Introduction
Vacuum forming is a versatile manufacturing process that involves shaping plastic sheets into specific forms using heat and pressure. It is widely used across various industries due to its cost-effectiveness and ability to produce complex shapes with relative ease. However, the success of the vacuum forming process relies heavily on the molds used.
Molds play a crucial role in the vacuum forming process, as they determine the final shape and quality of the formed plastic. Without molds, it would be nearly impossible to achieve consistent and accurate results. The molds act as the foundation for the plastic sheets, providing the necessary structure and form during the heating and shaping stages.
The purpose of this article is to delve into the different types of molds commonly used in vacuum forming. By exploring these mold types, we aim to provide insights into their characteristics, advantages, and applications. Whether you’re a beginner looking to understand the basics or an industry professional seeking to expand your knowledge, this article will serve as a comprehensive guide to the various molds used in vacuum forming. So, let’s dive in and explore the world of vacuum forming molds.
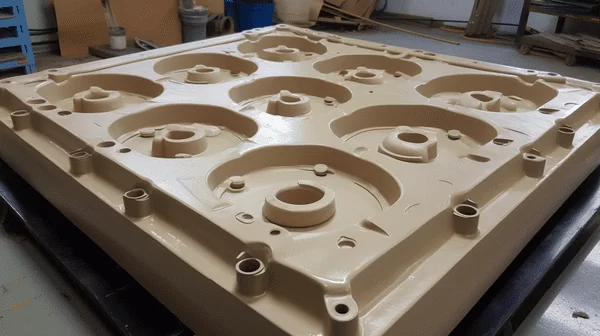
II. Wooden Molds for vacuum forming process
A. Description and Characteristics:
Wooden molds, as the name suggests, are molds made from wood materials such as plywood or medium-density fiberboard (MDF). They are typically crafted to match the desired shape of the final product. Wooden molds are relatively simple in construction and can be customized easily to achieve specific designs. They are commonly used in vacuum forming processes, especially for smaller-scale or prototype productions.
B. Advantages and Disadvantages:
Advantages of using wooden molds in vacuum forming include:
- Cost-Effectiveness: Wooden molds are generally less expensive compared to other mold materials, making them a budget-friendly option for small-scale projects or initial prototypes.
- Easy Customization: Wood is a versatile material that can be easily shaped, cut, and modified to create the desired mold design. This flexibility allows for quick adjustments and iterations during the product development process.
- Low Heat Conductivity: Wood has relatively low heat conductivity, which can be advantageous for certain vacuum forming applications where precise temperature control is required.
However, wooden molds also have some limitations and disadvantages:
- Limited Durability: Wood is susceptible to wear, warping, and degradation over time. The heat and moisture involved in the vacuum forming process can cause damage to wooden molds, reducing their lifespan.
- Limited Complexity: Wooden molds may not be suitable for highly complex or intricate shapes due to the limitations of wood as a material. Achieving intricate details may be challenging with wooden molds.
- Surface Finish: The surface finish of wooden molds may not be as smooth or refined compared to other mold materials. This can result in slight imperfections on the final vacuum-formed products.
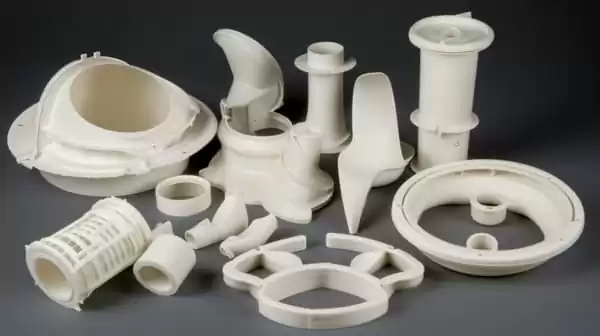
C. Suitability for Different Applications:
Wooden molds find suitability in various applications, including:
- Prototyping: Wooden molds are often used in the initial stages of product development to create prototypes and test designs before investing in more expensive mold materials.
- Low-Volume Production: Wooden molds can be suitable for low-volume productions where cost-effectiveness and quick iterations are prioritized over long-term durability.
- Education and DIY Projects: Wooden molds are commonly utilized in educational settings or for DIY projects due to their accessibility, ease of use, and affordability.
D. Considerations for Using Wooden Molds in Vacuum Forming:
When using wooden molds in a vacuum forming machine, it is important to consider the following:
- Mold Preparation: Properly seal and treat the wooden mold to protect it from the heat and moisture involved in the vacuum forming process. Applying a suitable sealant or coating can enhance its durability.
- Design Complexity: Evaluate the complexity of the desired shape and consider if wooden molds can adequately reproduce the intricate details. Complex or highly precise shapes may require alternative mold materials.
- Lifespan and Maintenance: Understand the limitations of wooden molds in terms of durability and lifespan. Regular inspection and maintenance, such as sanding and refinishing, may be necessary to extend their usability.
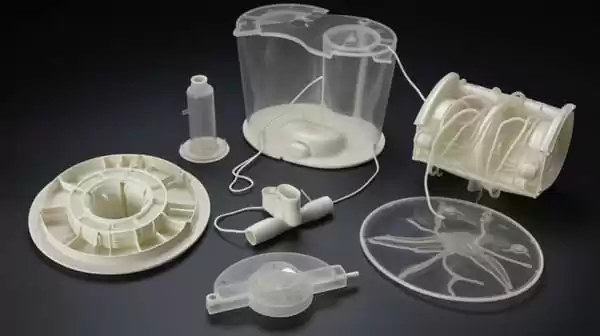
Despite their limitations, wooden molds can be a cost-effective and accessible option for certain vacuum forming applications, particularly in prototyping and low-volume productions. By understanding their characteristics and considering the specific requirements of your project, you can effectively utilize wooden molds in the vacuum forming process.
III. Composite Molds for vacuum forming process
A. Description and Characteristics:
Composite molds used in vacuum forming are made from a combination of materials, typically epoxy resin and fiberglass. The composite materials are layered and reinforced to create a strong and durable mold. Composite molds offer unique characteristics that make them suitable for various vacuum forming applications.
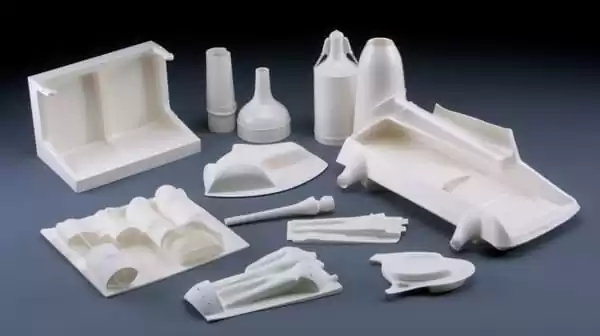
B. Advantages and Disadvantages:
Advantages of using composite molds in vacuum forming include:
- Durability: Composite molds are highly durable and can withstand repeated use and exposure to high forming temperature without warping or deforming. They have superior resistance to wear and damage compared to wooden molds.
- Versatility: Composite molds can be easily shaped and formed to create complex designs and intricate details. They provide greater flexibility in reproducing precise shapes, allowing for intricate vacuum-formed parts.
- Heat Resistance: Composite molds have excellent heat resistance properties, making them suitable for vacuum forming processes that involve high temperatures. They can maintain their structural integrity under prolonged exposure to heat.
However, composite molds also have certain limitations:
- Cost: Composite molds are generally more expensive to produce than wooden molds. The materials and manufacturing processes involved contribute to the higher cost.
- Manufacturing Complexity: Creating composite molds requires expertise and specialized techniques such as hand-layup, filament winding, or vacuum infusion. The manufacturing process can be more complex and time-consuming compared to other mold materials.
C. Applications and Industries:
Composite molds find applications in various industries where vacuum forming method. Some common applications include:
- Automotive Industry: Composite molds are used in the production of automotive parts such as interior trim components, instrument panels, and bumpers.
- Aerospace Industry: Composite molds are utilized in the manufacturing of aircraft components, including cockpit panels, interior fittings, and structural parts.
- Packaging Industry: Composite molds are employed for the production of packaging solutions such as custom-formed trays, blisters, and protective enclosures.
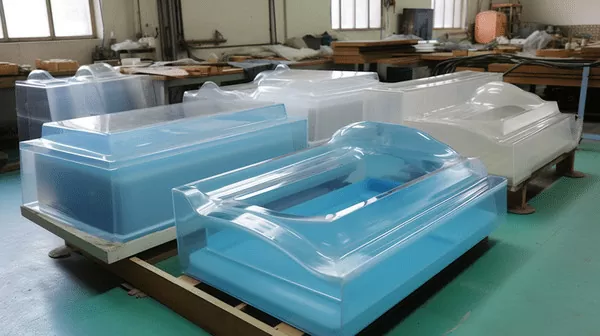
D. Key Considerations when Using Composite Molds for Vacuum Forming:
When using ceramic composite mold molds in vacuum forming , it is important to consider the following:
- Design Complexity: Composite molds are well-suited for complex shapes and intricate details. Consider the design requirements of your vacuum-formed parts and assess if composite molds can effectively reproduce those features.
- Manufacturing Expertise: Creating composite molds requires specialized knowledge and skills. Ensure that you work with experienced mold makers who are proficient in composite materials and techniques.
- Cost and Volume: Evaluate the cost-effectiveness of using composite molds based on your production volume. Composite molds are often preferred for larger production runs due to their durability and longevity.
- Maintenance and Repair: Composite molds may require periodic maintenance and repair to address any wear or damage. Consider the availability of maintenance services and factor in the associated costs.
By carefully considering the advantages, limitations, and specific requirements of your vacuum forming project, composite molds can offer a durable and versatile solution for producing high-quality vacuum-formed parts.
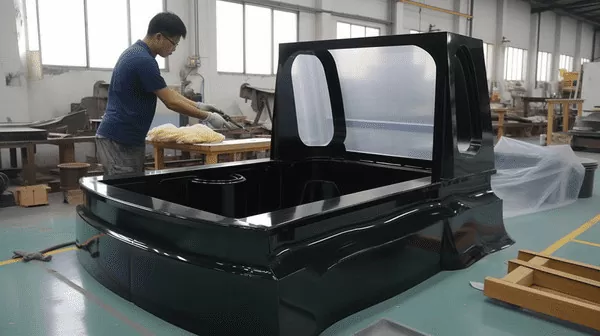
IV. Aluminum Molds
A. Description and Characteristics:
Aluminum molds used for vacuum forming applications are widely renowned for their superior characteristics such as thermal conductivity, durability and versatility. Aluminum molds have long been considered among the premier choices for use in this application. A. Description and Characteristics: Wrought aluminum is one of the top choices among mold materials when it comes to vacuum forming applications due to its exceptional properties such as thermal conductivity, durability and versatility – three hallmarks that aluminum stands out against in terms of its applications in various vacuum forming mold applications.
B. Consider Aluminum Molds for Vacuum Forming:
Aluminum molds present several advantages that make them highly desirable in vacuum forming applications:
Thermal Conductivity: Aluminum’s excellent thermal conductivity facilitates efficient heat transfer during vacuum forming processes, leading to uniform heating of plastic sheets for consistent pressure forming, and higher quality parts.
Durability and Longevity: Aluminum molds are exceptionally robust, withstanding repeated uses without deforming or warping, as well as having an extended lifespan when compared to other mold materials – making them the more economical long-term choice.
Precision and Accuracy: Aluminum molds can be machined with exceptional precision, enabling the creation of intricate details and complex shapes with pinpoint accuracy. This feature makes aluminum molds suitable for industries requiring consistent vacuum-formed parts with precise dimensions.
Aluminum molds are extremely flexible and compatible with various plastics used for vacuum forming. They can accommodate various thermoplastic sheets including polyvinyl chloride (PVC) and acrylonitrile butadiene styrene (ABS), among others.
C. Different Methods of Creating Aluminum Molds:
There are two primary methods of creating aluminum molds for vacuum forming:
CNC Machining: Aluminum molds can be created using CNC (Computer Numerical Control) machining. CNC machines precisely cut and shape solid blocks of aluminum, following the design specifications. This method allows for accurate replication of complex shapes and intricate details.
Casting: Another method involves casting aluminum molds. Molten aluminum is poured into a pre-formed cavity, which replicates the desired mold shape. This casting process is well-suited for producing aluminum molds with intricate features and complex geometries.
D. Common Applications and Industries Using Aluminum Molds in Vacuum Forming:
Aluminum molds find applications across various industries that utilize the vacuum forming technique, including:
Automotive Industry: Aluminum molds are extensively used for manufacturing automotive components, such as interior trims, instrument panels, and exterior body parts.
Consumer Goods: Industries producing consumer goods, such as appliances, electronic enclosures, and product packaging, utilize aluminum molds for high-quality and precise vacuum-formed parts.
Aerospace Industry: Aluminum molds are used in the production of components for aerospace applications, including aircraft interiors, seating systems, and structural elements.
Industrial Equipment: Aluminum molds are employed in the manufacturing of industrial equipment components, such as machine housings, enclosures, and protective covers.
Aluminum molds are favored in industries where precision, durability, and consistent quality are paramount. Their thermal conductivity, versatility, and longevity make them a preferred choice for producing high-quality vacuum-formed parts across various sectors.
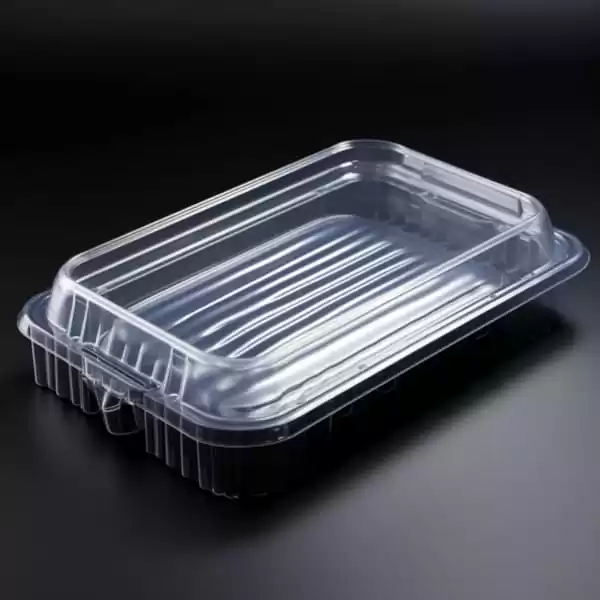
V. Machined Aluminum Molds
A. Description and Characteristics:
Machined aluminum molds used in vacuum forming machines are precision-engineered molds made from aluminum. They are created through CNC (Computer Numerical Control) machining processes, which involve cutting and shaping solid blocks of aluminum to the desired mold design. Machined aluminum molds offer exceptional accuracy and durability, making them a popular choice for vacuum forming applications.
B. Advantages and Suitability for Specific Applications:
Machined aluminum molds provide several advantages and are particularly suitable for specific applications:
- Precision and Accuracy: The CNC machining process ensures precise reproduction of complex shapes and intricate details, resulting in highly accurate vacuum-formed parts.
- Durability: Aluminum is a strong and robust material that can withstand the rigors of the vacuum forming process, including exposure to high temperatures and pressures.
- Longevity: Machined aluminum molds have a longer lifespan compared to other mold materials. They can withstand repeated use and maintain their structural integrity over time.
- High-Volume Production: Machined aluminum molds are well-suited for high-volume production runs due to their durability and ability to maintain consistent results over extended periods.
C. Process of Creating Machined Aluminum Molds:
The creation of machined aluminum molds involves the following steps:
- Design: The mold design is created using CAD (Computer-Aided Design) software, specifying the desired shape, dimensions, and intricate details.
- Material Selection: High-quality aluminum blocks are selected for machining, ensuring they possess the necessary properties for the vacuum forming process.
- CNC Machining: CNC machines are programmed to cut and shape the aluminum blocks based on the mold design. The process involves precision cutting, milling, and drilling to achieve the desired mold shape.
- Finishing: The machined aluminum mold undergoes finishing processes such as polishing, smoothing, and surface treatment to ensure a high-quality mold surface.
D. Examples of Industries Utilizing Machined Aluminum Molds in Vacuum Forming:
Machined aluminum molds find extensive use in various industries where vacuum forming is employed, including:
- Automotive Industry: Machined aluminum molds are utilized for manufacturing automotive components such as dashboards, door panels, and exterior trim parts.
- Consumer Electronics: Industries producing electronic device enclosures, such as mobile phones and tablets, utilize machined aluminum molds for precise and durable vacuum-formed parts.
- Medical Equipment: Machined aluminum molds are used in the production of medical equipment components, including instrument casings, covers, and housings.
- Industrial Packaging: Machined aluminum molds are employed in the production of custom-formed packaging solutions for industrial products, ensuring secure and efficient packaging.
Machined aluminum molds offer exceptional precision, durability, and suitability for high-volume vacuum forming production. Their versatility and ability to reproduce intricate details make them an ideal choice for industries that require precise and durable vacuum-formed parts.
VI. Cast Aluminum Molds
Cast aluminum molds used for vacuum forming are created by pouring molten aluminum into preformed cavities, offering unique characteristics which make them well suited to particular vacuum forming applications.
Cast aluminum molds offer several distinct advantages and features that set them apart, such as:
Complex Designs: The casting process makes possible the creation of molds with intricate details and complex forms, providing industries with highly precise vacuum-formed parts an opportunity for greater customization.
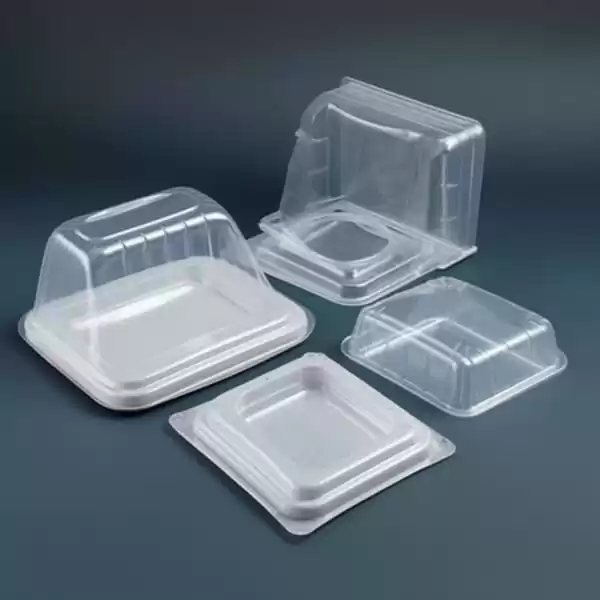
Heat Transfer: Cast aluminum plastic sheet molds feature outstanding heat transfer properties, effectively dispersing heat across their entirety during vacuum forming processes to ensure even heating and consistent shaping of plastic sheets.
Durability: Cast aluminum molds are highly resilient, lasting through repeated use without warping or deforming, providing long-term cost effectiveness in high volume production environments over plastic materials. Their excellent resistance to wear provides longevity as well as cost efficiency for longevity and cost efficiency in mass production environments.
C. Process of Creating Cast Aluminum Molds:
The process of creating cast aluminum molds for vacuum forming involves the following steps:
- Mold Design: The mold design is created based on the desired shape and features of the vacuum-formed part.
- Pattern Creation: A pattern is formed, typically made of wood, foam, or other materials, to serve as a template for the mold cavity.
- Mold Cavity Creation: The pattern is placed in a mold box, and a mixture of sand and bonding agents is packed around it. This creates the mold cavity in which the molten aluminum will be poured.
- Casting: Molten aluminum is poured into the mold cavity and allowed to cool and solidify.
- Finishing: Once the cast aluminum mold has cooled, it undergoes finishing processes such as sanding, polishing, and machining to achieve the desired surface finish and dimensional accuracy.

D. Applications and Industries Benefiting from Cast Aluminum Molds in Vacuum Forming:
Cast aluminum molds find applications in various industries where vacuum forming is employed, including:
- Automotive Industry: Cast aluminum molds are used in the production of automotive components such as exterior body panels, bumpers, and grille inserts.
- Consumer Goods: Industries producing consumer goods, including appliances, electronics, and packaging, benefit from cast aluminum molds for producing high-quality and intricate vacuum-formed parts.
- Aerospace Industry: Cast aluminum molds are utilized for manufacturing aerospace components such as interior panels, ducting systems, and cabin furnishings.
- Industrial Equipment: Cast aluminum molds are employed in the production of industrial equipment components, such as machine housings, enclosures, and structural elements.
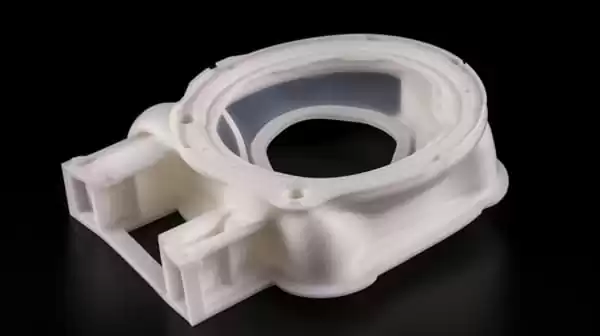
Cast aluminum molds provide exceptional precision, durability, and the ability to reproduce intricate details in vacuum-formed parts. Their superior heat transfer properties and longevity make them a preferred choice in industries that require highly complex and durable vacuum-formed components.
Conclusion
Conclusion Vacuum forming molds are crucial elements in the vacuum forming process, helping shape plastic sheets into desired forms using heat and pressure. We explored different kinds of vacuum forming molds commonly employed during vacuum forming: wooden molds, composite molds, aluminum molds (machined aluminum or cast), machined aluminum or cast aluminum.
Each type of mold offers distinct advantages. Wooden molds provide cost-effective prototyping and low-volume production solutions while composite ones boast durability and versatility. Aluminum machines or cast molds stand out for their excellent heat conductivity, precision, and durability – making them a top pick in many applications.