Thermoforming is a plastic processing technology, the main principle is to spread the hard plastic sheet heated to soften, the use of vacuum adsorption will be softened sheet adsorption on the surface of the mold, after cooling the molding technology.
Vacuum forming is widely used in plastic packaging, lighting, advertising, decoration and other industries.
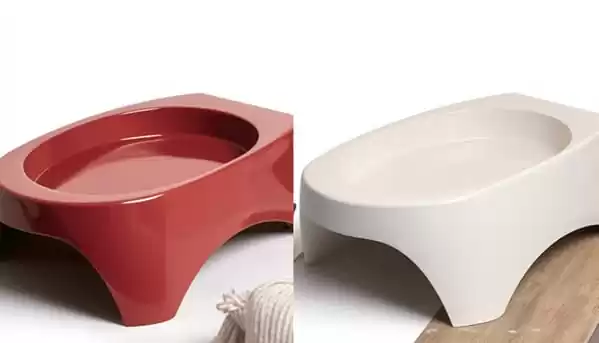
With the continuous development of science and technology, the manufacturing industry is also constantly innovating and progressing. Among them, thermoforming plastics process, as an emerging manufacturing technology, is gradually becoming the new trend of the future manufacturing industry.
Vacuum forming according to the thickness of the sheet is divided into thin gauge thermoforming and heavy gauge thermoforming, this article we will focus on thick gauge thermoforming.
Principle of Heavy Gauge Thermoforming
Heavy gauge thermoforming refers to the use of material thickness of more than 2mm, can not be in the fully automatic tool on the thermoforming machine, must be used in heavy gauge thermoforming semi-automatic thermoforming machine for processing and production. light gauge thermoforming, the thickness of the plastic is 1.5 mm or less and is usually roll fed into the thermoforming machine.
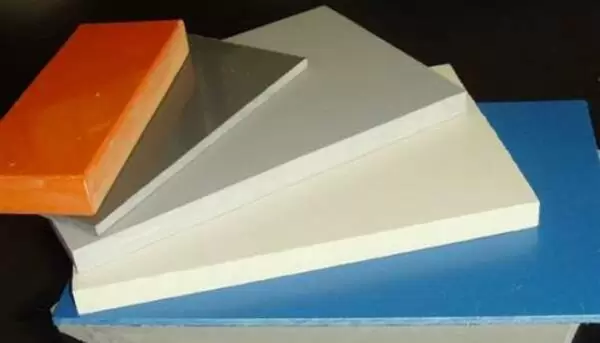
Thick piece of pressure forming machine is a plastic sheet as raw material, through the vacuum forming process to produce plastic parts of the key process equipment, it is a thermoplastic material plastic sheet as raw material, through the oven heated to a softening temperature, and then through the plastic sheet and the mold between the plastic sheet and the key process equipment.
It takes thermoplastic plastic flat sheet as raw material, heated to softening temperature by oven, and then through the negative pressure of vacuum between plastic sheet and mold, the plastic sheet in thermoplastic state is adsorbed on the working surface of the mold and then cooled to form.
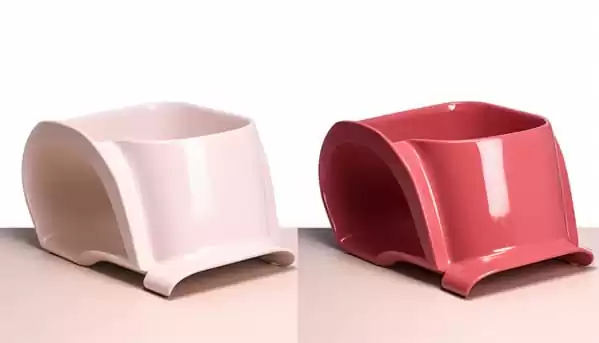
Difference Between Heavy Gauge Thermoforming and Thin Gauge Thermoforming
Different Materials
Heavy gauge thermoforming is generally used ABS, HIPS, etc.. Thin gauge thermoforming commonly used materials for PVC, PET, PP, PS, PETG, etc..
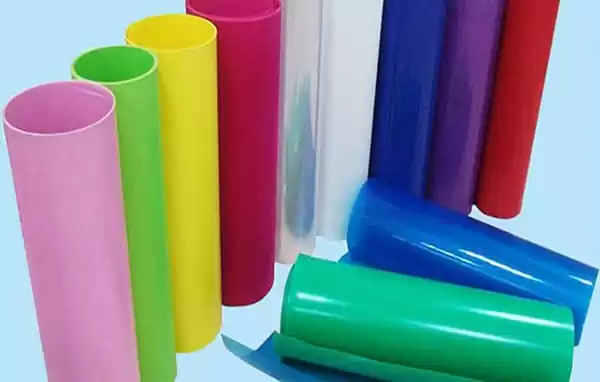
Material thickness is different, heavy gauge thermoforming industry need to use the material is sheet, that is, plate, 1-15mm thick, and light gauge thermoforming used in the material is coil 0.2-1mm thick.
.jpg.webp)
Different Uses
Heavy gauge thermoforming is commonly used in machine shells, display racks, advertisements, bases, image boards, sports equipment shells, beauty equipment shells, medical equipment shells, golf cart shells, toy car shells, turnover trays, game machine shells, refrigerator liners, light boxes and other vacuum forming products. The product thickness 1-10mm or even thicker.
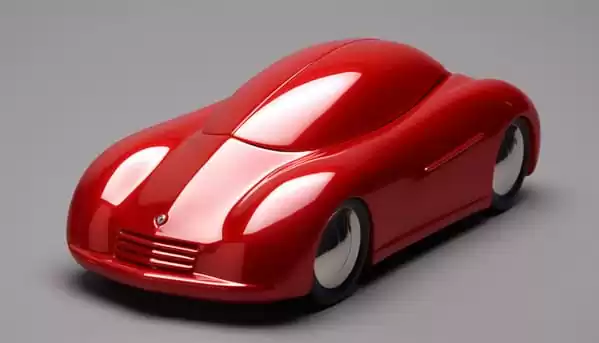
Thin gauge thermoforming is generally used in electronic products, cosmetics, food, health care products, toys, daily necessities and other pressure forming products. The thickness of the product is 10-100 silk.
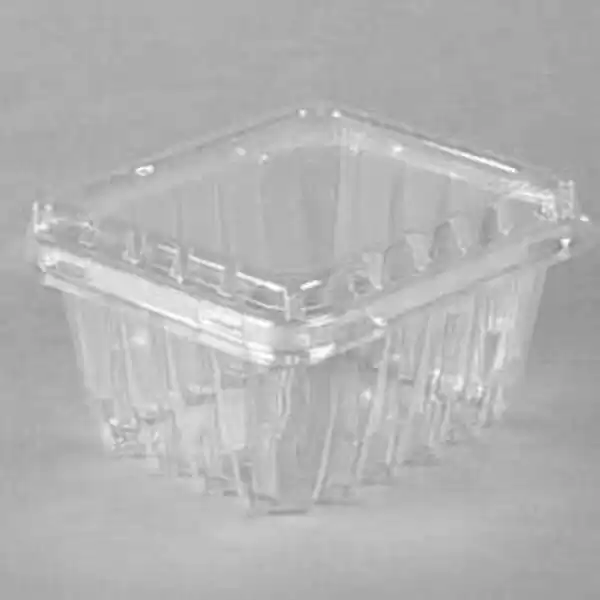
Different Processes
Heavy gauge thermoforming than thingauge thermoforming is more complex, on the basis of the process, heavy gauge thermoforming than thin gauge thermoforming more than a few milling edges, skeleton washing, grinding and other processing procedures.
Heavy gauge thermoforming industry cut edges and holes are CNC engraved, while the thin gauge thermoforming industry is punched with a knife mold, so the price of thick gauge thermoforming than thin gauge thermoforming is a little more expensive.
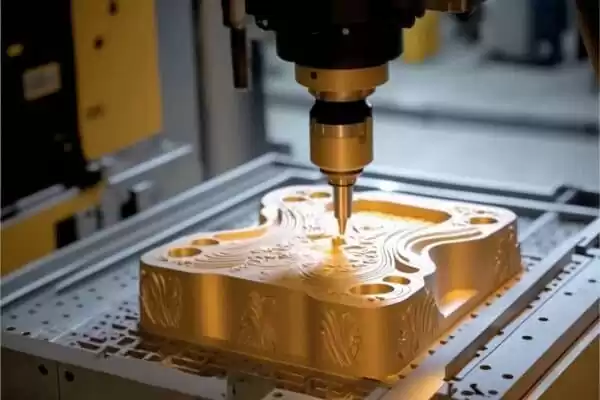
Different Machines
The machines used in heavy gauge thermoforming industry are semi-automatic thermoforming machines, which have a slow production time, while those used for light gauge thermoforming are high-speed machines, which are very fast.
Application
Heavy gauge thermoforming products are mainly used in: electrical appliance shell, automobile body jacket, pet tray, advertising light box, automobile interior and exterior, transportation, building materials, packaging, medical equipment, household appliances, education and sanitary ware, sporting goods, medical equipment, food equipment, instrument shell, lighting, refrigerator industry, air conditioning industry and home appliance parts and other people’s daily life in various fields.
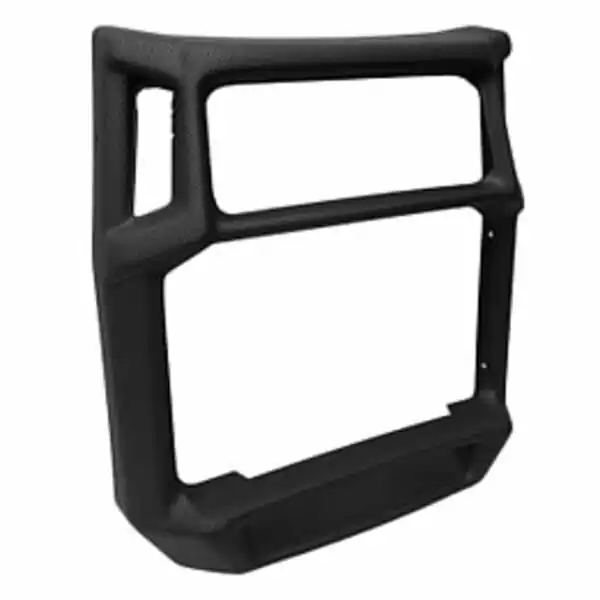
Heavy gauge thermoforming products can not only replace the injection molding process, saving the cost of expensive injection molds, but also replace the traditional handmade, with the advantages of advanced production process, fast speed, reliable quality and so on.
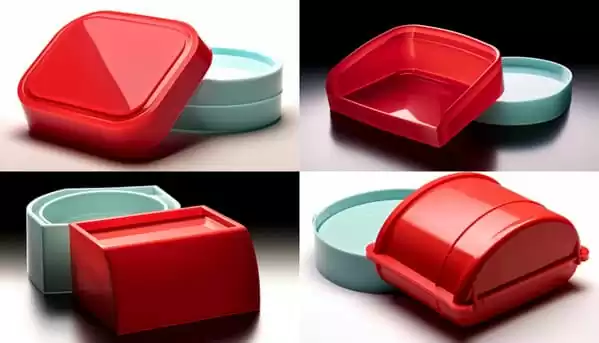
Heavy Gauge Thermoforming Materials
A variety of thermoplastic materials are used in heavy gauge thermoforming, each with unique properties for specific applications. The main materials used in thick sheet blister molding are: various colors of ABS, acrylic, PETG, PVC, PC, PP, PE, PS, etc. and a variety of modified plastics such as glossy, skinned and transparent sheets. The thickness ranges from 3mm to 60mm.
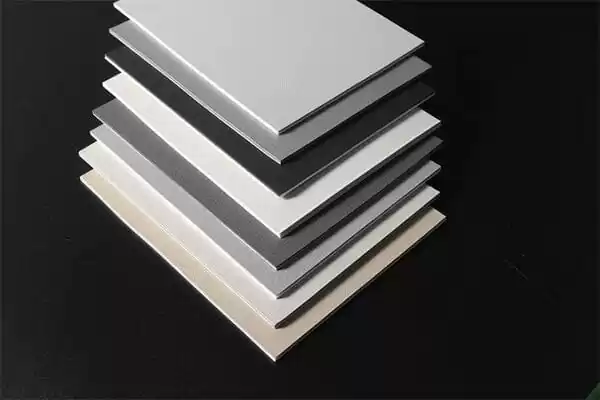
ABS: ABS is a thermoplastic known for its strong and durable properties. It has good impact resistance and high temperature resistance, making it ideal for both interior and exterior applications. In the automotive industry, ABS is used to make interior panels and instrument panels because of its strength, elasticity and aesthetic flexibility. In consumer products, it is used to produce everything from toys to cell phone cases.
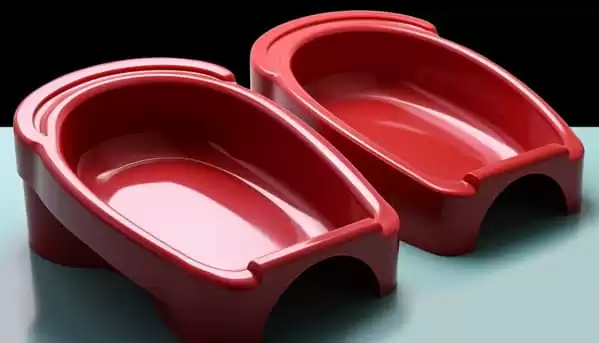
PE: Chemically resistant and highly durable and cost effective. PE is available in a wide range of densities and different properties with good elasticity and strength. PE is widely used in packaging due to its ability to effectively keep out moisture and other contaminants. Its chemical resistance makes it the material of choice for containers holding corrosive substances.
PS: PS has good rigidity and clarity and is easy to work with. It provides a cost-effective alternative for scenarios where clear, rigid plastic is required. Because of its transparency and rigidity, PS is often used to produce displays and models where a clear view of the product is critical.
PVC: prized for its versatility, strength and chemical resistance.
PC: prized for its transparency and impact resistance.
PMMA: prized for its optical transparency and UV resistance.
HIPS: tough and low cost.
Production Process
Heavy gauge thermoforming and thin gauge thermoforming principle is similar, is the positioning of the plate through the oven heated to a soft state, the vacuum forming mold and its periphery to form a closed space and will be the cavity air instantly pumped away, the plate is tightly covered in the surface of the mold, cooled and shaped to obtain the product of the process.
Vacuum forming is a cyclic process, each cycle mainly consists of: loading – heating softening – blowback pre-drawing – suction molding – cooling and shaping – demolding and taking out the parts. After removing the molded part, the sheet is placed again (either received or automatically) for the next cycle.
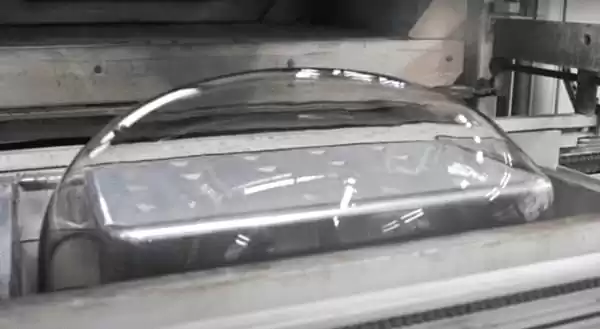
Mold Design and Making
Different customers have specifications for their products, so plastic molds must be made before production. In this case, the molds are made from plaster of plastic molds and the molds are produced using plastic. The lower cost is plaster molds, followed by electroplated copper molds, while aluminum molds are more expensive. When the molds are made, they are allowed to dry naturally or are dried and then treated according to the specific conditions of the product surface.
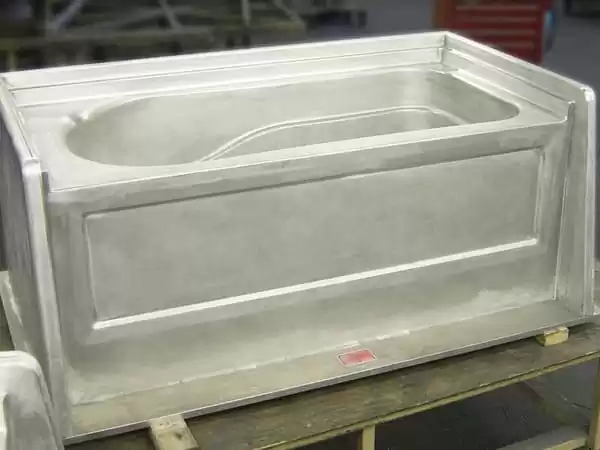
Mold Installation
When the mold is completely dry, it should be placed on the upper iron plate of the vacuum chamber, then the mold should be loaded to the applicable size according to the size of the mold then the paper should be placed in a hot wood cabinet to hold it in place and process it.
Forming
Fix the plastic sheets on the mold with fixing clips, heat the ends of the plastic sheet until they become soft, then use a vacuum pump to pump out the air between the material and the mold, so that the softened plastic sheet is adsorbed on the top of the mold, and then blow the air in the reverse direction to release the product from the mold when it cools down.
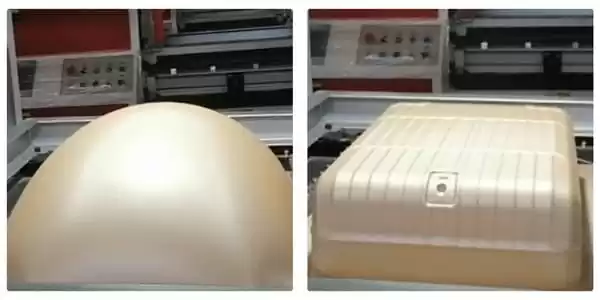
Finished Product
The finished plastic components is trimmed and integrated into a product that can be sold after sale packaging.
Agvantages
The advantage of heavy gauge thermoforming is its simplicity. For businesses or individuals looking to produce prototypes quickly, heavy gauge thermoforming stands out. The molds for heavy gauge thermoforming can be made from less durable materials such as wood or epoxy, so converting prototypes to physical form is both faster and cheaper.
Heavy gauge thermoforming is particularly cost-effective for low to medium volumes. Because tooling costs are typically lower than injection molding costs, small quantities can be produced without significant financial outlay. Another advantage is the relative ease of design changes. Because molds are less expensive, modifications can be made without incurring excessive costs.
Due to the large area and thick material of thick gauge thermoforming products, their strength and durability are high and they are able to protect the integrity of the goods. Secondly, heavy gauge thermoforming products can be customized to provide a wide range of features and shapes. In addition, the production process of heavy gauge thermoforming products is relatively simple and highly efficient, allowing them to meet the demands of mass production.
The automatic molding of heavy gauge thermoforming is particularly suitable for the production and processing of large products, because it realizes the automated operation from raw materials to finished products, so the efficiency is high and the quality is relatively stable.
In thick plate thermoforming technology, a variety of additional services can be performed, such as mold design, surface treatment, processing details and supporting assembly. Through these services, the appearance and performance of plastic products can be further enhanced.
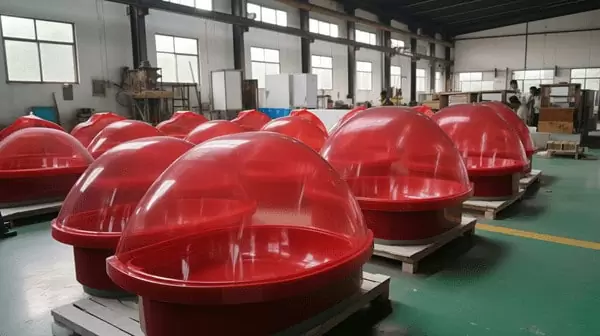
Conclusion
In conclusion, as an emerging manufacturing technology with advantages of complex shape, high production efficiency and low cost, the plastic thermoforming process is gradually becoming a new trend in the future manufacturing industry. With the continuous progress of science and technology and the continuous expansion of the application, I believe that the pressure forming process will play a more important role in the future manufacturing industry.
Heavy gauge thermoforming technology plays an important role in creating a wide variety of plastic products, while also helping to improve product quality and customer satisfaction. The proper selection of plastic materials, proper control of the manufacturing process, and the provision of additional services are all important factors in the creation of high-quality and value-added thick gauge thermoforming products.
We also continue to explore and advance, pushing the limits of material capabilities and part complexity using advanced molding technologies such as thermoforming, vacuum forming, twin sheet forming, and pressure forming.