Introduction
In the dynamic realm of modern manufacturing, the process of vacuum forming emerges as a cornerstone of innovation and efficiency. This technique, revered for its ability to transform plastic sheets into intricate shapes, plays a pivotal role in various industries. At the heart of this process are two exceptional contenders – ABS (Acrylonitrile Butadiene Styrene) and HIPS (High Impact Polystyrene) – each possessing a unique set of attributes that contribute to their widespread acclaim.
A Brief Glimpse into Vacuum Forming:
Vacuum forming stands as a testament to the art of shaping plastics with precision. By applying heat to a plastic sheet, molding it over a carefully crafted form using vacuum pressure, and allowing it to cool, a plethora of products come to life. This method finds its foothold in industries as diverse as packaging, automotive, and electronics, serving as a cornerstone of versatile manufacturing.
Unveiling ABS and HIPS:
Meet the protagonists of our exploration – ABS and HIPS. Acrylonitrile Butadiene Styrene, affectionately known as ABS, boasts unparalleled strength and resilience, making it an optimal choice for products that demand unyielding structural integrity. On the other hand, we have High Impact Polystyrene, or HIPS, which touts exceptional impact strength and formability, captivating industries with its cost-effectiveness and versatility.
Peering into the Journey Ahead:
As we embark on this enlightening journey, our focus will be twofold. First, we will delve into the intrinsic differences that set ABS and HIPS apart in the context of vacuum forming. These disparities, ranging from material properties to their behavior during the vacuum forming process, lay the foundation for their distinct roles in the manufacturing arena. Second, we will explore the suitability and applications of these materials, shedding light on the industries they serve and the products they help bring to life.
With the stage set and the spotlight on ABS and HIPS, we invite you to join us in deciphering the intricacies that shape these remarkable thermoplastics and the pivotal roles they play in the world of vacuum forming.
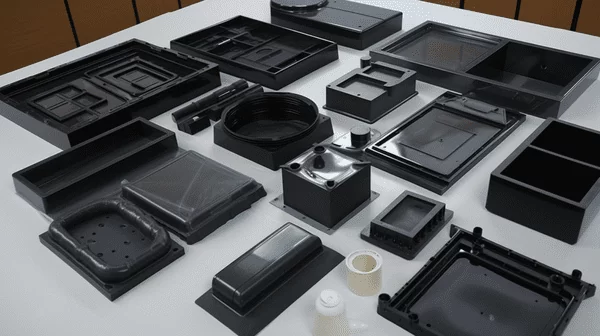
II. Vacuum Forming: A Closer Look
A. Unveiling the Vacuum Forming Process:
At the heart of innovative manufacturing lies the captivating technique known as vacuum forming. This process, which marries artistry with engineering precision, involves a meticulous dance between heat and pressure. To witness this transformation, a plastic sheet is subjected to controlled heating until it becomes pliable – a state where creativity meets malleability. The sheet is then carefully draped over a meticulously crafted mold. Enter the stage: vacuum pressure. As it is applied, the plastic sheet adheres to the contours of the mold, assuming a shape that mirrors imagination. And just as quickly as the magic unfolds, the sheet cools, solidifying its newfound form. Thus, vacuum forming stands as a testament to the mastery of shaping plastics with finesse and accuracy.
B. The Crucial Role of Material Selection:
In the realm of vacuum forming, the material selected serves as the bedrock upon which the final product’s success is built. Just as a symphony conductor meticulously selects the right instruments to craft a harmonious melody, manufacturers must make astute choices when it comes to materials. Material properties, such as strength, impact resistance, and heat tolerance, determine the product’s suitability for its intended purpose. This pivotal decision can spell the difference between a resilient, enduring creation and a lackluster endeavor that falls short of expectations. As the saying goes, the right material is the canvas upon which the masterpiece of vacuum forming is painted.
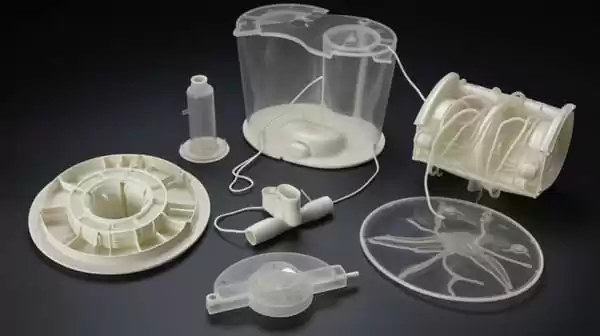
C. Embarking on the ABS and HIPS Exploration:
With the canvas of high quality materials selection now vividly set, our journey takes a thrilling turn as we delve into the realm of ABS and HIPS. These two remarkable thermoplastics step onto the stage of vacuum form with their unique attributes and potential. As we explore their differences, similarities, and distinct behaviors during the vacuum forming plastics process, a tapestry of insights will emerge, shedding light on how each material responds to the dance of heat, pressure, and creativity. Join us as we unravel the secrets held by ABS and HIPS, and how they infuse the vacuum forming process with their unparalleled characteristics.
III. ABS – Acrylonitrile Butadiene Styrene
A. Unveiling the Essence of ABS:
Acrylonitrile Butadiene Styrene, or ABS, emerges as a titan in the realm of thermoplastics, renowned for its versatility and strength. This amalgamation of acrylonitrile, butadiene, and styrene creates a symphony of properties that set ABS apart in the world of vacuum forming.
B. The Mosaic of ABS’s Attributes:
As ABS takes its place under the vacuum forming spotlight, a trio of key characteristics emerges, each contributing to its prowess in this manufacturing process.
1. Impact Resistance and Structural Integrity:
At the heart of ABS lies an exceptional resistance to impact – a trait that weaves a narrative of durability and endurance. When the vacuum forming process beckons, ABS steps forward, ready to mold itself into shapes that stand the test of time. Whether it’s a rugged machine guard or a protective electrical enclosure, ABS holds steadfast, weathering the storms of mechanical stress and safeguarding what lies within.
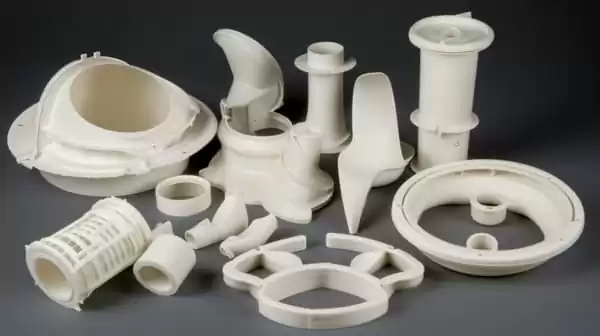
2. Chemical Resistance and Stability:
In the intricate dance of vacuum forming, ABS proves itself to be more than just a malleable material. Its robust chemical resistance ensures that the products formed retain their structure and strength, even when faced with the challenges posed by oils, additives, and an array of materials. This resilience paints a portrait of reliability, where the vacuum-formed creations maintain their integrity amidst a world of chemicals.
3. High Tensile Strength and Dimensional Stability:
As the vacuum forming process unfurls, ABS showcases its mettle with high tensile strength and dimensional stability. These traits translate into creations that not only boast enduring shapes but also stand tall in the face of fluctuating temperatures. From heat-resistant food containers to packaging materials, ABS takes on the role of a guardian, preserving both form and function.
C. ABS Applications in Vacuum Forming:
As the curtain rises on ABS’s applications in vacuum forming, a tapestry of possibilities is unveiled, spanning an array of industries and products.
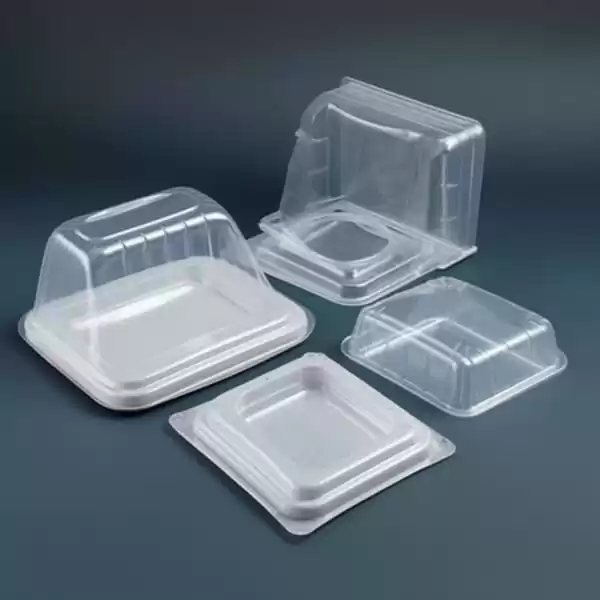
1. Electrical Enclosures and Machine Guards:
The world of electrical appliances and machinery finds a reliable ally in ABS. It forms the backbone of electrical enclosures and machine guards, lending its impact resistance and structural integrity to ensure the safety and longevity of vital components.
2. Heat-Resistant Food Containers and Packaging Materials:
Vacuum-formed heat-resistant food containers and packaging materials bear the hallmark of ABS’s chemical resistance and stability. These creations cater to industries that prioritize the preservation of food quality and safety.
3. Automotive Parts and Outdoor Applications:
The automotive arena welcomes ABS with open arms, as it takes center stage in the vacuum-formed production of vehicle parts. Furthermore, the material’s resistance to UV degradation paves the way for its outdoor applications, from structural elements to components that brave the elements with unwavering resilience.
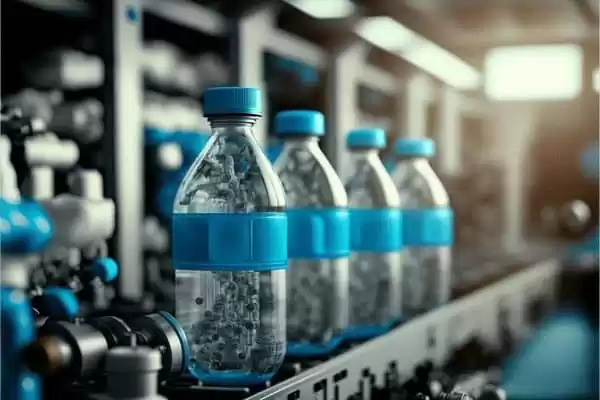
As we bid adieu to the world of ABS in vacuum forming, its role as a stalwart of strength and reliability remains etched in the annals of modern manufacturing.
V. Comparing ABS and HIPS: Suitability and Applications
A. Distinct Characteristics at a Glance:
As we stand at the crossroads of ABS and HIPS in the realm of vacuum forming, a symphony of differences unfolds. ABS emerges as the epitome of strength, embodying impact resistance and structural integrity that make it a stalwart in demanding applications. In contrast, HIPS boasts its own set of virtues, with very high impact strength, formability, and affordability taking center stage.
B. Deciphering the Art of Material Selection:
The decision to choose between ABS and HIPS in vacuum forming is an art that hinges on multiple factors. From the intended application to the functional requirements, each parameter plays a role in the intricate dance of material selection. As manufacturers weigh the balance between strength, impact resistance, cost-effectiveness, and other attributes, the ideal choice emerges – one that sets the stage for a vacuum-formed masterpiece.
C. Applications Explored and Compared:
The applications of ABS and HIPS in vacuum forming showcase their individual strengths, catering to diverse industries and needs.
1. ABS: Strength, Heat Resistance, and Structural Applications:
ABS’s journey through vacuum forming yields creations that exemplify good chemical resistance and creep resistance structural integrity. Its high impact strength makes it a prime candidate for crafting electrical enclosures, machine guards, and automotive parts. The realm of heat-resistant food and flame retardant containers and food packaging materials also embraces ABS, where its stability and dimensional prowess shine through. Furthermore, the material’s outdoor applications, fortified by its resistance to UV degradation, paint a picture of durability in the face of the elements.
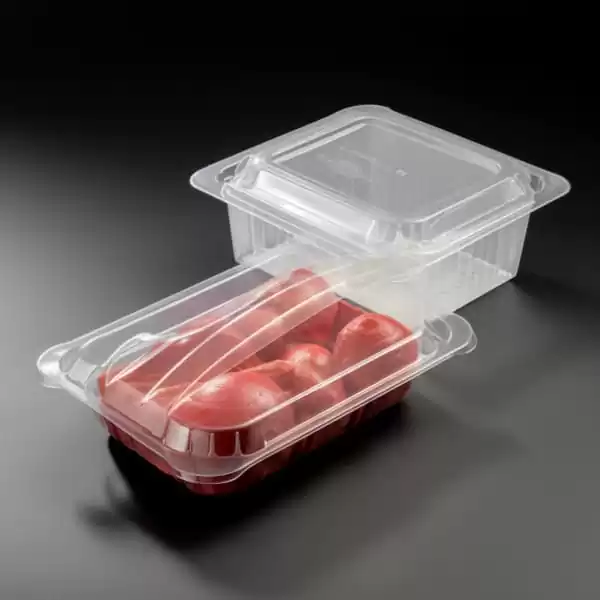
2. HIPS: Affordability, Impact Resistance, and Packaging Solutions:
HIPS, with its remarkable impact strength, lends itself beautifully to crafting packaging materials that embrace fragility with confidence. From trays that cradle contents to blister packs that offer a transparent view, HIPS’s affordability and ease of processing form a dynamic duo that resonates with industries prioritizing cost-effectiveness. While not as robust as ABS, HIPS’s impact resistant finds its niche in applications where toughness reigns supreme, making it a steadfast companion in a world where form meets function.
In this grand symposium of material comparison, ABS and HIPS take their respective places, each offering a unique melody that contributes to the harmonious crescendo of vacuum forming. As industries embrace the subtleties of their characteristics, needs, and possibilities, the choice between these thermoplastics emerges as a testament to the artistry of manufacturing, where materials dance in unison to shape a world of innovation and ingenuity.
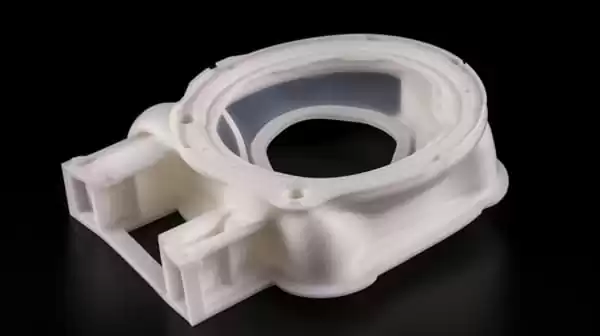
Conclusion
As our journey through the realm of vacuum forming draws to a close, we find ourselves standing at the intersection of ABS and HIPS – two remarkable thermoplastics that have left an indelible mark on the art of shaping plastics. With each material embodying a unique set of characteristics, their roles in modern manufacturing stand as a testament to innovation, resilience, and creative versatility.
In the tapestry of vacuum forming, ABS and HIPS emerge as distinct voices, each contributing to the symphony of creation. ABS dazzles with its exceptional impact resistance, chemical stability, and high tensile strength, making it a go-to choice for applications that demand unyielding structural integrity. HIPS, on the other hand, impresses with its very high impact strength, affordability, and ease of processing, finding its niche in industries where cost-effectiveness and resilience harmonize.
At the core of successful vacuum forming lies the art of material selection. This pivotal decision, influenced by a myriad of factors, shapes the destiny of the final product. From strength requirements to cost considerations, the choice between ABS and HIPS holds the power to elevate the outcome from mere creation to a masterpiece that excels in its intended application. The journey of a vacuum-formed product begins with the material selected – a decision that can ultimately make the difference between ordinary and extraordinary.
In the grand tapestry of modern manufacturing, the roles of ABS and HIPS transcend mere thermoplastics. They embody the essence of versatility, adaptability, and ingenuity, becoming the backbone of industries that span from automotive to packaging. Their significance reverberates in products that range from electrical enclosures safeguarding vital components to packaging materials cradling delicate contents. The symphony of vacuum forming finds its crescendo in the partnership of these materials, where form meets function with finesse.
As we bid adieu to our exploration of ABS and HIPS in vacuum forming, let us be reminded of the elegance and brilliance that these materials bring to the table. Informed material selection stands as the guiding star, ensuring that each creation born through the vacuum forming process emerges as a testament to the art of craftsmanship, innovation, and the limitless possibilities that shape our world.