To some extent, the rapid development of manufacturing industry depends largely on the rapid development of plastics. Its versatility and adaptability revolutionized the entire manufacturing industry. From packaging materials to car and computer parts, almost anything can be made from plastic.
It is important to mention in this context that one of the manufacturing processes that drives this rapid development is thermoforming (vacuum forming). Vacuum forming offers a way to transform a flat plastic sheet into a 3D shape by heating it until it becomes soft so that you can stretch or bend it as needed to get the final product.
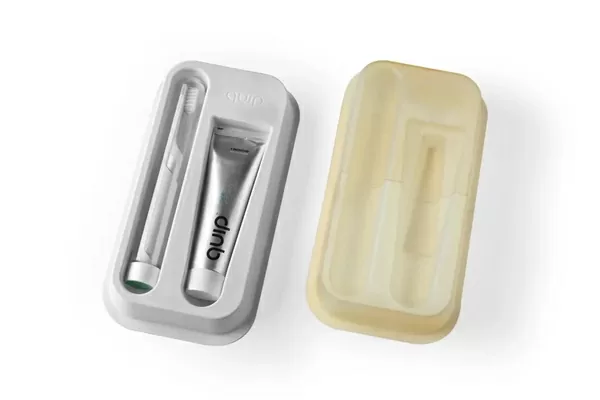
However, the secret to vacuum forming doesn’t just lie in what’s done to the sheet after it’s been heated and formed, but begins during the preparation process. If this stage is done well, your final product will be consistent in appearance and quality.
In this blog post, we break down all the steps involved so you can perform them yourself without worrying about whether things are going according to plan, ensuring you have the knowledge to produce high-quality molded plastic every time.
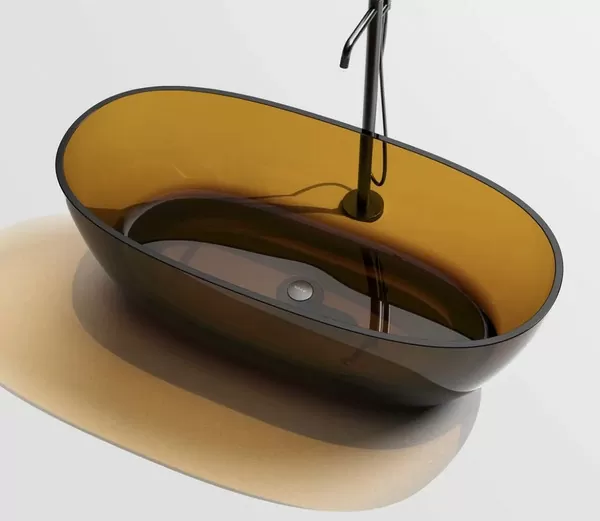
The Forming Process
When the plastic sheet is ready and the mold is ready, the molding process can begin. There are several steps involved:
Clamping
Clamp the prepared plastic sheet onto the mold so that it seals tightly with the mold shape.
Heat
Applying heat (generated by an oven or heat lamp) gradually softens the sheets until they become elastic enough.
Shaping
After heating long enough, at the correct temperature. By using a vacuum pump to suck out the air between the mold and the sheet, the material is adsorbed to the surface of the mold to form the final shape.
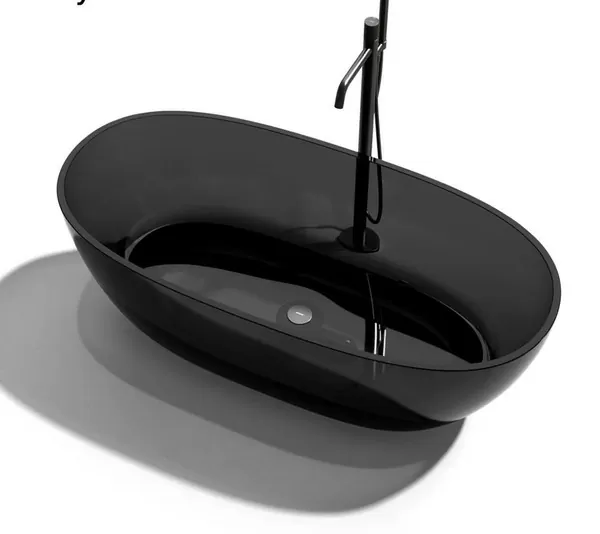
Cooling
After the plastic is molded, it is cooled to final shape by circulating air or using a water-cooled mold.
Trimming
Excess material is typically trimmed away, leaving the vacuum formed parts in its final shape.
Selecting the Right Plastic Sheets
Choosing the right material for your vacuum formed product is a crucial first step. The plastic sheet you choose affects factors such as strength, flexibility.
Common Materials
Acrylonitrile Butadiene Styrene (ABS)
Tough and impact resistant. Commonly found in car parts and items we use around the home every day.
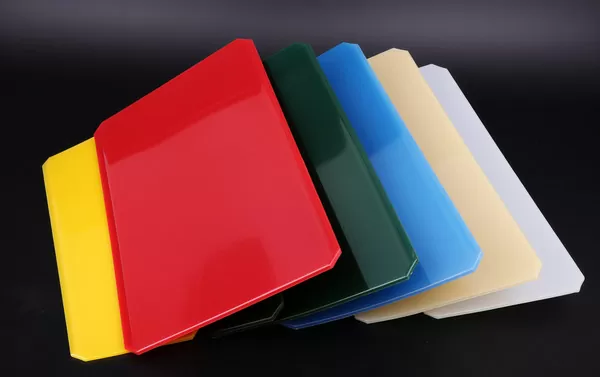
High Impact Polystyrene (HIPS)
Inexpensive but still performs well. HIPS works great if you need to make a large number of refrigerator liners or display cabinets quickly and cheaply.
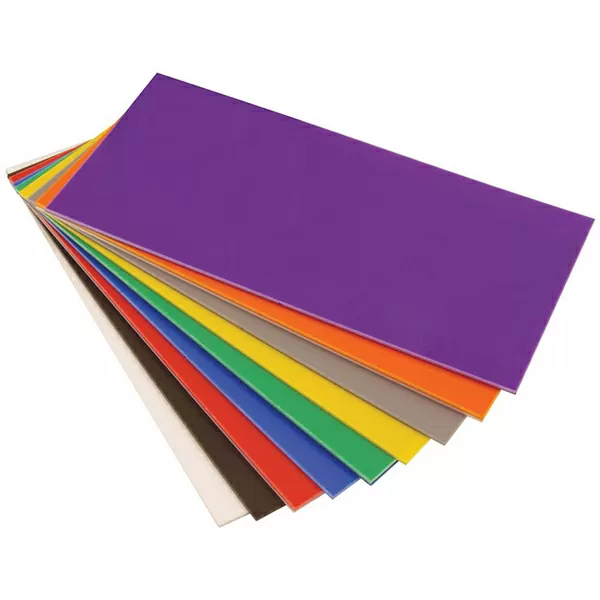
Polyethylene Terephthalate Glycol (PETG)
PETG offers excellent clarity and light transmission while being strong enough for packaging packaging and signage.
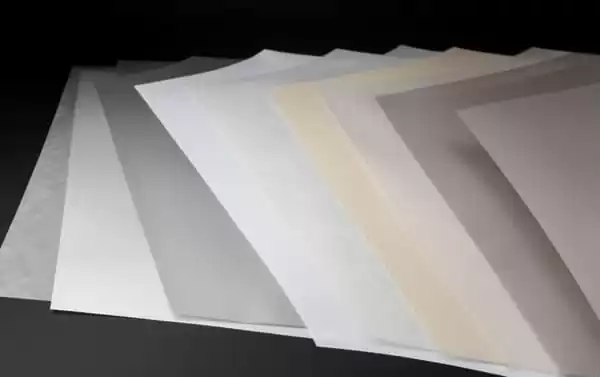
Polyvinyl Chloride (PVC)
The most commonly used vacuum forming material, which is soft, tough, and malleable. It can be made into transparent and various colors.
Transparent PVC is commonly used to package electronics, cosmetics, toys, gifts and other products.
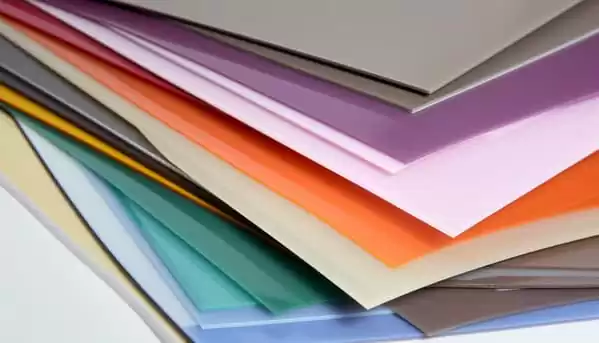
Polyethylene Terephthalate (PET)
Hard, tough, high strength, bright surface, environmentally friendly and non-toxic, available in transparent and various colors. The disadvantage is that high-frequency heat sealing of PET is difficult and the price is much more expensive than PVC.
This material is often used to replace PVC by users who require high-end and environmentally friendly products.
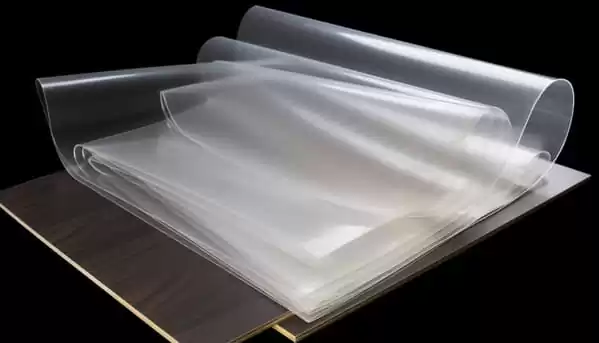
Polystyrene (PS)
Low density (light weight), environmentally friendly and non-toxic, very good plasticity, poor toughness and easily brittle. It cannot be made into transparent materials, so it can only be made into bottom-type vacuum forming. Because it is easy to crack, this type of vacuum forming should not be recycled.
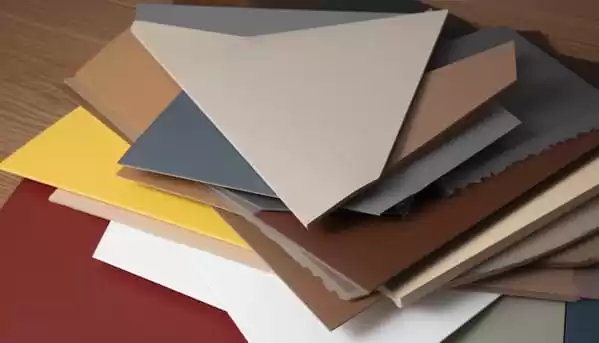
Polypropylene (PP)
The material is particularly soft, has good toughness, is environmentally friendly, non-toxic, and resistant to high temperatures.
It is often made into packaging for dining utensils or other high-temperature-resistant products; however, it has poor plasticity, difficulty in processing, poor surface gloss, and the color will change during processing.
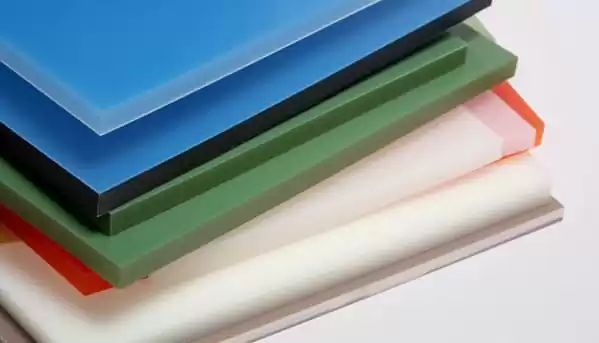
Polyethylene (PE)
PE is the world’s most produced synthetic resin and the most consumed plastic packaging material, accounting for about 30% of plastic packaging materials. Its performance advantages are mainly reflected in its good transparency, softness, high elongation, and better impact resistance and low temperature resistance than HDPE.
It is still used in large amounts in various types of packaging, but its shortcomings are obvious as a food packaging material.
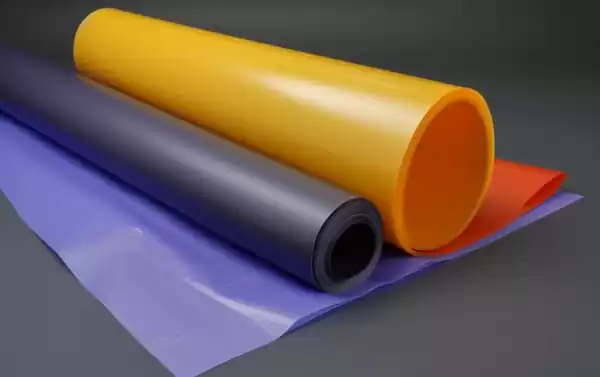
Polyvinylidene Chloride (PVDC)
The characteristics of PVDC are that it is soft and has extremely low air and water permeability, which can prevent the penetration of odors, has good freshness and fragrance retention properties, and is suitable for long-term preservation of food; it has excellent acid, alkali, chemical and grease resistance, and has good heat shrinkage.
It is suitable for sealing packaging and is a good heat shrink packaging material. The disadvantages of PVDC are that it is too soft and has poor operating performance; it is highly crystalline, easy to crack and perforate, and has poor aging resistance; its monomer is also toxic, so it is mainly used as coating materials or manufacturing composite materials.
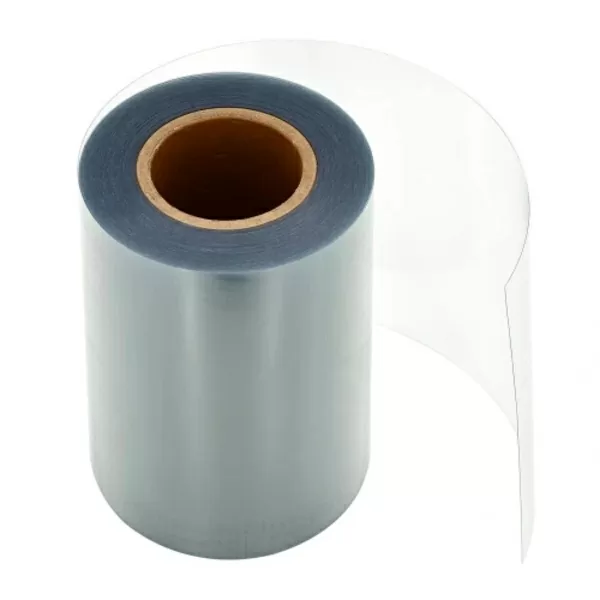
High Density Polyethylene (HDPE)
HDPE has good heat and cold resistance, chemical stability, strong rigidity, good toughness and resistance to environmental stress cracking. Main uses: top covers of vacuum forming tray, fuel tanks, special packaging of most automobile parts, etc.
The thickness of the material is also worth considering, as thicker sheets may require more heating before they are ready to be properly formed by the vacuum forming machine, so each cycle time may end up being longer compared to thinner gauge materials. The boards may not support more rugged applications.
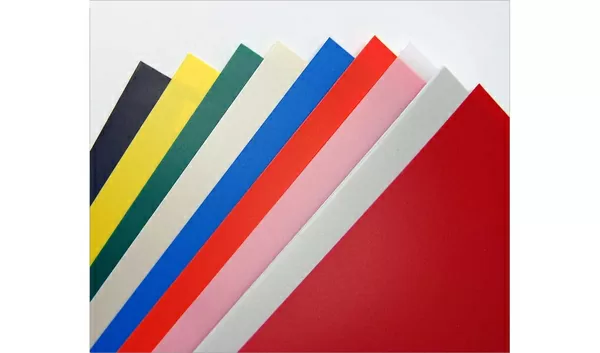
How to Choose the Right Material?
Before we start the vacuum forming process, the first thing you need to do is choose the right vacuum forming plastic material. This is an important choice because it will affect the strength, beauty, and usefulness of your finished product.
Material Properties
Material properties play a vital role in vacuum forming packaging. Specifically, the properties of the plastic sheet must be considered, including but not limited to softening point, crystallinity, melting point, etc.
Failure to select materials that meet the appropriate levels of pressure forming temperatures and these factors may result in the inability to melt them sufficiently for molding purposes during production.
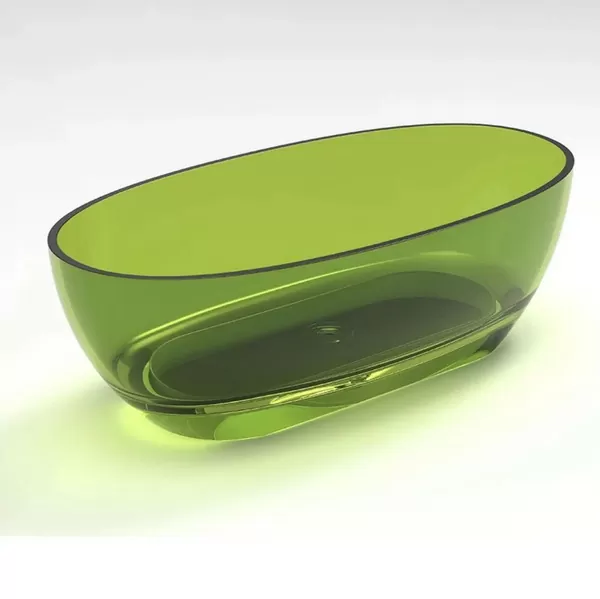
Material Thickness
The thickness of the material used must be considered as it affects the rate of heat transfer through the material and the efficiency with which molten plastic is formed.
When choosing a vacuum pressure forming material, it is very important to choose a material with the right thickness, so that it can not only melt smoothly, but also ensure successful molding after melting.
Material Surface Treatment
Material surface treatment is an important factor to consider for plastic sheets. This includes processes such as printing or coating.
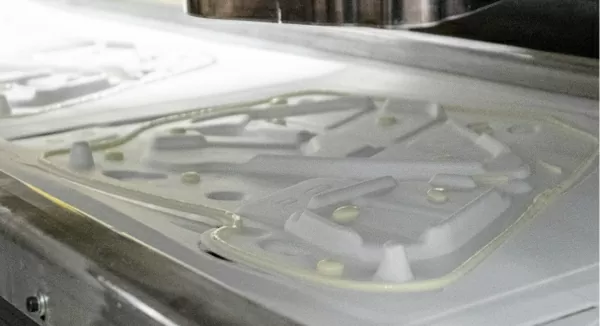
When selecting materials, it is crucial to select the correct surface treatment technology for your vacuum forming requirements – this way you can ensure that the overall finish, as well as the molding results during the molding process, are as expected.
Material Strength
Material strength should be considered as plastic sheets must withstand pressure and heat during vacuum forming.
Therefore, the appropriate strength must be selected when selecting materials to ensure that the sheet can withstand the given temperature/ air pressure.
Material Cost
Material cost is an important factor to consider for plastic sheets, because the cost of blister sheets will directly affect the cost of blister molding.
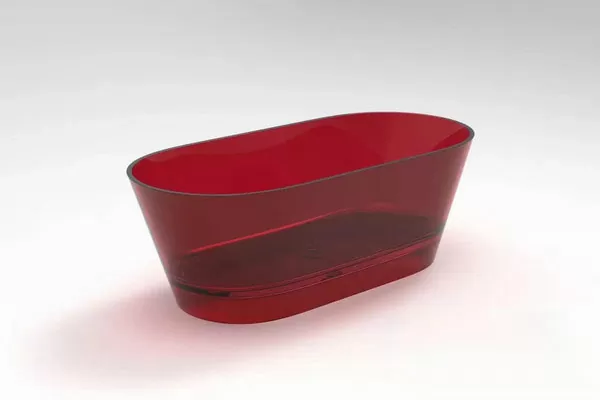
When selecting materials, it is necessary to select appropriate raw materials according to the requirements of vacuum forming to ensure that the cost and quality of the vacuum sheet match.
Heat Resistance
The material must soften evenly at the desired molding temperature, which may vary depending on the plastic type.
Cleaning and Drying
In order to make the plastic sheet molding more perfect, the sheet needs to be thoroughly cleaned before molding.
This removes dirt, dust, and other impurities that might otherwise affect its molding effect. Additionally, this step helps ensure that coatings or labels added later will adhere properly.
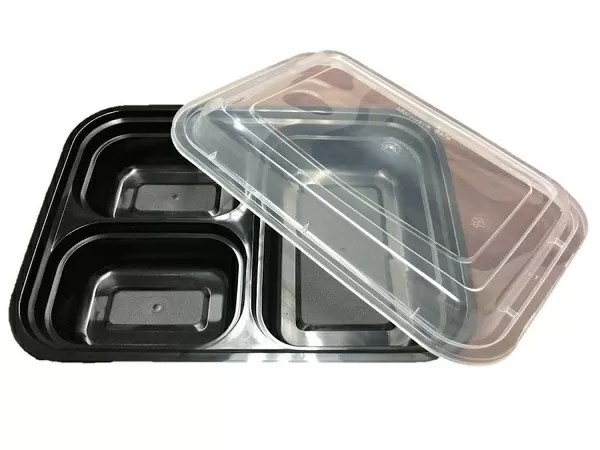
The drying process is even more important. If there is water or moisture in the sheet, bubbles or other issues may form when heated, creating defects in the final result.
When this happens, moisture in the air can also be absorbed by the plastic, so manufacturers sometimes address this situation by blowing the plastic sheet dry with compressed air before molding.
Preheating and Forming Temperature
The preheating stage is as important as all other stages in the vacuum forming process. In this step, the plastic sheet is slowly heated until it reaches a temperature just below its molding point, which makes the material more pliable while also minimizing the chance of thermal fracture later on.
The temperature required to heat a plastic varies depending on the specific thermoforming properties of its raw material and the type of plastic used. For example, PETG typically requires temperatures between 300-320°F (149-160°C), while for ABS it is not uncommon to use temperatures in excess of 360°F (>182°C).
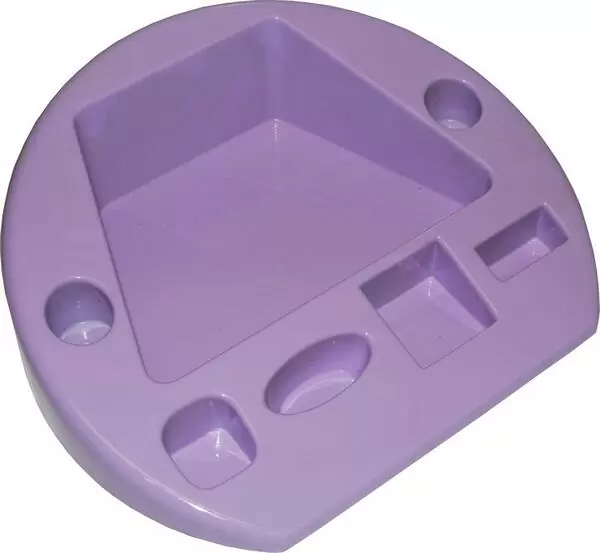
Changes of just a few degrees can significantly affect the behavior of a material, so it is crucial to refer to the material manufacturer’s recommendations.
Molds and Molding Surfaces
In the plastic vacuum forming manufacturing process, the mold is very important for shaping. Choosing the right mold material is important as it needs to conduct heat well so that the plastic sheet heats evenly. Manufacturers often choose materials such as composites or aluminum because of their ability to efficiently transfer heat energy and their overall strength; they also have other useful properties.
The mold surface is equally important, it must be smooth and free of flaws or blemishes. If there are any flaws or blemishes on its surface, these will also show up on the molded plastic as well as the final product. This may mean finishing has to be done after molding to deal with flaws or blemishes, which not only costs money but takes up valuable production time.
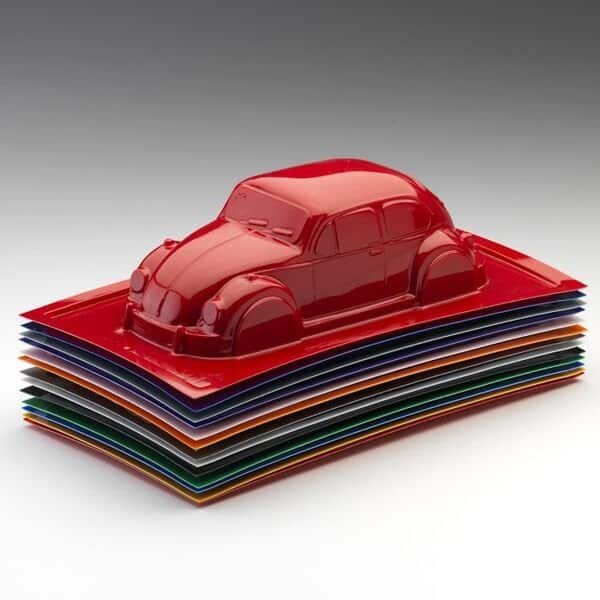
Common Challenges and Solutions
Despite careful planning, vacuum forming can still present some difficulties. Some common questions include:
Bottom Too Thin or Too Thick: Inconsistent heating may be the culprit, try changing the temperature or rotating the mold during the molding process.
Webbing: Webbing occurs because certain areas are stretched more than they should be, creating thin strands of plastic between them. Using a plug assist or changing materials will solve this problem nicely.
Material Hangs Too Much: Sometimes, material can hang too much, causing it to sag or mold below the mold line. Hotter preheating and controlling the molding speed can solve this problem.

Mold Maintenance and Material Reuse
Regular mold maintenance is an important but often forgotten step in vacuum forming. To ensure that molds are durable and produce high-quality parts, they must be inspected and cleaned regularly.
If obvious signs of wear or deformation appear during this process, take immediate steps to correct the problem to avoid defects in the final product.
Recycling or reusing materials when possible saves money and is good for the environment. Building off scraps and excess materials and mixing them with fresh materials makes future products cost less than buying new raw materials each time.
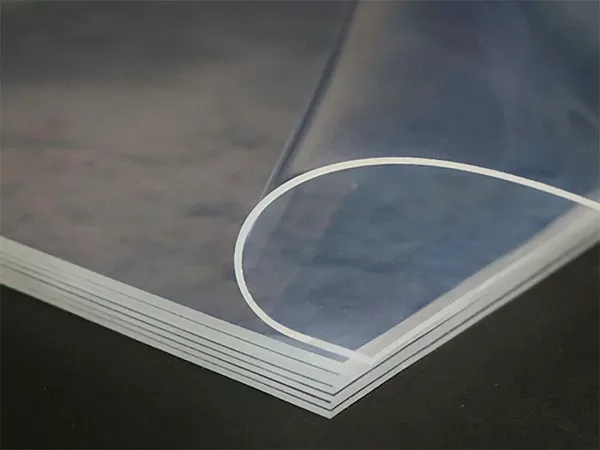
The Future of Vacuum Forming Prep
The process of preparing vacuum-formed plastic sheets is both art and science. Recent advances in heating technology, materials and finishing techniques have improved the process as a whole: now it produces a better product while using fewer resources and reducing waste, which is an all-around win.
Future Trends Shaping Vacuum Forming Preparation Include:
Use Recyclable and Biodegradable Materials
The industry is moving toward greener options, although it still faces obstacles in finding sustainable and high-performing materials.
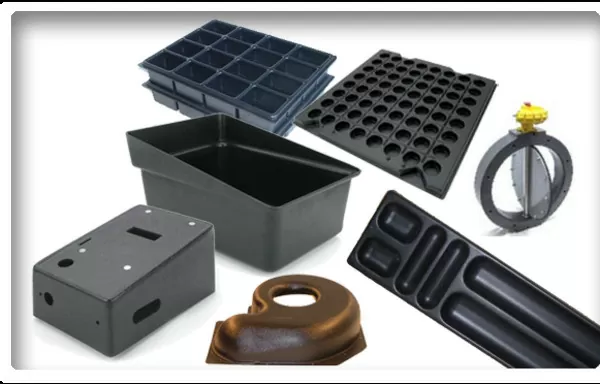
Advanced Heating Technology
Induction heating and infrared technology are becoming increasingly popular as people look for ways to use less energy while getting precise results.
Automate Finishing Processes
Companies are now programming robots to perform finishing jobs because these machines can perform complex tasks faster and more accurately than humans.
Real-Time Monitoring and Feedback
Manufacturers have begun using sensors connected to artificial intelligence systems, for example, allowing them to detect defects early in production, thereby reducing products that need to be scrapped or reworked later.
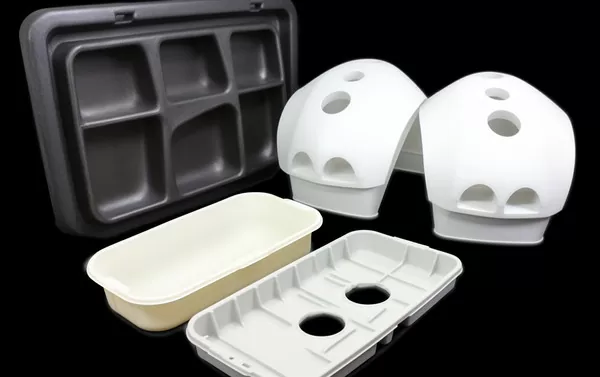
The technology for preparing vacuum formed plastic sheets requires traditional techniques and modern knowledge. To make a top-notch product with excellent performance, you must choose the right materials; prepare the plastic sheet correctly, use the best molding methods and final trimming and finishing, and understand all the details involved.
Technology continues to advance, as do material options, which means there are almost no limits to what vacuum forming can do and the range of applications its products can be used for.
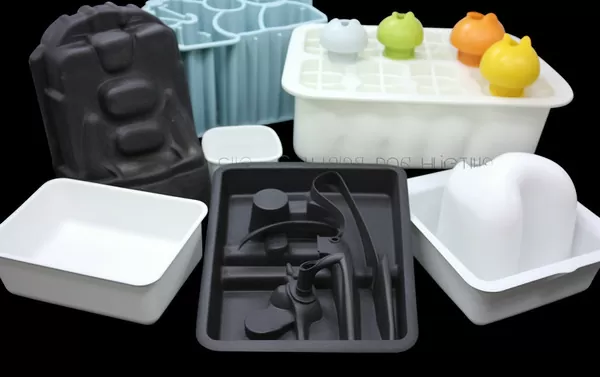
Differences in Material Selection between Vacuum Forming and Injection Molding
The preparation of plastic sheets for vacuum forming and injection molding processes is critical in determining the quality and performance of the final product. Although the two processes require slightly different material properties, they share a common goal: to find a plastic sheet or resin that, when manipulated, easily conforms to specific conditions to achieve its intended shape. Below we outline how both methods prepare plastic before processing.
Vacuum Forming Preparation
1. Choose the Right Plastic Sheet: The first step before starting vacuum forming is to choose the type of plastic sheet that best suits your needs. Some options you can consider include acrylic (PMMA), polystyrene (PS), acrylonitrile butadiene styrene (ABS), and polyvinyl chloride (PVC). They all have different properties, such as impact resistance, transparency and heat resistance, which make them suitable for specific applications.
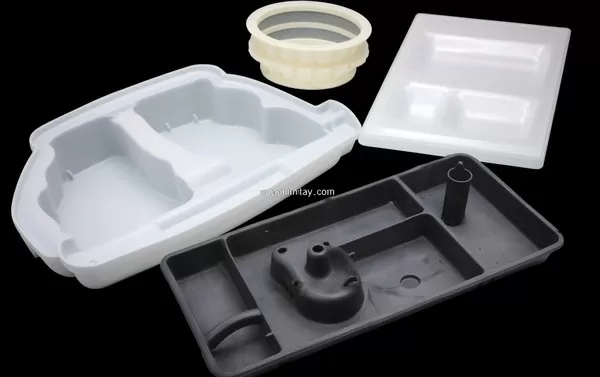
2. Sheet Thickness and Size: Based on your design, you need to choose plastic sheets with appropriate thickness and size. Thicker sheets are used for sturdier products; thinner papers capture finer details. Of course, the sheet size must fit your industrial vacuum forming machines or diy vacuum forming machines.
3. Pre-Dry Plastic Sheets: Certain types of plastics (especially hygroscopic plastics like ABS) require pre-drying if you don’t want moisture to cause defects in the final product. Industrial dryers circulate hot air to remove moisture from these materials.
4. Heating the Plastic Sheet: In order to shape it through vacuum forming, the plastic sheet must be heated to a temperature where it is pliable but not yet melted (different types of plastic require different temperatures). It also needs to be heated evenly so that your molded product always has a consistent thickness; this also helps capture detail.
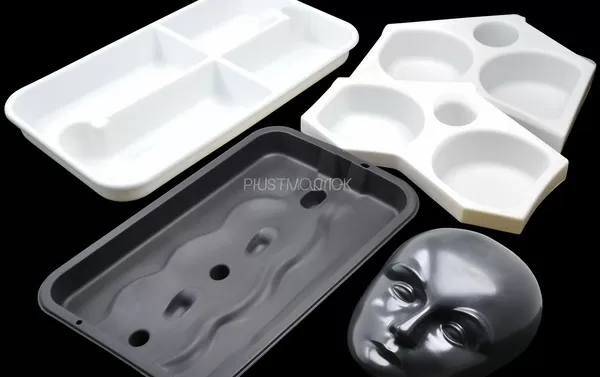
Injection Molding Preparation
1. Material Selection: Just like vacuum forming, the first step is choosing the right resin. You typically need a thermoplastic or thermoset material to meet the strength, flexibility, and other performance requirements of your application.
2. Resin Drying: For injection molding, some resins may need to be dried before use to eliminate any residual moisture content. If it occurs during the molding process, it may cause problems such as gaps or expansion in the finished product.
3. Resin Pellets: Pellets rather than powder Injection molding compounds are typically available in small pellets rather than powder form. Pellets make it easier to transport material and feed it into the machines that do the forming – they’re also helpful when you need to measure quantities.
4. Coloring: If you require color, it can be included in the pellets before molding.
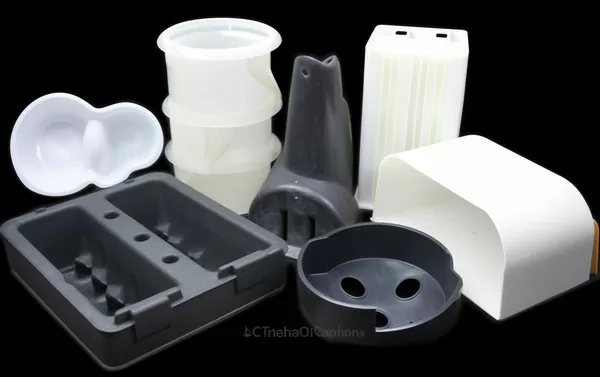
5. Melting: In the injection molding machine, the resin particles are fed into the heated barrel and melted there. The molten plastic is then injected into the mold cavity, where it cools and solidifies into its final shape.
The preparation of plastic sheets for vacuum forming and resin pellets for injection molding is a delicate process that has a great impact on the quality, strength and appearance of the final product. If you want to achieve good results with either technique, you need to carefully consider what materials to use, how to handle them before starting, and follow all the correct steps during the production process.
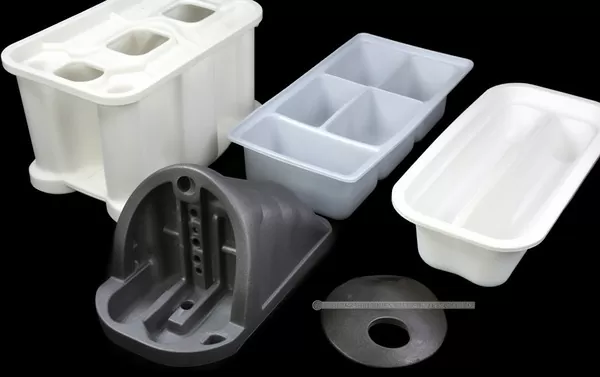
Conclusion
The first step in making first-class plastic parts is preparing the plastic sheet for vacuum forming. This meticulous work requires you to pay attention to everything, accurately follow the requirements of the materials, and do things in the best way from start to finish to ensure the perfection of the product.
From material selection to tooling and maintenance, every stage is important to the success of vacuum forming. When manufacturers master these steps and how to put them together, they end up with fine parts that perform well every time.
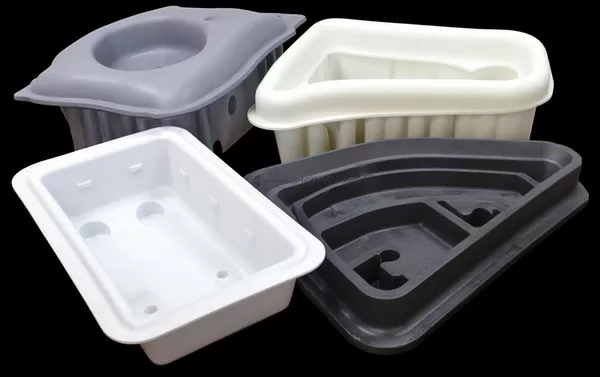
When vacuum forming manufacturers can become proficient in preparing plastic sheets for vacuum forming, they can streamline the way vacuum forming machines operate while improving the products they sell: By making these materials available through better technology, companies may find themselves using only More products can be made from one substance than previously thought.