Introduction:
Vacuum forming is a versatile manufacturing process used across numerous industries, such as food packaging and automotive. The process entails heating plastic sheets to a specific temperature before using vacuum pressure to shape it into desired forms. Temperature control is critical in maintaining proper flow and shaping of heated plastic sheet material, and here we explore key points of the vacuum forming process, address frequently asked temperature-related questions, and explore factors involved in selecting an ideal temperature setting for successful vacuum forming.
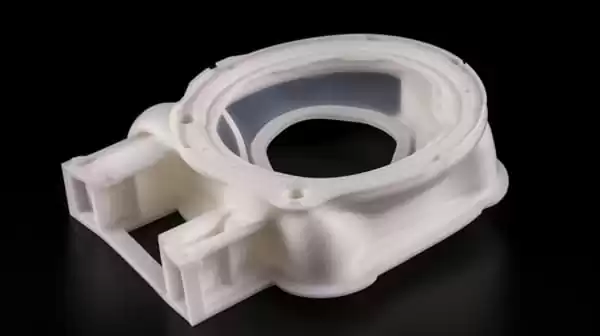
II. Factors Influencing Temperature Selection
A. Material Considerations
When determining the right temperature for vacuum forming, various material considerations come into play.
1.Different plastic materials and their temperature requirements:
Different types of plastic materials, such as polyvinyl chloride (PVC), acrylonitrile butadiene styrene (ABS), or polyethylene terephthalate (PET), have distinct temperature requirements for effective forming. Each material has its own melting point, flow characteristics, and heat sensitivity.
2.Consultation of material specifications for recommended temperature range:
It is essential to consult the material specifications provided by the manufacturer or supplier. These specifications often include a recommended temperature range that ensures proper material flow and prevents issues like underforming or overheating.
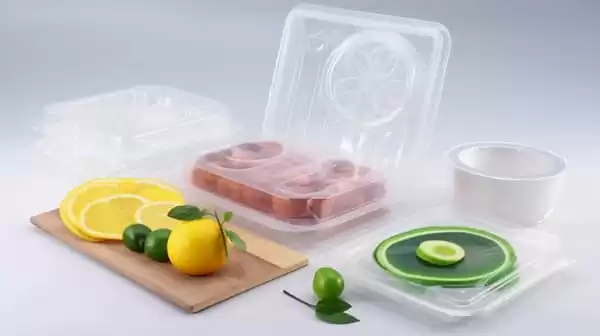
3.Impact of material properties on temperature selection:
Material properties, such as heat distortion temperature, flexibility, and chemical resistance, influence temperature selection. These properties can determine the optimal temperature range that allows for successful vacuum forming while maintaining the desired mechanical and visual characteristics of the final product.
B. Sheet Temperature and Heating Zones
The temperature of the plastic sheet and the heating zones within the vacuum forming machine are crucial factors in achieving accurate and consistent forming.
1.Importance of initial sheet temperature:
The initial temperature of the plastic sheet before it enters the forming process is significant. It affects the material’s flow and ability to conform to the mold. Preheating the sheet to the correct temperature ensures proper plasticity and reduces the risk of defects during forming.
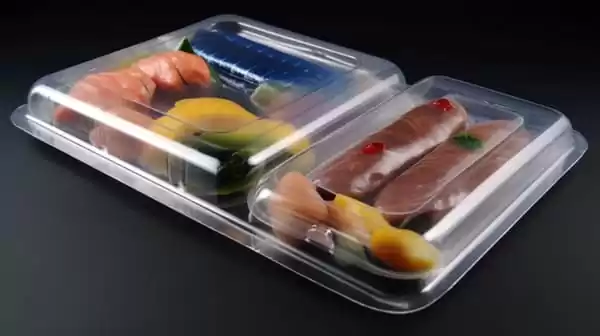
2.Heating zones in vacuum forming machines and uniform heating:
Vacuum forming machines are equipped with heating zones that distribute heat across the plastic sheet. These heating zones allow for uniform heating, which is vital to achieve consistent forming and prevent uneven material distribution.
3.Achieving consistent forming and proper thickness distribution:
Proper temperature control in the heating zones ensures consistent forming throughout the plastic sheet. Uniform heating helps maintain an even thickness distribution, resulting in high-quality formed parts that meet dimensional specifications.
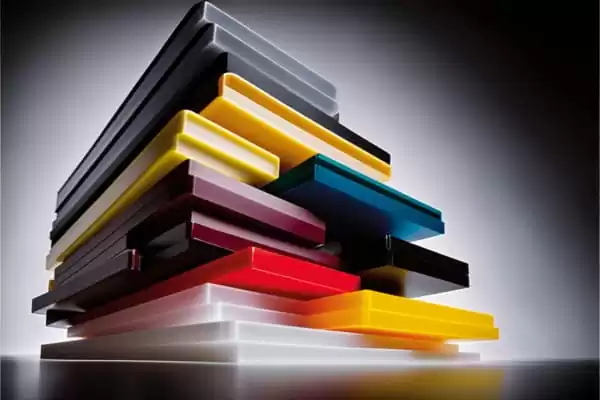
C. Mold Surface and Desired Shape
Temperature considerations extend to the mold surface and the desired shape of the formed part.
1.Controlling mold surface temperature:
The temperature of the mold surface affects the cooling and solidification of the plastic sheet during the forming process. Controlling the mold surface temperature prevents premature cooling, allowing the material to fully conform to the mold and retain its desired shape.
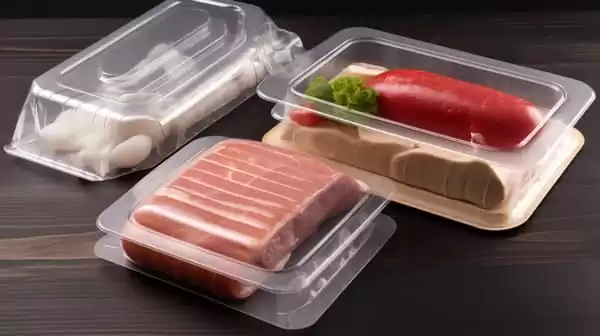
2.Temperature variations for complex shapes:
Complex-shaped parts may require temperature variations within the mold to ensure complete material flow and the desired level of detail. Adjusting the temperature in specific areas of the mold can help achieve optimal forming of intricate features and undercuts.
3.Consideration of draft angles and part thickness:
Draft angles and part thickness influence temperature selection. Parts with steep draft angles or varying thickness may require adjustments in the temperature to achieve uniform forming and avoid issues such as thinning or inadequate material distribution.
By considering material properties, sheet temperature, heating zones, and mold surface temperature in relation to the desired shape, manufacturers can make informed decisions about temperature selection in the vacuum forming process.
III. Determining the Right Temperature
A. Trial and Error Approach
Determining the appropriate temperature for vacuum forming often involves a trial and error approach. This method allows for fine-tuning the temperature to achieve the desired results.
1.Starting with the recommended temperature range:
Begin by setting the temperature within the recommended range provided by the material specifications. This initial temperature serves as a baseline for further adjustments.
2.Gradual adjustment and observation of results:
Make incremental adjustments to the temperature and observe how the plastic material responds during the forming process. Increase or decrease the temperature in small increments to gauge the impact on material flow, forming accuracy, and part quality.
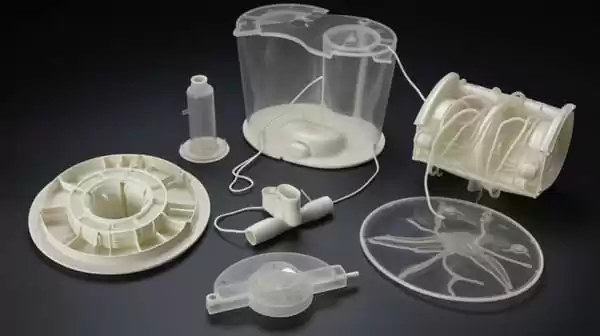
3.Conducting test runs to find the optimal temperature:
Perform a series of test runs at different temperature settings. Evaluate the formed parts for consistency, structural integrity, surface quality, and dimensional accuracy. Through these test runs, identify the temperature that produces the desired outcomes and meets the specific requirements of the vacuum-formed products.
B. Thermoforming Methods and Techniques
Temperature variations are influenced by different thermoforming methods and techniques employed in the vacuum forming process.
1.Temperature variations based on different methods:
Thermoforming methods such as pressure forming or twin sheet forming may require specific temperature adjustments. Pressure forming typically involves higher temperatures to achieve better material flow and mold definition. Twin plastic sheet temperature forming, on the other hand, involves heating two plastic sheets simultaneously at different temperatures to create a bond between them.
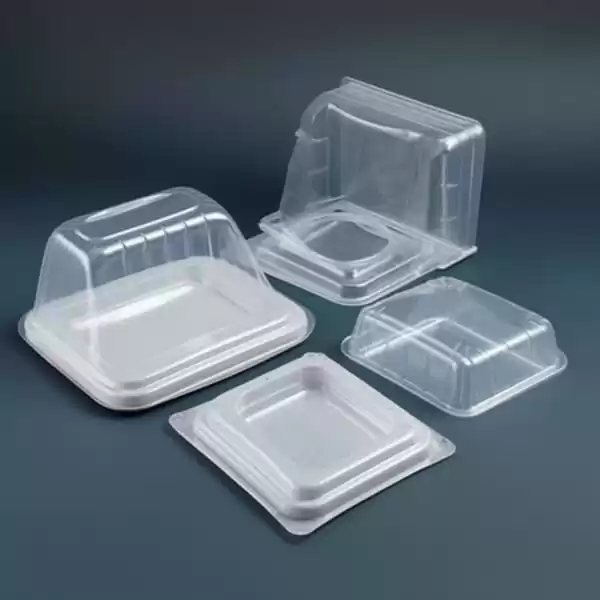
2.Consideration of specific technique requirements:
Each thermoforming technique has its own temperature requirements and guidelines. Consider the specific technique being used and follow the recommended temperature ranges and process guidelines provided for that particular method. Adhering to these guidelines ensures optimal results and avoids potential issues during the forming process.
By adopting a trial and error approach and considering the temperature requirements specific to different thermoforming methods, manufacturers can determine the right temperature for vacuum forming. This iterative process, combined with knowledge of the thermoforming techniques employed, allows for precise temperature control and the production of high-quality vacuum-formed products.
IV. Common Temperature-Related Questions
A. What is the temperature of a vacuum forming machine?
The temperature of a vacuum forming machine can vary depending on the specific machine and the plastic material being used. Typically, the temperature ranges from around 150 to 400 degrees Fahrenheit (65 to 200 degrees Celsius). However, it is important to consult the machine’s specifications and material guidelines to determine the appropriate temperature range for a specific application.
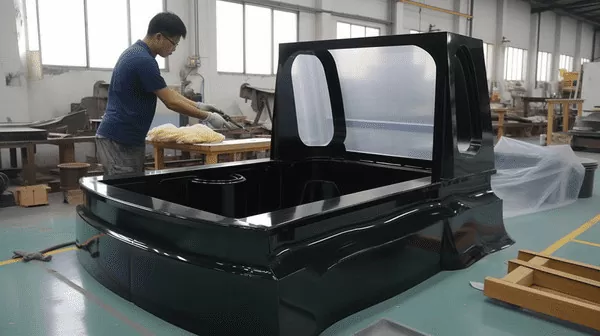
B. What temperature is needed for vacuum forming plastic?
The exact temperature thresholds needed for vacuum forming plastic depends on the specific plastic material being used. Different plastics have different melting points and flow characteristics. It is crucial to consult the material specifications or conduct trials to identify the recommended forming temperature range for each plastic type. Common plastic materials used in vacuum forming, such as polystyrene, ABS (acrylonitrile butadiene styrene), or PVC (polyvinyl chloride), typically have recommended temperature ranges between 320 and 400 degrees Fahrenheit (160 and 200 degrees Celsius).
C. What is the 10 10 5 rule in thermoforming?
The 10 10 5 rule is a general guideline used in thermoforming to estimate the cooling time required for a formed part. It suggests that for every 1/10 inch (2.5 mm) of material thickness, you should allow 10 seconds of cooling time for the part to fully solidify. This rule helps determine the overall cycle time for the vacuum forming process, including the time required for cooling and solidification.
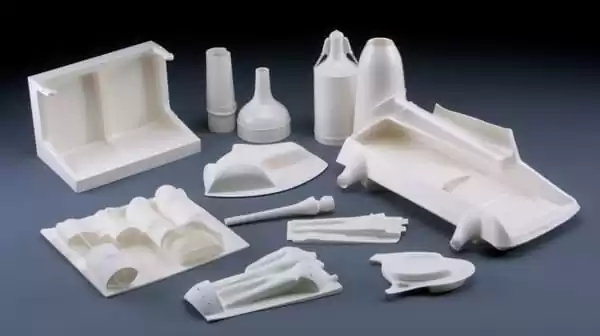
D. What temperature is needed for vacuum forming polystyrene?
Polystyrene is a common plastic material used in vacuum forming. The recommended forming temperature range for vacuum forming polystyrene typically an oven temperature that falls between 320 and 400 degrees Fahrenheit (160 and 200 degrees Celsius). However, it is essential to consult the specific material specifications provided by the manufacturer to ensure accurate temperature selection for the particular grade of polystyrene being used.
By addressing these common temperature-related questions, manufacturers can gain a better understanding of temperature requirements for vacuum forming and make informed decisions to achieve optimal results.
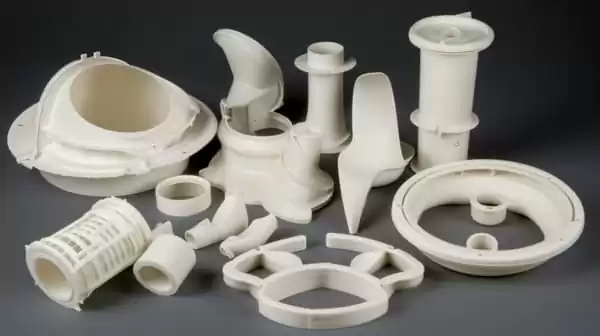
Conclusion:
In conclusion, selecting the appropriate temperature for the vacuum forming process is essential to ensure the production of high-quality vacuum-formed products that meet the desired shape and mechanical properties. By considering factors such as material selection, heating process, mold surface temperature, and conducting trial and error, manufacturers can determine the suitable temperature range for optimal results.
Factors such as material considerations, including different plastic materials and their temperature requirements, play a crucial role in temperature selection. Consulting material specifications for the recommended temperature range and considering the impact of material properties further aids in determining the right temperature.
Sheet temperature and heating zones in the vacuum forming machine are critical aspects. Starting with the recommended temperature range, making gradual adjustments, and conducting test runs help identify the optimal temperature for achieving consistent forming and proper thickness distribution.
Controlling the mold surface temperature is vital in preventing premature cooling and ensuring the inner surface of the plastic sheet conforms to the desired shape. Temperature variations for complex shapes and consideration of draft angles and part thickness contribute to achieving accurate and precise forming.
Additionally, addressing common temperature-related questions, such as the temperature of a vacuum forming machine and the temperature requirements for specific plastic materials like polystyrene, helps manufacturers make informed decisions during the vacuum forming process.
By fine-tuning the temperature within the recommended range, manufacturers can achieve precise temperature control, ensuring consistent quality, dimensional accuracy, and mechanical properties of the final vacuum-formed products.
In conclusion, determining the right temperature for vacuum forming involves considering various factors, conducting trial and error, and addressing specific material and process requirements. By doing so, manufacturers can achieve optimal results, meet industry standards, and produce high-quality vacuum-formed products.