Introduction:
Vacuum forming, a versatile manufacturing process, holds the key to transforming flat plastic sheets into three-dimensional shapes that cater to a myriad of industries and applications. From consumer electronics casings to food packaging, this technique shapes the world around us. Yet, beyond the mechanics lies a crucial element that often goes unnoticed – the texture of the vacuum-formed parts. This article embarks on a journey to uncover the art of choosing the perfect texture for vacuum-formed parts, exploring how this seemingly subtle decision can significantly impact both aesthetics and functionality. In a realm where form meets function, the texture chosen for vacuum-formed parts becomes an essential touchpoint that unites visual appeal and practicality. Let’s delve deeper into the realm of texture selection and unveil the intricacies that make it an art in itself.
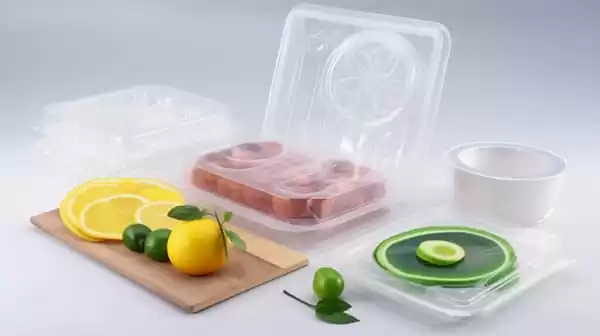
Understanding Vacuum Forming:
At the heart of modern manufacturing, vacuum forming is a process that takes flat plastic sheets and transforms them into complex three-dimensional shapes with precision and efficiency at low cost. This process involves a sequence of carefully orchestrated steps that balance heat, pressure, and design intricacies.
Heating, Molding, and Cooling:
The journey begins by heating a plastic sheet to a specific temperature, rendering it pliable and ready for transformation. Once malleable, the sheet is draped over a meticulously crafted mold. This mold is the blueprint for the final form, and its design plays a pivotal role in determining the finished product’s appearance and functionality. The plastic sheet then conforms to the mold’s contours, adhering to its shape with remarkable precision. During this phase, vacuum or compressed air is employed to ensure the plastic snugly adheres to the mold’s surface, capturing every detail and texture. Following the shaping process, cooling is of paramount importance. Rapid cooling solidifies the plastic, preserving the form and texture projected by the mold.
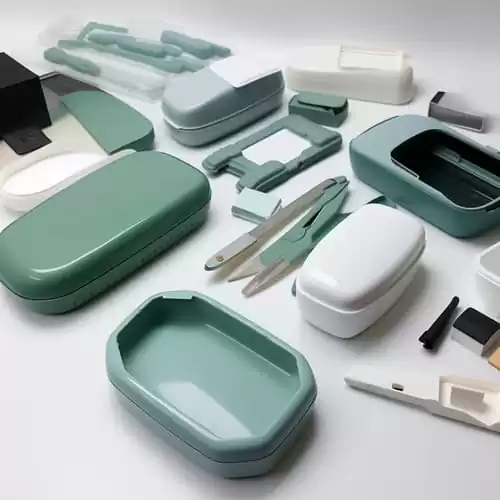
Benefits of Vacuum Forming:
The advantages of vacuum forming are manifold. Notably, this process offers a cost-effective avenue for both prototyping and production. Its ability to quickly generate prototypes with minimal tooling costs makes it a popular choice for design validation. Moreover, vacuum forming’s adaptability enables the production of parts with varying levels of complexity – from intricate components to simple forms. This versatility makes pressure forming a valuable tool in industries spanning consumer goods, automotive, and even medical devices.
3D Printing’s Role in Mold Creation:
Behind the scenes, technology takes center stage in the form of 3D printing. The fusion of traditional craftsmanship and modern innovation is evident in the creation of molds. 3D printing has revolutionized this aspect, allowing for the production of intricate molds with remarkable detail. This synergy of technology and craftsmanship empowers manufacturers to bring even the most intricate designs to life, pushing the boundaries of what is achievable through vacuum forming.
In the dynamic world of manufacturing, vacuum forming stands as a testament to innovation and precision. Its ability to harmonize heat, pressure, and form has reshaped industries, from consumer goods to automotive components. As we venture deeper into the realm of texture selection, we uncover how these formed parts gain their unique identity through textures that enhance both visual appeal and functionality.
Material Considerations:
In the world of vacuum forming, the choice of material is a critical cornerstone that influences every facet of the process. The materials selected not only dictate the end product’s physical properties but also influence the intricacies and speed of forming and the quality of the final texture.
Suitable Materials for Vacuum Forming:
Several materials stand out as prime candidates for vacuum forming due to their desirable properties. Acrylonitrile Butadiene Styrene (ABS), renowned for its high impact resistance and structural integrity, is a popular choice. Similarly, polycarbonate, celebrated for its optical clarity and robustness, finds its way into many applications. The versatility of vacuum forming is exemplified by the range of materials it accommodates, allowing manufacturers to tailor the process to the specific needs of each project.
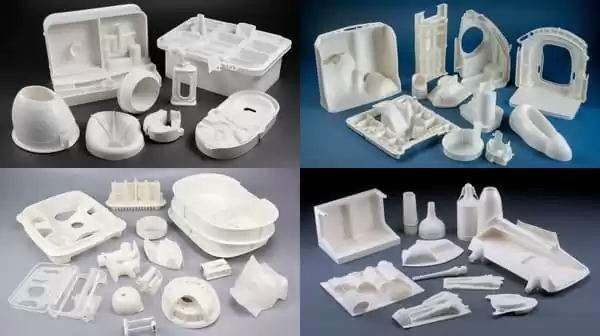
Impact of Material Properties on Forming:
Material properties weave into the very fabric of the forming process. The chosen material’s flexibility, strength, and elasticity define how it will respond to the molding process. Materials with excellent formability are preferable, as they can stretch and conform smoothly to the mold’s contours without undue stress. Uniform material thickness across the formed part ensures consistent and predictable outcomes. Additionally, materials with high impact resistance lend durability to the finished parts, increasing their suitability for various applications.
Heating: The Key to Malleability:
As the material’s properties are pivotal, so is the role of heating. The plastic sheet’s malleability hinges on reaching the correct temperature. Heating elements, such as specialized heaters or cast aluminum molds, are utilized to ensure precise and uniform heating. This controlled temperature elevation transforms the plastic sheet from a rigid form to a pliable material ready to adopt the mold’s shape. The synergy between material and heat sets the stage for successful pressure forming process.
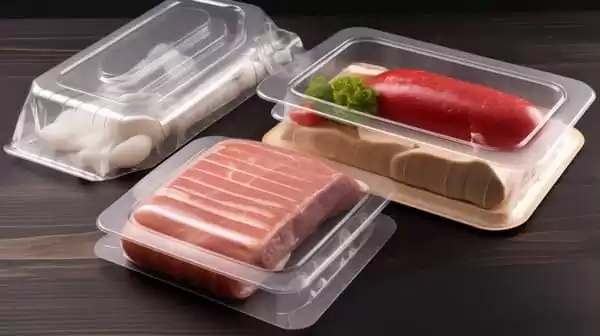
In the intricate dance of vacuum forming, materials and their properties define the process’s rhythm. The marriage of material selection, meticulous heating, and craftsmanship results in parts that boast not only the desired texture but also the strength and resilience demanded by diverse applications. As we delve further into the realm of texture, we unearth how these materials interact with molds to yield textures that both captivate the eye and fulfill functional requirements.
Achieving Texture: Mold Surface and Design:
Q4: What makes a good vacuum forming mold?
A good vacuum forming mold is a symphony of precision, functionality, and craftsmanship. It starts with an impeccable design that lays the foundation for the texture that will ultimately grace the formed parts. This is where the magic begins, the point where the desired texture is projected onto the final part.
Influence of Mold Surface on Texture:
The mold surface, akin to a canvas, imprints its intricacies onto the vacuum-formed part. The texture originates at this interface, and the mold’s surface quality and design intricacies are paramount. A polished and meticulously crafted mold yields a smooth, refined texture, while a mold with intricate patterns results in textures that captivate the eye. The nuances of the mold surface’s contact with the heated plastic determine the depth, consistency, and character of the final texture.
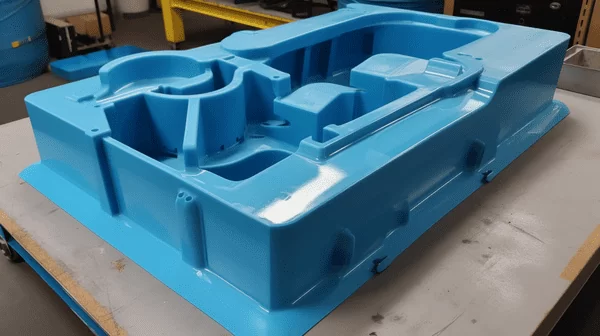
Crafting Texture through Techniques:
One technique that adds an artistic dimension to used in vacuum forming is sandblasting. This process involves projecting fine particles onto the mold’s surface, creating textures that range from subtle dimples to bold patterns. Sandblasting introduces an element of depth, enhancing the aesthetic appeal of the formed parts. This technique, combined with the synergy of design and material properties, creates a texture that resonates with the intended purpose and aesthetics.
Draft Angles and Draw Ratios:
The meticulous art of vacuum forming extends to draft angles and draw ratios. . Draft angle and angles are crucial to enable easy part removal from the mold. These slight angles facilitate a smooth demolding process, ensuring that the formed part doesn’t adhere to the mold or sustain damage. Draw ratio, on the other hand, is the measure of how much the plastic sheet is stretched over the mold. Balancing draw ratio with material properties is essential for achieving the desired texture without compromising structural integrity.
In the realm of vacuum forming, the mold reigns as both artist and architect. Its surface quality, design intricacies, and subtle angles converge to create textures that harmonize with form and function. As we navigate deeper into the landscape of texture selection, we uncover how these mold elements shape the aesthetics and tactile experience of vacuum-formed parts.
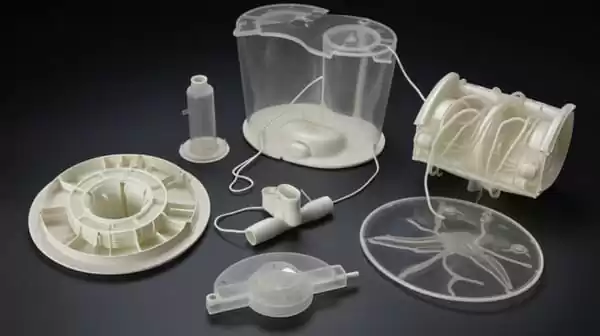
Balancing Aesthetics and Functionality:
In the intricate dance between form and function, texture emerges as a pivotal element that bridges the gap between aesthetics and practicality. Texture, often an understated aspect, holds the power to elevate both the visual allure and the functional prowess of vacuum-formed parts.
Role of Texture in Aesthetics and Functionality:
Texture plays a dual role, intertwining aesthetics with functionality. Consider an electronic casing – a smooth, sleek texture enhances its modern appeal while also facilitating easy cleaning. On the other hand, tools benefit from grip-enhancing textures that ensure secure handling and precision. The texture’s function aligns with its form, transforming it from a mere surface to an intrinsic part of the user experience.
Textures for Different Applications:
In the realm of vacuum forming, texture selection is a canvas that reflects the essence of the application. For electronic casings, a smooth and polished texture imparts a sense of sophistication. For tools and implements, a textured surface provides a tactile advantage, promoting confident usage even in challenging conditions. Food packaging might demand smooth textures for hygienic considerations, facilitating easy cleaning and compliance with stringent industry standards.
Enhancing Grip, Appeal, and Compliance:
Textures hold the potential to significantly enhance grip, especially in tools and handheld devices. Textured surfaces not only provide a secure hold but also contribute to safety by minimizing slippage. Beyond functionality, textures contribute to visual appeal. Intricate patterns and designs on vacuum-formed parts can elevate the overall aesthetics, making products stand out on shelves and displays.
Moreover, textures can bolster compliance with industry standards. Food packaging, for instance, often requires textures that align with hygiene regulations, ensuring easy cleaning and preventing the accumulation of residues. By thoughtfully selecting textures that cater to both functionality and industry standards, manufacturers can create products that resonate with end-users while adhering to guidelines.
In the tapestry of vacuum forming, texture emerges as a thread that weaves together form, function, and aesthetics. With a keen understanding of the role of texture, manufacturers can imbue vacuum-formed parts with tactile delight, visual intrigue, and a touch of practical magic. As we journey further into the intricate details of material properties and mold design, we uncover how these elements interact to culminate in textures that are not only visually striking but also functionally purposeful.
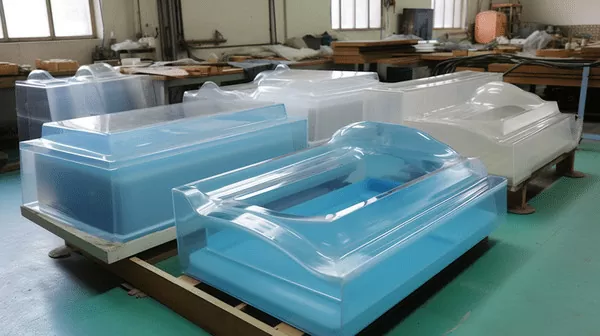
Material Properties and Heating:
In the realm of vacuum forming, the materials selected are the building blocks that shape the very essence of the final product. These materials possess distinct properties that intertwine with the vacuum forming process, creating a symphony of form, function, and texture.
Properties of Vacuum Forming Materials:
The materials utilized in vacuum forming are chosen with precision, each boasting specific properties that lend themselves to the process. High impact resistance is a hallmark of materials like acrylonitrile butadiene styrene (ABS), ensuring the formed parts can withstand external forces. Polycarbonate, another popular choice, offers remarkable optical clarity and durability. These material properties define the physical characteristics of the finished part and determine how it responds during the forming process.
Importance of Correct Heating Temperature:
As materials enter the realm of vacuum forming, the spotlight turns to the art of heating. The correct heating temperature is paramount; it dictates the transition from a rigid sheet to a malleable substance ready to take on the mold’s shape. Heating elements, including specialized heaters and molds crafted from cast aluminum, work in tandem to ensure that the material reaches the appropriate temperature uniformly. Achieving this balance guarantees the plastic sheet’s pliability, a state where it can seamlessly adopt the desired form without distortion.
Heating Techniques:
Heating is an intricate choreography, conducted to perfection by a range of techniques. Specialized heaters evenly distribute heat across the plastic sheet, avoiding inconsistencies that might result in uneven forming. The utilization of cast aluminum molds as heating elements efficiently transfers heat to the plastic sheet, preparing it for the intricate dance of vacuum forming. These techniques underscore the precision required to harness the material’s potential and create a canvas upon which textures and forms can flourish.
The convergence of material properties and heating techniques sets the stage for the artistry of vacuum forming. Materials, carefully chosen for their attributes, marry with the right temperature to transform into pliable canvases awaiting the touch of the mold. The subsequent symphony of vacuum forming brings forth textures that reflect both the material’s inherent qualities and the designer’s vision, uniting form, function, and aesthetic allure. As we delve deeper into the technical intricacies of mold creation and the balance between heating and cooling, we uncover how these elements synergize to birth textures that mesmerize and captivate.
Cooling and Quality:
As the curtains draw on the forming phase of vacuum forming, cooling takes center stage, poised to preserve the shape, texture, and integrity of the newly formed part. Cooling, often an unsung hero, holds the power to elevate quality, prevent defects, and ensure that the artistry of vacuum forming endures.
Significance of Proper Cooling:
Proper cooling is the final brushstroke that crystallizes the artistry of vacuum forming. Rapid cooling is essential to solidify the plastic sheet, ensuring that it maintains the shape and texture projected by the mold. Insufficient cooling time can lead to deformations, surface imperfections, and a lack of structural stability. Inadequate cooling jeopardizes the overall quality of the formed parts, rendering them unfit for their intended applications.
Defects and Insufficient Cooling:
The consequences of insufficient cooling are a tapestry of defects that tarnish the final product. Warping, where the part deviates from its intended form, can occur when the material doesn’t have enough time to solidify evenly. Uneven cooling can result in stress marks, where different sections of the formed part solidify at varying rates. These defects not only compromise aesthetics but also affect the part’s structural integrity, rendering it less durable and reliable.
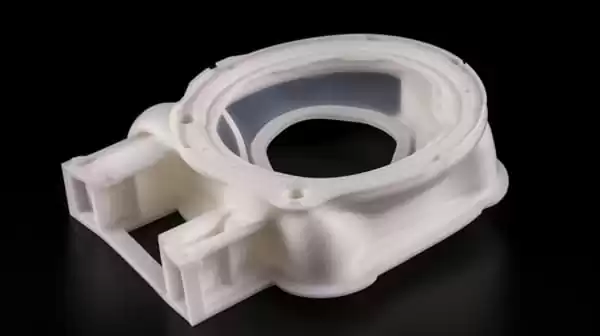
Role of Cooling Channels within Molds:
Cooling channels within molds are silent architects, directing a steady flow of cooling agents to the heart of the process. These channels ensure that the cooling process is consistent and efficient. By carefully controlling the temperature, these channels reduce cooling time and minimize the risks of defects. The cooling channels work in concert with the heating elements, creating a harmonious dance that balances temperature to perfection.
In the grand tapestry of vacuum forming, cooling is the grand finale, the phase that solidifies the artistry of the process into tangible form. It’s a reminder that every step, from material selection to mold design, must culminate in a process that preserves the texture, shape, and structural integrity. As we delve further into the journey, we uncover the intricate interplay between heating and cooling, two elemental forces that breathe life into vacuum-formed parts, creating textures that mesmerize the eye and enchant the touch.
Balancing Heating and Cooling: Key to Quality:
In the intricate ballet of vacuum forming, the delicate equilibrium between heating and cooling emerges as the linchpin to crafting high-quality vacuum-formed parts. This symphony of temperature, spanning from molten plastic to solidified form, is orchestrated with precision to create textures that captivate and forms that endure.
Achieving High-Quality Vacuum-Formed Parts:
The pursuit of high-quality vacuum-formed parts is an endeavor that hinges on a harmonious partnership between heating and cooling. A balanced heating process, where the plastic sheet reaches the optimal malleability, sets the stage for the subsequent forming. But it’s the meticulous cooling that seals the fate of the formed part, ensuring that it retains its shape, texture, and structural integrity.
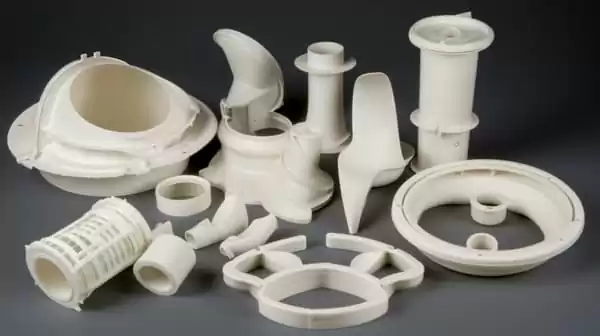
Interplay Between Heating and Cooling Stages:
The interplay between heating and cooling stages is a dance that demands choreography. The heating phase elevates the plastic sheet to a state of pliability, ready to embrace the mold’s contours. It’s a bridge between the rigid and the malleable, a transformation that relies on precision temperature control and heating techniques like heaters and cast aluminum molds.
However, the dance isn’t complete without cooling. Cooling solidifies the plastic sheet’s transformation, locking in the texture and structure projected by the mold. This balance is intricate – cooling too quickly risks deformations, while cooling too slowly prolongs the process and can lead to defects. Cooling channels within molds act as conductors, directing a calculated flow of cooling agents to ensure even and controlled cooling.
The rhythm between heating and cooling stages dictates the success of vacuum forming. It’s a synergy that transforms materials into textures, flat sheets into intricate forms, and concepts into tangible reality. The artistry of vacuum forming thrives in this balance, where temperature, time, and technique coalesce to birth parts that carry the fingerprints of craftsmanship and the allure of textures. As we delve deeper into the nuances of materials, molds, and textures, we unravel the exquisite tapestry woven by the partnership of heating and cooling – a partnership that defines the essence of vacuum-formed excellence.
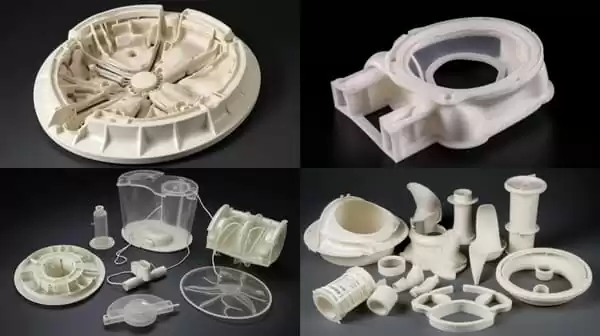
Conclusion:
The journey through the art and science of vacuum forming has unveiled a tapestry of intricacies, where every element – from material properties to mold design, heating to cooling – converges to shape vacuum-formed parts that transcend mere functionality. In this symphony of creation, texture emerges as the silent protagonist, a thread that weaves together aesthetics and purpose into a harmonious whole.