Introduction:
Vacuum forming is a versatile manufacturing process that is widely used to create plastic products of various shapes and sizes. It involves heating a plastic sheet until it becomes pliable, then placing it over a mold and using a vacuum to draw the sheet tightly against the mold’s contours. This process allows for the creation of complex and detailed plastic parts with relative ease and cost-efficiency.
One critical aspect of achieving successful vacuum forming results is determining the right draw depth. Draw depth refers to the vertical distance that the plastic sheet is drawn into the mold during the forming process. It plays a crucial role in ensuring uniform material distribution and preventing defects such as thinning or stretching.
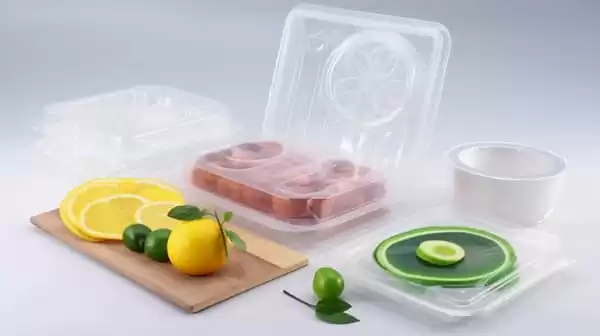
Determining the appropriate draw depth is of utmost importance for several reasons. Firstly, it directly affects the overall quality and structural integrity of the formed plastic part itself. If the draw depth is too shallow, the plastic may not fully cover the mold, resulting in incomplete or unevenly formed finished parts. On the other hand, if the draw depth is too deep, the plastic may stretch excessively or thin out, leading to weak spots or even tears in the final product.
Moreover, the draw depth influences the thickness of the plastic in different areas of the formed part. By adjusting the draw depth, manufacturers can control the wall thickness and ensure it meets the desired specifications. This is particularly crucial when producing parts that require specific mechanical properties or structural strength.
Additionally, determining the right draw depth is vital for optimizing material usage and minimizing waste. By accurately calculating the required draw depth, manufacturers can reduce excess material and trim costs, making the vacuum forming process more efficient and cost-effective.
In conclusion, understanding and determining the right draw depth in vacuum forming is crucial for achieving high-quality, structurally sound, and cost-efficient plastic parts. By carefully considering the draw depth in relation to mold design, material properties, and desired specifications, manufacturers can ensure optimal material distribution, minimize defects, and produce parts that meet the intended requirements.
II. Understanding Draw Depth
A. Definition and Significance of Draw Depth in Vacuum Forming:
Draw depth, in the context of vacuum forming, refers to the vertical distance that a plastic sheet minimum starting gauge is drawn into a mold during the forming process. It is a critical parameter that directly influences the outcome and quality of the formed part. The draw depth determines how much the plastic sheet is stretched and deformed to conform to the mold’s shape.
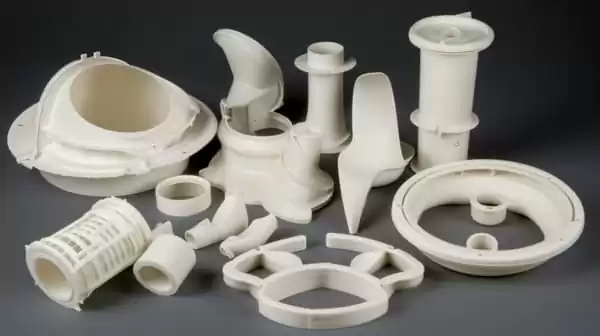
B. Explanation of its Impact on Material Distribution and Defects:
The draw depth plays a significant role in achieving uniform material distribution throughout the formed part. When the plastic sheet is drawn into the mold, it stretches and thins out to cover the mold’s contours. The draw depth directly affects the degree of stretching and thinning, which can impact the material’s thickness and distribution.
If the draw depth is insufficient, the plastic may not fully reach all areas of the mold, resulting in incomplete coverage and uneven material distribution. This can lead to weak spots or thin areas in the formed part, compromising its structural integrity and functionality.
On the other hand, if the draw depth is excessive, the plastic sheet can overstretch and become too thin in certain areas. This can cause issues such as thin spots, tears, or even ruptures, rendering the part unusable. Excessive stretching can also distort the shape or dimensions of the formed part, deviating from the intended design.
Balancing the draw depth is crucial for minimizing defects and achieving consistent quality. By carefully determining the appropriate draw depth, manufacturers can ensure that the plastic sheet adequately covers the mold’s features and maintains a consistent thickness throughout the formed part. This results in a structurally sound and visually appealing product.
In addition to material distribution, the draw depth also impacts other aspects of the forming process. It influences factors like cycle time, cooling requirements, and the ease of part removal from the injection molding itself. Therefore, understanding and controlling the draw depth are essential for achieving the desired outcomes in vacuum forming.
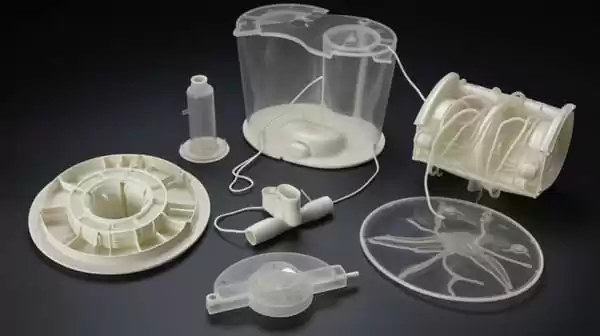
By considering factors such as material thickness, mold design, and the specific properties of the plastic being used, manufacturers can determine the optimal draw depth for each specific application. This attention to detail ensures proper material distribution, minimizes defects, and ultimately produces high-quality plastic parts.
III. Factors Influencing Draw Depth
A. Material Thickness
Importance of Material Thickness in Determining Draw Depth: The thickness of the plastic sheet used in vacuum forming is a crucial factor in determining the appropriate draw depth. Material thickness directly affects the amount of stretching and deformation that the plastic can undergo without compromising its integrity. Choosing plastic sheets with the right material thickness is essential for achieving uniform material distribution and avoiding defects such as thinning or tearing.
Guidelines for Selecting Appropriate Thickness:
When selecting the material thickness for vacuum forming, several factors should be considered:
Size and complexity of the formed part:
Larger or more intricate parts may require thicker material to ensure sufficient coverage and structural integrity.
Desired strength and rigidity:
Parts that need to withstand mechanical stresses or load-bearing applications may require thicker material for added strength.
Aesthetic requirements:
Thicker materials can provide a more substantial and high-quality appearance.
Material flexibility: Thinner materials are more flexible and can conform to complex shapes more easily.
B. Mold Design and Complexity
Role of Mold Design in Determining Draw Depth: The design of the mold used in vacuum forming has a significant impact on the required draw depth. Mold draft angles design influences the shape, contours, and features of the formed part. The complexity of the mold determines how deeply the plastic needs to be drawn to accurately reproduce the mold’s details.
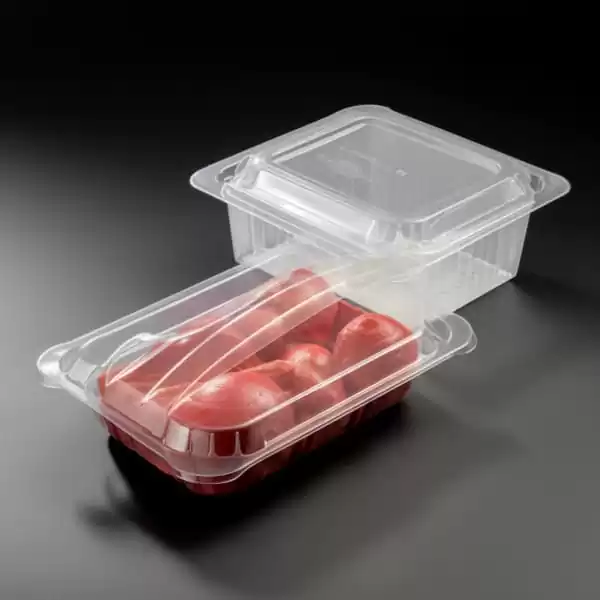
Considerations for Complex or Simple Molds:
Complex molds with intricate features, sharp corners, or deep undercuts may require a larger draw depth to ensure proper material coverage and prevent thinning or tearing.
Simple molds with fewer features may allow for a shallower draw ratio depth while still achieving the desired part characteristics.
C. Material Properties
Understanding How Material Properties Affect Draw Depth: Different plastic materials have unique properties that influence their behavior during vacuum forming. Some materials are more stretchable, while others are more rigid or prone to thinning. Understanding the specific properties of the plastic being used is crucial in determining the ideal draw depth.
Selection of the Right Material for Vacuum Forming:
When choosing a material for vacuum forming, considerations should include:
Mechanical properties: The material should possess the required strength, flexibility, or rigidity for the intended application.
Thermoforming characteristics: Some materials are better suited for vacuum forming due to their ability to stretch and conform to molds while maintaining uniform thickness.
Special requirements: Certain applications may require specific properties like flame retardancy or chemical resistance.
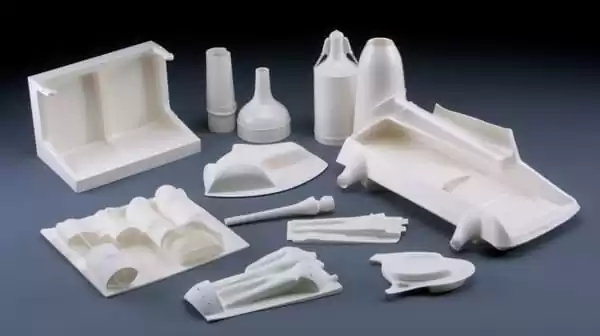
By carefully considering material thickness, mold design, and material properties, manufacturers can determine the optimal draw depth for vacuum forming. This ensures proper material distribution, minimizes defects, and produces high-quality plastic parts.
IV. Determining the Optimal Draw Depth
A. Trial and Error Approach
1.Starting with a Conservative Draw Depth:
When determining the draw depth for vacuum forming, a trial and error approach can be effective. Start with a conservative draw depth in the initial forming attempts. This means using a shallower draw depth than what might be initially estimated as necessary. By starting conservatively, you can observe the behavior of the plastic sheet, the material distribution, and any potential defects that may occur.
2.Gradual Adjustments Based on Test Results:
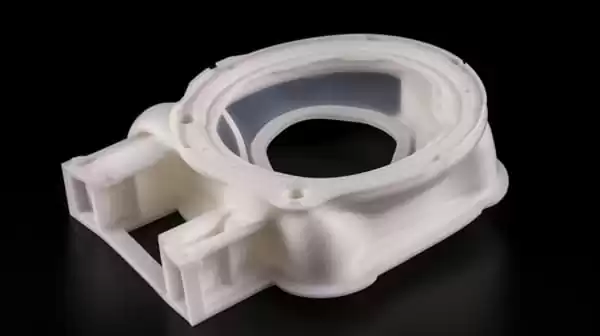
After the initial forming attempts, carefully examine the formed parts for any issues such as thinning, stretching, or incomplete coverage. Analyze the test results and make gradual adjustments to the draw depth. If thinning occurs in specific areas, increasing the draw depth might be necessary. Conversely, if parts appear over-stretched, reducing the draw depth might be appropriate. Continue iterating and adjusting the draw depth until the desired results are achieved.
B. Expert Consultation
1.Importance of Seeking Advice from Experienced Professionals:
Consulting with experienced professionals in vacuum forming can be invaluable in determining the optimal draw depth. Seasoned experts have extensive knowledge about different materials, molds, and vacuum forming techniques. Their expertise allows them to provide valuable insights, guiding you in making informed decisions throughout the process.
1.Benefits of Expert Guidance in Determining Draw Depth:
Experts can help you avoid common pitfalls and challenges associated with vacuum forming. They can offer recommendations on the most suitable material for your specific application, suggest mold design improvements, and help fine-tune the draw depth for the best possible results. By leveraging their knowledge, you can save time, reduce waste, and ensure a smoother and more successful vacuum forming process.
In summary, determining the optimal draw depth in vacuum forming requires a combination of trial and error as well as seeking expert guidance. Starting with a conservative draw depth and making gradual adjustments based on test results helps refine the process and achieve the desired outcomes. Additionally, consulting with experienced professionals can provide valuable insights and recommendations, enhancing the efficiency and effectiveness of the vacuum forming process. By combining these approaches, manufacturers can achieve high-quality plastic parts that meet their specific requirements and applications.
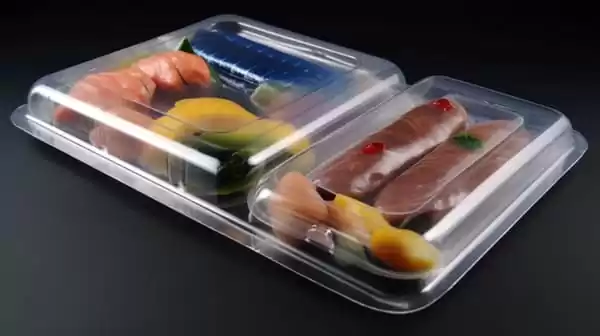
Conclusion
In conclusion, determining the right draw depth is a crucial aspect of achieving successful vacuum forming results. Throughout this article, we have explored the key considerations and factors that influence the determination of draw depth in vacuum forming. Let’s recap the key points discussed:
Draw depth refers to the vertical distance that a plastic sheet is drawn into a mold during the vacuum forming process.
Determining the appropriate minimum thickness and draw depth is essential for achieving uniform material distribution and avoiding defects such as thinning or stretching.
Factors such as material thickness, mold design and complexity, and material properties play a significant role in determining the optimal draw depth.
Material thickness directly affects the strength, distribution, and aesthetics of the formed part.
Mold design influences the depth required to accurately reproduce the mold’s features and contours.
Material properties impact the behavior of the plastic during vacuum forming and should be considered for selecting the right material.
Emphasizing the importance of determining the right draw depth is crucial for successful vacuum forming. It directly impacts the quality, structural integrity, and aesthetics of the formed parts. A well-calculated draw depth ensures uniform material distribution, minimizing defects and ensuring consistent results.
It is important to consider the outlined factors, such as material thickness, mold design, and material properties, when determining the draw depth. Manufacturers are encouraged to carefully analyze these factors and conduct trials to find the optimal draw depth for their specific applications.
Furthermore, seeking expert guidance and consultation is highly recommended. Experienced professionals in vacuum forming can provide valuable insights and expertise, helping manufacturers make informed decisions and achieve optimal results.
In conclusion, determining the right draw depth is a critical step in the vacuum forming process. By considering the outlined factors and seeking expert guidance, manufacturers can ensure optimal material distribution, minimize defects, and produce high-quality plastic parts that meet their intended requirements.