Introduction
Plastics play a crucial role in the manufacturing and product development industries, offering versatility, durability, and cost-effectiveness. Shaping plastics into desired forms is a fundamental aspect of the production process. Two widely used methods for shaping plastics are thermoforming and vacuum forming. Understanding the differences between these two processes is essential for manufacturers and designers seeking to choose the most suitable method for their specific needs. In this article, we will explore the distinctions between thermoforming and vacuum forming, highlighting their unique characteristics, applications, and advantages. By the end, you will have a clear understanding of these two processes and their implications for the manufacturing industry. So let’s dive in and discover the world of plastic thermoforming and vacuum forming!
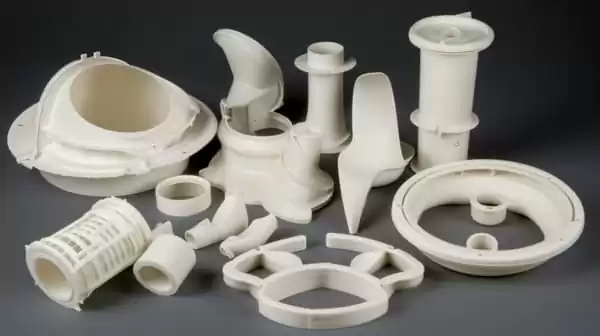
II. What is Thermoforming?
Thermoforming is a widely used manufacturing process for shaping plastic sheets into desired forms. Here’s a breakdown of the thermoforming process:
1.Heating the Plastic Sheet:
The process begins by heating a plastic sheet made of thermoplastic material. The sheet is heated to a specific temperature until it reaches a pliable state. Various heating methods, such as radiant heat, convection heat, or infrared radiation, can be employed.
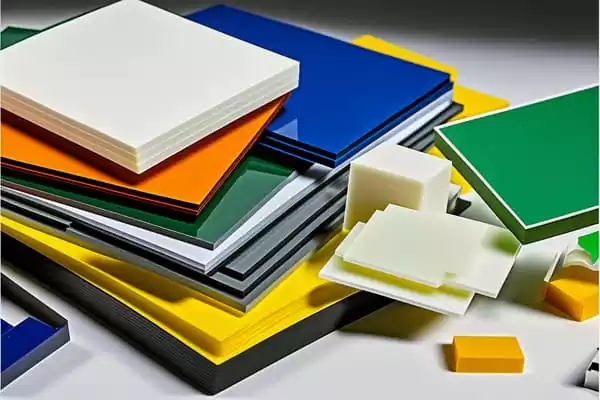
2.Shaping over a Mold:
Once the plastic sheet is sufficiently heated, it is carefully placed over a mold. The mold is typically made of metal or composite materials and has the desired shape or form that the plastic will take.
3.Cooling and Solidifying:
After the heated sheet mold plastic is draped over the mold, it is left to cool and solidify. Cooling can be accelerated by using fans or water jets to speed up the process. As the plastic cools, it maintains the shape of the mold and solidifies into the desired form.
4.Trimming and Finishing:
Once the formed plastic has fully cooled and solidified, it is removed from the mold. Any excess material or rough edges are trimmed away to achieve the desired final shape. Additional finishing processes, such as polishing or surface treatment, can be performed to enhance the aesthetics and functionality of the product.
Thermoforming is known for its versatility and efficiency in creating a wide range of products, including packaging materials, disposable cups and plates, automotive interior components, and large-scale industrial items like plastic pallets. It offers a cost-effective solution for producing plastic parts with relatively low tooling and setup costs compared to other manufacturing processes.
III. What is Vacuum Forming?
Vacuum forming is a subset of the thermoforming process that involves an additional step utilizing vacuum force. Here’s how vacuum forming differs from conventional thermoforming:
1.The Vacuum Forming Process:
The vacuum forming process starts with heating a plastic sheet until it becomes pliable, similar to the thermoforming process. However, during vacuum forming, an extra step is introduced.
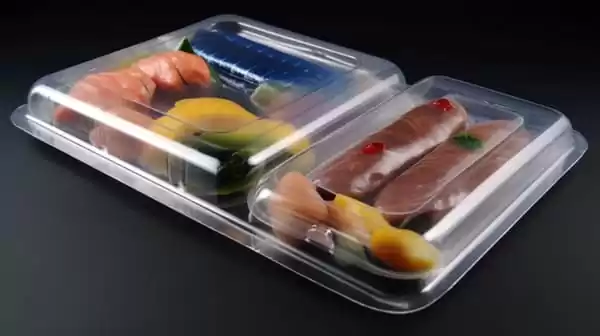
2.Applying Vacuum:
After the plastic sheet is heated and positioned over the mold, a vacuum is applied. The vacuum removes the air trapped between the sheet and the mold. This creates a vacuum pressure that assists in pulling the heated sheet tightly against the contours of the mold.
3.Tightening the Plastic:
The vacuum force plays a crucial role in the vacuum forming process. It ensures that the plastic sheet conforms precisely to the shape of the mold, capturing all the fine details and contours. The vacuum pressure tightens the plastic against the mold, resulting in a high level of accuracy and replication.
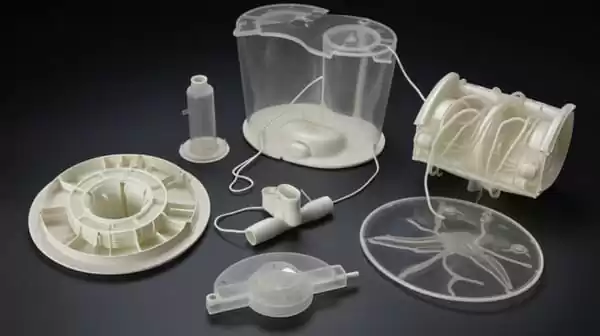
4.Cooling and Separation:
Once the vacuum forming process is complete, the formed plastic part is cooled to maintain its shape and rigidity. After cooling, the vacuum formed part is separated from the mold. The result is a plastic component that accurately matches the mold’s shape and detail.
Vacuum forming offers advantages in creating products that require intricate mold details and precise replication. Its ability to pull the heated sheet tightly against the mold’s contours makes it suitable for applications such as medical equipment housings, electronic enclosures, custom-designed trays, and point-of-purchase displays. The vacuum forming process provides manufacturers with a cost-effective method to produce high-quality plastic components with excellent detail and accuracy.
IV. Key Differences between Thermoforming and Vacuum Forming
Thermoforming and vacuum forming are two distinct processes within the realm of plastic shaping. Let’s explore the key differences that set them apart:
1.Methodology:
Thermoforming involves stretching and pressing the heated plastic sheet onto the mold’s surface. This action allows the sheet to conform to the mold’s shape. In contrast, vacuum forming utilizes the force of vacuum to remove air between the hot plastic sheet and the mold. The vacuum force pulls the heated sheet tightly against the mold’s contours, resulting in precise replication.
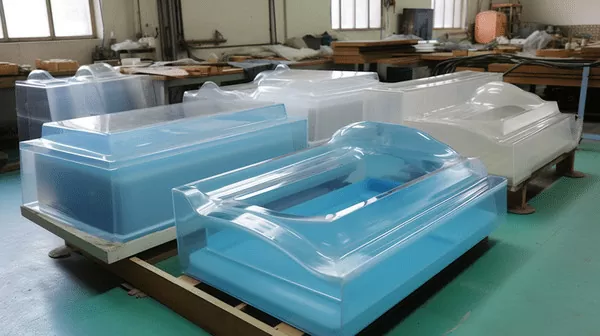
2.Complexity:
Vacuum forming introduces an additional step compared to thermoforming. While thermoforming only requires heating, shaping, and cooling the plastic sheet, vacuum forming requires the application of vacuum to create the necessary force. This additional step adds complexity to the process.
3.Precision:
Vacuum forming offers greater accuracy when it comes to replicating intricate mold details. The vacuum force ensures that the heated plastic sheet tightly adheres to the mold’s surface, capturing even the finest contours and features. Thermoforming, while capable of producing accurate shapes, may have limitations in reproducing intricate details.
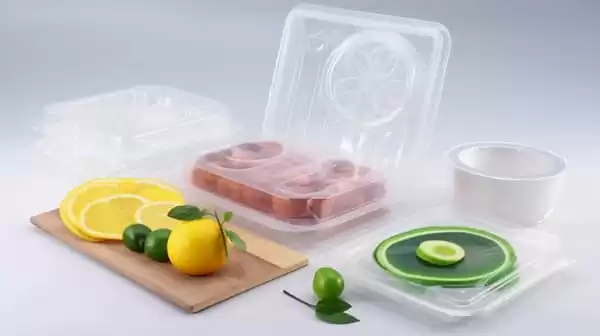
4.Tooling:
Thermoforming generally requires simpler molds due to the stretching and pressing action, both vacuum which aids in conforming the plastic sheet to the mold’s shape. On the other hand, vacuum forming necessitates specific design considerations for the mold. The mold design must allow the vacuum force to pull the sheet tightly against it, requiring careful engineering and construction.
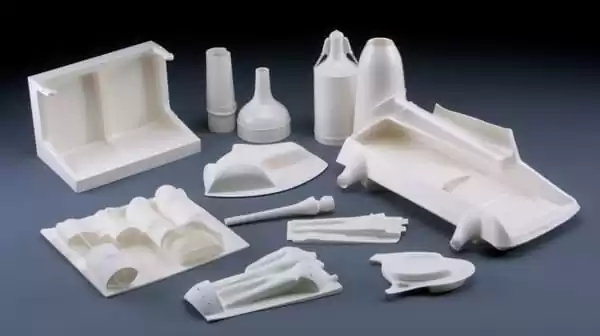
5.Cost:
Thermoforming is often more cost-effective compared to vacuum forming. This is primarily because thermoforming requires simpler molds, which are typically less expensive to produce. In addition, vacuum forming requires the use of vacuum equipment to generate the necessary force, adding to the equipment and operational costs.
Understanding these key differences between thermoforming and vacuum forming helps manufacturers make informed decisions about the most suitable process for their specific needs. While thermoforming offers cost-effectiveness and simplicity, vacuum forming excels in precision and intricate mold replication. Both processes have their unique advantages and considerations, making them valuable tools in the world of plastic component production.
V. Exploring Pressure Forming as an Alternative
In addition to thermoforming twin sheet forming and vacuum forming, another plastic shaping method worth exploring is pressure forming. Here’s an overview of pressure forming as an alternative process:
1.Introduction to Pressure Forming:
Pressure forming is a plastic shaping method that shares similarities with thermoforming and vacuum forming. It involves the use of compressed, air pressure, or other pressure methods to shape the plastic sheet over a mold.
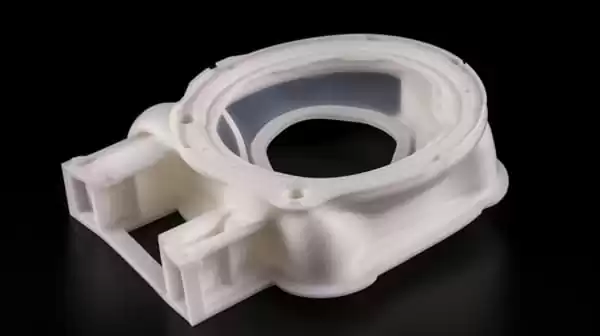
2.Process Involving Compressed Air or Pressure:
In pressure forming, the plastic sheet is heated until it becomes pliable, similar to thermoforming and vacuum forming. Once heated, the sheet is positioned over the mold. However, instead of relying solely on vacuum force or stretching and pressing, pressure forming applies positive pressure using compressed air or other methods. This pressure is used to press the heated plastic sheet onto the mold, allowing it to conform to the mold’s shape.
3.Achieving Fine Details and Replicating Intricate Mold Designs:
Pressure forming excels in achieving fine details and replicating intricate mold designs, similar to vacuum forming. The application of pressure allows for better control over the plastic sheet, resulting in accurate reproduction of complex features and textures.
4.Comparison to Vacuum Forming and Thermoforming:
Pressure forming differs from vacuum forming in terms of the force used to shape the plastic sheet. While vacuum forming utilizes negative pressure or vacuum force, pressure forming utilizes positive pressure. In terms of methodology, the pressure forming process is more similar to thermoforming, as both involve applying pressure to shape the plastic sheet. However, pressure forming offers advantages in achieving fine details and replicating intricate mold designs, making it a preferred choice for products requiring high-level precision.
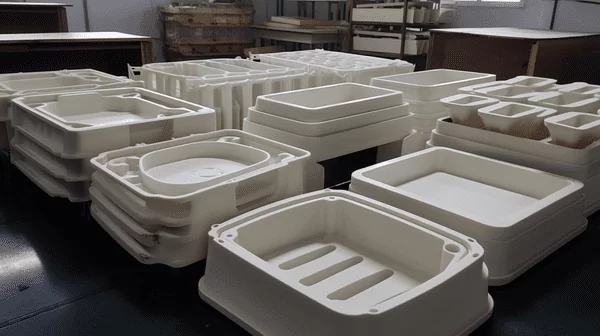
Pressure forming offers manufacturers an alternative method for shaping plastic components, particularly when fine details and intricate mold replication are essential. By utilizing compressed air or other pressure methods, pressure forming provides flexibility and control over the shaping process. When compared to vacuum forming and thermoforming, pressure forming stands out for its ability to achieve precise detailing.
VII. Advantages of Thermoforming and Vacuum Forming
Thermoforming and vacuum forming offer several advantages that make them popular choices in the plastics manufacturing industry. Let’s explore their key advantages:
- Flexibility in Creating Large Parts and Complex Shapes: Thermoforming and vacuum forming processes provide flexibility in producing large parts and complex shapes. The pliable nature of the heated plastic sheet allows it to be molded into various sizes and configurations. This flexibility makes these processes suitable for a wide range of products, from packaging materials to automotive components.
- Cost-Effectiveness for Lower Production Volumes: Thermoforming and vacuum forming are cost-effective solutions, particularly for lower production volumes. These processes require relatively low tooling and setup costs compared to other manufacturing methods like injection molding. The simplicity of the mold design in thermoforming and the absence of complex equipment in vacuum forming contribute to cost savings, making them viable options for small to medium production runs.
- Ability to Achieve Fine Details and Replicate Intricate Mold Designs: Despite their cost-effectiveness and flexibility, thermoforming and vacuum forming do not compromise on achieving fine details and replicating intricate mold designs. Both processes can accurately reproduce intricate features, textures, and contours on the formed plastic parts. Vacuum forming, in particular, with its vacuum force, offers excellent precision and replication capabilities, making it suitable for applications that demand high-level detail.
These advantages make thermoforming and vacuum forming versatile options in various industries. They are widely used for producing products such as packaging materials, automotive components, medical equipment housings, electronic enclosures, and more. By leveraging the flexibility, cost-effectiveness, and precision of thermoforming and vacuum forming, manufacturers can efficiently bring their design concepts to reality while meeting their production requirements.
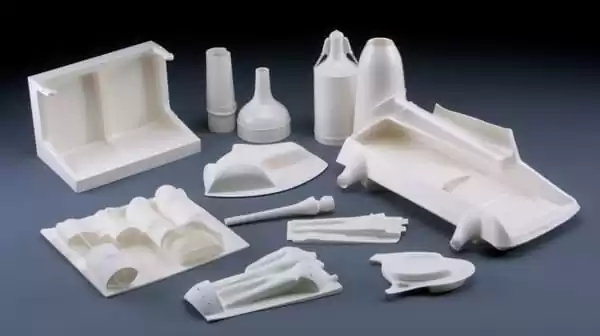
Conclusion:
Thermoforming and vacuum forming offer several advantages that make them popular choices in the plastics manufacturing industry. These advantages make thermoforming and vacuum forming versatile options in various industries. They are widely used for producing products such as packaging materials, automotive components, medical equipment housings, electronic enclosures, and more. By leveraging the flexibility, cost-effectiveness, and precision of thermoforming and vacuum forming, manufacturers can efficiently bring their design concepts to reality while meeting their production requirements.