heavy gauge thermoforming. It gives them exactly what today’s market calls for – plus a competitive advantage that’s hard to beat! Thermoforming really does have it all: strength; intricate design work; and the promise of future triumphs in industry and commerce alike.
If you invest in this technology, you will be investing in the future. This means giving your business the tools it needs to make ground-breaking products – ones that perform better than anything rivals have to offer.
The heavy gauge thermoforming revolution is underway—are you ready to form the future?