Given the hectic nature of daily commutes, passenger cars may sometimes go unnoticed, but technology developers may not feel the same way. They focus on one thing in particular: heavy gauge thermoforming. Thanks to this manufacturing technology, tomorrow’s buses could look completely different to today’s – which has major implications for other forms of public transport too!
Passenger comfort and safety are the most important factors in today’s public transport industry. The vehicle used plays an important role in ensuring both qualities, and one manufacturing technique helps achieve this: heavy gauge thermoforming. It’s a complex process in which the plastic is molded into strong, detailed shapes that can incorporate many different aspects when designing a transportation system.
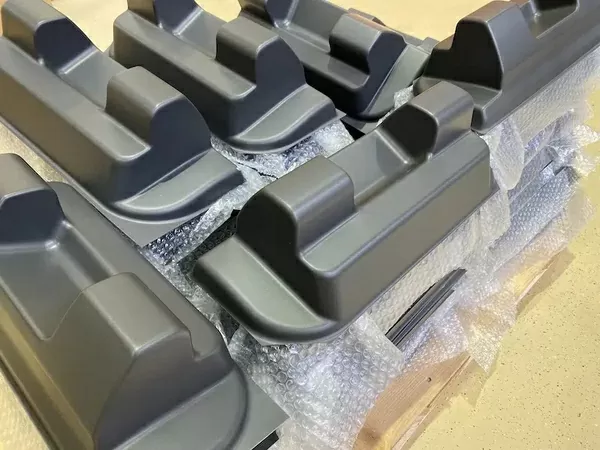
Today we’re going to take a closer look at the world of heavy-duty thermoforming – specifically the passenger car industry. We’ll detail the ins and outs of this manufacturing process and show how it’s revolutionizing transportation by producing buses that are better looking, safer, greener, and more durable than ever before.
In this detailed exploration, we will delve into the area of heavy-duty thermoforming as it relates to passenger car design and manufacturing. We will look at its impact on everything from sustainability and visual appeal to mechanical functionality, all the way to passenger comfort in transport environments. Every aspect of these important vehicles is worth exploring!
To fully grasp current advances in passenger car production, we must first understand what heavy gauge thermoforming is and why this process is integral when it comes to creating roadworthy vehicles that can travel thousands of miles with a steady stream of passengers.
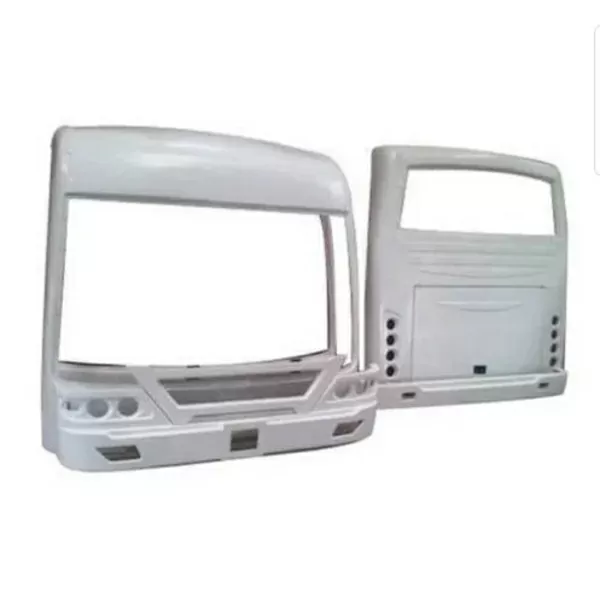
Heavy Gauge Thermoforming
Thermoforming is a type of plastic manufacturing that is used specifically to shape rigid sheets made of thermoplastics. To do this, manufacturers heat these sheets until they are ductile enough to be shaped; when cooled again (while still stretched over the mold), the now-hard material will take on its new shape entirely. It works great in some cases, such as using a giant panel to make a curve-hugging bus side – because the thermoformed part is both big and curved!
Thermoforming is a flexible technology used to transform flat plastic sheets into 3D objects and comes in different types. Heavy gauge thermoforming specifically refers to molded plastics that are much thicker than the plastic in thin gauge thermoforming.
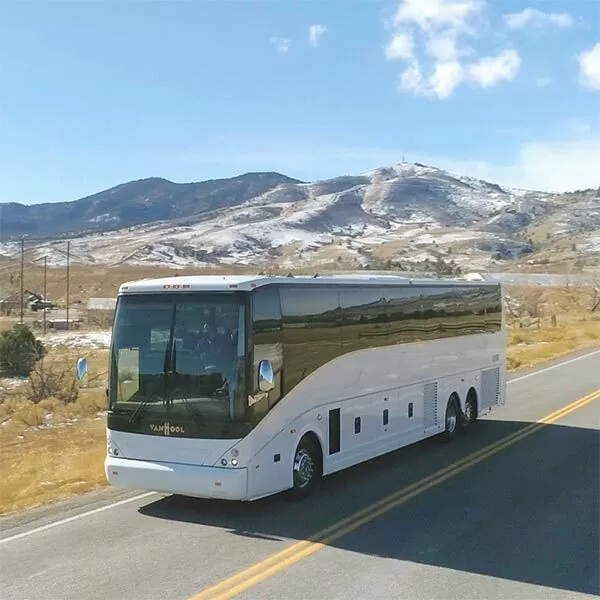
This process is useful when the sturdiness of the plastic products is important, as it produces a product that can withstand a lot of wear and tear. This is why heavy gauge thermoforming works well in the harsh world of public transportation: if you need to make something sturdy for a bus or train (or really anything similar), this might be just what you’re after.
The Thermoforming Toolkit
Thermoforming relies on a series of essential tools and machinery:
Tooling: Molds, produced typically from aluminum, wood, or composites, are used to shape the heated materials.
Heating Elements: Ovens or infrared heaters are used to warm the plastic sheets uniformly.
Vacuum or Pressure Systems: For creating the necessary forces to shape the material within the mold.
Cutting Devices: Once formed, the material needs to be trimmed to its final size.
Cooling Systems: To thermally stabilize the formed parts.
These elements combined allow manufacturers to create intricate, large-scale components with impressive efficiency.
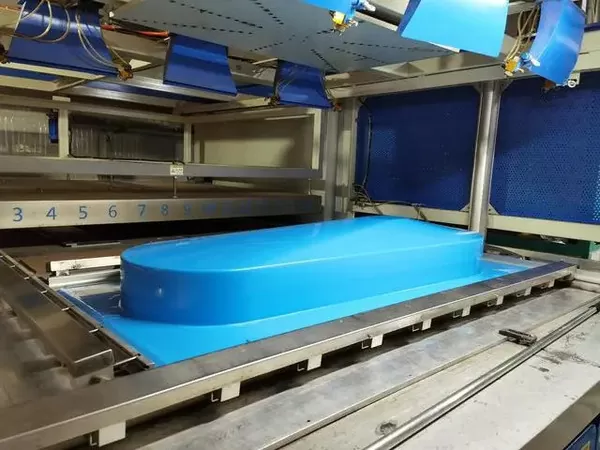
The Heavy Gauge Difference
Heavy gauge thermoforming is a type of plastic sheet molding that focuses on making parts thicker than 3mm. This manufacturing process produces components that are strong enough to meet the structural requirements faced by buses, while also being durable enough for year-round use in any climate. It’s not just about looks; heavy gauge thermoforms also perform extremely well from a functional perspective – being very strong for their weight and overall solid throughout use!
In the transportation industry, vehicle components need to withstand the wear and tear of daily driving, and large-scale thermoforming may mean more durability for various vehicle components.
The process combines the best attributes of thermoformed plastic—the ability to be molded into complex shapes at low cost—with a high-strength material that can withstand long-term wear and tear.
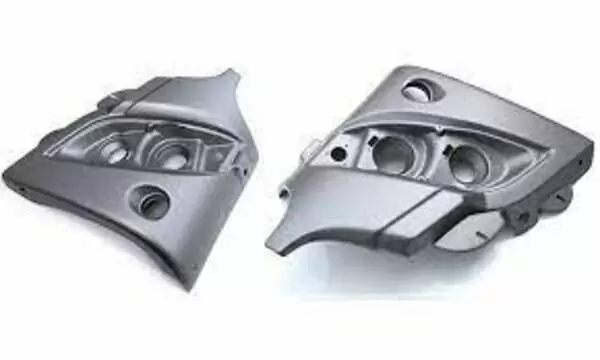
Enhancing Design Freedom for Aesthetics and Functionality
A major advantage of thermoforming is the freedom it offers in terms of design and aesthetics. Unlike some other manufacturing processes, thermoforming can be used to create complex shapes – a big advantage for buses that require streamlined or even aerodynamic designs! This flexibility, combined with the creativity of designers, will produce vehicles that not only look great but perform well; they also do what is intended.
Integrating Form and Function
Thermoformed parts can be tailored to integrate functional elements seamlessly into the bus’s design, such as:
Aerodynamic Features: Curvatures and contours designed to reduce air resistance and improve fuel efficiency.
Structural Components: Strong, one-piece parts that contribute to the bus’s overall structural integrity.
Interior Molding: Custom shapes that align with space utilization needs and provide for unique passenger experiences.
With thermoforming, buses are not just boxes on wheels but highly engineered systems that balance form and function.
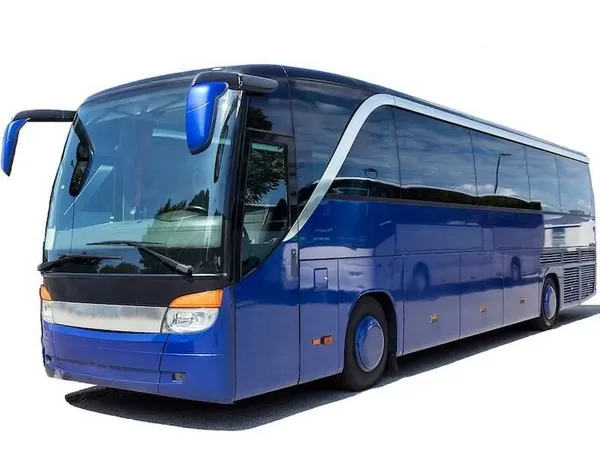
The Economics of Heavy Gauge Thermoforming
In addition to being able to create impressive designs, vacuum forming process is also an attractive option from an economic perspective. This method is less expensive than injection molding because there are not as many tools involved, are there any changes that need to be made? This is no problem either (notable when speed matters most). Plus: usually cheaper! Plus, their size is lighter and stronger, which means loads can be larger without damaging anything.
Fueling Fleet Upgrades and Expansions
For transit authorities and bus manufacturers, the cost savings can be significant, enabling them to:
Maintain Competitive Pricing: In an industry driven by tenders and bids, a cost-effective manufacturing process can be a competitive differentiator.
Facilitate Upgrades: Lower production costs can catalyze the integration of advanced features and technologies within buses.
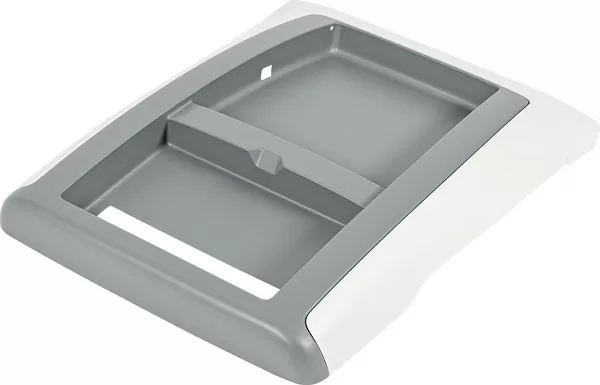
Accelerate Fleet Expansions: Reduced production times mean more buses can enter service sooner, supporting urban growth and public transit sustainability.
The financial advantages of thermoforming make it a pivotal tool in the innovation and growth strategies of bus manufacturers worldwide.
Applications of Heavy Gauge Thermoforming in Passenger Buses
Exterior Applications
Front and Rear Bumpers
Heavy gauge thermoforming is extremely important in bus manufacturing for a number of reasons. The most important of these are the front and rear bumpers: they need to be able to withstand impacts without cracking, while also being as light as possible so that they don’t unnecessarily weigh the vehicle. Bumpers manufactured through this process offer excellent crash protection – the materials used are indeed tough stuff!
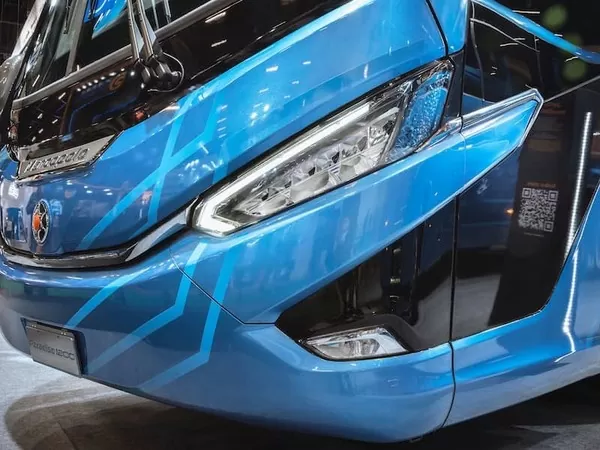
Roof Covers
Heavy-gauge thermoformed semi-monocoque components for bus roofs are not only strong and durable, but also simple to produce. These exterior components not only protect against the elements; They also help make the vehicle sufficiently aerodynamic to reduce fuel consumption – important when making large journeys between stops.
Side Panels
Cost-efficiency and ease of replacement are at the heart of heavy gauge thermoformed side panels. If damage does occur, operators can replace thermoformed panels faster and cheaper, which is good news for anyone worried about costs and sticking to schedules.
If damage occurs, replacing thermoformed panels is a less labor-intensive process, reducing downtime and costs to the operator. This quick turnaround also enhances the ongoing operations of the fleet, which is crucial for the rapid movement of urban traffic.
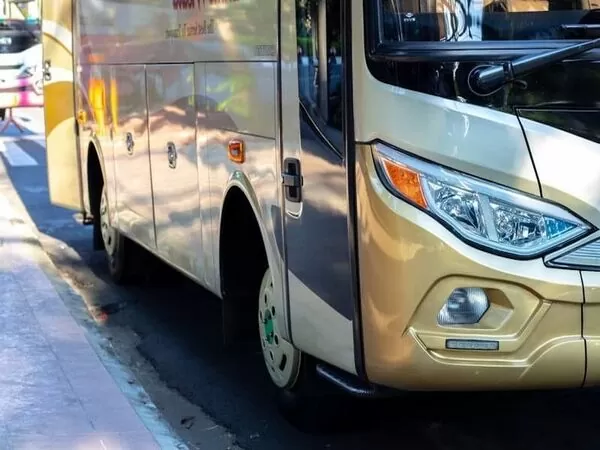
Interior Applications
Seat Components
Providing a comfortable ride for passengers is critical, and thick gauge thermoforming can provide seat components that both increase comfort and extend service life.
What’s more is that thanks to customization options within its manufacturing process itself (thermoforming), the company can also adapt to different ergonomic designs, making passengers feel at ease throughout the journey.
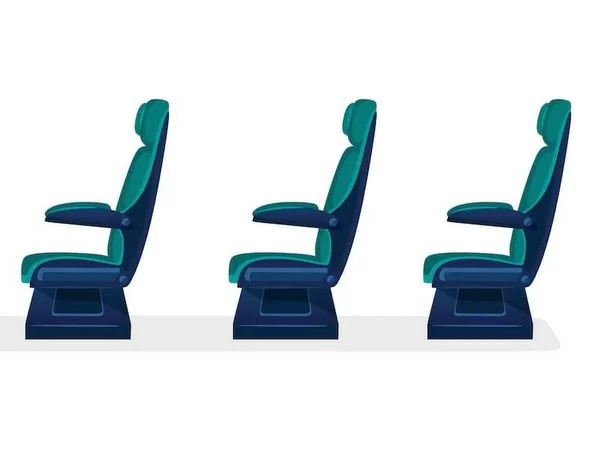
Dashboard and Control Panels
For manufacturers who want to stand out, the ability to customize their products is critical. Heavy gauge thermoforming can be used perfectly when instrument panels and control panels – not only giving them the opportunity to express their personal style, but also integrating with state-of-the-art functionality, giving the driver more say in how things work rights while providing passengers with a modern and enjoyable travel experience.
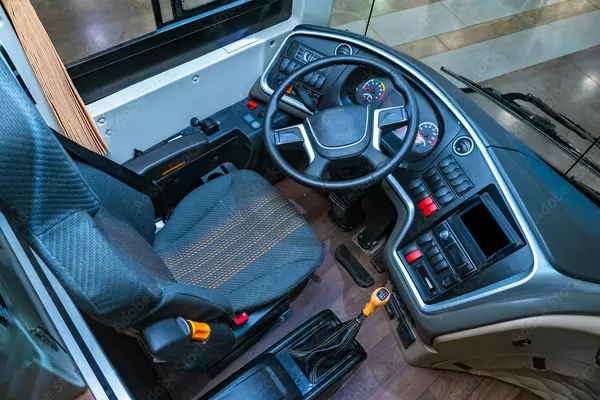
Internal Cladding and Trim Parts
Passengers’ impressions of the vehicle’s overall quality largely depend on the atmosphere inside the bus. By installing interiors with cladding and trim made from heavy gauge thermoforms, you can add sophistication – as well as improve appearance (aesthetics) and sound (acoustics).
But there’s more: Because these same parts deliver strong performance and attractive looks over time, they offer more than just durability.
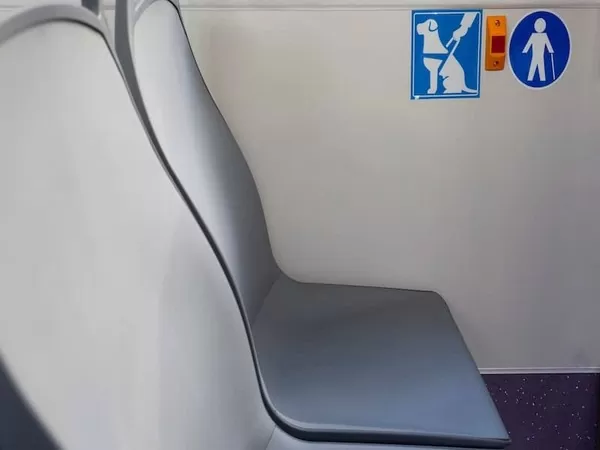
Streamline Aesthetics and Advanced Airflow
The design of bus body panels and interior walls requires finding the right balance between functionality and appeal. This is where heavy gauge thermoforming process really comes into play, it can create smooth and uninterrupted large formats that are not only strong and durable, but also help reduce wind resistance, meaning the vehicle only needs less fuel. These same sculpted parts not only make the bus more aerodynamic (and therefore quieter inside), they also ensure that air flows in a controlled manner throughout the interior of the cabin: something passengers will appreciate when driving at high speeds!
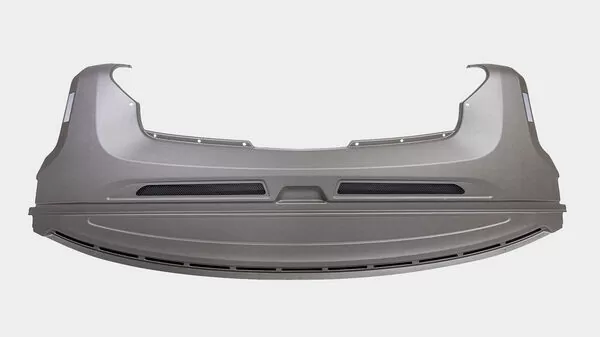
In Terms of Passenger Experience
Ultimately, the true test of any advancement in passenger car design is how it feels to the people riding inside. Thermoformed parts serve a variety of functions that impact passenger comfort and well-being, both of which should never be underestimated.
Acoustics and Climate Control
Thermoformed panels can help create a more comfortable journey by reducing noise levels within the passenger area. They also play an important role in temperature control of the climate system, meaning buses equipped with this technology use less fuel overall.
Seating and Stowage
Thermoformed components are versatile enough to create comfortable and space-saving seating arrangements and storage options in the cab and passenger areas; they can even be molded around entire walls if necessary.
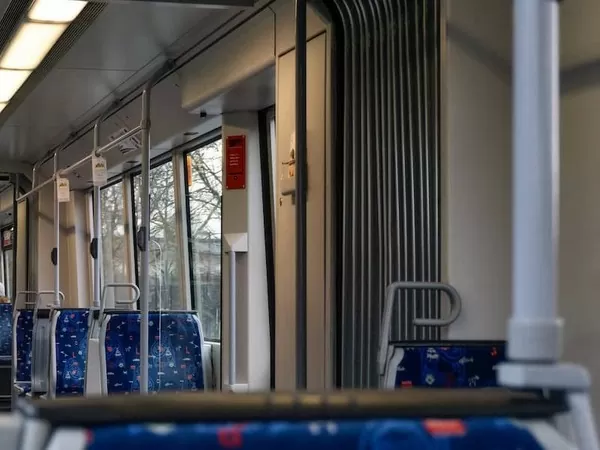
Accessibility
The ability to thermoform to produce strong, large structural components is critical when creating easy-to-use features such as ramps or handrails, which need to be both durable and large enough for everyone to use. This also means designing the wheelchair platform as a standard accessory so that it can be easily used by any passenger who needs it.
Commonly Used Materials in Heavy Gauge Thermoforming for Passenger Buses
ABS (Acrylonitrile Butadiene Styrene): ABS was chosen because it is strong, can withstand rough handling well, and is highly impact resistant. It is used on many parts of passenger car exteriors, interiors, dashboards, seat components and provides an excellent surface finish.
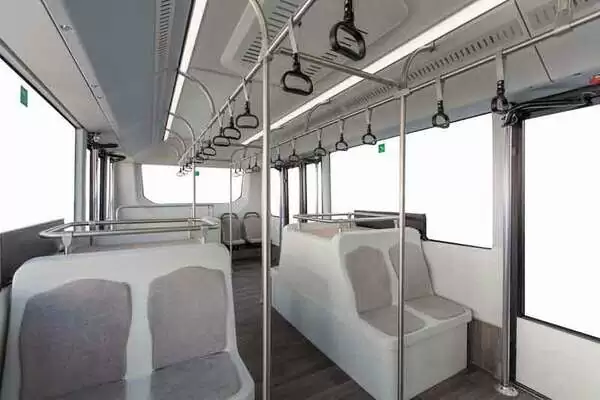
Polycarbonate: Polycarbonate is used where good transparency and high impact strength are required, such as window panels, protective covers, or light fixtures where visibility is important.
HDPE (High Density Polyethylene): HDPE is valued for its strength to density ratio, which allows manufacturers to create parts that are strong but not too heavy. Some exterior body panels and storage bins on buses may be made of HDPE.
TPO (Thermoplastic Polyolefin): Has good chemical resistance, is durable over a wide temperature range without degrading, and is able to flex on impact without breaking; TPO can be used on bumpers/fenders or other exposures Vehicle dashboard depending on weather conditions and road use/abuse factors!
PVC (polyvinyl chloride): PVC’s flame retardant properties and chemical/corrosion resistance mean that it is often chosen when a material such as conduit for running electrical cables is required.
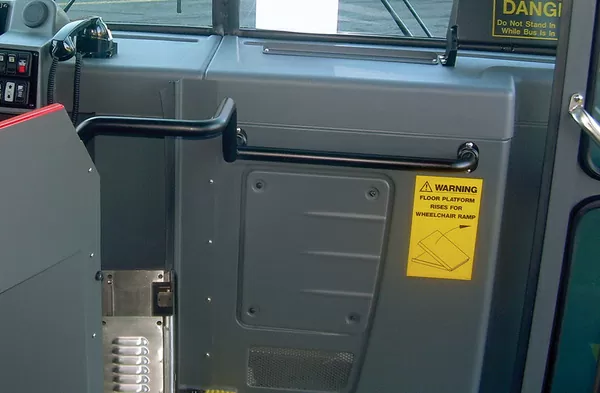
Reimagining the Lifespan of Buses
Through thermoforming, buses are not only more eco-friendly during production but also more durable throughout their operational life:
Reduce maintenance
Thermoformed parts are durable and require less frequent repairs. Using these components on buses could mean they can run longer without maintenance work, saving time and money.
Recyclability
When buses reach the end of their useful life, those equipped with thermoformed parts can be recycled more easily—a process that’s better for the environment overall.
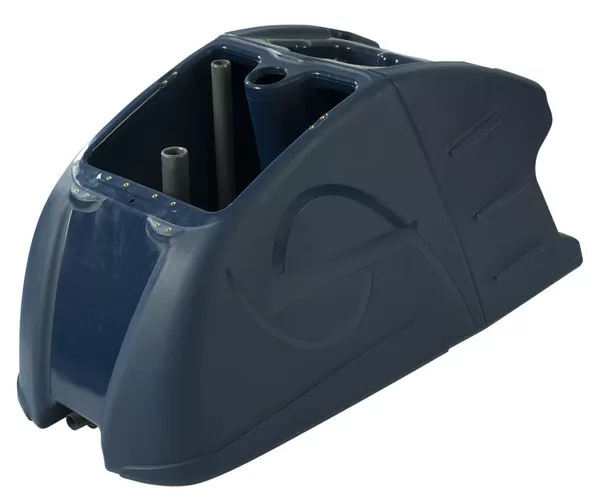
Secondary Market
Because the overall quality of assemblies manufactured by plastic vacuum forming tends to be higher, there may be opportunities to resell or repurpose them in secondary markets (such as selling bus parts to people not involved in transportation). This way, energy/materials are fully utilized even after first use!
Durability meets Sustainability
Large thermoformed parts have an impressive quality: they can last a long time without losing any toughness. Even when faced with bumps, knocks and bad weather, these parts mean your coach will look good and run well for many years. But it’s not just their durability, heavy gauge thermoforming also offers sustainable advantages. Many thermoformed materials are recyclable, thus closing the life cycle of plastics used in buses and significantly reducing the environmental impact of public transport.
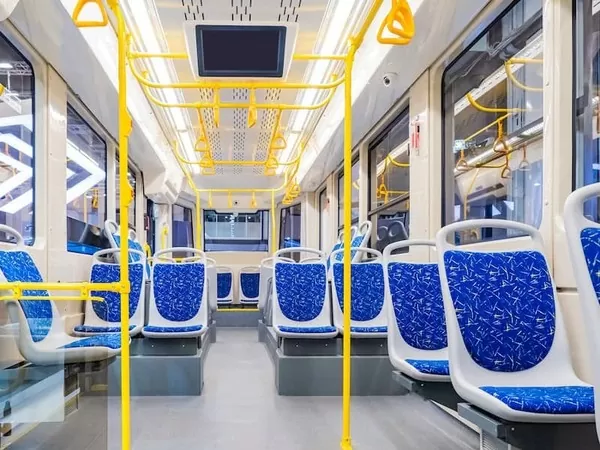
Future Trends: Technology, Innovation, and Sustainability
The transportation industry’s use of heavy gauge thermoforming is likely to become increasingly technology-driven and environmentally friendly. Advances in materials science and digital manufacturing will enable bus parts to be produced in smarter, more resource-efficient ways than ever before.
One innovation on the horizon is the development of self-healing thermoformed plastics that can use sensors to detect small-scale damage such as cracks or chips and then automatically repair these problems.
Furthermore, the trend toward sustainable materials and methods must not be underestimated. The ecological impact of buses can be reduced if we produce heavy gauge thermoformed products or automotive components using recycled or bio-based materials. It could also set a new standard for the industry, prompting other manufacturers to follow suit.
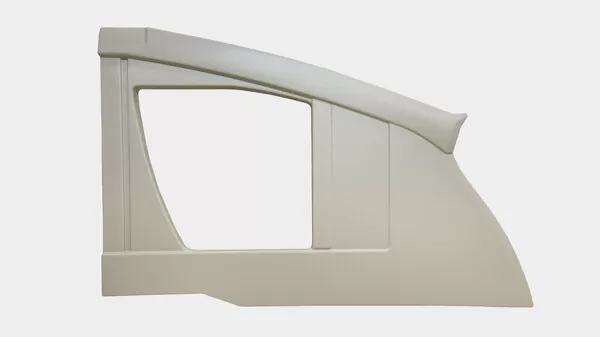
Conclusion
The importance of heavy gauge thermoforming in the design and production process of passenger car manufacturing cannot be overstated. This area seamlessly combines practicality and creativity, engineering principles and precautions, durable materials and rider comfort. Further advances should bring us bespoke, greener vehicles, and we can expect to see more personalized, efficient and sustainable buses on our roads.
Manufacturers are considering the benefits and applications of heavy gauge thermoforming and understanding that the path to a better tomorrow for transportation starts with decisions made today. This is testament to the transformation underway within the industry that promises buses not just as transportation, but as feats of modern engineering.
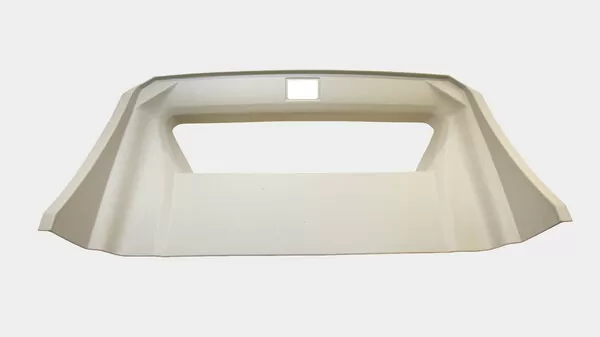
The passenger car industry has only recently been transformed by thermoforming, but there is more to come. For example, advances in materials science are expected to make buses not only lighter and stronger than ever before, but also more environmentally friendly. At the same time, breakthroughs in areas such as digital manufacturing technology and smart materials can also create possibilities for cheaper personalized design solutions.
While passenger buses may seem like a normal part of everyday life, there’s actually a lot going on behind the scenes. Innovation never stops in the factories that build these vehicles – increasingly in the form of heavy gauge thermoforming. This new technology has changed the function of public transport; instead of being slow coaches that always need to catch up with everyone else around them, they now lead the way people move around town.