Introduction
Vacuum forming is a widely used manufacturing process in which a heated sheet of thermoplastic material is stretched over a mold and then drawn tightly onto the mold’s surface using a vacuum. As the plastic cools and solidifies, it takes on the shape of the mold, resulting in the formation of three-dimensional plastic parts. Vacuum forming is known for its versatility and cost-effectiveness, making it a popular choice for producing plastic parts with various applications.
Undercuts in vacuum-formed parts refer to recesses or protrusions on the part’s surface that complicate the demolding process. During vacuum forming, the plastic sheet needs to be tightly drawn over the mold to achieve an accurate representation of the mold’s shape. However, undercuts hinder the smooth removal of the part from the mold, potentially causing damage to the part or the mold itself. Properly incorporating undercuts can significantly enhance the aesthetics and functionality of the final product, but it also poses challenges during demolding.
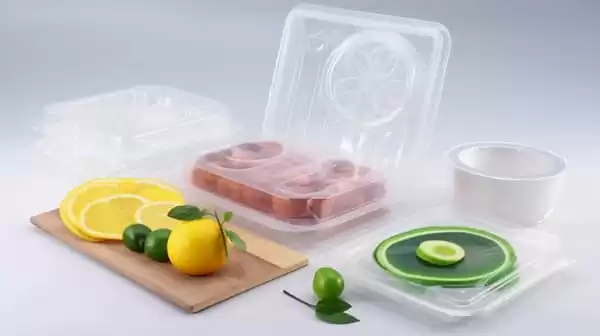
The purpose of this article is to explore techniques for creating undercuts successfully in vacuum-formed parts. It will provide valuable insights into the design considerations, mold construction, and secondary operations required to handle undercuts effectively. By discussing various methods and considerations, the article aims to help manufacturers and designers overcome the challenges of incorporating undercuts in vacuum-formed parts and achieve visually appealing and functional outcomes.
I. Understanding Undercuts in Vacuum Forming process
Definition of Undercuts in Vacuum Forming:
In the context of vacuum forming, undercuts refer to features on the surface of the formed part that create recesses or protrusions that hinder the smooth removal of the part from the mold during the demolding process. These features prevent the part from being released easily, leading to challenges during part production and potentially causing damage to the part or mold.
Challenges Caused by Undercuts during Demolding and Part Production:
Undercuts can pose several difficulties during the demolding process in vacuum forming. When the vacuum is applied to draw the heated plastic sheet tightly onto the mold, undercuts may get caught, causing the part to snag or become trapped. This can result in deformation of the part, distortion of the mold, or even breakage. In extreme cases, undercuts can render the formed part unusable, leading to production delays and increased costs.
Additionally, undercuts can affect the overall quality of the part. Improperly designed undercuts may lead to excessive thinning of the plastic in certain areas, resulting in weakened structural integrity. Sharp angles and deep recesses may be challenging to form accurately, affecting the part’s aesthetics and functionality.
Importance of Proper Design Considerations for Undercuts:
Incorporating undercuts effectively in vacuum-formed parts requires careful design considerations. Designers need to evaluate the mold geometry, material properties, and part dimensions to ensure that the undercuts can be successfully demolded without compromising the part’s quality. Proper draft angles should be incorporated into the mold design to allow for smooth release during demolding. Additionally, selecting the right thermoplastic material with appropriate flexibility and elongation properties is crucial for the successful formation of undercuts.
By paying attention to these design considerations and understanding the challenges posed by undercuts, manufacturers can create vacuum-formed parts with intricate and visually appealing designs while ensuring efficient and problem-free production processes.
II. Designing for Undercuts in Vacuum Forming
Design Process for Creating Undercuts in Vacuum-Formed Parts:
The design process for incorporating undercuts in vacuum-formed parts requires careful planning and consideration. Designers need to visualize the final part’s shape and identify areas where undercuts can enhance the part’s aesthetics or functionality. Once the desired undercut features are determined, the mold design is crucial in achieving successful vacuum forming. The mold must be precisely machined to accommodate the undercuts and allow for smooth demolding without causing damage to the part or the mold.
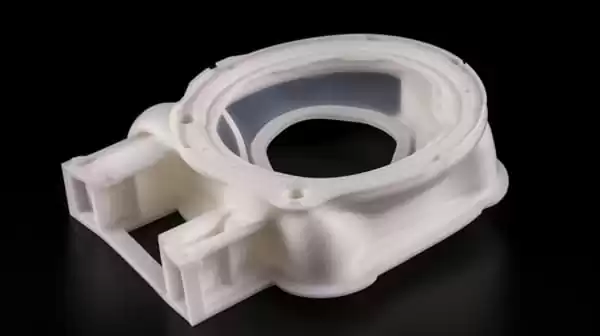
Use of Draft Angles to Facilitate Easy Demolding:
Draft angles play a significant role in vacuum forming to facilitate the easy demolding of the part and minimize undercut-related issues. Draft angles are slight tapers or angles incorporated into the mold’s design. These angles allow the formed part to release smoothly from the mold by reducing the contact area between the part and the mold surface. Proper draft angles ensure that the part does not get caught on the mold’s edges or features, avoiding deformation and part damage during the demolding process.
Role of Material Thickness and Sharp Angles in the Design Process:
Material thickness is a critical consideration when designing for undercuts in vacuum forming. The thickness of the thermoplastic sheet affects the part’s flexibility and the forming process. Thicker materials may require longer heating times to become pliable, while thinner materials may cool more rapidly, affecting the forming accuracy and the ease of demolding.
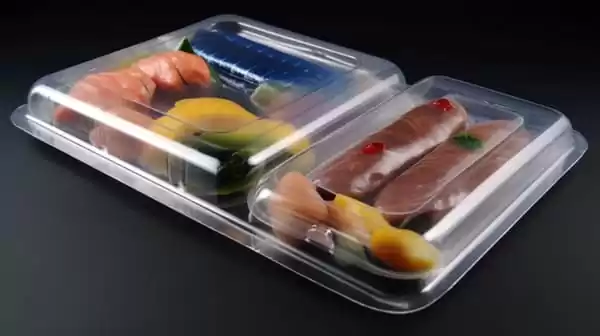
Sharp angles in the part design can also pose challenges during vacuum forming, especially when dealing with undercuts. Sharp angles may lead to stress concentrations in the material, potentially causing thinning or distortion during the forming process. Designers need to consider using smoother curves and rounded features to reduce the stress on the material and improve the part’s overall structural integrity.
In conclusion, designing for undercuts in vacuum-formed parts involves meticulous planning, mold design, and consideration of draft angles, material thickness, and the use of smoother features. By implementing proper design practices, manufacturers can successfully incorporate undercuts in vacuum-formed parts, achieving visually appealing and functionally superior products while ensuring efficient demolding and part production processes.
III. Techniques for Creating Undercuts
Use of Sliding Molds for Handling Undercuts:
Sliding molds are an effective and commonly used method to handle undercuts in vacuum forming. Sliding molds consist of two or more mold sections, where one portion can slide or rotate to release the undercut feature. During the vacuum forming process, as the plastic sheet conforms to the mold’s contours, the sliding portion moves away, allowing the formed part to be easily released without getting caught on the undercut. Sliding molds are particularly useful for complex undercuts and parts with multiple features, enabling smooth and efficient demolding while maintaining the integrity of the formed part.
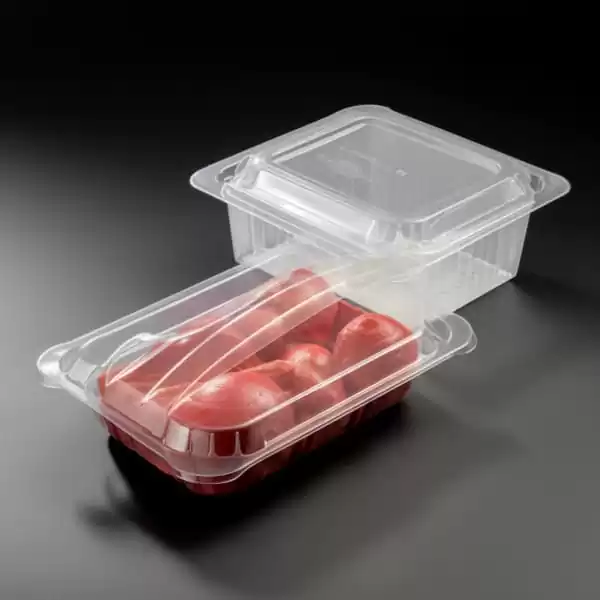
Tapered Undercuts for Smoother Demolding:
Tapered undercuts are another technique used in vacuum forming to aid in smoother demolding. By designing the undercut with a tapered angle, the formed part can release more easily during demolding. The taper allows the plastic to gradually disengage from the undercut feature, reducing the risk of snags or resistance. Tapered undercuts are especially beneficial for parts with deep or intricate undercut features, as they minimize stress on the material and ensure a more uniform demolding process.
Importance of Selecting Flexible Thermoplastic Materials:
Choosing the right thermoplastic material is crucial when incorporating undercuts in vacuum-formed parts. Flexible thermoplastic materials with higher elongation properties are better suited for forming undercuts. These materials can stretch and adapt to the mold’s contours, effectively accommodating the undercut features without significant deformation or distortion. Materials with higher flexibility also provide better resilience during the demolding process, reducing the likelihood of part damage or sticking.
Additionally, the selection of a flexible thermoplastic material enhances the part’s overall durability, making it more resistant to impact and potential stresses that may occur during handling or use. Furthermore, certain flexible thermoplastics offer chemical resistance, UV stability, and other desirable properties, making them well-suited for specific applications where undercuts are necessary.
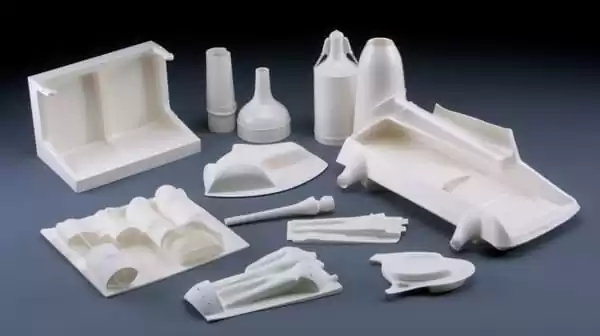
In conclusion, utilizing sliding molds, incorporating tapered undercuts, and selecting flexible thermoplastic materials are valuable techniques for successfully creating undercuts in vacuum-formed parts. These approaches enhance the ease of demolding, improve the quality of the formed parts, and broaden the range of design possibilities. By employing these techniques, manufacturers can achieve intricate and visually appealing vacuum-formed parts with undercuts, meeting the demands of various applications and industries.
IV. Secondary Operations for Undercuts
In some cases, incorporating undercuts directly during the vacuum forming process may not be feasible due to design complexity or material limitations. However, secondary operations can be employed after vacuum forming to achieve undercuts and expand the design possibilities. These secondary operations offer a practical solution for creating undercuts in vacuum-formed parts.
Option of Incorporating Undercuts through Secondary Operations:
Secondary operations refer to additional post-processing steps that are performed after the initial vacuum forming process. These operations allow manufacturers to introduce undercuts to the formed parts and enhance their aesthetics and functionality. Secondary operations are particularly valuable when dealing with complex undercuts that are challenging to achieve directly through the vacuum forming process.

Trimming, Cutting, or Adding Additional Pieces for Undercuts:
One common secondary operation for incorporating undercuts is trimming. After the vacuum forming process, excess material or flash extending beyond the desired part shape is removed. By carefully trimming specific areas, designers can create undercuts, transforming a simple vacuum-formed part into a more intricate and functional design.
In some cases, cutting or adding additional pieces to the formed part can also introduce undercuts. By carefully cutting into the formed part or attaching separate components, designers can achieve undercuts in specific locations, further enhancing the part’s features and complexity.
Examples of Using 3D Printing or Machining for Complex Undercuts:
For more intricate and complex undercuts, 3D printing and machining are valuable techniques in secondary operations. 3D printing allows for the creation of custom molds with intricate geometries, enabling the formation of undercuts that might be challenging with traditional mold-making techniques. The flexibility of 3D printing allows designers to experiment with various undercut designs and quickly iterate until the desired result is achieved.
Machining, on the other hand, offers precision and accuracy in creating undercuts. CNC machining can be used to mill away specific areas of the formed part, introducing undercuts with high precision. Machining is particularly suitable for parts with complex shapes and tight tolerances, ensuring the accurate formation of undercuts according to the design specifications.
In conclusion, secondary operations offer a practical option for creating undercuts in vacuum-formed parts. By employing trimming, cutting, adding additional pieces, 3D printing, or machining, manufacturers can achieve complex and intricate undercut features that enhance the visual appeal and functionality of the final product. These techniques provide greater design flexibility and open up possibilities for creating innovative and unique vacuum-formed parts with undercuts.
V. Considerations and Challenges
Complexity of Mold Design when Incorporating Undercuts:
Incorporating undercuts in vacuum-formed parts introduces additional complexity to the injection molding and design process. The mold must be carefully engineered to accommodate the undercut features and allow for smooth demolding without damaging the part or the mold. Designers need to consider the shape, size, and location of the undercuts, ensuring that the mold can be precisely machined to form these features accurately. Complex undercuts may require sliding molds, collapsible cores, or other intricate mechanisms to achieve successful demolding. Proper mold construction is essential to ensure that the formed part retains its intended shape while allowing for the smooth release of undercuts during the vacuum forming process.
Influence of Part Size on the Feasibility of Creating Undercuts:
The size of the part can significantly influence the feasibility of incorporating undercuts in vacuum-formed parts. Smaller parts with intricate features may be more amenable to including undercuts, as they offer greater design flexibility and ease of demolding. However, larger parts with deep or complex undercuts may pose challenges during the forming process. Larger parts require more extensive and robust mold structures to support the undercut features and maintain part integrity. Additionally, the size of the vacuum forming equipment and the available forming area also dictate the maximum size of parts that can incorporate undercuts effectively.
Thermoplastic Materials Unsuitable for Forming Undercuts:
While many thermoplastic materials are well-suited for vacuum forming and can accommodate undercuts, certain materials may not be suitable due to their properties. For example, rigid and brittle materials like polycarbonate or acrylic may not adapt well to undercuts, leading to cracking or breakage during demolding. Similarly, materials with low elongation properties, such as PVC or HDPE, may be challenging to form into intricate undercuts without experiencing deformation or material failure.
Materials with high melt viscosity, like high-impact polystyrene (HIPS), may have difficulties flowing into complex mold cavities, making the formation of undercuts less feasible. It is essential for designers to carefully consider the material’s flexibility, elongation, and flow characteristics to select a thermoplastic material that can effectively handle the desired undercuts without compromising the part’s quality or performance.
In conclusion, incorporating undercuts in vacuum-formed parts requires meticulous mold design, consideration of part size, and the selection of appropriate thermoplastic materials. By addressing these considerations and challenges, manufacturers can successfully achieve undercuts that enhance the design and functionality of vacuum-formed parts. It is vital to strike a balance between design complexity, material properties, and manufacturing capabilities to produce visually appealing and functional vacuum-formed parts with undercuts.
VI. Demolding Strategy
Importance of Planning a Demolding Strategy: Planning a demolding strategy is crucial to ensure the successful removal of vacuum-formed parts without causing damage or deformation. Without a well-thought-out demolding approach, undercuts and complex features may get caught on the mold’s surface, leading to part sticking or breakage. A carefully planned demolding strategy reduces the risk of part damage and ensures that the formed parts maintain their intended shape and quality throughout the demolding process.
Use of Compressed Air or Mechanical Aids for Smooth Demolding: Compressed air and mechanical aids are effective techniques used during the demolding process to prevent parts from sticking to the mold and facilitate smooth release. Compressed air is introduced between the formed part and the mold surface to create a thin air cushion, allowing the part to lift away more easily. This technique is particularly useful when dealing with intricate features and undercuts that require delicate handling.
Mechanical aids, such as ejector pins or push rods, can also be incorporated into the mold design to help push the formed part away from the mold after vacuum forming. These aids provide an extra force to disengage the part from any intricate mold features, ensuring a more controlled and reliable demolding process.
Significance of Rounded Corners and Trimmed Edges to Facilitate the Demolding Process: Rounded corners and trimmed edges play a vital role in easing the demolding process. Sharp corners or jagged edges can become points of resistance during demolding, potentially causing stress concentrations or snagging. By incorporating rounded corners and ensuring properly trimmed edges, designers can reduce the risk of part damage and achieve smoother demolding.
Additionally, rounded corners and trimmed edges contribute to the overall aesthetics and safety of the final part. They eliminate potential sharp edges that could pose safety hazards in the end product, making the vacuum-formed parts more user-friendly and visually appealing.
In conclusion, a well-planned demolding strategy is essential to preserve the integrity of vacuum-formed parts and avoid damage during the removal process. By utilizing techniques such as compressed air and mechanical aids, manufacturers can achieve smooth and controlled demolding, particularly when dealing finished parts with intricate features and undercuts. The use of rounded corners and trimmed edges further enhances the demolding process, ensuring the successful production of visually appealing and high-quality vacuum-formed parts.
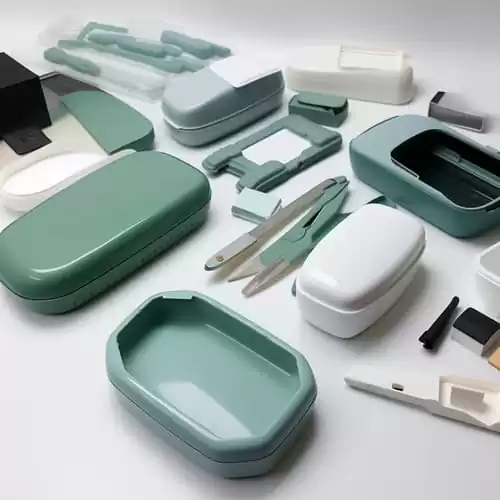
Conclusion
In conclusion, creating undercuts in vacuum-formed parts is an art that requires careful planning, design expertise, and mold construction. By considering the discussed techniques and challenges, manufacturers can achieve stunning vacuum-formed parts with undercuts that elevate their designs and performance. We encourage readers to embrace undercuts in their vacuum-formed parts, paving the way for the production of exceptional plastic components that stand out in a competitive market.