Plastic manufacturing process is a complex and ever-changing industry, with countless variables that can impact a company’s bottom line. One factor that people talk about a lot is economies of scale—and for good reason.
In essence, economies of scale determine a company’s ability to convert raw materials into profits, especially as competition becomes increasingly fierce. But what does this mean for thermoforming, a popular way to process plastics?
If you also want to get into the thermoforming industry, this blog post is for you! We are looking into the role of thermoforming and how it can change the quality or quantity of a plastic product in depth analysis, for example – all of which depends on economies of scale. Finally, you’ll gain a comprehensive understanding of how to leverage economies of scale in thermoforming operations to increase competitiveness and profitability.
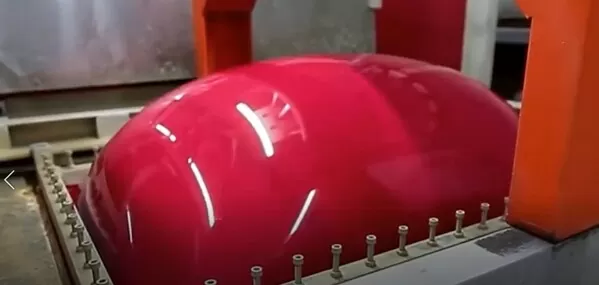
Understanding Thermoforming
Thermoforming is a popular method of manufacturing products. It involves heating sheets of plastic until they become soft enough to be shaped, then cooling them again and then trimming away the excess material to give you the desired shape. Many different types of industries rely on this technology as its functions are so diverse – from food packaging to medical devices all the way to automotive components or create hollow plastic parts!
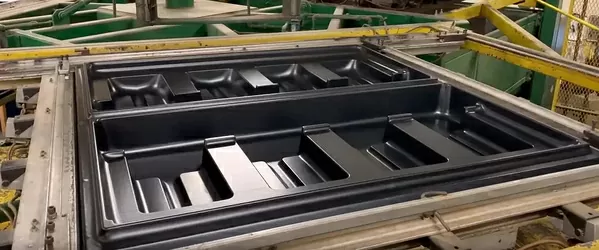
Heating the Plastic Sheet
The first step in the thermoforming process involves heating the thermoplastic materials plastic sheet. The exact temperature at which this is done depends on factors such as the type of plastic used and the complex geometries of the final product.
Forming
After the plastic is heated and softened, it is attracted to the mold. Vacuum pressure or mechanical pressing can be used – this varies depending on the thermoforming method used.
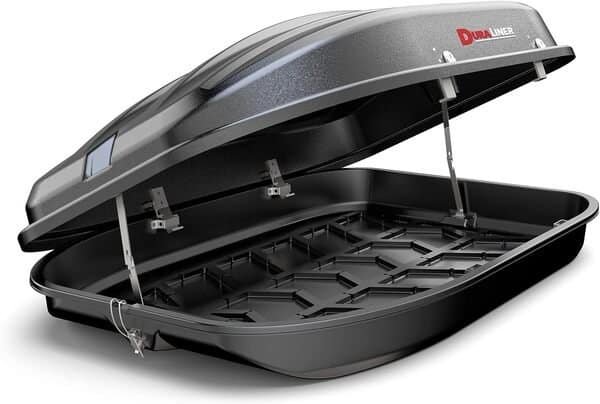
Cooling, Trimming, CNC Machining
Once formed, the product cools rapidly and solidifies into the final product. Next comes the finishing process: during this process, all excess material as well as possible imperfections are removed – all to ensure that each item ends up fully meeting quality control standards!
Productivity and Thermoforming Efficiency
Productivity is the silent partner in the manufacturing. It dictates everything from the speed at which machines run to the number of units produced per hour. This immediate relationship can be broken down into a few key efficiency factors:
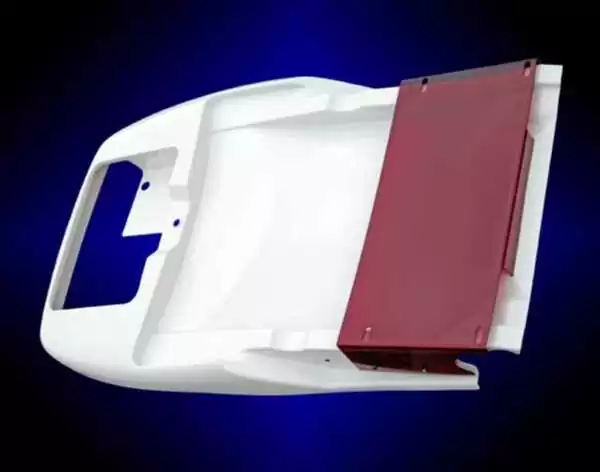
Machine Utilization and Downtime
When it comes to producing high-volume parts, thermoforming machines do perform equally well in addition to injection molding process. With the right setup and materials, high-volume parts can be produced. However, some initial investment in downtime is required for installation purposes and when maintenance or material changeovers must occur. But overall, high-volume production tends to have less downtime per unit of production than low-volume production operations.
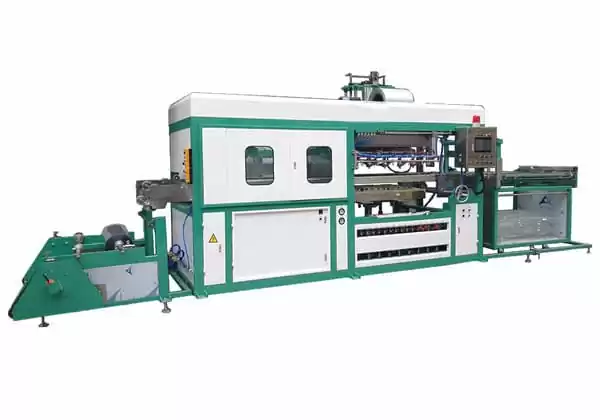
Labor and Training
The human presence in the manufacturing process is important but costly. When working with small quantities of products, training workers to create unique items or items that require special skills may not be as cost-effective as having them focus on one job, whereas high-volume production allows workers to focus on specific tasks and learn related best practices more quickly .
Raw Material Cost and Orders
The advantage of mass production is the ability to order raw materials in large quantities. Since thermoforming relies heavily on these materials, purchasing in bulk can result in significant cost savings. In addition to lowering the unit cost of each material used; the total number of orders is also reduced, making supply chain management overall more efficient!
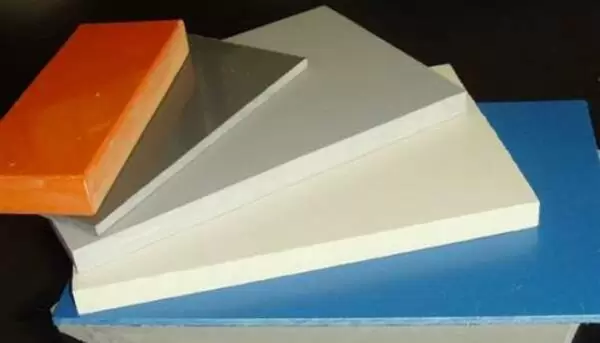
Energy Consumption
Thermoforming requires a lot of energy. If the machine is running at maximum output, energy costs per part will drop significantly; if enough parts are being manufactured, it may make sense to purchase a new machine with lower overall energy consumption, which will further reduce running costs!
Tooling and Capital Investment
The cost of tooling used in thermoforming represents a significant amount of capital. However, this cost is spread over the number of products manufactured. As the number of units produced increases, the percentage of amortized tooling cost per unit decreases.
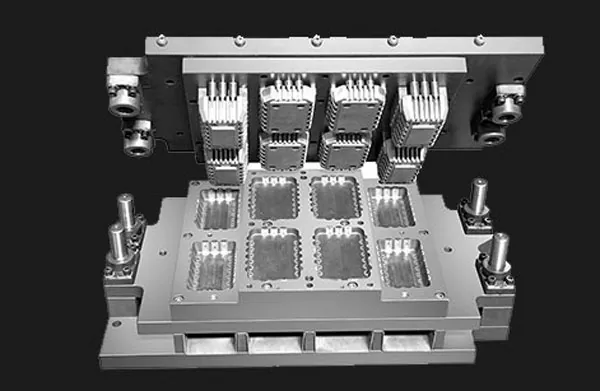
Waste and Recyclability
When producing large batches, less scrap is produced compared to the total amount of raw material produced, thus increasing material yield. At scale, it becomes more possible (and cheaper) and more cost-effective to manage waste through recycling or reuse.
These efficiency drivers illustrate that thermoforming is a process inherently designed to benefit from scale—each increase in volume is a corresponding increase in potential efficiency and reduction in cost.
The Concept of Economies of Scale
Economies of scale occur when production costs fall as output increases. These lower costs often come from running the business more efficiently—for example, by spreading the cost of certain investments or purchases over larger production units.
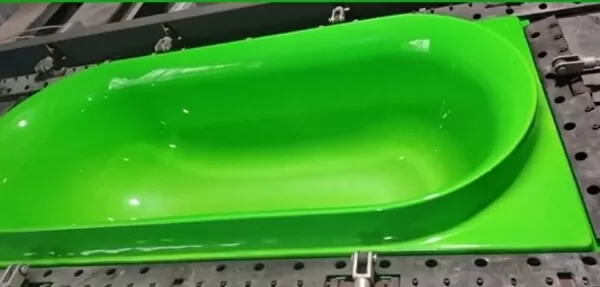
Why Economies of Scale Matter
To remain profitable and competitive, companies must grasp and take advantage of economies of scale. These can have a real impact on what companies offer to the market – lower prices for consumers; higher profit margins for producers.
Economies of Scale in Thermoforming
Thermoforming is a prime example of how economies of scale work best. The technology itself depends heavily on your output; by significantly increasing your output, you can save a lot of money.
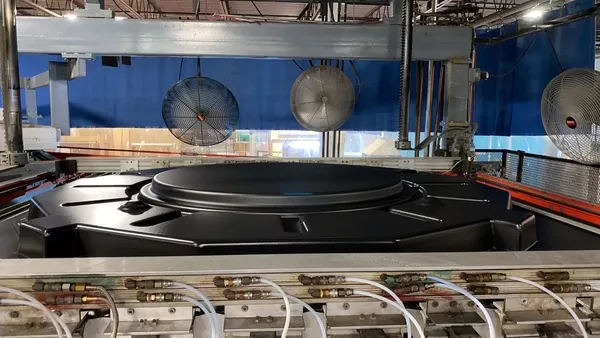
Material Costs
Compared with injection molding, blow molding or other traditional molding methods, vacuum forming manufacturing processes has a relatively lower cost in terms of mold materials. You can save a lot of money when you buy raw materials in bulk and bargain with suppliers to get a better deal. Of course, it’s nice to spend less money upfront on these items, but the benefits don’t end there! The real value comes from purchasing and consuming these materials efficiently.
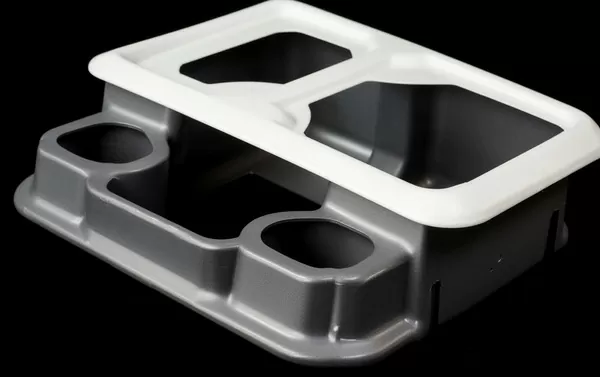
Operational Efficiencies
Producing more products has several benefits, including streamlining production process and reducing waste. When you increase the output of each product, costs (such as those associated with setting up the mold) can be spread over the entire order; therefore, the overall cost of manufacturing per unit becomes cheaper.
Equipment and Tooling Costs
The cost of machinery and tooling required for thermoforming represents a significant portion of the total expense. However, as you produce more units, the price per unit becomes cheaper. This directly affects how competitive your final costs are compared to other products.
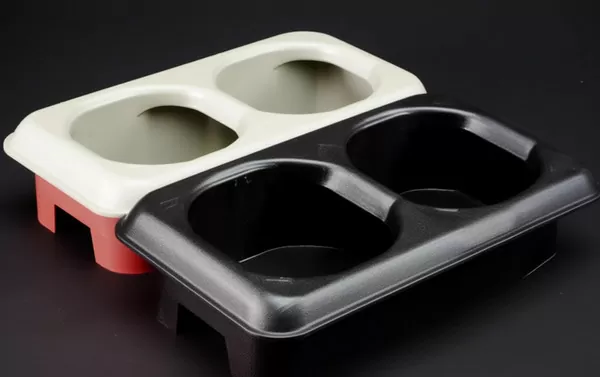
Labor Costs
The advantages of scale are evident in workforce management too. When both equipment and procedures can be specialized, the cost of labor doesn’t have to keep pace with output: There will still be big savings per unit as volume ramps up because these costs increase more slowly.
Energy Efficiency and Conservation
On a larger scale, investments can be made in more advanced energy recovery systems and other conservation measures that may be too expensive for smaller businesses. These steps bring a dual benefit: not only do they reduce costs, but they also reduce carbon footprint levels.
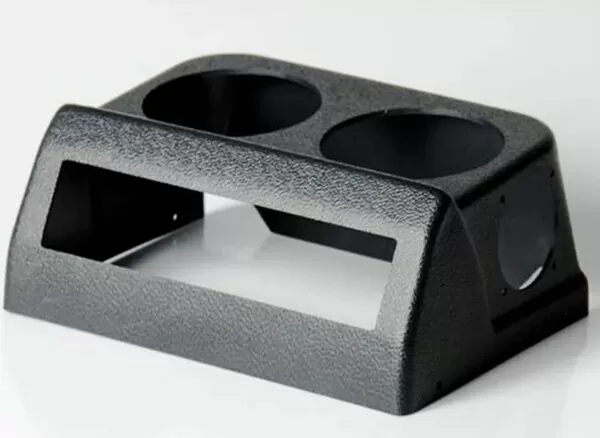
Waste Reduction, Recyclability, and Circular Economy
For larger quantities, there is more material to recycle and there are greater opportunities to collaborate and invest in circular economy models at scale.
Efforts to minimize waste and aim at recycling make economic sense and may even create value over time.
Sustainability efforts are inextricably linked with the scale of operation and can be a significant driver in shaping a thermoforming company’s approach to business.
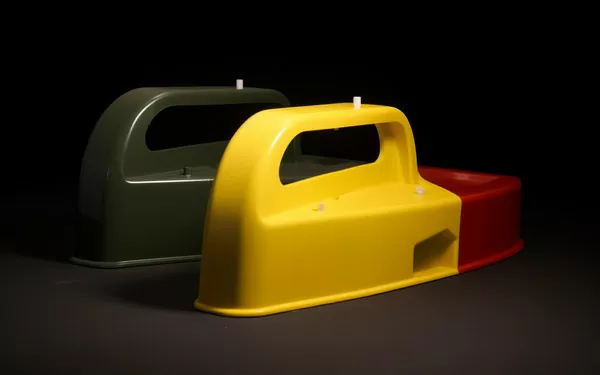
Case Studies and Examples
An examination of the cost structures of small and large thermoforming operations reveals significant differences. To further illustrate this point, we will provide real-world examples and case studies that highlight how economies of scale can help businesses cut costs and ultimately improve profits.
Case
Real-life examples can be a compelling way to understand how economies of scale work in thermoforming. There are many examples in the industry – from companies that leveraged large-scale operations to capture markets, to those that excel by being nimble and able to offer a niche. These stories illustrate when companies achieve strategic growth.
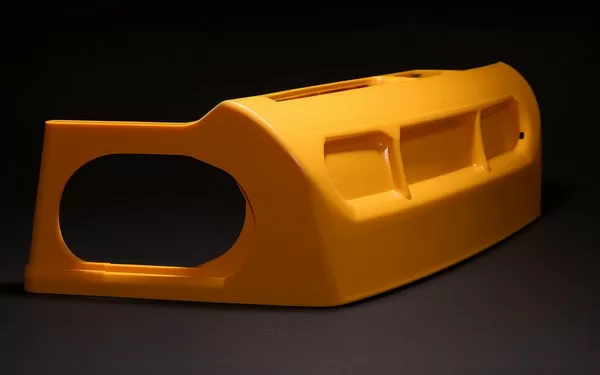
1. Food Packaging Giant
A leading food packaging company is thriving on its ability to scale production based on customer demand. This is because they can use data analytics to predict demand and scale up or down production accordingly.
As a result, customers can get exactly what type and quantity they want (whether it’s a small or large batch of a limited-edition item) without paying the additional fees associated with overstocking unsold items.
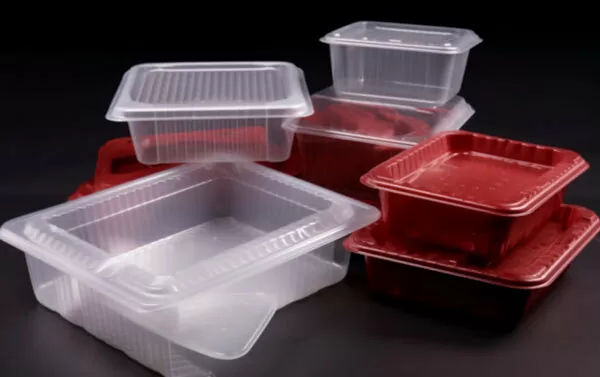
2. Medical Industry
A specialty medical device manufacturer can make a name for itself in the industry by producing customized, low-volume products.
By paying close attention to efficiency and reducing waste, the company has found a way to operate both profitably and sustainably while meeting the unique needs of each customer.
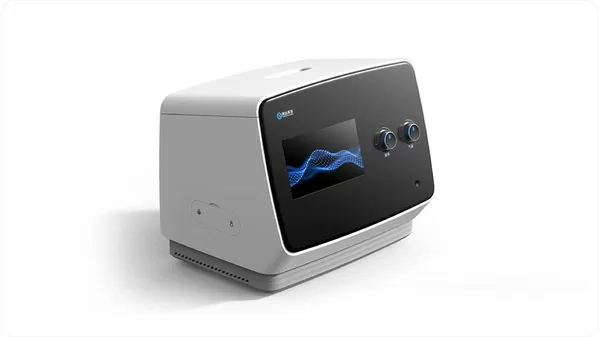
Cost Implications of Scaling Up Production
After studying the cost structure at different production levels, we found that unit costs dropped significantly as production volume increased. Companies that successfully expand their thermoforming operations can help educate others about best practices and methods in the field.
Evidence from Industry Studies
This evidence is not anecdotal but based on practical and actionable insights. From industry research, we can see real-world data that highlight the cost advantages achieved through economies of scale in thermoforming.
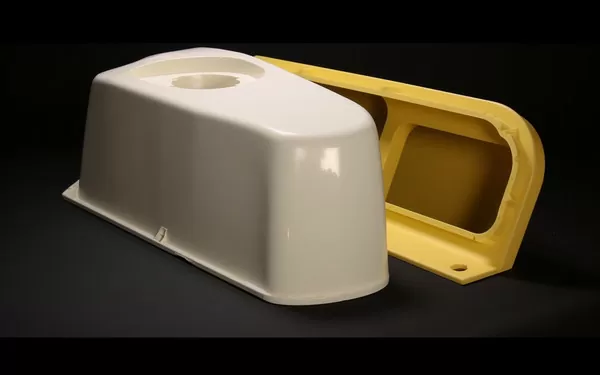
Overcoming Challenges to Achieve Economies of Scale
Achieving economies of scale in thermoforming isn’t a straightforward process and businesses must be aware of the potential challenges that can arise when looking to scale up their operations.
Capital Investment
One of the biggest hurdles to overcome when trying to achieve economies of scale is the necessary upfront investment in infrastructure, machinery and labor. In this blog, we’ll explore strategies for securing the capital you need to invest in the scaling process.
Quality Control
When a company scales up rapidly, it needs to ensure that its quality standards don’t drop. We will examine ways in which firms can introduce checks and balances that increase with output.
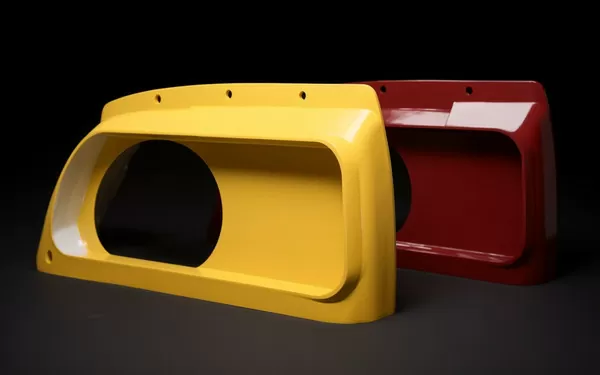
Supply Chain Management
To fully realize economies of scale, it is critical to have a well-functioning and strong supply chain. Dealing with suppliers, materials, logistics arrangements – all of these can become complex when you operate at a higher level, so we need to look at how to make their management more efficient and effective; this may also involve a certain degree of ( or many) changes.
Leveraging Technology and Innovation
Using automation and artificial intelligence can be really beneficial for companies that want to grow. We will examine examples of innovative technologies and their impact on thermoforming operations.
Strategic Partnerships
Entrepreneurs can also overcome some of the scalability challenges by forming strategic partnerships and collaborations. When companies pool their resources and expertise, they can spread their work and wealth over a larger base to achieve greater scale.
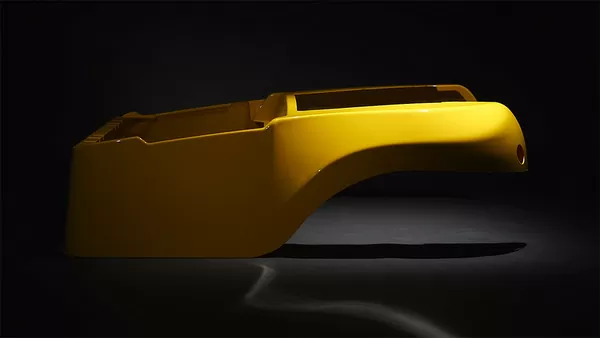
Preparing for Scale
When expanding a thermoforming business, companies must proceed with caution and careful planning. Here are some tips for preparing responsibly and successfully.
Conducting Market Research
Understanding market demand and accurately forecasting are two of the most important parts of scaling effectively. We can provide you with some guidance on how to conduct robust market research for this purpose – helping you make decisions as you scale!
Planning for Scale from the Start
The best way to scale is to plan for it from the beginning. We’ll explore ways businesses can structure their operations and workflows to prepare for higher volumes in the future, making overall scaling easier!
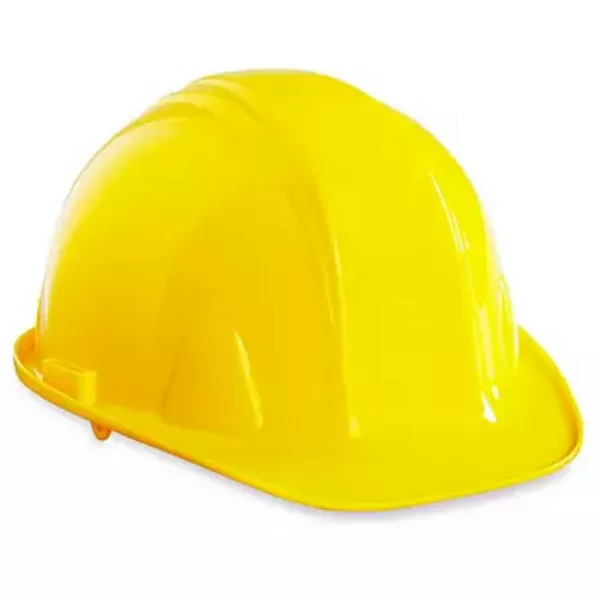
Investing in Quality Tooling and Equipment
People may think that in order to cut costs, they should not invest in expensive tools and equipment. But if you look at the long term, these quality tools are sometimes just what is needed to make an operation leaner overall – which means less money spent per unit manufactured!
Conclusion
Economies of scale are critical to the economic prosperity of a thermoforming company—in fact, economies of scale can determine the success or failure of such an enterprise. Thermoformers that understand how to take full advantage of scale will find themselves able to significantly cut costs and enter the market (or do more in existing markets) at a price point that competitors without similar capabilities cannot match.
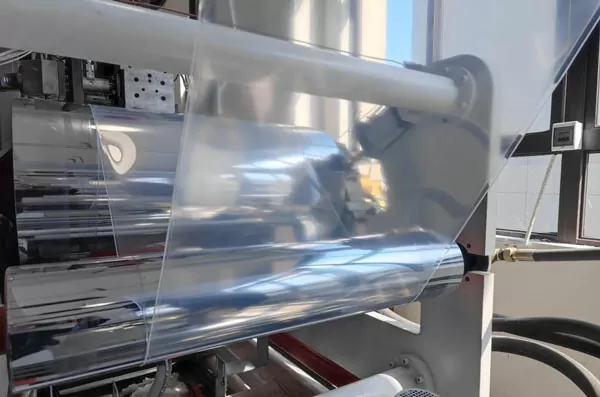
Staying ahead in manufacturing requires keeping up with changes and applying these principles. This is especially true for thermoforming. Companies must understand how scale affects this process and take advantage of its advantages: producing large quantities of products quickly