Introduction
When it comes to vacuum formed parts, the finish applied to the surface plays a crucial role in both the aesthetics and functionality of the final product. The finish not only enhances the visual appeal but also provides protection and durability to the vacuum formed parts. In this article, we will explore the significance of finishes for vacuum formed parts and delve into the various types of finishes that can be applied. Whether you are a manufacturer looking to improve your product’s appearance or a consumer seeking to understand the options available, this article will provide valuable insights into the world of finishes for vacuum formed parts.
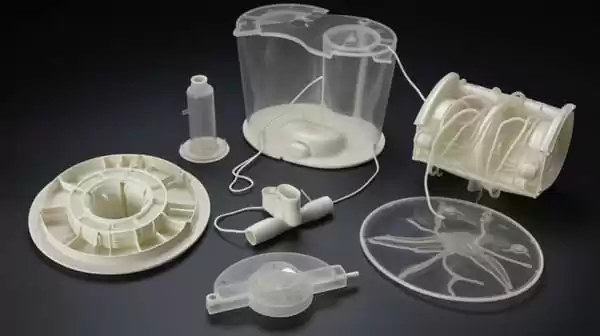
II. Understanding Vacuum Forming and the Process
A. Explanation of the Vacuum Forming Process:
Vacuum forming is a versatile manufacturing process used to create plastic parts. It involves heating a plastic material sheet until it becomes pliable and then forming it over a mold using vacuum pressure. The process can be summarized as follows:
1.The plastic material sheet is clamped in place.
2.The sheet is heated to a specific forming temperature, making it flexible.
3.Once heated, the sheet is draped over a mold.
4.Vacuum pressure is applied, drawing the sheet tightly against the mold’s surface.
5.As the sheet cools and solidifies, it takes on the desired shape of the mold, creating the desired plastic part.
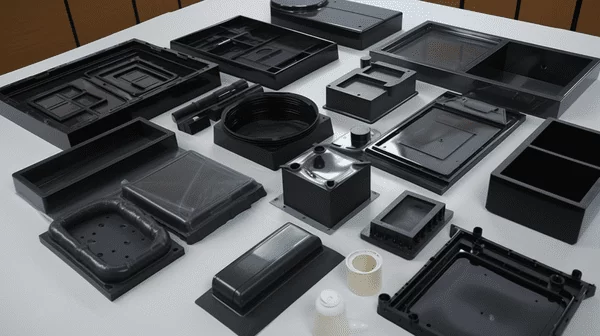
B. Vacuum Forming Machines and Forming Temperature:
Vacuum forming machines are essential equipment used in the vacuum forming process. These machines typically consist of a heating element, a mold or tooling platform, a vacuum system, and controls. The forming temperature is carefully controlled based on the type of plastic material being used. Different materials require different forming temperatures to achieve optimal results.
C. Suitable Materials for Vacuum Forming:
Vacuum forming is compatible with a wide range of plastic materials. Some common materials include acrylonitrile butadiene styrene (ABS), polyvinyl chloride (PVC), polyethylene terephthalate glycol (PETG), polycarbonate, and more. The choice of material depends on factors such as the desired properties of the final part, its intended application, and the required level of chemical resistance.
D. Types of Vacuum Forming and Vacuum Pressure:
1.Single-Sheet Vacuum Forming:
This is the most common type of vacuum forming, where a single sheet of plastic is used to form the part.
2.Pressure Forming:
In pressure forming, compressed air is used in addition to vacuum pressure to force the heated sheet against the mold surface, resulting in higher detail and sharper corners.
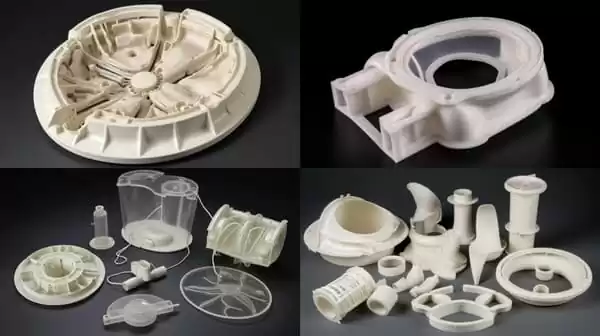
3.Plug Assist Vacuum Forming:
This process involves a plastic form, using a plug, often made of wood or aluminum, to assist in forming complex shapes by pushing the plastic material into the mold cavity.
4.Twin Sheet Thermoforming:
In this process, two sheets of plastic are heated and formed simultaneously, and then fused together to create a hollow part with increased strength.
Vacuum pressure is crucial in the vacuum forming process. It is applied to draw the heated plastic sheet tightly against the mold surface, ensuring proper alignment and a detailed finish. The level of vacuum pressure used per vacuum pump may vary depending on the specific requirements of the part being formed.
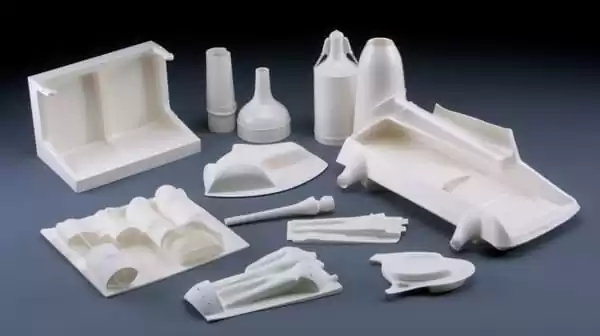
III. Advantages and Applications of Vacuum Forming process
A. Versatility of the Manufacturing Process:
Vacuum forming offers a high level of versatility in producing plastic parts. Its flexibility allows for the creation of parts with various shapes, sizes, and complexities. Whether it’s a simple enclosure or a complex component with intricate details, vacuum forming can accommodate a wide range of design requirements. Additionally, vacuum forming allows for the production of both large and small parts, making it suitable for diverse applications.
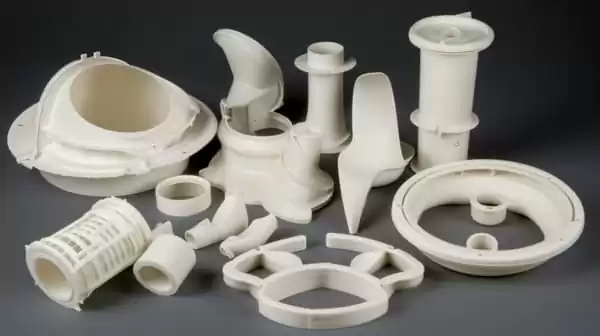
B. Wide Range of Applications in Different Industries:
Vacuum forming finds applications in numerous industries due to its versatility and cost-effectiveness. Some notable industries that benefit from vacuum formed parts include automotive, packaging, electronics, medical, and consumer goods. Here are a few examples of its applications:
Automotive:
Vacuum forming is used to manufacture interior components, such as dashboards, door panels, and trim pieces.
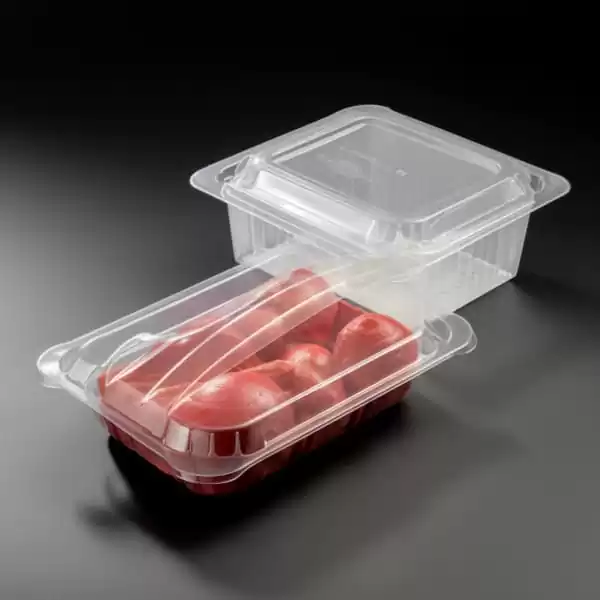
Packaging:
Vacuum formed trays and blister packs are commonly used for food packaging, electronic device packaging, food storage containers and retail display purposes.
Electronics:
Vacuum forming is employed to create enclosures and housings for various electronic devices, ensuring protection and functionality.
Medical:
The medical industry utilizes vacuum formed parts for items like medical equipment casings, device components, and custom trays for sterile packaging.
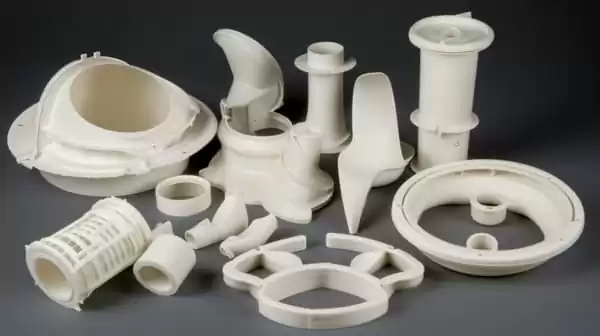
C. Cost-Effectiveness and Efficiency of Vacuum Forming:
One of the significant advantages of vacuum forming is its cost-effectiveness compared to other plastic manufacturing processes, such as injection molding. The low-cost tooling and quick setup time of vacuum forming make it an attractive option for small to medium production runs. Additionally, vacuum forming allows for efficient material usage, reducing waste and optimizing production costs. The process also offers faster turnaround times, enabling manufacturers to meet tight deadlines and market demands effectively.
In conclusion, vacuum forming offers versatility, a wide range of applications, and cost-effectiveness in the manufacturing of plastic parts. Its ability to produce parts with different shapes, sizes, and complexities makes it suitable for diverse industries. Whether it’s automotive components, packaging solutions, electronic enclosures, or medical device parts, vacuum forming provides an efficient and cost-effective manufacturing process.
IV. Types of Finishes for Vacuum Formed Parts
A. Paint Finishes:
Vacuum formed parts are ideal candidates for paint finishes due to the variety of colors and finishes they can offer. Coated with paint, these parts not only add color but also provide protection from the environment. Manufacturers can create various aesthetic effects and meet design specifications with this option by coating their parts glossy, matte, or metallic colors; manufacturers may even incorporate custom designs, logos or branding elements for added visual appeal on the vacuum formed parts.
B. Textured Finishes:
Textured Finishes: Its Textured finishes add visual and tactile interest to vacuum formed parts, adding tactile grip or tactile functionality while making them more visually appealing and tactilely functional. From smooth textures to intricate patterns, textured finishes offer versatility that can be tailored to specific design preferences or product needs.
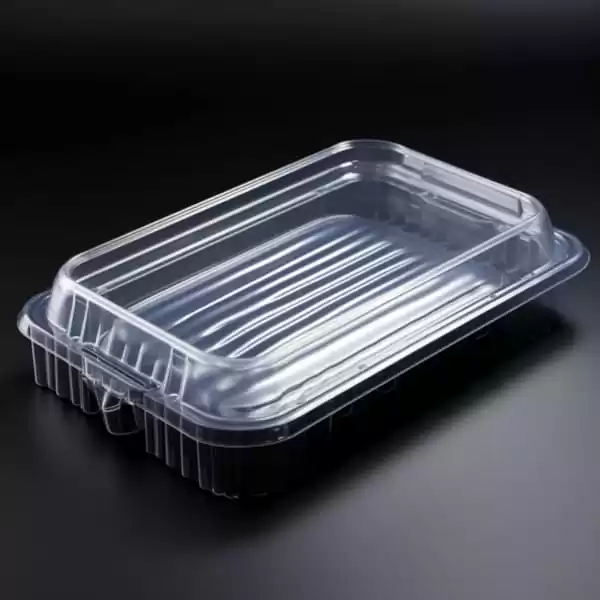
C. Graphic Overlays:
Graphic overlays are useful when vacuum formed parts require labels, instructions or functional markings such as labels. Made from durable materials like polycarbonate or polyester and adhered directly onto the parts’ surfaces, graphic overlays provide vital information or enhance user experiences and are commonly seen on control panels, instrument panels and product branding applications.
D. Clear Finishes:
Clear finishes are applied to vacuum formed parts when transparency or visibility of the underlying components is desired. These finishes provide a clear, glossy surface that allows for the visibility of internal components or showcases the aesthetics of the formed part itself. Clear finishes are commonly used in applications such as display cases, packaging, and protective covers.
E. Custom Finishes:
Custom finishes offer endless possibilities for vacuum formed parts. Manufacturers can apply specialized coatings, textures, or patterns to achieve unique effects or meet specific requirements. For example, finishes that provide anti-glare properties for outdoor displays, chemical resistance for harsh environments, or UV protection for outdoor applications. Custom finishes allow for creativity and customization, ensuring that the vacuum formed parts meet the desired functional and aesthetic goals.
In conclusion, vacuum formed parts can be finished with various options to enhance their appearance, functionality, and durability. Whether it’s paint finishes for vibrant colors, textured finishes for tactile appeal, graphic overlays for labeling, clear finishes for visibility, or custom finishes for specialized requirements, each option adds value and uniqueness to the final product. Manufacturers can choose the most suitable finish based on their specific needs and the intended application of the vacuum formed parts.
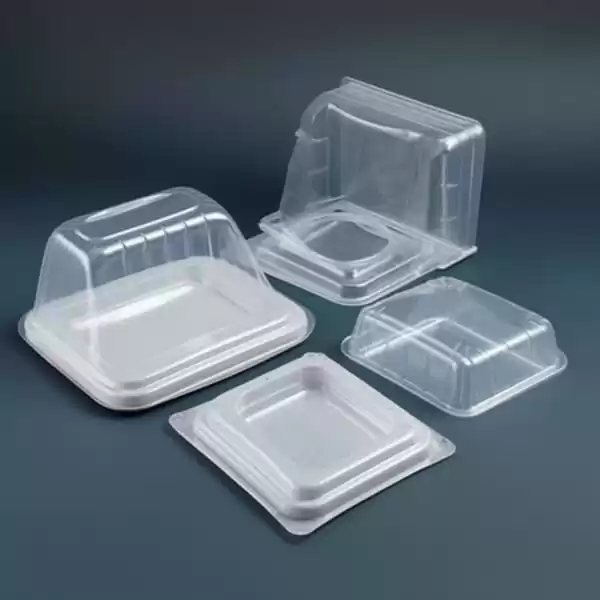
V. Post-Processing Techniques for Vacuum Formed Parts
A. Removing Vacuum Formed Parts from the Mold Surface:
Once the vacuum forming process is complete and the formed parts have cooled and solidified, they need to be carefully removed from the mold surface. This is typically done by manually releasing the clamps or vacuum pressure and gently lifting the parts away from the mold. Care must be taken to avoid any damage or distortion to the formed parts during the removal process.
B. Cutting Vacuum Formed Items using a Roller Cutter or Other Tools:
To achieve precise shapes and sizes, vacuum formed parts often require cutting. A common tool used for this purpose is a roller cutter machine, which consists of a sharp rotating blade that rolls along the material, creating clean and accurate cuts. Roller cutters allow for efficient and consistent cutting of vacuum formed items. Alternatively, other cutting tools such as saws, routers, or laser cutters may be used depending on the specific requirements of the parts.
C. Creating Holes and Features in Vacuum Formed Parts:
Vacuum formed parts often need holes, slots, or other features to accommodate fasteners, connectors, or functional elements. Various techniques can be employed to create these features. For example, drilling or punching can be used to create holes of different sizes. Heat or specialized tools can be applied to create indentations, ridges, or textured surfaces. The choice of technique depends on the material, part design, and desired outcomes.
D. Other Post-Processing Techniques (e.g., Screen Printing, Hot Stamping):
In addition to removing and cutting vacuum formed parts, various other post-processing techniques can be applied to enhance their appearance and functionality. Screen printing allows for the application of precise and detailed graphics, logos, or labels onto the surface of the parts. Hot stamping involves the transfer of foil or metallic finishes onto the vacuum formed plastic parts using heat and pressure, adding a decorative or branding element. These techniques offer customization options and can elevate the visual appeal of the vacuum formed parts.
In conclusion, post-processing techniques play a vital role in refining and customizing vacuum formed parts. Removing the parts from the mold surface, cutting them accurately, and creating necessary features are essential steps in the production process. Additionally, techniques like screen printing and hot stamping offer opportunities for branding and decorative enhancements. By employing these post-processing techniques, manufacturers can ensure that vacuum formed parts meet the desired specifications, functionality, and visual appeal required for their intended applications.
VI. Examples of Vacuum Formed Products
A. Automotive Components:
Vacuum forming finds extensive use in the automotive industry for manufacturing various components. Examples of vacuum formed automotive parts include interior trim pieces, such as dashboards, door panels, center consoles, and instrument clusters. Additionally, exterior components like bumper covers, fender liners, and wheel arches can also be vacuum formed. The lightweight and customizable nature of vacuum formed parts make them ideal for automotive applications.
B. Food Packaging:
Vacuum forming plays a crucial role in the food packaging industry, offering a cost-effective and versatile solution. Vacuum formed trays, containers, and blister packs are commonly used for food packaging purposes. These vacuum formed products provide protection, preservation, and display of food items. Examples include food trays for fruits, vegetables, and baked goods, as well as blister packs for candies, chocolates, and small snack items.
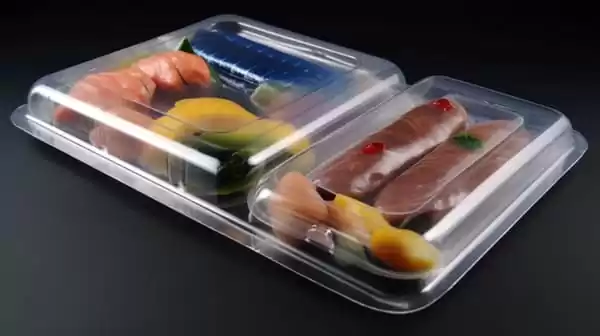
C. Electronic Device Casings:
Vacuum forming is widely employed for the production of casings and enclosures for electronic devices. These casings provide protection and structural support for various electronic components. Examples of vacuum formed electronic device casings include those used for mobile phones, tablets, laptops, gaming consoles, and audio equipment. Vacuum forming allows for precise customization, accommodating specific design requirements and branding elements.
D. Light Diffusers:
Vacuum formed light diffusers are commonly used in architectural lighting and other applications that require controlled illumination. These diffusers distribute and scatter light evenly, reducing glare and providing aesthetically pleasing lighting effects. Vacuum formed light diffusers are found in various settings, including commercial buildings, residential spaces, retail environments, and signage applications.
E. Other Applications in Various Industries:
Apart from the automotive, food packaging, electronic, and lighting industries, vacuum formed products are utilized in numerous other sectors. Some examples include:
Medical industry: Vacuum formed trays and sterile packaging solutions for medical devices and equipment.
Consumer goods: Vacuum formed parts for household appliances, toys, and personal care products.
Industrial equipment: Vacuum formed panels, covers, and enclosures for machinery and equipment.Display and signage: Vacuum formed panels, display stands, and signage solutions for retail and promotional purposes.
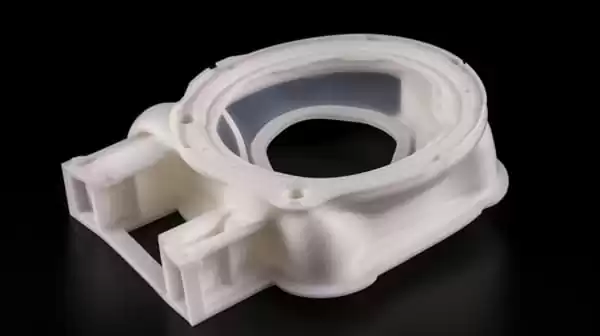
Marine and recreational vehicles: Vacuum formed parts for boat interiors, RV components, and recreational vehicle accessories.
In conclusion, vacuum forming is a versatile manufacturing process that finds applications in various industries. From automotive components and food packaging to electronic device casings, light diffusers, and beyond, vacuum formed products are widely used. Their lightweight, customizable, and cost-effective nature makes them suitable for diverse applications, providing solutions for both functional and aesthetic needs across different sectors.
Conclusion
In conclusion, finishes play a crucial role in enhancing the quality and aesthetics of vacuum formed parts. The type of finish applied to these parts can significantly impact their appearance, functionality, and durability. Whether it’s paint finishes, textured surfaces, graphic overlays, clear coatings, or custom finishes, each option adds value and uniqueness to the final product.
We have explored the vacuum forming process, which involves heating a plastic material, placing it over a mold, and applying vacuum pressure to shape it into the desired form. This process offers several benefits, including cost-effectiveness, flexibility in design, and the ability to produce parts of various sizes and complexities. Vacuum forming machines, along with appropriate forming temperatures and suitable materials, are key considerations in achieving successful outcomes.
Furthermore, vacuum formed products exhibit versatility and find applications across a wide range of industries. From automotive components and food packaging to electronic device casings and light diffusers, vacuum forming proves its adaptability and effectiveness. Its cost-effectiveness, quick turnaround times, and the ability to produce both small and large parts make it a favorable choice in diverse sectors.
In conclusion, finishes, the vacuum forming process, and the wide range of applications for vacuum formed products highlight the significance of this manufacturing technique. Whether it’s creating customized automotive parts, functional food packaging, sleek electronic device casings, or innovative light diffusers, vacuum forming offers a reliable and efficient solution.
Overall, vacuum forming continues to be a preferred manufacturing process due to its versatility, cost-effectiveness, and ability to produce high-quality plastic parts. With the right finishes, vacuum formed products can meet both functional and aesthetic requirements, making them an indispensable choice for industries seeking efficient and customizable solutions.