Introduction
Designing products requires a balance between appearance and functionality. It’s not just about making something eye-catching – designers also need to know that their creations can be made easily, last a long time and aren’t too expensive. Manufacturers have been using vacuum forming for a long time because the process takes a lot of time. Take the box for example: it doesn’t cost much, and you can do all kinds of things with it. But now there’s vacuum forming in a variety of materials, which adds more functionality to the product during the design process!
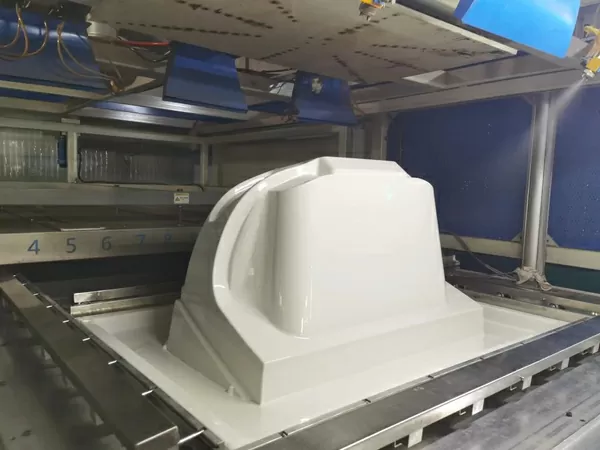
In an ever-changing industry like product manufacturing, manufacturers are always looking for ways to make better products. One of the great advances in the world of manufacturing is the advent of multi-material vacuum forming processes: using this process it is possible to completely change the appearance and functionality of products. This article takes an in-depth exploration of multi-material vacuum forming: explaining what it is, why it’s useful, and how its use can grow in future industries beyond manufacturing!
Understanding Vacuum Forming
Definition and Basic Explanation
Vacuum forming process is a manufacturing method that uses heated plastic sheets soft and bendable. These flexible sheets are then placed over molds, where the air is sucked out and they are tightly sealed so they take on the desired shape they are molded into. The cooled and formed plastic retains the shape of the mold, allowing the creation of a wide variety of products. Packaging materials or automotive parts can be made with this technology; its popularity stems from the fact that the process is relatively simple, has short turnaround times and is cost-effective and is widely used.
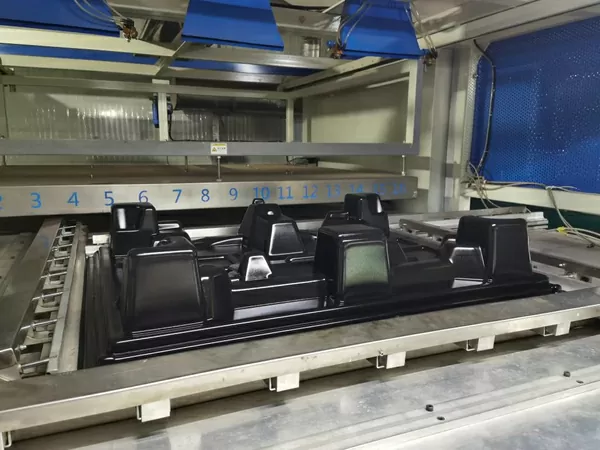
History
Vacuum forming manufacturing process has been around since the 1930s, when it was first used by the aircraft industry to create canopies and other items. It exploded in popularity in the 1950s thanks to advances in plastic technology: manufacturers suddenly had an easier way to produce large quantities of components cheaply.
Advantages of Thermoforming
1. Simplicity and speed
Vacuum forming requires simpler molds than injection molding or other traditional molding methods, simplifying the production process. This makes overall manufacturing faster.
2. Low Mold Costs
In pressure forming, molds tend to be much cheaper than those used elsewhere – meaning prototypes as well as small and medium-sized batch production are available at affordable prices!
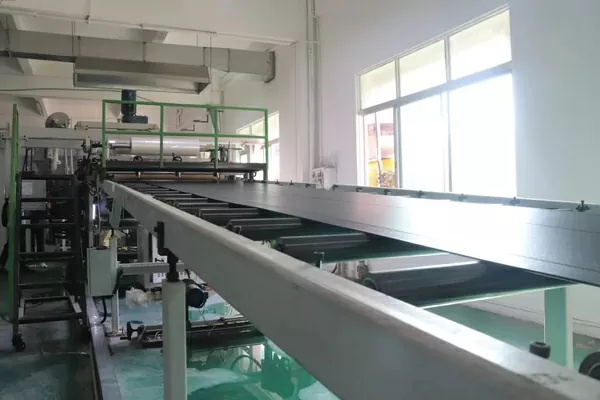
3. Flexibility when forming to size
If you need flexibility in determining the size of your product that can be manufactured, look no further; vacuum forming can be used to manufacture parts from small to large, providing a high degree of flexibility in product size.
Why Vacuum Forming?
One reason for vacuum forming’s popularity is its relatively low price and speed at producing top-notch plastic parts. It works equally well for small or large products during the prototyping stage, which saves time and money in a range of sectors such as automotive; home appliances etc.
Limitations of Traditional Vacuum Forming
Although it offers several advantages over traditional technologies, their use is sometimes limited, especially when just one material cannot meet the complex requirements of modern product design.
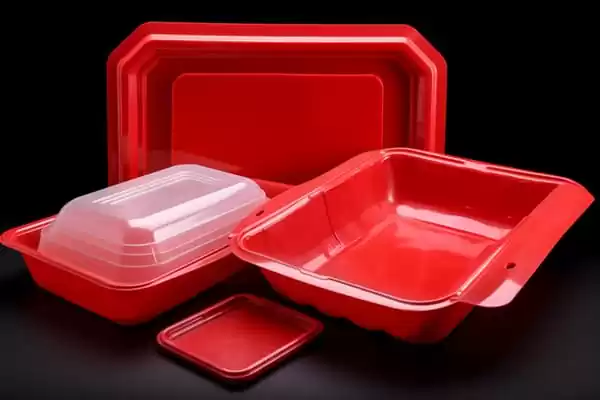
The Advent of Multi-Material Vacuum Forming
Definition of Multi-Material Vacuum Forming
Multi-material vacuum forming improves upon traditional vacuum forming. Vacuum formed products made in this way not only have the shape and form of the vacuum forming molds, but can also have the properties of multiple materials at the same time – a significant advance in performance.
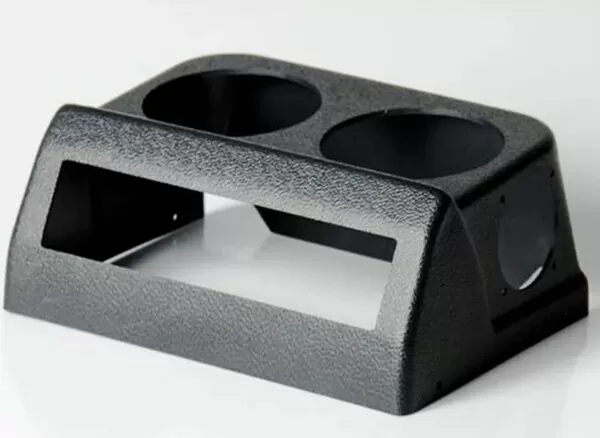
How Multi-Material Vacuum Forming Evolved from Traditional Vacuum Forming
Manufacturers are expanding vacuum forming capabilities by moving from using just one material to using multiple materials. This means they can now do more with the process than ever before: improve the way the product works; plus, it opens up opportunities for designs that were previously unachievable.
Technological Advancements Enabling Multi-Material Capabilities
Thanks to a series of technological innovations, it is now possible to use multiple materials simultaneously for vacuum forming. State-of-the-art tooling and material handling systems mean different substances can be combined into a single part during the molding process, while new temperature controls ensure all parts are properly bonded together after molding.
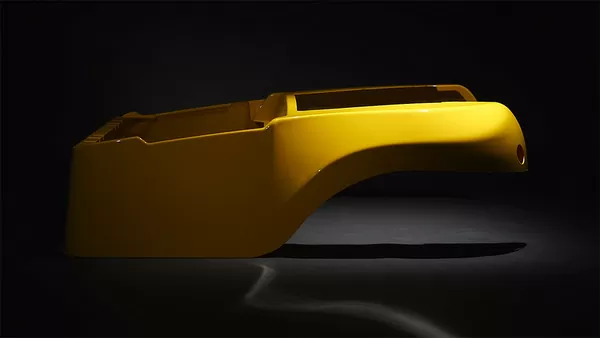
Benefits of Multi-Material Vacuum Forming
The shift from traditional single-material molding to multi-material vacuum forming has brought many benefits to both manufacturers and buyers. Manufacturers and designers are more inclined to this new process to push the boundaries of product design.
Enhanced Product Functionality through the Use of Different Materials
Today’s products can combine a variety of materials to create visual and tactile interest as well as added functionality. For example, a car console may have both hard-wearing plastic parts and soft-touch areas, or in a medical device, antimicrobial handles may be combined with clear plastic that needs to remain sterile. Vacuum forming using multiple materials makes it easy to produce these types of combinations in one go.
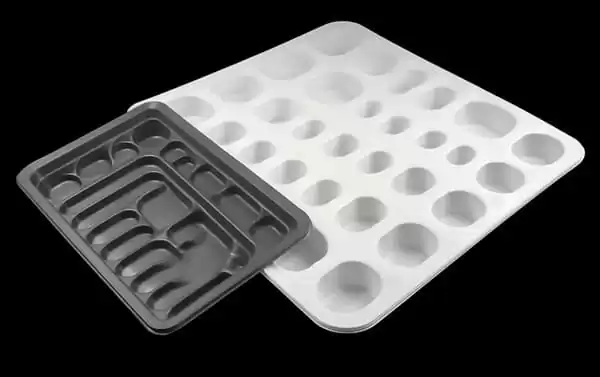
Ability to Combine Materials with Different Properties for Composite Results
This approach makes it possible to create composite materials that exploit the strengths of each component and offset their weaknesses. The result is a finished part with better mechanical or aesthetic properties than if the entire product was made from just one material type.
Cost and Time Savings
There are also efficiencies associated with using multiple materials simultaneously: there is less need for subsequent assembly operations because all materials are integrated in one operation; labor costs per unit of production are reduced, partly due to increased automation; compared with traditional vacuum forming method alone , resulting in less waste per product as far less scraps etc. are produced.
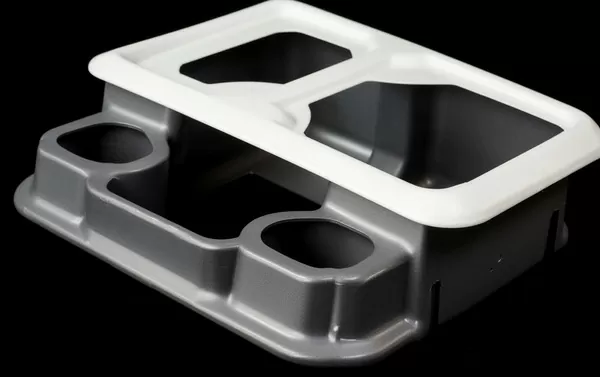
Reduction in Environmental Impact
The reduction in material waste and energy consumption associated with multi-material vacuum forming aligns with modern sustainability goals, making it a more eco-conscious manufacturing process.
Design Considerations for Multi-Material Vacuum Forming
When it comes to multi-material vacuum forming, one must take a different approach than if they were using the traditional method. Having a good grasp of what this technique can and cannot do will help guide your design decisions effectively.
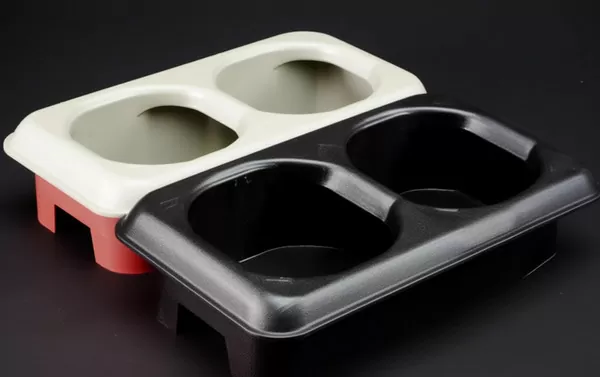
Material Selection
One major factor designers need consider is picking materials that are compatible enough with each other for thermoforming purposes while still being able to meet any necessary structural requirements once formed; otherwise you may end up compromising both aesthetics as well functionality!
Mold Design
Designing molds takes extra care too: They have got be fashioned precisely so all those disparate substances fit snugly –– but also stick together nicely when heated plastic sheet into shape during processing time (or else!).
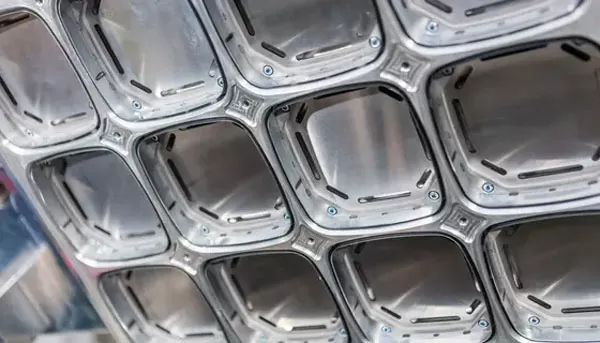
Process Control
Being adept at controlling variables is pivotal here—namely how much heat things get exposed too overall plus individually along every step in between molding out an object cooling its component parts down afterward … all while working multi-task magic upon several diverse materials concurrently.
Applications of Multi-Material Vacuum Forming
This advanced form of vacuum forming has far-reaching relevance, evident in its application across a broad spectrum of industries.
Automobile Industry
Multi-material vacuum forming is an important technique for creating car interiors that look good while also being practical. One example of this is making dashboards using multi-material vacuum forming: it allows designers to include electronics like buttons and screens seamlessly within them – as well as giving different areas their own textures.
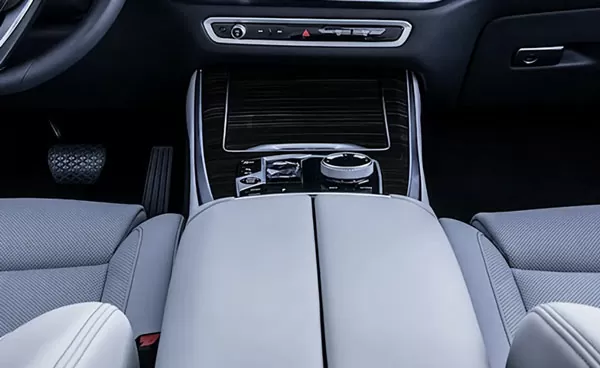
Medical Sector
Healthcare equipment such as machines for diagnosis or products to care for patients needs to be clean, safe and easy to use too; they must also often be ergonomic (efficient and comfortable) for staff or patients’ bodies. Multi-material vacuum forming can tailor products to fit these stringent requirements.
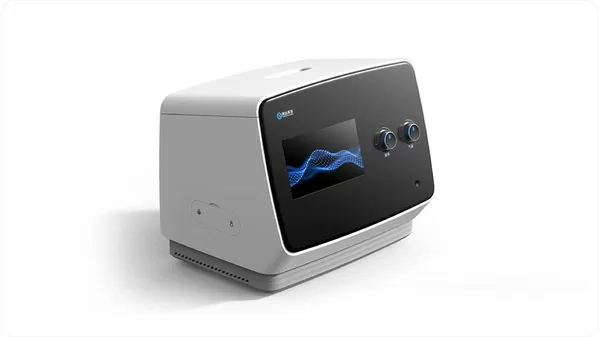
Consumer Products
Consumer goods generally do best when able both work properly & appeal visually whether we are talking about domestic appliances e. g., kitchen stuff / electronic gadgets like phones computers etc.) This usually calls needing materials with different properties- More than one kind may need combining so each part does jobs expected its function while looking great overall Multi-material Vacuum Forming offers way achieve exactly that.
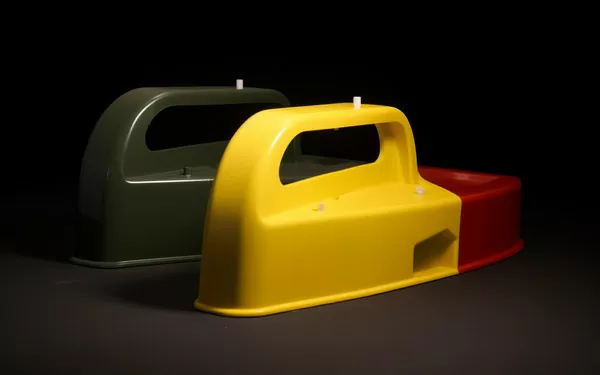
Challenges and Considerations
Despite its advantages, multi-material vacuum forming also presents designers and manufacturers with distinct challenges that demand thoughtful consideration and strategic resolution.
Technical Complexity
The operation of multi-material vacuum forming equipment necessitates a high level of technical expertise and accuracy. When designing for this technique, it is necessary to have a deep understanding of how different materials interact with one another, their heating profiles, as well as what happens during the final stages of forming.
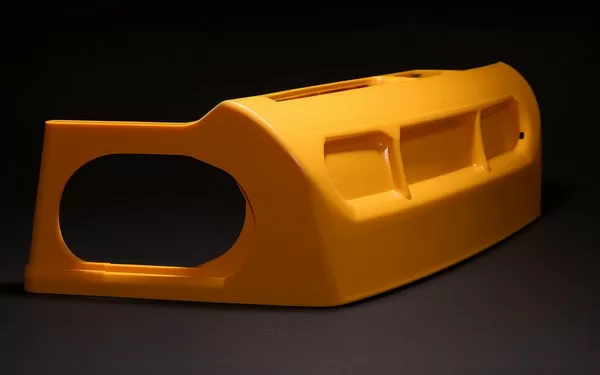
Material Compatibility and Adhesion
One key thing to get right is making sure that any materials chosen stick together properly while they are being formed: if there are adhesion problems then defects may appear in the finished item – affecting both its quality levels and how well vacuum forming work.
Design for Manufacturability
Designing parts destined for use in multi-material vacuum forming processes requires striking balances between creativity on the one hand; manufacturability (things can actually be made!) on the other. Among considerations designers must bear in mind are process limitations like undercuts plus parting lines – because these too will have an impact upon whether something succeeds or fails.
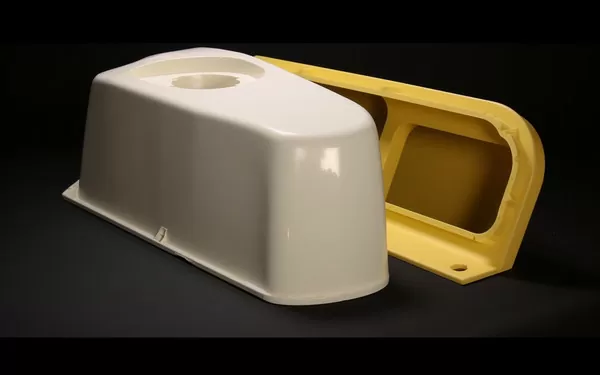
Quality Control
Making sure every single product produced is up-to-scratch presents considerable challenges. To overcome them manufacturers need not only to keep a close eye on processing parameters at all times but also handle materials in ways known reduce defect risk – thereby ensuring all vacuum formed parts meet required standards once complete!
The Future of Multi-Material Vacuum Forming
As we look forward, it is clear that there is great potential for multi-material vacuum forming to continue advancing and meeting evolving needs in product design and manufacturing.
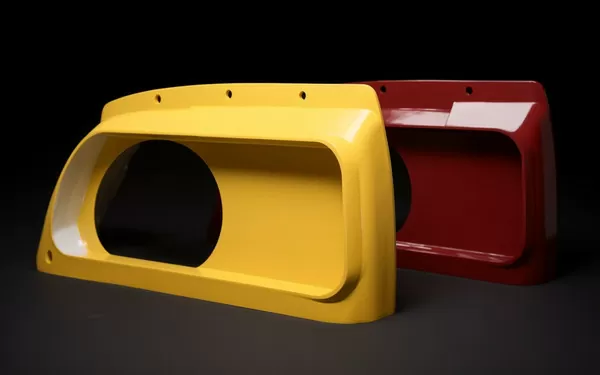
Technological Innovation
Ongoing research and development efforts may soon yield even more sophisticated vacuum forming machine for this process – machines(industrial vacuum forming machines, diy vacuum forming machines) able not just to work with a broader array of materials but also to integrate smart materials and composites among them.
New Horizons for Industries
Industries such as aerospace engineering or industrial equipment production that have yet fully to explore the advantages offered by multi-material vacuum forming might discover applications hitherto undreamed-of: they could find themselves redefining what’s possible in their respective fields entirely!
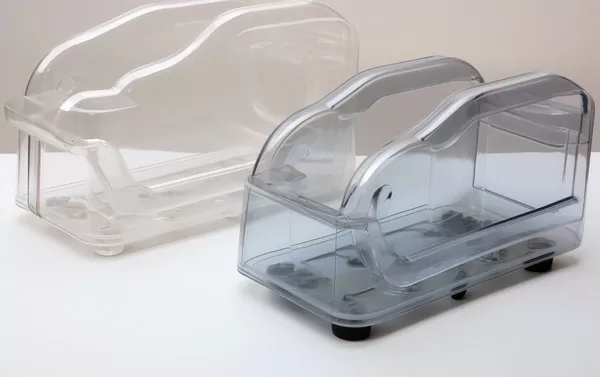
Impact on Product Development
Indeed, widespread adoption would enable manufacturers from all sectors access at once both ease when changing things up during fabrication (thanks-you-very-much versatility) plus efficiency gains via lighter-weight designs popping forth daily off 3D printed or 3d printed molds worldwide – which might well disrupt some existing marketplaces too much so do check back next month. In short? The future looks bright if innovation continues unabated within R&D departments across industry.
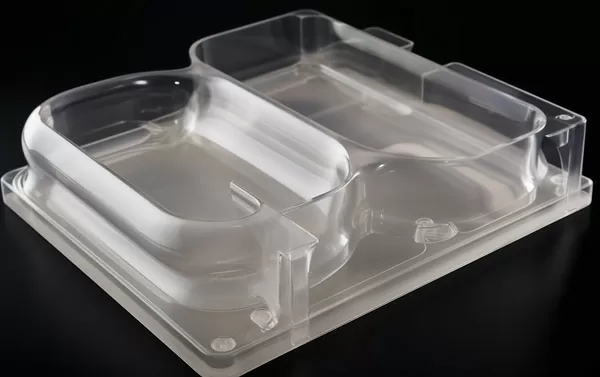
Case Studie
One way to understand how multi-material vacuum forming works is by looking at real-life examples. These case studies demonstrate how designers have overcome problems and made new things thanks to multi-material vacuum forming.
Multifunctional Automotive Interior Panels
Automotive companies want to create interior panels that are comfortable (e.g., soft-touch materials), durable (e.g., wear-resistant materials), and beautiful (e.g., stylish decorative finishes). Using multi-material vacuum forming means they can do it all in one go – as each panel mold has many different functions!
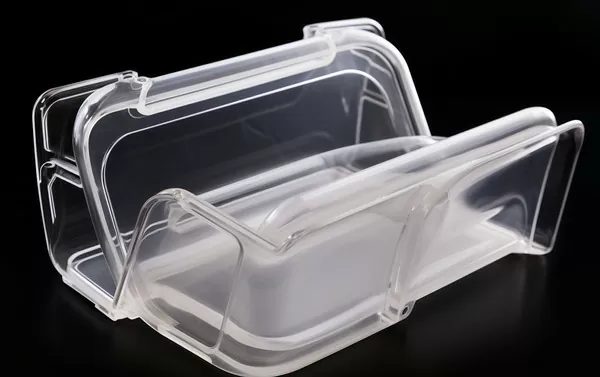
Lightweight and Durable Sports Equipment
A lot of sports equipment needs to be strong enough not to break easily, but light enough so the user can move quickly without tiring too quickly! Some companies are now using a multi-material approach to multi-functional manufacturing when manufacturing their products, which allows them to choose different materials based on where strength/flexibility is most important while keeping overall weight low.
Advanced Electronic Enclosure
Electronics companies’ products often require safe enclosures and insulating conductive properties so that their products can perform well even under harsh conditions such as extreme temperatures, vibrations, and drops from heights. Multi-material vacuum forming is a very good way to produce this product.
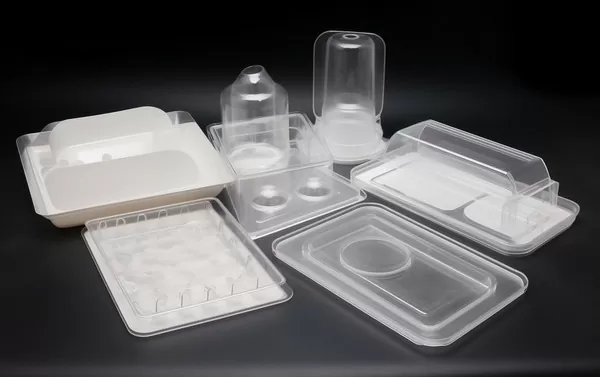
Conclusion
The emergence of multi-material vacuum forming opens up new possibilities for the manufacturing industry. This technique enables different materials to be seamlessly combined in ways that were not previously feasible, thereby changing both how products can be designed and what they are capable of doing.
Multi-material vacuum forming is changing the game in product design and manufacturing. It allows the use of multiple types of materials in a single molding – opening up endless possibilities in creating new products! Multi-material vacuum forming provides a platform for enhanced functionality, improved aesthetics and cost-effective production.
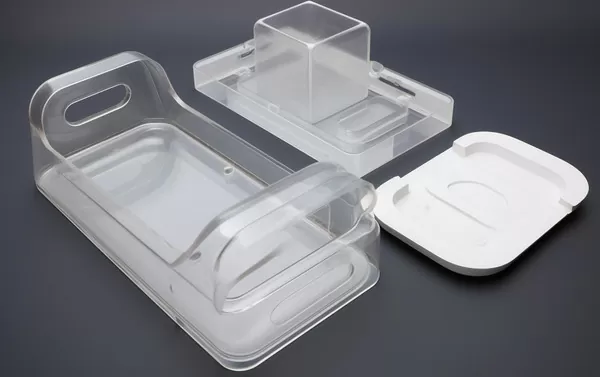
Designers and manufacturers who want to stay ahead of the curve should consider multi-material vacuum forming. As materials science and manufacturing technology advance, it will soon be necessary for these professionals to routinely use this technology in their product development processes if they hope to not only keep up with, but surpass, their competitors.
Call to Action
If you work in design or manufacture and want access these benefits too — don’t wait any longer before exploring multi material vacuum forming! Today adopting such cutting edge methods may give firms an advantage over rivals tomorrow who have yet see their potential impact on productivity levels as well competitiveness within global markets where consumers increasingly expect both inventiveness alongside high standards from producers.