Production is a complex process that requires precision, ingenuity and efficient organization. Among the many steps involved in manufacturing goods, one step stands out for its importance, and often its difficulty, and that is paying close attention to project cost control and budget management during the project progress.
This is especially true when it comes to thermoforming, a process in which plastic sheets are heated until they become malleable enough, then adsorbed onto a mold and allowed to cool to achieve the final product shape. Because this type of manufacturing involves a lot of cash (raw materials plus equipment expenses; wages, and other overhead), costs can easily get out of control if expenses are not carefully monitored at all times.
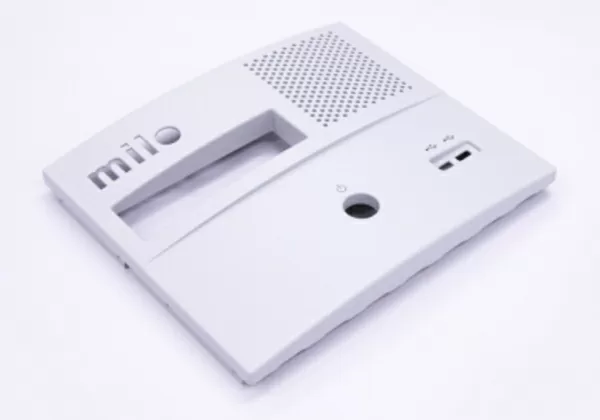
For companies across a wide range of industries, one of the biggest hurdles to overcome when it comes to thermoforming solutions is tightly controlling costs and sticking to a budget, but with its adaptability, the process also offers cost-saving opportunities.
This blog post will reveal the strategic framework and tactical tactics required to effectively manage your budget when thermoforming a project. We use real-life examples and provide you with concrete steps so you can learn how to control costs and improve overall operational efficiency while remaining profitable even when performing complex thermoplastic manufacturing tasks. In today’s blog post, we’ll delve into the financial aspects specifically related to these methods; by following our advice, you’ll not only cut expenses, but also streamline other areas, freeing up valuable resource costs.
Understanding Thermoforming Projects
Before we discuss cost control in the process, it is important to understand thermoforming projects. To fully understand how to reduce costs during the thermoforming process, you first need to understand what a thermoforming project entails and how these efforts fit within broader product development goals.
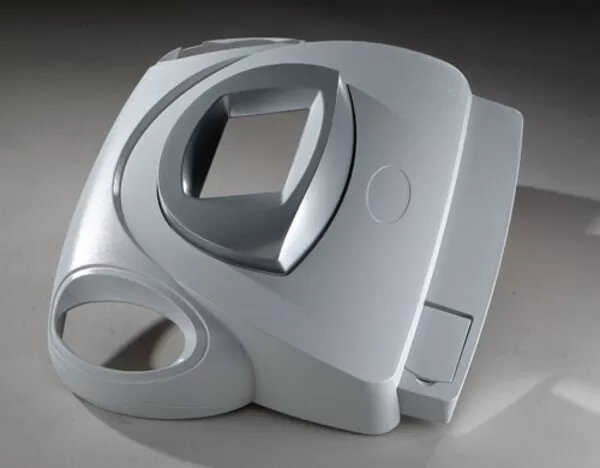
The Thermoforming Process
The thermoforming process uses heat to shape a flat thermoplastic sheet into something useful. Thermoforming is a versatile, cost-effective process. How it works: First you heat the plastic sheet; next, you cover it over the mold; and finally you apply vacuum pressure with a machine (or sometimes just plain old hands) until you get what you want! Thermoformed items are everywhere—from food trays to auto parts—because the technology is both versatile and cost-effective.
The Essentials of Project Planning
Comprehensive project planning is the first step to effective project budget management. This stage requires careful consideration of details, including:
Design considerations: The design phase has a direct impact on how much material is used and how long production takes. With the right design, standard panel sizes can be optimized, resulting in less scrap.
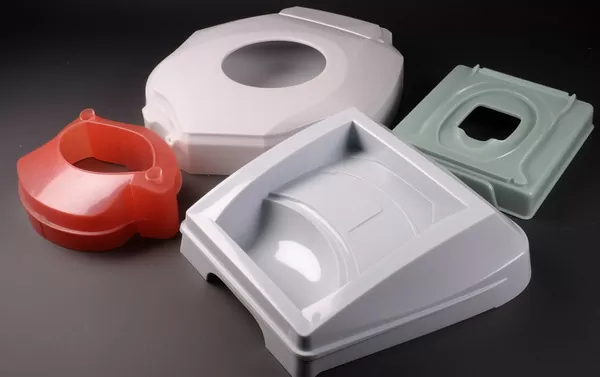
Material Selection: Choosing the right material is crucial. Factors to consider include strength (does the item need to support something heavy?), clarity (is it important that something can be seen through?), and overall cost compared to available alternatives.
Mold Cost: Mold costs vary greatly depending on complexity and size! Typically, such expenses are incurred up front during the project rather than spread evenly over time.
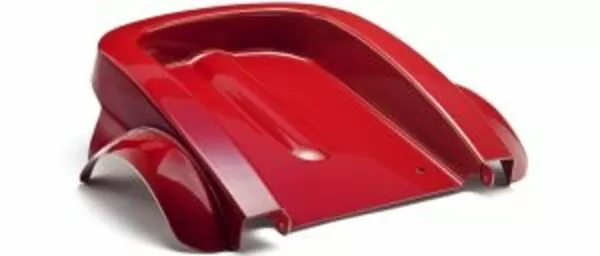
Cost Segregation in Thermoforming
In vacuum forming, costs can be segmented into various categories, each warranting a unique strategy for control and optimization.
Raw Material Costs
Thermoforming projects often require the purchase of large quantities of raw materials. Therefore, inefficient use of these materials can result in high costs. There are two main ways to solve this problem:
Material Efficiency: Striving to get the most out of each part through smart design and ensuring components fit together in the best possible way;
Inventory Management: Use a just-in-time approach to minimize storage costs while avoiding supplies becoming obsolete before they are used.
Labor Costs
In industries that rely heavily on labor, one way to cut costs is to automate tasks where feasible. Here are two strategies for achieving this without sacrificing quality:
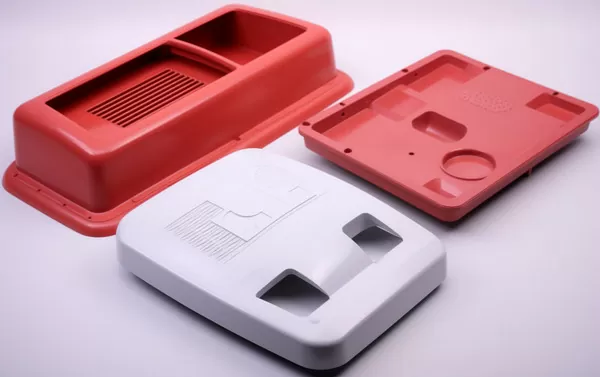
Automate: Identify processes that are suitable for automation and then implement them accordingly.
Cross-Training: Provide employees with multiple skills through cross-training – this way, if demand suddenly increases, you won’t spend more money hiring new employees because existing employees can handle it on their own.
Overhead and Operating Costs
Facility costs, energy usage and maintenance all incur overhead costs:
Prioritize Energy Conservation: You can reduce your utility bills by using more efficient equipment and processes.
Plan for Maintenance: Regular inspections mean catching potential problems early, avoiding costly emergency calls and lost production due to mechanical failure.
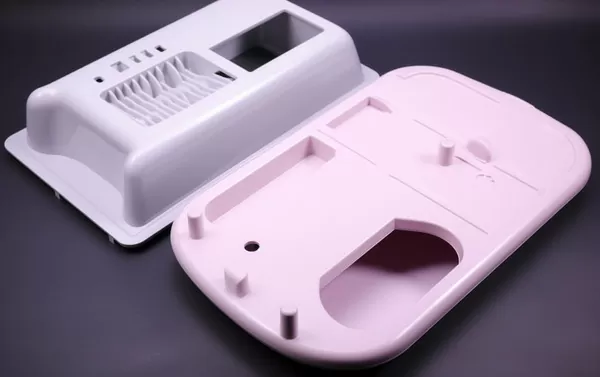
Tooling and Equipments Expenses
Tool and Equipment Costs Managing the costs associated with tooling and equipment is an important aspect of thermoforming:
Tool Life Cycle: The tool life used in thermoforming is limited. Knowing when they need to be replaced and budgeting for those replacements can help avoid unwelcome financial surprises later on.
Comparison Shopping: It’s wise to get quotes from different suppliers to ensure you’re not paying more than necessary for machinery or tools.
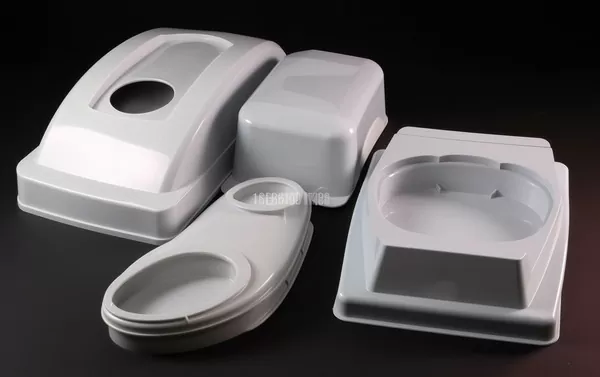
Pre-project planning
The Role of Accurate Planning in Thermoforming
When it comes to financial planning, the beginning of a project is crucial. In thermoforming, we must have a complete grasp of the project as a whole: its design, required materials, and production schedules, among other factors. Without enough forward thinking at this stage, costly changes may occur in the future and deadlines may be pushed back – both of which impact project costs and ultimately the bottom line!
Forecasting Techniques in Thermoforming
There are tons of ways to forecast thermoforming budgets, such as bottom-up cost estimate and regression analysis, and tools like predictive software, project management software and parametric modeling, there’s no shortage of technology, just like there’s no such thing as a typical project! In this article, we’ll help you choose which type (or types) is most effective given certain parameters; a delicate balance between being reliable enough and being useful enough.
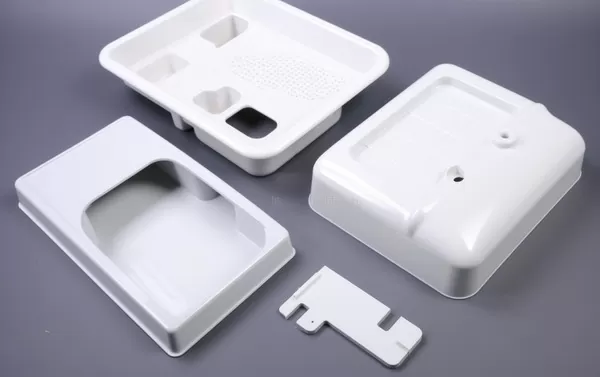
A Planner’s Triumph: A Real-world Example
A thermoforming company conducts extensive customer research to anticipate demand and justify investments ahead of time, using customer surveys and other data sources, and carefully plans expansion into new markets. Exceeded its profit targets based on survey results by not allocating too many resources to underperforming products.
Material Selection and Cost
1. How Materials Shape Your Budget
In a thermoforming project, one of the main factors to consider in order to save costs without sacrificing product quality is the material. Their characteristics, such as surface finish or thickness, can have a strong impact on product production. Because they collectively take up a large portion of the project budget, understanding the impact of material properties such as thickness and surface finish is key to making informed cost-saving decisions without compromising product quality.
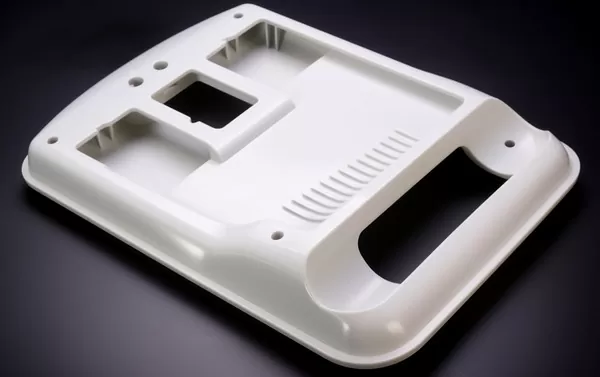
2. Strategic Material Selection
The project managers should choose the perfect material for a job, one that performs well without breaking your budget. Also master the art of negotiating with raw material suppliers so that you get what you want without breaking any friendships, as well as the quality of finding a good material supplier.
3. Material Selection Mastery: A Case Study
By switching to a cheaper material with similar aesthetics and protective properties that still looks good and offers the same level of protection, one thermoformed packaging manufacturer has no complaints from customers about the change – meaning savings across the board . The packaging project successfully reduced costs without compromising the product’s appeal.
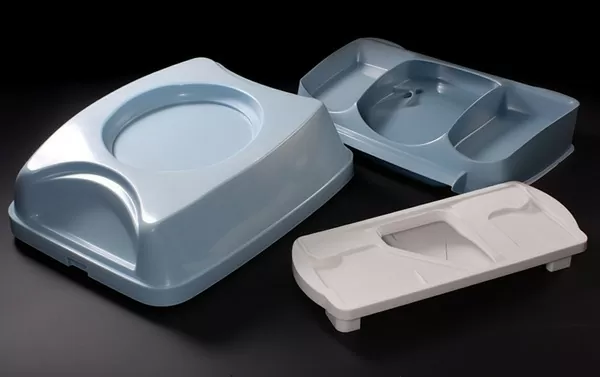
Maximizing Operational Efficiency
1. Reducing Waste
Waste is eating away at budgets—but vacuum forming offers a solution. Learn how techniques like nesting and using recycled materials can effectively reduce waste and lower costs.
2. Labor and Overhead
Labor is an expense that can easily get out of hand, but having well-trained, efficient employees is invaluable. Thermoforming manufacturers should explore ways to strike the right balance between wages and output, as well as smart facility operations management to cut other types of costs.
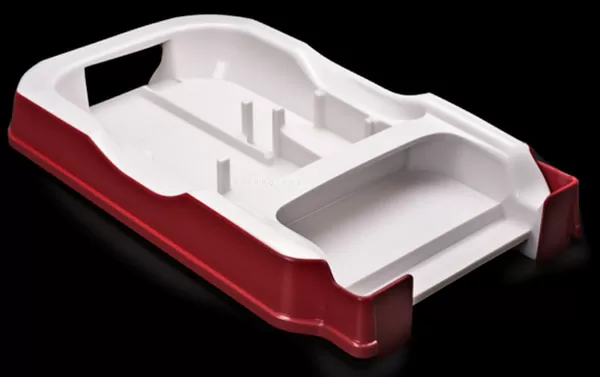
3. Equipment and Technology Adoption
Allocating funds to technology and equipment is a financial undertaking that requires careful consideration. Thermoforming manufacturers have relevant expertise that can help you make decisions about cost-effective use of new developments: run an up-to-date and efficient operation.
4. Efficiency Embodied
For example: A manufacturer modernized its thermoforming machines, with each upgrade carefully weighing potential reductions in energy consumption and increases in production speed.
As a result, the company has gained a streamlined and more cost-effective process, thereby greatly improving the efficiency of product production and reducing process costs.
Advanced Cost Control Strategies
Once you have a handle on the primary cost segments, it’s time to explore advanced strategies to refine your budget management.
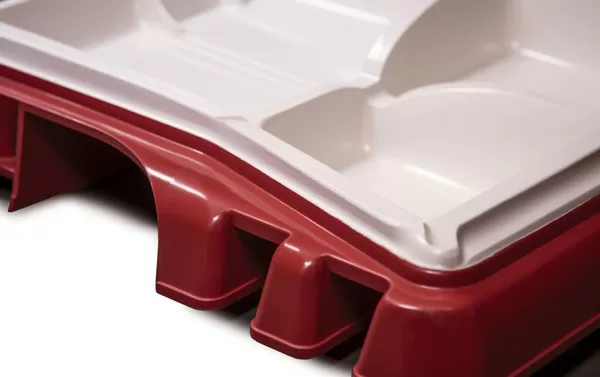
1. Value Engineering
The value engineering process systematically examines the functionality of goods and services to increase their overall value. In the case of thermoforming, this may mean rethinking factors such as shape, size or thickness, making adjustments so that performance remains the same (if not better) but at a lower overall cost.
2. Strategic Sourcing
Cost control is largely affected by purchase price. Working with key suppliers may result in discounts based on volume and price, making them more favorable overall. There are also significant cost savings when sourcing opportunities arise in areas where labor costs are lower or where the work can be done better/faster/with fewer errors, etc.
3. Lean Manufacturing Principles
Implementing lean manufacturing methods can lead to long-term cost savings. This involves finding ways to streamline production processes – from layout to workflow – to make them as efficient as possible; it also involves taking steps to minimize waste in terms of materials used and time taken up during production.
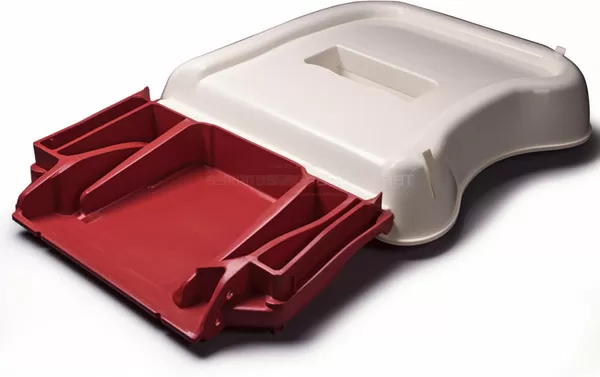
Leveraging Technology and Data for Cost Control
In the age of Industry 4.0, technology and data reign supreme as cost-controlling assets that promise precision and predictive power.
1. Realizing the Power of Data Analytics
Data analysis can reveal valuable information that can help cut costs. This includes:
Predictive Maintenance: Use IoT devices on machines for predictive maintenance, which helps avoid costly breakdowns.
Resource Optimization: Use sophisticated data analysis to determine how machines can be used more efficiently so they don’t sit idle, and the costs involved.
2. Automating for Cutting-Edge Efficiency
Automation is key to achieving efficiency, saving labor and reducing human error. Some things to consider:
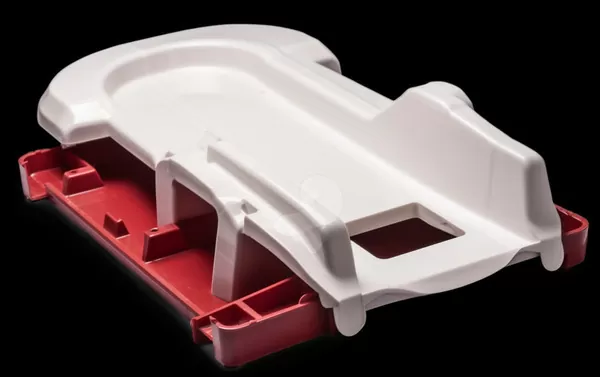
Robotics and Artificial Intelligence: By introducing robots and artificial intelligence into your production line, you can achieve constant high-speed output every day of the week without the need for humans to do all the work.
Workflow Automation: Automating workflows, such as checking inventory levels or ensuring products meet quality standards, not only gets the job done faster but also prevents costs from spiraling when things go wrong.
Conclusion
For companies in the thermoforming industry, controlling costs and managing budgets isn’t just about spending money wisely, it’s critical to success and survival. The above tips and strategies should help businesses approach every job they undertake from a financial perspective: increasing efficiency, minimizing waste and ensuring every part of production runs smoothly. This not only saves direct costs; Opportunity; having such a solid foundation could mean the ability to innovate further in the next round, or steady growth in this fast-paced industry.
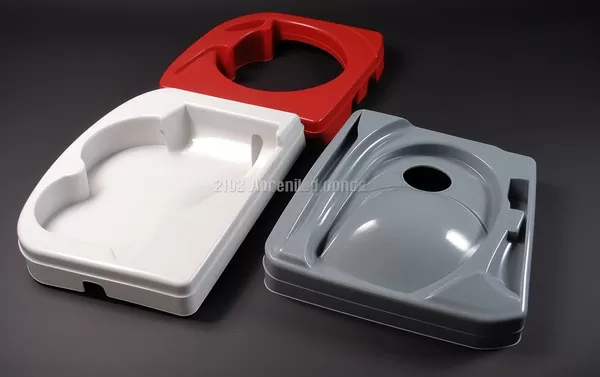
Actual cost control and project budget management are ongoing processes in thermoforming projects. They require careful strategic planning, thorough inspection and proactively increasing the value and longevity of your work. This comprehensive guide lays out strategies that will help you stay on track, but be ready to pivot to get the most out of it from a financial perspective once it’s all said and done.
When it comes to pressure forming, being able to effectively control actual costs and manage your project budgets is crucial if you want your business to not only survive but thrive. Past projects and every new project brings its own set of obstacles and rewarding opportunities – as long as you approach them with the right attitude: a hard-working attitude; flexibility when necessary (such as changing plans mid-stream); plus an understanding of finances Not just “doing math”. Now that you understand how the process works—and some practical techniques/tools for keeping tabs on money matters—you’re in a good position.