Manufacturing today is highly competitive, and the success of product production depends, in part, on the ability to create accurate products. Heavy gauge thermoforming and thin gauge thermoforming are two common product application forms of thermoforming. There are differences between them before, not only the difference in product thickness, but also this very subtle difference, just like a master’s paintbrush, can have a profound impact on the final shape and effect of the product. When it comes to thermoforming, deciding between thick gauge and thin gauge requires more than just size. This choice is crucial because it not only determines how your product looks or sells, but also whether customers can use it.
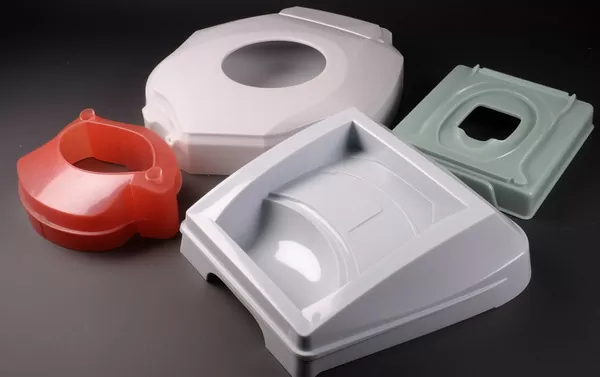
Many manufacturers overlook these subtle differences, ultimately leading to subpar results related to cost or performance (or both). Even the final product was seriously inconsistent with the prototype design. In this lengthy blog post, we take a deep dive into the world of thick gauge thermoforming vs. thin gauge thermoforming: explaining why understanding them can make such an important difference.
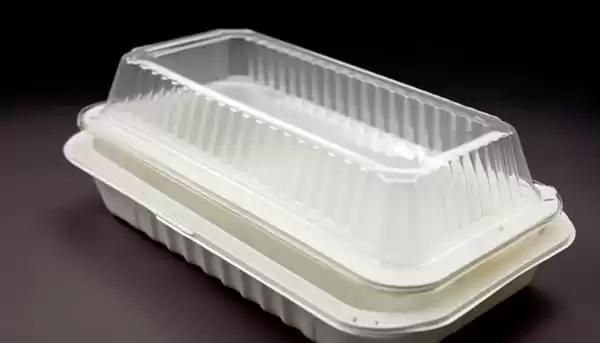
Thermoforming Process
Before we dissect the intricacies of heavy and thin gauge thermoforming, it is pivotal to understand thermoforming as a whole.
1. What is Thermoforming?
Unlike injection molding, the thermoforming process involves heating a flat plastic sheet until it is soft enough to be formed. This can be done using vacuum suction, compressed air or through mechanical force applied mechanically; this means there are so many possibilities that can be created with this technique alone! Examples include anything from food containers all the way to car parts like bumpers and aerospace components.
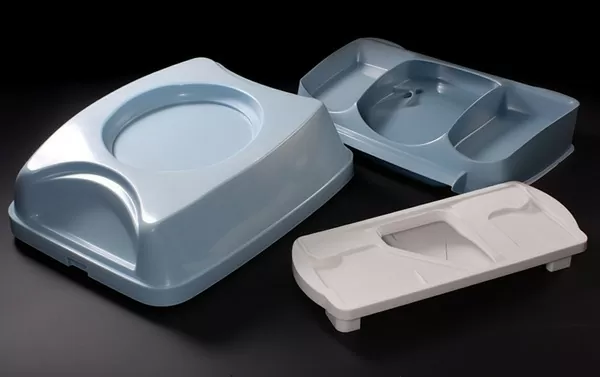
2. A Historical Perspective
The roots of thermoforming date back to the 1940s and can be traced back to their development from the general idea of plastic molding. It has helped the manufacturing industry achieve significant progress in many ways. Since then, new materials have emerged, processes have become more streamlined, and applications have multiplied.
3. Materials at the Forefront
Common thermoplastic materials: ABS (acrylonitrile butadiene styrene), PC (polycarbonate), PET (polyethylene terephthalate), and PVC (polyvinyl chloride). These materials each have different mechanical strengths that help determine the appearance and performance of the finished product.
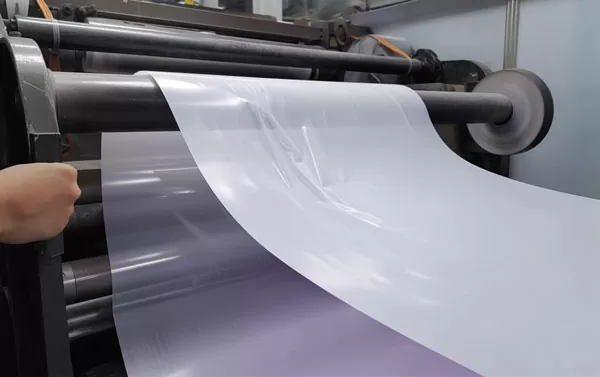
Heavy Gauge Thermoforming
When it comes to heavy gauge thermoforming, the word “heavy-duty” really hits home. This rugged technology is designed to create durable products that can withstand the long term.
1. Defining Heavy Gauge
Heavy gauge thermoforming uses plastics that are at least 0.060 inches thick. It also features large plate sizes and high clamping tonnage; both of which help create a stronger item.
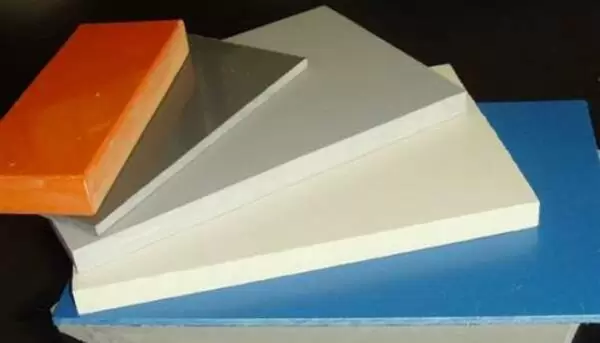
2. Application
There are many use cases for heavy gauge thermoforming. Consider things like automotive interior panels, medical pallets, or even guards on large machinery—these complex products all rely heavily on this type of manufacturing process to ensure their overall strength during long-term use under huge strain loads.
3. Advantage
The high impact resistance of heavy gauge thermoformed products makes them ideal for items that need protection from rough handling. They are also a popular choice in industry because they do not change shape when conditions become extreme, so their dimensions remain stable.
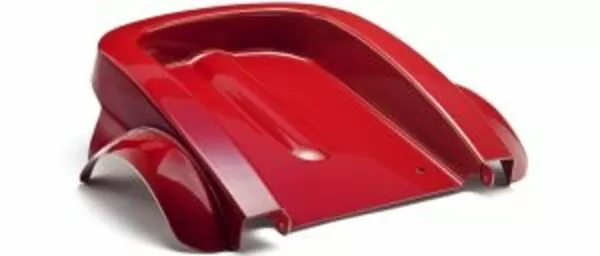
Thin Gauge Thermoforming
In contrast, thin gauge thermoforming is akin to the sonnet — focusing on fluency, aesthetics, and finesse.
1. What Constitutes Thin Gauge Thermoforming
Thin gauge thermoforming is a process used to manufacture plastic products with thicknesses between 0. 010 and 0. 060 inches and is usually roll fed into the thermoforming machine. This is an efficient method because it requires less time per cycle and the tools are simpler than other methods—both factors help reduce costs when manufacturing products in high volumes.
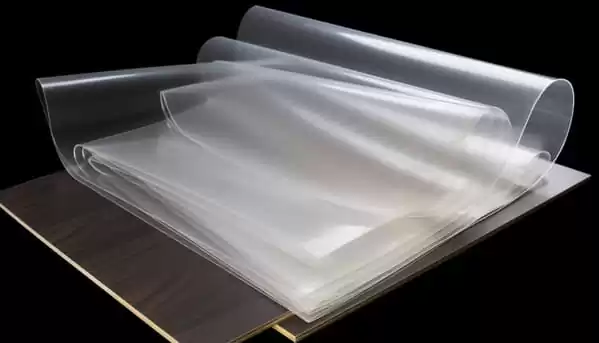
2. Application
Thin gauge thermoforming is key to producing electronic casings, consumer product packaging and even disposable tableware. The process can provide a wider range of textures and finishes to products, such as those made of plastic, due to the ability to achieve finer detail than its heavier counterparts.
3. The Economical Edge
Thin gauge thermoforming has the advantage of being cost-effective, especially for high-volume production. Its ability to work quickly while using materials efficiently means lower unit costs – something that will appeal to any industry that needs affordable products that can still be produced again and again without variation.
.jpg.webp)
Distinguishing Heavy and Thin Gauge Thermoforming
Understanding the fundamental differences between these thermoforming methods is crucial for manufacturers making informed production decisions.
1. Material Layers Apart
The thickness of the material used is a key difference. It affects everything from the design of the production process to the performance of the product after use; for example, mold design needs to consider light or heavy-duty applications.
2. Process and Precision
The manufacturing processes for thick gauge and thin gauge thermoforming are very different. If it is a large gauge, it may require more manpower and complex molds, while thin gauge thermoforming just need lower tooling costs; on the other hand, thin gauge manufacturing often relies on automated systems that run at faster speeds.
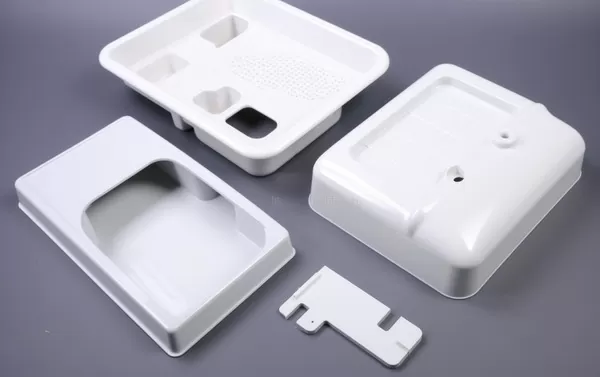
3. Machine
The use of heavy gauge thermoforming industrial equipment is very different from thin gauge equipment. When forming thicker materials, higher pressure levels are needed, while lower pressure levels are enough to make things out of thin sheets – sometimes requiring delicate touches that can only be achieved with a less powerful machine!
4. Speed
While thin gauge thermoforming is faster for manufacturing high volume products, heavy gauge is better when very precise forming of complex shapes or large objects is required.
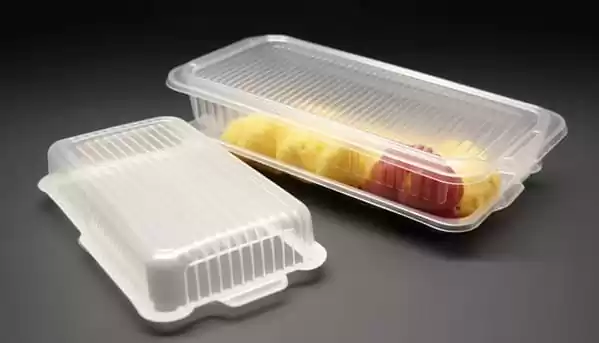
5. Suitability in Favorable Situations
In the end, the intended use might take care of this: thin gauge thermoforming is great for retail packaging because it’s lightweight and cost-effective; but if you need strength and resistance to heavy loads (like in a harsh environment), then heavy gauge thermoforming is better for you.
Choosing the Right Thermoforming Path
Manufacturers stand at the crossroads of heavy and thin gauge thermoforming, and choosing the correct path can make all the difference.
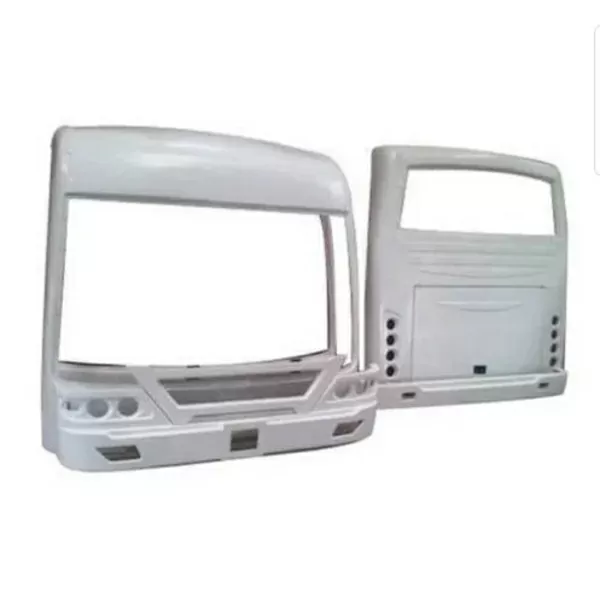
1. Economic Considerations
Cost implications are the primary concern here. While thin gauge materials may result in lower setup expenses when handling high-volume production (because they run faster and use less material overall), this doesn’t necessarily apply to every job size or type.
2. Aesthetic and Functional Design
Choice will also be influenced by product design and the emphasis placed on appearance versus practicality. If you want a slim electronics case, choose the thin gauge. If the product needs to be stronger and more durable, then heavy duty might be better.
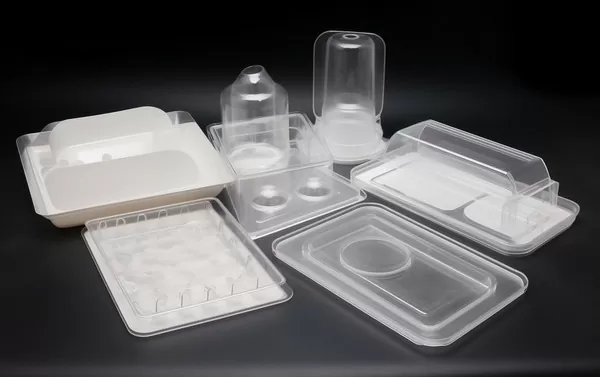
3. Volume and Velocity
For low-volume specialized products, heavy gauge’s bespoke nature may be indispensable, while the mass production demands of consumer goods often find a perfect match in thin gauge thermoforming.
4. A Design for Impact
When it comes to thermoforming, material selection is closely tied to your design. By understanding how choosing a thicker or thinner gauge will affect your design options, you’ll be able to create products that really catch people’s eyes and stick with them.
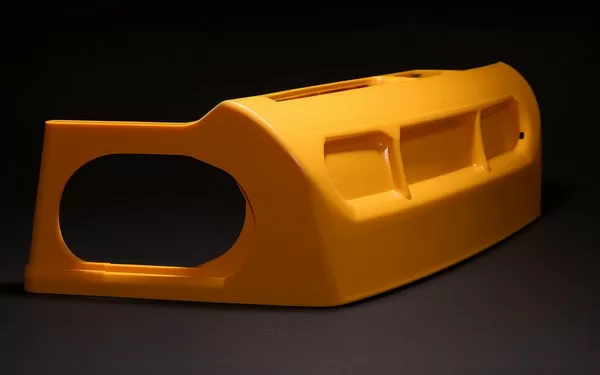
Heavy gauge thermoforming: Because this technique uses stronger materials, it’s ideal for creating plastic components with a comfortable interior and tough exterior, such as automotive parts. This durability also means these items will stay in good shape over time – a plus if they’re going to be exposed to harsh conditions or rough handling. Thin gauge plastic thermoforming: Ideal when intricate designs or details are required. This makes it ideal for enhancing product presentation, creating clear food packaging that showcases content, and increasing shelf appeal through innovative shapes and decorative elements.
Conclusion
When it comes to thermoforming, the choice of heavy gauge thermoforming versus thin gauge thermoforming is an important decision that can have wide-ranging consequences—meaning it’s as much about artistry as it is about scientific understanding. Whether your goal is to create rugged automotive parts or attractive retail display packaging, the right selection will make the difference from end use to manufacturing. The benefits and trade-offs associated with using thicker versus thinner gauges deserve careful consideration; after all, you want a product that not only performs well, but also looks good.
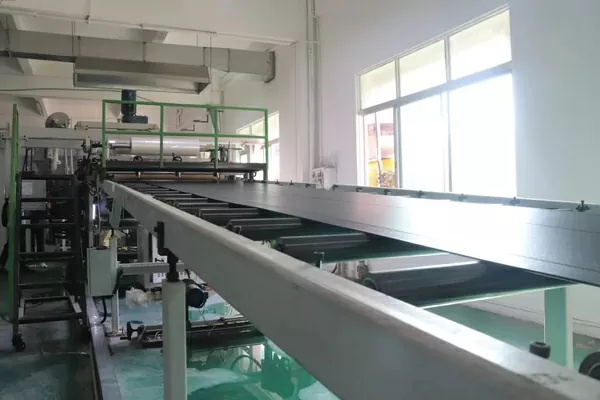
The decision to use heavy gauge or light gauge thermoforming ultimately comes down to a clear understanding of your product, how it will be used, your market positioning and whether your company has any sustainability goals. Once you explore the capabilities of each thermoplastic material and imagine how these properties might work with your own project, making the right choice becomes much easier; in fact, doing so will guarantee its success.