Introduction
Vacuum forming method has quickly become one of the go-to methods for manufacturing plastic products, with various processes available to manufacturers. One such process that has grown increasingly popular over time is vacuum forming, which involves heating a sheet of plastic until it becomes malleable before using vacuum pressure to shape it into desired forms using molds and vacuum-forming machines.
Vacuum forming is an indispensable process within the manufacturing industry due to its versatility and cost-efficiency. It can be used to produce products ranging from car parts to food packaging and lifesaving medical devices, all using vacuum pressure forming.
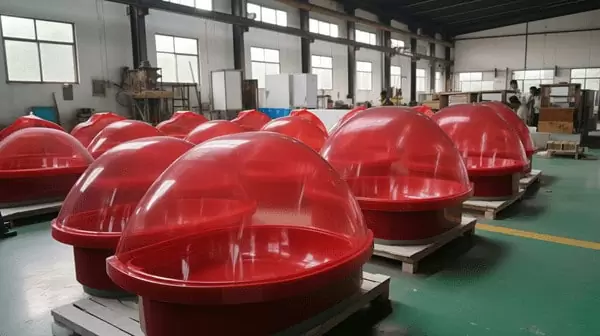
Plastic vacuum forming offers numerous advantages, from low-cost tooling and flexible design/production processes, and rapid prototyping, to minimal waste production. In this article we’ll take a deeper dive into these benefits while discussing their pros/cons impacting on the environment – by the end, you should have a greater grasp on why this form of production has become essential in many industries.
II. Advantages of Vacuum Molding Process
A. Low Cost Tooling
One of the key advantages of using vacuum forming tooling is its cost-effective. In contrast to injection molding, which requires expensive metal molds, vacuum forming tools are constructed from more cost-effective materials like wood, foam, or cast aluminum making this method of production suitable for small-scale production runs or prototyping purposes.
Vacuum forming also allows for multiple parts to be created from one mold, eliminating additional tooling costs and making the production of thinner walls or lower surface areas much less complex.
Vacuum forming offers the option of in-house tooling, providing greater control of production while decreasing lead times.
B. Flexibility in Design and Production
Vacuum forming’s advantage lies in its flexibility in design and production. Because this method involves heating a sheet of plastic until it becomes malleable before shaping it into molds, vacuum forming allows for the creation of complex parts with curves or contours; particularly useful when producing concave or contoured shapes.
Vacuum forming allows manufacturers to use an assortment of plastic materials, including PVC, HDPE, and thermoplastics such as ABS. This gives them flexibility in selecting a material based on factors like durability, flexibility, and heat resistance for their product.
Vacuum forming offers the capability of producing parts with various sizes and thicknesses, making it a viable solution for many industries. From producing small components to larger-scale products, vacuum forming can meet a range of production needs.

C. Rapid Prototyping
Vacuum forming provides the additional advantage of rapid prototyping. Because mold creation is quick and simple with vacuum forming, designers and manufacturers can rapidly prototype their products within days rather than weeks or months.
Rapid prototyping can be especially valuable when testing out new product designs or making modifications to existing ones. By creating and testing prototypes quickly, businesses can save both time and money in their product development processes.
Vacuum forming provides another low-risk method of rapid prototyping, as it enables multiple iterations of designs without incurring costly tooling expenses. This allows businesses to further refine their products before moving forward with full-scale production.
D. Reducing Waste Generation
Vacuum forming is an eco-friendly production option, as it creates minimal waste during its creation process. Unlike injection molding or other processes that use excess plastic material such as extrusion molding, vacuum forming only uses what is necessary to create the part desired – thus decreasing any extra material that needs to be disposed of or recycled.
Vacuum forming provides businesses the option of using recycled plastic sheets, further reducing waste and encouraging sustainability. This makes vacuum forming an excellent way for businesses to reduce their environmental impact.
Overall, vacuum forming’s low waste production makes it an eco-friendly and sustainable option suitable for numerous industries.
III. Pros and Cons of Vacuum Forming process
A. Pros
- Low Tooling Costs: As mentioned earlier, vacuum forming offers low-cost tooling compared to other plastic manufacturing processes. This makes it a cost-effective option for businesses, especially for smaller-scale production runs.
- Quick Turnaround Time: Vacuum forming allows for a relatively quick production process, from creating the tooling to forming the plastic sheet to the desired shape. This quick turnaround time makes it a good option for businesses with tight production schedules or for producing prototypes.
- Wide Range of Materials: Vacuum forming can be used with a variety of plastic materials, allowing businesses to choose the most appropriate material for their product based on factors such as durability, flexibility, and heat resistance.
- Ability to Create Complex Shapes: Vacuum forming allows for the creation of parts with complex shapes, curves, and contours, making it a versatile option for many industries.
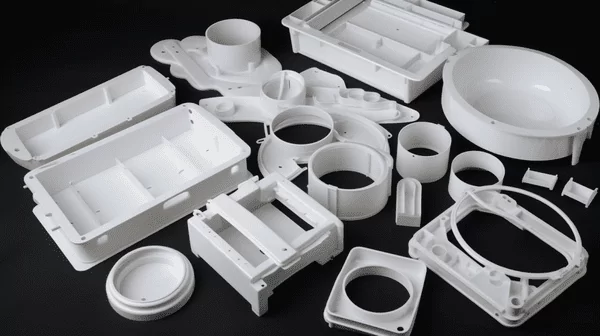
B. Cons
- Limited Wall Thickness: Vacuum forming has a limited wall thickness capability, which may not be suitable for all products. This limitation can affect the structural integrity of the product and may require additional reinforcements.
- Limited Product Size: Similarly, vacuum forming has limitations in terms of the size of the product that can be produced. This may not be suitable for larger-scale products or those that require a larger surface area.
- Limited Surface Detail: Vacuum forming may not be suitable for products that require a high level of surface detail. The forming process can result in surface imperfections, which may require additional finishing processes such as sanding or polishing.
Overall, while vacuum forming offers many benefits, it also has its limitations. Businesses need to consider these pros and cons when deciding whether vacuum forming is the best option for their product.
IV. Vacuum Forming and the Environment
A. Environmental Considerations in Vacuum Forming
Vacuum forming is an environmentally sustainable plastic manufacturing process due to its reduced waste material and energy use. Only what’s necessary for creating the desired product will be utilized, thus cutting down on extra plastic that would otherwise end up in landfills or require recycling.
Vacuum forming has lower energy requirements than other plastic manufacturing processes such as injection molding due to not needing as high of temperatures or pressures for its process of plastic sheet formation.
B. Benefits of Recycling Vacuum Formed Products
Vacuum forming can contribute to sustainability in several ways through recycling. Products made of vacuum formed plastics can be recycled into new products, decreasing virgin plastic production needs while simultaneously decreasing environmental waste in landfills and oceans.
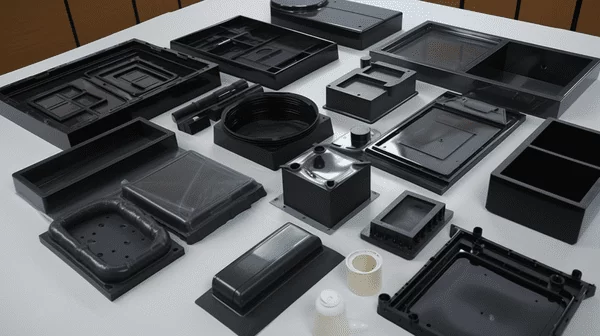
C. Examples of Eco-Friendly Vacuum Formed Products
Vacuum forming has produced many eco-friendly products. Companies use vacuum formed plastic to create sustainable food packaging such as compostable fruit and vegetable containers made with vacuum formed plastics. Vacuum formed products are also being utilized by medical companies for making life-saving devices such as prosthetics made from recycled materials as well as instrument trays with recycled content.
Overall, vacuum forming offers many sustainable advantages when used as a manufacturing process, including low material waste levels and energy efficiency benefits as well as the creation of recycled products. Choosing this form of manufacturing to contribute towards a more environmentally sustainable future.
V. Applications of Vacuum Forming process
Automotive Industry
The automotive industry is one of the biggest users of vacuum forming. Vacuum formed parts can be found throughout a vehicle’s interior trim, dashboards, door panels, and wheel arch liners – ideal applications of vacuum forming that produce large complex shapes for this industry.
B. Medical Industry
Vacuum forming is widely employed within the medical sector. Vacuum formed parts can be found in devices like prosthetic limbs, medical trays, and instrument handles that need precise shapes created via vacuum forming technology – ideal for creating medical devices.
C. Food Packaging
Whilst vacuum forming may be one of the more cost-effective means of producing food packaging, vacuum forming remains one of the go-to methods in terms of custom-shaped containers for various foods like meat, produce, and baked goods. It has become an indispensable aspect of today’s food industry and should continue its use going forward.
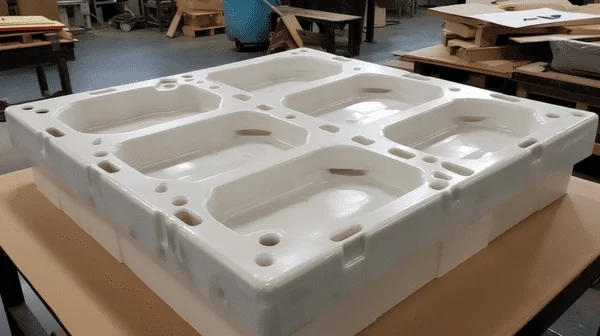
D. Other Industries
Vacuum forming can be applied across numerous industries, from electronics to consumer goods and construction. It can create parts such as machine enclosures, housing for electronic components, and point-of-sale displays; plus the versatility makes vacuum forming an appealing option in multiple fields.
Overall, vacuum forming is an efficient and versatile manufacturing technique used by businesses across numerous industries. With its ability to produce custom shapes, low-cost tooling costs, and rapid prototyping capability, vacuum forming offers businesses cost-cutting production processes.
VI. How Vacuum Forming Works
A. Step-by-Step Production Process
Vacuum forming involves heating a sheet of plastic until it becomes malleable forming temperature, then placing it over a same mold surface and using vacuum pressure to mold it into its desired form. Here are the steps involved with vacuum forming:
- Design of Mold: When designing the mold for a product, its shape must conform to what it will eventually produce.
- Create the Mold: When designing the mold, materials such as wood, foam or cast aluminum may be utilized to help complete this step.
- Heat the plastic sheet: Once heated, plastic sheets become malleable and ready for shaping.
- Attach the plastic sheet to the mold: Once hot, the heated plastic sheet should be carefully laid over the mold and its edges secured to keep it in place.
- Apply vacuum pressure: Vacuum pressure should be applied to the mold to pull the plastic sheeting over and form it into desired shapes.
- Cool the Part: Once formed into its mold, the plastic sheet must be cooled quickly to harden and retain its desired form.
- Remove the Part: Once complete, the formed piece should be extracted from its mold and any excess material trimmed away.
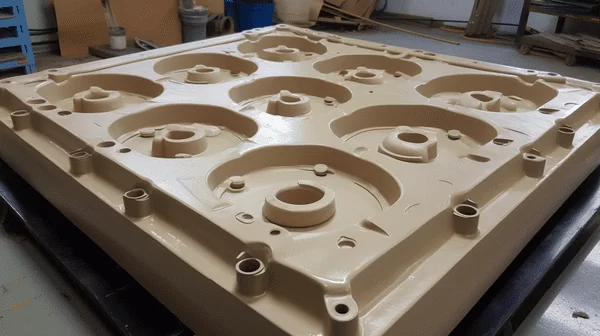
B. Explanation of Vacuum Pressure and Positive Air Pressure
Vacuum pressure refers to the force created when air is removed from a closed space by pulling backward. In vacuum forming, this force is utilized to draw plastic sheets onto molds for shaping into desired forms.
Positive air pressure is the opposite of vacuum pressure; it refers to any pressure generated from adding air into a closed space. Positive air pressure can be used effectively during vacuum forming to help push plastic sheets onto mold more securely for more detailed shapes.
C. Description of Vacuum Forming Equipment and Materials
Vacuum forming requires specific equipment, including a vacuum forming machine, mold, and plastic sheet made from PVC or HDPE thermoplastics.
A vacuum-forming machine consists of three primary elements: a heated platen, mold, and vacuum system. The heated platen heats plastic sheets before molding them to desired shapes using vacuum pressure applied through the mold – while vacuum pressure applied via the vacuum system pulls plastic sheets from heated sheet and onto the mold for shaping into desired forms.
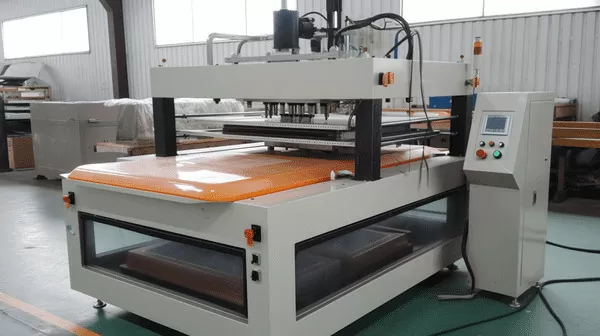
Conclusion
As previously discussed, vacuum forming is a versatile and cost-effective plastic manufacturing process that offers many benefits for its users, such as low-cost tooling costs, flexible designs and production lines, rapid prototyping capabilities, minimal waste production rates, and sustainability. Vacuum forming can be found across several industries including automotive, medical, food packaging, and construction industries.
Companies seeking cost-effective and efficient production processes should consider vacuum forming. With its low tooling costs, ability to form complex shapes quickly and fast turnaround time, and sustainability benefits – vacuum forming offers businesses an ideal way to reduce production costs while decreasing environmental impact.
As technology continues to advance, vacuum forming looks poised for an impressive future. New developments in equipment and materials make the process even more efficient and sustainable; and with its versatility and cost-effectiveness, vacuum forming should remain an attractive choice across various industries in years to come.