Introduction
Vacuum forming is a widely used manufacturing process that involves shaping plastic sheets into desired forms. It is a versatile and cost-effective method employed in various industries, including packaging, automotive, and signage. One crucial factor that significantly influences the outcome of the vacuum forming process is the temperature at which the plastic sheet is heated. Determining the correct temperature is vital to ensure successful and high-quality vacuum-formed products.
The temperature at which the heated plastic sheet is heated directly affects its behavior during the forming process. Heating the plastic sheet to an optimal temperature range allows it to become soft and pliable, making it easier to shape and mold according to the desired design. However, excessive heat can cause overstretching, deformation, or even material degradation of mold surface, leading to poor-quality products. On the other hand, inadequate heating may result in incomplete molding or insufficient material flow, affecting the accuracy and integrity of the formed part.
Achieving the right temperature is a critical aspect of the vacuum forming process, as it directly impacts the final product’s quality, structural integrity, and dimensional accuracy. Proper oven temperature control ensures the plastic sheet reaches the ideal state for effective forming and minimizes the risk of defects or inconsistencies. Consequently, understanding how to determine the right temperature for vacuum forming is essential for manufacturers and designers striving to achieve optimal results and meet specific requirements for their products.
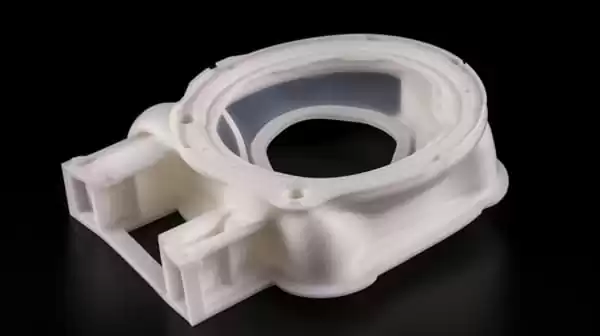
In the following sections, we will delve into various methods and considerations involved in determining the correct temperature for vacuum forming. By exploring these factors, manufacturers and practitioners can enhance their understanding of the vacuum forming process, improve their manufacturing capabilities, and ultimately deliver high-quality vacuum-formed products.
II. Understanding the Material and Temperature Range
Vacuum forming utilizes a wide range of plastic materials that possess unique characteristics suitable for different applications. Understanding these materials and their temperature requirements is crucial for achieving successful vacuum forming results. Here, we will explore the common plastic materials used in vacuum forming, the concept of heat distortion temperature, and the recommended temperature ranges for various plastic materials.
1.Different Plastic Materials for Vacuum Forming:
In vacuum forming, various thermoplastic materials are commonly employed due to their favorable properties for shaping and molding. Some commonly used plastic materials include:
Acrylonitrile Butadiene Styrene (ABS):
Known for its strength, impact resistance, and versatility, ABS is widely used in industries such as automotive, electronics, and consumer goods.
High Impact Polystyrene (HIPS):
HIPS offers excellent impact resistance and dimensional stability, making it suitable for applications like packaging, signage, and display items.
Polycarbonate:
Polycarbonate combines high strength, transparency, and heat resistance, making it ideal for applications requiring durability and optical clarity, such as protective covers, lenses, and automotive components.
Polypropylene (PP):
PP is lightweight, chemically resistant, and possesses good impact strength, making it suitable for packaging, automotive, and medical applications.
Polyvinyl Chloride (PVC):
PVC is known for its versatility, chemical resistance, and cost-effectiveness. It finds applications in areas such as signage, construction, and packaging.
2.Heat Distortion Temperature:
Heat distortion temperature refers to the temperature at which a plastic material begins to deform under load. It is a crucial factor in material selection for vacuum forming. Understanding the heat distortion temperature of different plastic materials helps ensure that the selected material can withstand the necessary forming temperatures without losing its structural integrity.
3.Recommended Temperature Ranges:
Each plastic material used in vacuum forming has a specific temperature range recommended by manufacturers. This range ensures that the material reaches the appropriate state for molding while avoiding excessive softening, degradation, or other undesirable effects. It is essential to consult the manufacturer’s guidelines or technical data sheets for the specific plastic material to determine the recommended temperature range.
For example, ABS typically requires a heating temperature range of 300°F (150°C) to 400°F (205°C), while HIPS may have a recommended range of 320°F (160°C) to 380°F (193°C). Polycarbonate, PP, and PVC may have their respective temperature ranges that need to be considered based on the specific grade and application requirements. Understanding the properties and temperature requirements of different plastic materials empowers manufacturers and designers to make informed decisions during the material selection process for vacuum forming. By adhering to the recommended temperature ranges, they can ensure successful forming, minimize material defects, and produce high-quality vacuum-formed products.
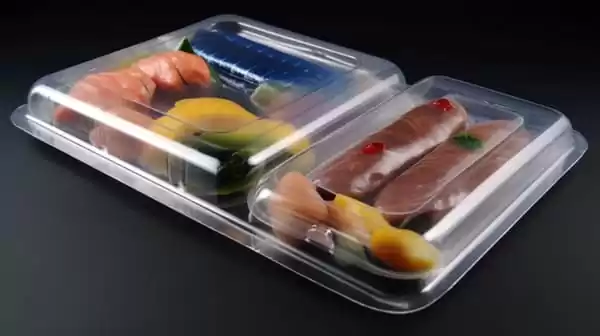
III. Methods to Determine the Right Temperature range
A. Consult Manufacturer Guidelines
When determining the right temperature for vacuum forming, one of the first steps is to refer to the guidelines provided by the manufacturer of the specific plastic material being used. Manufacturer guidelines offer valuable insights into the recommended temperature ranges and heating parameters for optimal vacuum forming results. By following these guidelines, manufacturers can ensure that the plastic material is heated within the specified temperature range, minimizing the risk of damage or inconsistencies during the under pressure forming process.
B. Conduct Material Testing
Material testing is an effective method to determine the suitable temperature for vacuum forming. It involves heating small sample sheets of the plastic material within a range of temperatures that are believed to be appropriate. By observing the behavior of the plastic sheets at different temperatures, manufacturers can assess the material’s response and identify any signs of softening, warping, or inadequate molding. Material testing allows for adjustments and fine-tuning of the temperature to achieve the desired forming characteristics and avoid potential issues during production.
C. Thermoforming Process Window
The thermoforming process window refers to the optimal temperature range within which a particular plastic material can be heated and formed without compromising its structural integrity. To determine this temperature window, manufacturers can perform trial and error experiments. Starting with a lower temperature within the recommended operational temperature range, they gradually increase the temperature while monitoring the behavior of the plastic material. The objective is to identify the exact temperature thresholds at which the plastic becomes pliable enough for effective forming without excessive stretching, deformation, or material degradation.
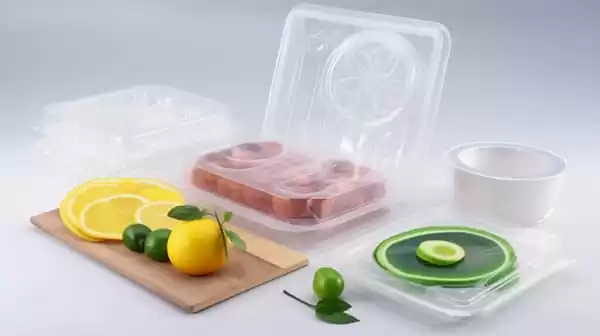
D. Heatig Zones and Sheet Temperature
In vacuum forming ovens, heating zones are utilized to ensure uniform heating of the plastic sheet. It is essential to maintain the correct sheet temperature throughout the forming process to achieve consistent results. By properly setting and controlling the temperature in each heating zone, manufacturers can ensure that the entire sheet receives uniform heat distribution. Monitoring the sheet temperature using appropriate sensors enables precise temperature control, contributing to accurate and reliable vacuum-formed products.
Temperature control throughout the vacuum forming process is crucial for achieving optimal results. By utilizing manufacturer guidelines, conducting material testing, determining the thermoforming process window, and maintaining accurate sheet temperature through heating zones, manufacturers can enhance their control over the forming process. This ensures that the plastic material is heated to the correct temperature, leading to successful vacuum forming with minimal defects and consistent quality in the final products.
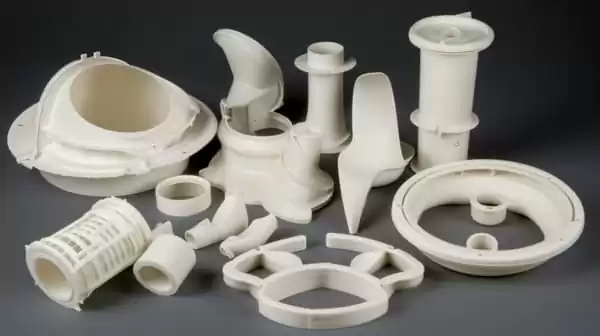
IV. Specific Considerations and Examples
A. Plastic Materials and Their Temperature Requirements
When determining the right temperature for vacuum forming, it is essential to consider the specific plastic material being used. Different plastic materials have distinct temperature requirements due to variations in their properties and composition. Here are some commonly used plastic materials in vacuum forming and their recommended temperature ranges:
Acrylonitrile Butadiene Styrene (ABS):
ABS is known for its strength, impact resistance, and versatility.
The recommended temperature range for ABS vacuum forming typically falls between 300°F (150°C) and 400°F (205°C).
High Impact Polystyrene (HIPS):
HIPS offers excellent impact resistance and dimensional stability.
The recommended temperature range for HIPS thermoforming usually ranges from 320°F (160°C) to 380°F (193°C).
Polycarbonate:
Polycarbonate combines high strength, transparency, and heat resistance.
The recommended temperature range for polycarbonate vacuum forming commonly ranges from 290°F (143°C) to 330°F (166°C).
Polypropylene (PP):
PP is lightweight, chemically resistant, and possesses good impact strength.
The recommended temperature range for PP vacuum forming typically ranges from 275°F (135°C) to 350°F (177°C).
Polyvinyl Chloride (PVC):
PVC is known for its versatility, chemical resistance, and cost-effectiveness.
The recommended temperature range for PVC vacuum forming often falls between 300°F (150°C) and 375°F (190°C).
B. Temperature Considerations for HIPS Thermoforming
High Impact Polystyrene (HIPS) is a commonly used plastic material in vacuum forming. When thermoforming HIPS, it is crucial to consider the recommended temperature range. Typically, the temperature range for HIPS thermoforming ranges from 320°F (160°C) to 380°F (193°C). However, it is essential to consult the manufacturer’s guidelines or conduct material testing to determine the optimal temperature within this range, as it may vary depending on the specific grade of HIPS and the desired forming characteristics.
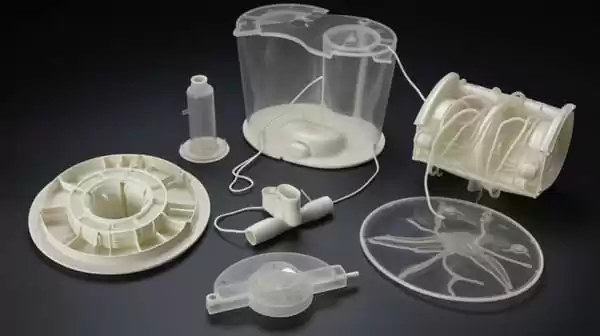
By considering the specific plastic material being used and its recommended temperature range, manufacturers can ensure that the heating process aligns with the material’s properties. This leads to successful vacuum forming, allowing for accurate and consistent shaping of the plastic sheets into the desired products.
Conclusion
In conclusion, determining the right temperature is a critical aspect of the vacuum forming process, as it directly affects the quality and success of the formed products. Here, we recap the key points in determining the right temperature for vacuum forming and emphasize the importance of temperature control for producing high-quality vacuum-formed products.
By understanding the specific plastic material being used and its recommended temperature range, manufacturers can make informed decisions during the compressed air process. Considering factors such as the heat distortion temperature and consulting manufacturer guidelines play a vital role in selecting the appropriate material and determining the optimal temperature range for successful vacuum forming.
Methods such as material testing and identifying the thermoforming process window help manufacturers fine-tune the temperature to achieve the desired forming characteristics. Conducting material testing allows for observation of the plastic sheet’s behavior at different temperatures, ensuring proper softening, minimizing deformation, and avoiding inadequate molding. Additionally, the thermoforming process window defines the optimal temperature range that maintains the plastic’s structural integrity without compromising the formed product’s quality.
Maintaining temperature control throughout the vacuum forming process is essential. Properly setting and controlling the heating zones in the vacuum forming oven ensure uniform heating of the plastic sheet, contributing to consistent results. Monitoring the sheet temperature using appropriate sensors enables precise temperature control, resulting in accurate and reliable vacuum-formed products.
To achieve optimal results, we encourage readers to consider material selection based on specific requirements, consult manufacturer guidelines for recommended temperature ranges, and conduct material testing to fine-tune the temperature for their specific applications. By following these practices and maintaining temperature control, manufacturers can produce high-quality vacuum-formed products with high accuracy of the desired shape, dimensional accuracy, and mechanical properties.
In summary, understanding and determining the right temperature for vacuum forming is crucial for successful manufacturing. By prioritizing temperature control, manufacturers can optimize the vacuum forming process, ensuring the production of high-quality, precisely formed products.