In manufacturing, cutting costs isn’t just a nice-sounding thing for companies to talk about—it’s what they need to do if they want to continue to be profitable and stay ahead of the curve. This is especially true if you work in thermoforming (making things out of plastic); custom packaging, automotive, and medical device manufacturers all use your products in large quantities, so being able to reduce packaging costs or decoration costs without compromising on quality helps them too.
Thermoforming is a highly adaptable manufacturing method in which a thermoplastic sheet is heated until it becomes easy to form. The softened plastic sheet is then adsorbed to the mold, where it cools and solidifies into the desired shape. It’s often used for a range of everyday items that need to be both beautiful and low-cost; in fact, there seems to be no end in sight to this one-off craft.
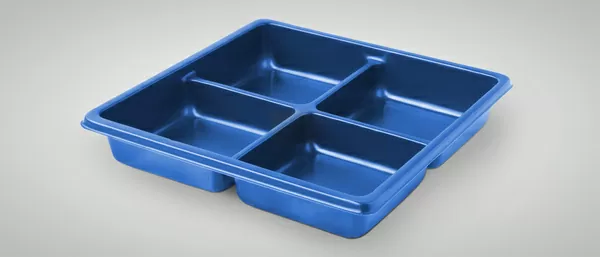
In this blog post, we’ll discuss different ways to reduce thermoforming costs. These methods can help businesses save a lot of money – and they’re not just changes made on the factory floor! We’ll also examine how managers need to shift their thinking if savings are to be sustained over the long term.
If you want to cut costs but still maintain high standards and stay safe, this blog is for you! We’ll show you the many different ways thermoforming companies can reduce expenses while increasing profits without taking any risks to quality or well-being. Learn more below…
Thermoforming Process
Before we discuss ways to reduce costs, it’s important to understand the basics of thermoforming. Thermoforming is a manufacturing process known for its simplicity and speed. It is suitable for making a variety of plastic products, such as disposable cups, blister packaging, or vehicle dashboards, interiors, etc. Thermoforming is likely to be your first choice. Because it can produce large and durable items faster and at lower cost than almost any other methods.

Like injection molding, the thermoforming industry is currently at a critical juncture, combining advances in the accuracy of manufacturing processes with the necessity of inexpensive production methods. As society becomes increasingly reliant on items such as plastic packaging materials, auto parts, plastic components, food containers and even healthcare necessities as everything is protected, thermoforming is a great solution and society is calling for using as few resources as possible to provide it. solution, so the importance of thermoforming machines becomes obvious.
The Unseen Burden of Unchecked Costs
The cost optimization potential of the thermoforming process covers every stage. If not carefully controlled, multiple factors can combine to create a significant cost burden. Below, we’ll take a closer look at key cost drivers and how they impact overall performance.
1. Material Costs and Utilization
When it comes to thermoforming, material costs make up a large portion of the total expense. Whether it is the trimming of the product after molding or the thickness of the product, any wasted material will increase the material cost in the production process.

2. Energy Efficiency
Thermoforming requires a lot of energy, and if left unchecked, the cost of heating, cooling and even machine operation can cause energy bills to inflate.
3. Labor and Productivity
Labor and productivity are important factors to consider when analyzing business costs. On the one hand, having enough workers is crucial to completing a task; on the other hand, too many can cut into profits.
4. Quality Control
If a company produces products that require repair and rework or discards them because they are substandard, these actions increase costs in the production process.

Streamlining Material Usage
1. Understanding Materials
When it comes to thermoforming, not all plastic materials are created equal—each has its own characteristics and costs. Whether you are using cost-effective polyvinyl chloride (PVC), high density polyethylene (HDPE), high-impact polystyrene (HIPS) or biodegradable polylactic acid (PLA); the choice of material will directly impact the cost incurred. Understanding the inherent advantages, ductility levels and post-consumer applications of different plastic types can help guide a smarter purchasing process.
This section explores some factors worth considering when assessing substances – arguing for an approach that makes products fit for purpose rather than over-specifying.

2. Material Waste Reduction
Reducing waste during production is an important area where costs can be cut. With careful measurements during the molding process, there could be far less waste in the production process than there is now. So it’s important to understand how technology can help with this, and understand the benefits of technologies like roll forming or pressure forming, both of which have potential advantages and can help us control waste in the production process.
For example, the regrind rate is reduced – the waste material is shredded and put back into place again. We also consider the design aspect: if you consider possible waste upfront when designing a part (thin walled designs or thick walled designed), it may not require as much trimming later, which can also reduce waste.

Operational Efficiency
1. Equipment and Technology
If you invest in machinery and technology with a focus on quality on one hand and efficiency on the other, it can save you a lot of money. Invest in the latest vacuum forming machines that not only increase speed but also offer predictive maintenance so they start up exactly when needed (and keep them running). Then, there are computer-aided design systems that allow workers to make quick adjustments, which means less waiting, but also cost savings through less damage to raw materials.
2. Energy Consumption
Energy use is a significant expense for thermoformers, so finding ways to reduce this cost can have a significant impact on their bottom line. Assessing the type of energy required before production and planning in advance the technologies available for energy management can therefore significantly reduce costs.

Labor Optimization
1. Up-Skilling the Workforce
Thermoforming companies can increase productivity and reduce training costs if they provide workers with ongoing education and training programs. Employees need to stay up to date on new machinery and production technologies; having a skilled workforce will help companies achieve higher output rates despite high employee turnover without having to spend too much on mentoring.
2. Process Standardization and Automation
By standardizing operating procedures and integrating automation, businesses can reduce labor hours and minimize human errors. At the same time, this action improves accuracy and control. Manufacturers should explore how automating in-line cutting, stacking, and quality inspection can save companies money—potentially a lot of money.

Design for Thermoforming (DFT)
An often overlooked area for cost mitigation is the design of the product itself. An efficient DFT approach can result in substantial savings across various facets of production.
1. Simplicity Equals Savings
The more complex the design, the longer the production cycle, so more material is likely to be wasted, and you also have to spend extra money on tooling. If you simplify the look of something without making it worse, you can save a lot of money. For example, design strategies such as rounding corners, using common radii, and standardized undercuts can not only reduce manufacturing complexity but also improve the overall quality of the product.

2. Tooling Optimization
Using inefficient molds can significantly increase costs. However, there are several ways to significantly reduce expenses: use modular tooling for multiple projects; employ CNC machining for high precision; and incorporate rapid prototyping to validate the design (this step alone will help avoid costly mistakes). Thermoformers may also want to consider how lower-cost materials such as epoxy or aluminum can provide cost savings on shorter runs/prototypes.

Supply Chain Management and Partnerships
An optimized supply chain and strategic partnerships can yield cost efficiencies and improved product quality and delivery times.
1. Local Sourcing
Where possible, sourcing materials and services locally can reduce shipping costs and lead times. This can also build stronger relationships with suppliers, potentially leading to volume discounts and improved service levels.

2. Collaborative Partnerships
Building lasting relationships with suppliers can bring many benefits to both parties, such as shared expertise, access to additional resources, and more manageable risk levels. Various ways of achieving this include pooling orders together; sharing expensive manufacturing machinery and even jointly working on product development projects aimed at improving efficiency – all actions that ultimately lower costs for everyone while also increasing competitiveness level.
Waste Reduction and Recycling
Minimizing waste and implementing recycling programs not only have environmental benefits but also contribute to significant cost savings.
1. Lean Inventory Management
Using an efficient inventory management system facilitates the use of reduced roll or plastic sheets sizes, which means less residual scrap while also reducing material costs. By keeping a close eye on inventory levels and consumption rates, thermoformers can better match material usage to production requirements: another step toward reducing waste.

2. Closed-Loop Recycling
Closing the recycling loop and reusing production scrap in the manufacturing process can reduce costs and make operations more environmentally friendly. Thermoformers need to work with their suppliers to seize the closed-loop opportunity—it’s really good business.
Regulatory Compliance and Process Standardization
Adhering to regulations and standardizing processes can lead to substantial financial benefits.
1. Compliance Cost Reduction
Manufacturers who want to avoid costly fines and reduced production must comply with the new regulations and take immediate steps to ensure their factories comply before they are penalized or find themselves unable to meet demand: services provided by consultants, employee training courses (plus Investments such as automated systems) provide manufacturers with ways to better deal with legal requirements.

2. Process Standardization and Optimization
Standardizing and optimizing thermoforming processes across products and production lines can bring economies of scale and resource sharing. For example, when best practices are established and all departments operate from a common operating manual, thermoformers can reduce errors and improve operational inefficiencies—both actions that tend to reduce costs.
Conclusion
Cost savings are not only a challenge for the thermoforming industry but also provide a way to achieve growth through innovation. Industry players who apply our concepts can become leaders in efficient production, adding value to customers and investors. Being resilient means continually adapting and improving operations. In this business environment where competition is everywhere and profits are tight, companies need every possible way to save money! We believe that if you follow our explanations of how to best use materials; standardized processes, etc., success will continue to come to you.